- お役立ち記事
- Proactive Troubleshooting Techniques for Manufacturing Success
月間76,176名の
製造業ご担当者様が閲覧しています*
*2025年3月31日現在のGoogle Analyticsのデータより
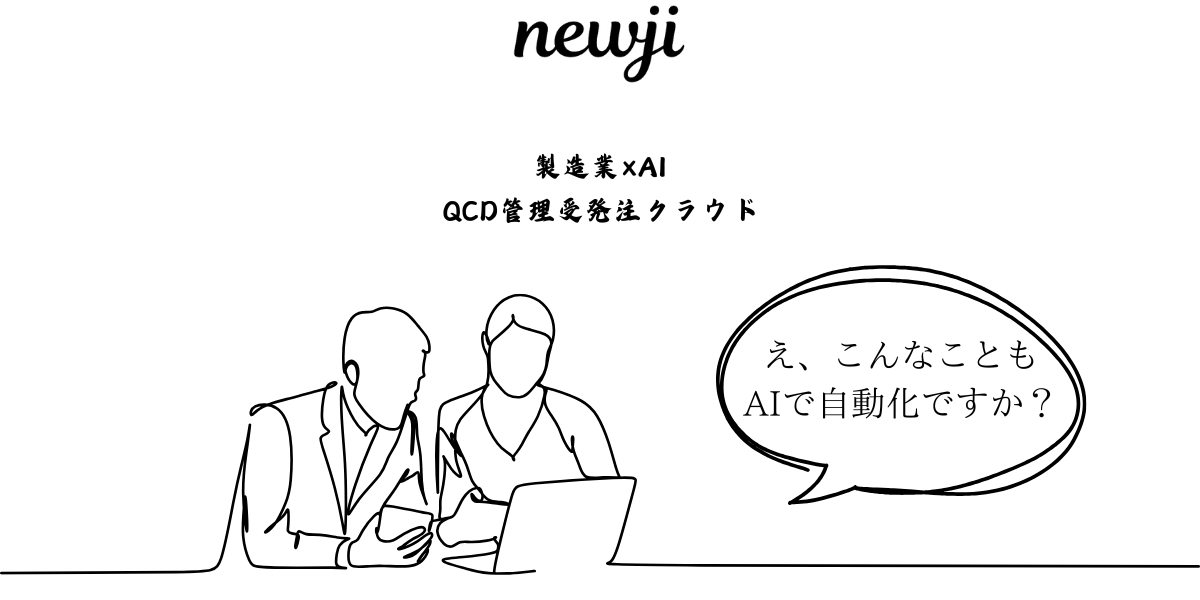
Proactive Troubleshooting Techniques for Manufacturing Success
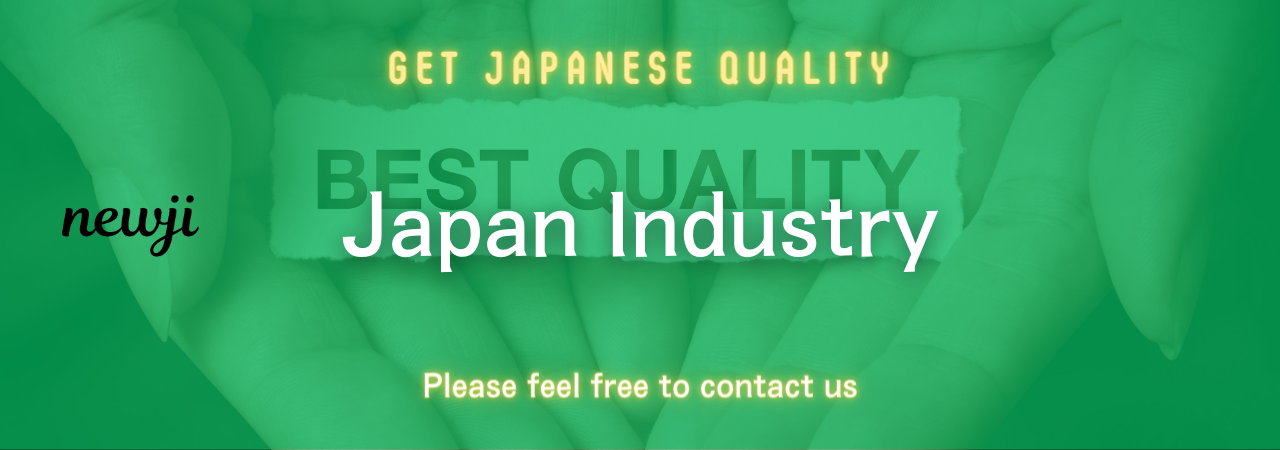
目次
Understanding Proactive Troubleshooting
In the fast-paced world of manufacturing, ensuring that production lines run smoothly is crucial for success.
Proactive troubleshooting is a technique used by manufacturers to prevent potential problems before they occur.
This approach not only saves time and resources but also enhances the overall efficiency of manufacturing processes.
By identifying and addressing issues early on, production can continue without unexpected hiccups that could lead to costly downtimes.
In this article, we’ll explore some effective proactive troubleshooting techniques that can contribute to manufacturing success.
Why Proactive Troubleshooting is Important
One of the main reasons proactive troubleshooting is important in manufacturing is the significant cost savings it offers.
