- お役立ち記事
- Principles of human error occurrence in the manufacturing industry and key points for prevention and countermeasures
月間77,185名の
製造業ご担当者様が閲覧しています*
*2025年2月28日現在のGoogle Analyticsのデータより
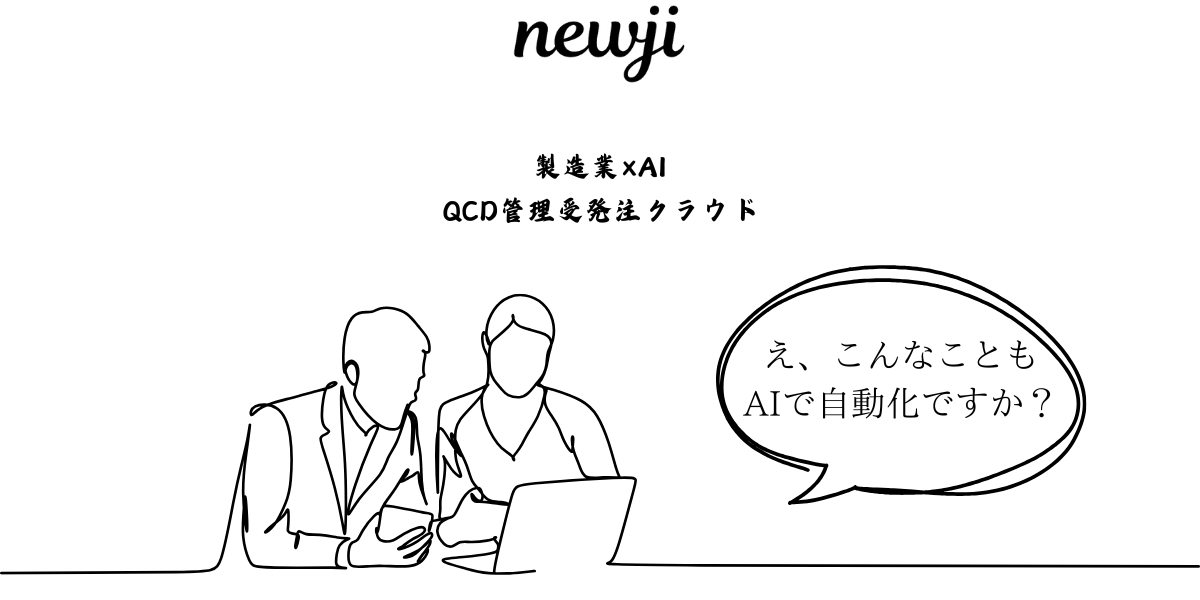
Principles of human error occurrence in the manufacturing industry and key points for prevention and countermeasures
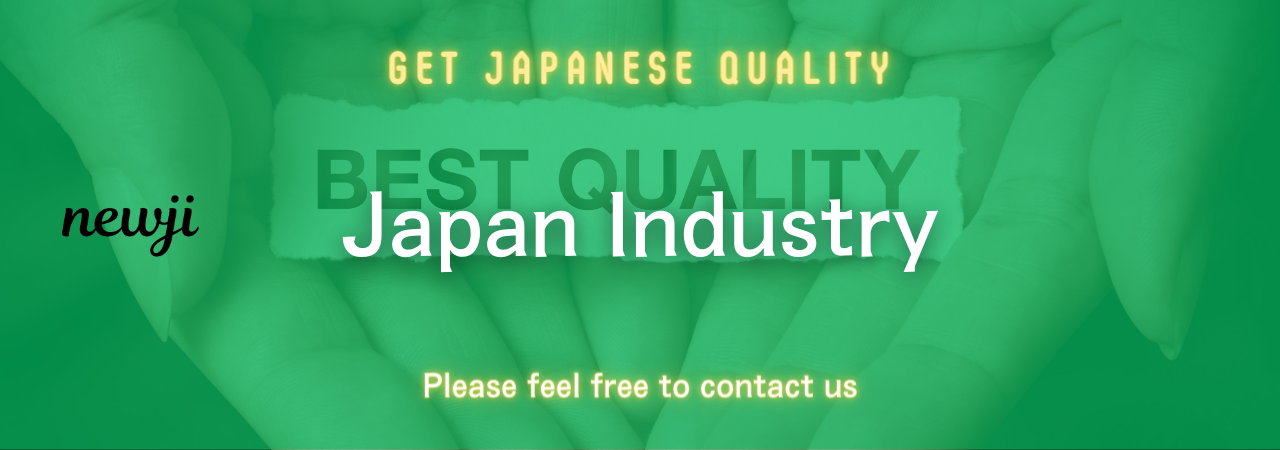
目次
Understanding Human Error in Manufacturing
Human error is an inevitable aspect of any industry, but its implications can be particularly significant in the manufacturing sector.
Understanding why human errors occur in this environment is crucial for developing effective prevention and countermeasure strategies.
In manufacturing, human errors can lead to production delays, increased costs, and even jeopardize safety.
Factors contributing to these errors range from inadequacies in training and work processes to equipment malfunctions and psychological influences such as stress or fatigue.
