- お役立ち記事
- Principles and Applications of Angular Rate Sensors
Principles and Applications of Angular Rate Sensors
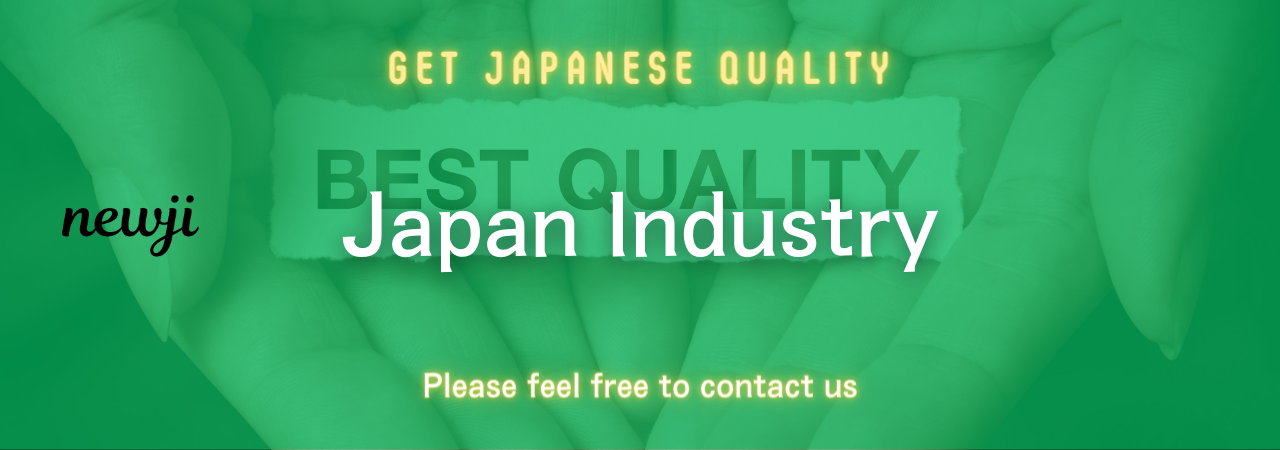
Angular rate sensors, also known as gyroscopes, have greatly impacted various fields with their ability to measure rotational motion. They are instrumental in automotive systems, aerospace engineering, robotics, and even in consumer electronics. Understanding the principles and applications of angular rate sensors can help us appreciate their significance and usefulness.
目次
What Are Angular Rate Sensors?
Angular rate sensors measure the rate of rotation around a particular axis. These sensors detect changes in the angular velocity, providing data that can be used to determine orientation and motion. There are different types of angular rate sensors, with the most common being MEMS (Micro-Electro-Mechanical Systems) gyroscopes and fiber optic gyroscopes. Each type operates on unique principles but serves the same fundamental purpose: measuring angular rate.
How Angular Rate Sensors Work
Principle of Operation
Angular rate sensors typically work based on the Coriolis effect, a phenomenon that occurs in rotating systems. When an object moves within a rotating reference frame, it experiences a force perpendicular to its direction of motion. Gyroscopes use this effect to measure angular velocity.
MEMS Gyroscopes
MEMS gyroscopes are widely used due to their compact size and high precision. These devices consist of a small vibrating structure that reacts to angular movements. When the gyroscope rotates, the Coriolis effect causes the vibrating structure to shift, and this shift is measured to determine the rate of rotation. MEMS gyroscopes are commonly found in smartphones, gaming controllers, and drones.
Fiber Optic Gyroscopes
Fiber optic gyroscopes operate using the Sagnac effect, which involves the behavior of light in a rotating system. In these gyroscopes, light travels around a loop of optical fiber. When the system rotates, the path length of the light changes, resulting in an interference pattern that can be measured to determine angular velocity. These gyroscopes are highly accurate and are used in applications that require precise measurements, such as aerospace navigation.