By anticipating and mitigating problems before they escalate, manufacturers can avoid expensive repairs, product recalls, and production delays.
This not only protects the bottom line but also ensures that customers receive quality products on time.
Furthermore, proactive troubleshooting enhances production efficiency.
When potential issues are identified and resolved promptly, production lines can operate without interruption.
This means that workers can maintain focus on their tasks, leading to a more streamlined and productive work environment.
Techniques for Proactive Troubleshooting
Regular Equipment Maintenance
Regular maintenance of equipment is a fundamental proactive troubleshooting technique.
By creating and adhering to a strict maintenance schedule, manufacturers can detect and fix minor issues before they develop into major problems.
This includes routine checks, cleaning, lubrication, and replacing worn parts.
Such preventive measures not only prolong the lifespan of machinery but also ensure optimal performance.
Data Monitoring and Analysis
In today’s digital age, data is a powerful tool in proactive troubleshooting.
By implementing data monitoring systems, manufacturers can continuously track equipment performance and production metrics.
This data can then be analyzed to identify trends and patterns that might indicate potential issues.
For example, if a machine consistently operates at a higher temperature than usual, it could signal an impending failure.
Identifying such anomalies early on allows for timely interventions, preventing downtime.
Training and Empowering Employees
Investing in employee training is another key aspect of proactive troubleshooting.
Workers who are well-trained are more likely to identify and address potential issues quickly.
By empowering employees to take initiative, manufacturers create a proactive culture that emphasizes problem-solving and innovation.
Regular training sessions can help workers stay updated on the latest troubleshooting techniques and best practices.
Additionally, fostering open communication allows employees to share their insights and experiences, contributing to continuous improvement.
Implementing Predictive Maintenance
Predictive maintenance is an advanced form of proactive troubleshooting that leverages technology to anticipate equipment failures.
Using sensors and machine learning algorithms, predictive maintenance systems can assess the health of machinery in real-time.
These systems predict when a component is likely to fail and schedule maintenance activities accordingly.
By relying on data-driven predictions, manufacturers can minimize unplanned downtimes and reduce maintenance costs.
Predictive maintenance also ensures that repairs are performed only when necessary, further optimizing resource allocation.
Benefits of Proactive Troubleshooting
Proactive troubleshooting offers numerous benefits that contribute to the overall success of manufacturing operations.
One of the most significant advantages is enhanced product quality.
By addressing potential issues early, manufacturers can ensure that products meet high standards and customer expectations.
Customer satisfaction is another critical benefit.
When products are delivered on time and without defects, customers are more likely to trust and continue doing business with the manufacturer.
This, in turn, leads to increased customer loyalty and positive brand reputation.
Moreover, proactive troubleshooting supports sustainability efforts.
By reducing waste and optimizing resource use, manufacturers can minimize their environmental footprint.
This aligns with global sustainability goals and showcases a commitment to responsible manufacturing practices.
Overcoming Challenges in Proactive Troubleshooting
While proactive troubleshooting offers numerous benefits, it is not without its challenges.
Implementing these techniques requires a change in mindset and operations, which can be difficult for some organizations.
Resistance to change, lack of resources, and limited expertise are common hurdles that manufacturers may face.
To overcome these challenges, it is essential to foster a culture of continuous improvement.
Encouraging collaboration and open communication can help address resistance to change.
Securing the necessary resources, such as training programs and technology investments, ensures that employees have the tools they need for successful troubleshooting.
Conclusion
Proactive troubleshooting techniques are essential for manufacturing success.
By preventing problems before they occur, manufacturers can save costs, enhance efficiency, and improve product quality.
Regular equipment maintenance, data monitoring, employee empowerment, and predictive maintenance are just a few of the strategies that can be employed.
While there may be challenges in implementing these techniques, the benefits far outweigh the obstacles.
Manufacturers who embrace proactive troubleshooting are better positioned to thrive in today’s competitive market, delivering superior products that meet customer demands.
資料ダウンロード
QCD管理受発注クラウド「newji」は、受発注部門で必要なQCD管理全てを備えた、現場特化型兼クラウド型の今世紀最高の受発注管理システムとなります。
ユーザー登録
受発注業務の効率化だけでなく、システムを導入することで、コスト削減や製品・資材のステータス可視化のほか、属人化していた受発注情報の共有化による内部不正防止や統制にも役立ちます。
NEWJI DX
製造業に特化したデジタルトランスフォーメーション(DX)の実現を目指す請負開発型のコンサルティングサービスです。AI、iPaaS、および先端の技術を駆使して、製造プロセスの効率化、業務効率化、チームワーク強化、コスト削減、品質向上を実現します。このサービスは、製造業の課題を深く理解し、それに対する最適なデジタルソリューションを提供することで、企業が持続的な成長とイノベーションを達成できるようサポートします。
製造業ニュース解説
製造業、主に購買・調達部門にお勤めの方々に向けた情報を配信しております。
新任の方やベテランの方、管理職を対象とした幅広いコンテンツをご用意しております。
お問い合わせ
コストダウンが利益に直結する術だと理解していても、なかなか前に進めることができない状況。そんな時は、newjiのコストダウン自動化機能で大きく利益貢献しよう!
(β版非公開)