Causes of Human Errors
Several common causes of human errors in manufacturing can be identified:
1. **Lack of Proper Training**:
Without proper training, workers may lack the necessary skills and knowledge to perform tasks accurately.
This can result in mistakes that could have been easily prevented with adequate instruction.
2. **Complexity of Operations**:
The intricate nature of manufacturing processes often involves multiple steps and machinery.
Errors can occur when an operation is too complex or when workers are not fluent with new technologies or procedures.
3. **Environmental Factors**:
Poor lighting, noise, or inadequate workspace can significantly impair a worker’s ability to maintain focus, leading to errors.
Work environments that are uncomfortable or unsafe contribute substantially to human mistakes.
4. **Psychological Issues**:
Factors like stress, fatigue, and repetitive tasks can impact worker concentration and attention to detail.
When under psychological strain, workers are more likely to make errors.
5. **Communication Breakdowns**:
Effective communication is vital to ensure all team members understand their roles and the procedures they must follow.
Miscommunication or misunderstanding of instructions frequently leads to errors.
Identifying Points for Prevention
Prevention is key in minimizing human errors.
Several strategies can be adopted:
1. **Enhanced Training Programs**:
Comprehensive training and regular refresher courses can equip workers with the expertise and confidence needed to perform their duties accurately.
Training should include hands-on experience and e-learning opportunities to cover various learning preferences.
2. **Improving Work Environment**:
Adjusting workplace factors such as lighting, noise levels, and ergonomic furniture helps reduce physical strain and increases concentration.
Maintaining a clean and organized workspace also plays a crucial role in minimizing errors.
3. **Task Simplification**:
Where possible, simplify complex tasks and operations.
Standardized procedures and the implementation of automation technology help mitigate human error by reducing the likelihood of oversight.
4. **Stress Management and Routines**:
Implementing programs to manage stress and ensure adequate rest breaks can help maintain employee well-being, enhancing their ability to focus.
Companies can also explore job rotation strategies to reduce the monotony of repetitive tasks.
5. **Fostering Open Communication**:
Encouraging a culture of open communication where workers feel comfortable sharing concerns or suggestions can prevent errors before they happen.
It also allows for collaborative troubleshooting of existing issues.
Implementing Effective Countermeasures
It’s one thing to identify where improvements can be made, but putting these measures into practice is another challenge:
1. **Utilizing Technology**:
Adopting new technologies like machine learning and AI can monitor operations in real-time, predict likely errors, and alert operators before they manifest into larger issues.
Robotics and automation can handle repetitive or risky parts of production, freeing humans for more critical tasks.
2. **Increased Supervision**:
Regular audits and supervisory checks can detect potential problems early.
Supervisors equipped with checklists can standardize processes and ensure compliance with safety and operational standards.
3. **Feedback and Improvement Cycles**:
Incorporating employee feedback into continuous improvement systems allows for dynamic responses to errors.
This process ensures that lessons learned from previous mistakes are implemented in future training and process development.
4. **Risk Assessment Tools**:
Regular use of risk assessment tools and safety audits allows for the identification of potential error hotspots, facilitating better preparation and counteractive measures.
Benefits of Reducing Human Errors
The reduction of human errors in manufacturing brings about numerous advantages:
– **Safety Enhancement**:
Reduced incidents lead to less injury risk, promoting a safer working environment for employees.
– **Cost Efficiency**:
Minimizing errors translates to fewer resources wasted on fixing mistakes and lower costs associated with production delays and rework.
– **Increased Productivity**:
With fewer interruptions due to errors, production runs more smoothly, and productivity rises.
– **Quality Improvement**:
Ensuring that operations proceed without undue errors results in a higher quality final product, fostering better brand reputation and customer satisfaction.
Conclusion
Managing human error is an ongoing challenge in the manufacturing industry.
However, with strategic training, environment optimization, effective communication, and the use of advanced technologies, these errors can be minimized.
Implementing proper prevention methods and countermeasures not only enhances safety and productivity but also boosts the overall efficiency and quality of manufacturing operations.
資料ダウンロード
QCD管理受発注クラウド「newji」は、受発注部門で必要なQCD管理全てを備えた、現場特化型兼クラウド型の今世紀最高の受発注管理システムとなります。
ユーザー登録
受発注業務の効率化だけでなく、システムを導入することで、コスト削減や製品・資材のステータス可視化のほか、属人化していた受発注情報の共有化による内部不正防止や統制にも役立ちます。
NEWJI DX
製造業に特化したデジタルトランスフォーメーション(DX)の実現を目指す請負開発型のコンサルティングサービスです。AI、iPaaS、および先端の技術を駆使して、製造プロセスの効率化、業務効率化、チームワーク強化、コスト削減、品質向上を実現します。このサービスは、製造業の課題を深く理解し、それに対する最適なデジタルソリューションを提供することで、企業が持続的な成長とイノベーションを達成できるようサポートします。
製造業ニュース解説
製造業、主に購買・調達部門にお勤めの方々に向けた情報を配信しております。
新任の方やベテランの方、管理職を対象とした幅広いコンテンツをご用意しております。
お問い合わせ
コストダウンが利益に直結する術だと理解していても、なかなか前に進めることができない状況。そんな時は、newjiのコストダウン自動化機能で大きく利益貢献しよう!
(β版非公開)