Applications of Angular Rate Sensors
Automotive Systems
Angular rate sensors play a crucial role in modern vehicles. They are key components of stability control systems, helping to maintain vehicle balance during sharp turns and sudden maneuvers. By measuring the vehicle’s rotation, these sensors provide data that allows electronic control units to adjust braking and throttle inputs, enhancing safety and handling.
Aerospace Engineering
In aerospace engineering, gyroscopes are used in inertial navigation systems to provide precise measurements of an aircraft’s orientation and movement. This data is essential for guiding and stabilizing aircraft, especially in environments where external references, such as GPS, might be unavailable. Angular rate sensors ensure that aircraft can navigate accurately and maintain their intended flight paths.
Robotics
Robotics is another field where angular rate sensors are indispensable. Robots often rely on gyroscopes to maintain balance and orientation, particularly in dynamic environments. For instance, bipedal robots use gyroscopes to adjust their posture and avoid falling. Additionally, angular rate sensors help drones and autonomous vehicles navigate and stabilize their movements, making them crucial for advanced robotic systems.
Consumer Electronics
In the realm of consumer electronics, angular rate sensors have become commonplace. Smartphones utilize gyroscopes for various functions, including screen rotation, augmented reality applications, and motion-based gaming. Gaming controllers also use these sensors to detect movement and provide a more immersive experience for users. The versatility of angular rate sensors makes them valuable in enhancing user interactions with everyday devices.
Challenges and Future Developments
Challenges
Despite their widespread use, angular rate sensors face certain challenges. One major issue is drift, where the sensor’s output may gradually deviate from the actual value over time. Calibrating the sensors and implementing algorithms to correct drift is crucial for maintaining accuracy. Additionally, environmental factors such as temperature changes and vibrations can affect sensor performance, necessitating robust designs and compensation methods.
Future Developments
The future of angular rate sensors holds exciting possibilities. Advances in technology, such as the development of quantum gyroscopes, promise to offer even greater precision and stability. These devices leverage quantum mechanical effects to provide unparalleled accuracy in measuring angular velocity. Additionally, the integration of angular rate sensors with other sensing technologies, such as accelerometers and magnetometers, can create more comprehensive motion-tracking systems.
Conclusion
Angular rate sensors are essential tools in modern technology, enabling precise measurements of rotational motion. From enhancing vehicle safety to guiding aircraft and improving consumer electronics, their applications are vast and varied. As technology continues to advance, the capabilities of these sensors will undoubtedly expand, opening new possibilities for innovation and improving the performance of various systems. Understanding the principles and applications of angular rate sensors allows us to appreciate their significant role in our everyday lives.
資料ダウンロード
QCD調達購買管理クラウド「newji」は、調達購買部門で必要なQCD管理全てを備えた、現場特化型兼クラウド型の今世紀最高の購買管理システムとなります。
ユーザー登録
調達購買業務の効率化だけでなく、システムを導入することで、コスト削減や製品・資材のステータス可視化のほか、属人化していた購買情報の共有化による内部不正防止や統制にも役立ちます。
NEWJI DX
製造業に特化したデジタルトランスフォーメーション(DX)の実現を目指す請負開発型のコンサルティングサービスです。AI、iPaaS、および先端の技術を駆使して、製造プロセスの効率化、業務効率化、チームワーク強化、コスト削減、品質向上を実現します。このサービスは、製造業の課題を深く理解し、それに対する最適なデジタルソリューションを提供することで、企業が持続的な成長とイノベーションを達成できるようサポートします。
オンライン講座
製造業、主に購買・調達部門にお勤めの方々に向けた情報を配信しております。
新任の方やベテランの方、管理職を対象とした幅広いコンテンツをご用意しております。
お問い合わせ
コストダウンが利益に直結する術だと理解していても、なかなか前に進めることができない状況。そんな時は、newjiのコストダウン自動化機能で大きく利益貢献しよう!
(Β版非公開)