- お役立ち記事
- Problems/case studies in powder processes and key points of troubleshooting techniques
Problems/case studies in powder processes and key points of troubleshooting techniques
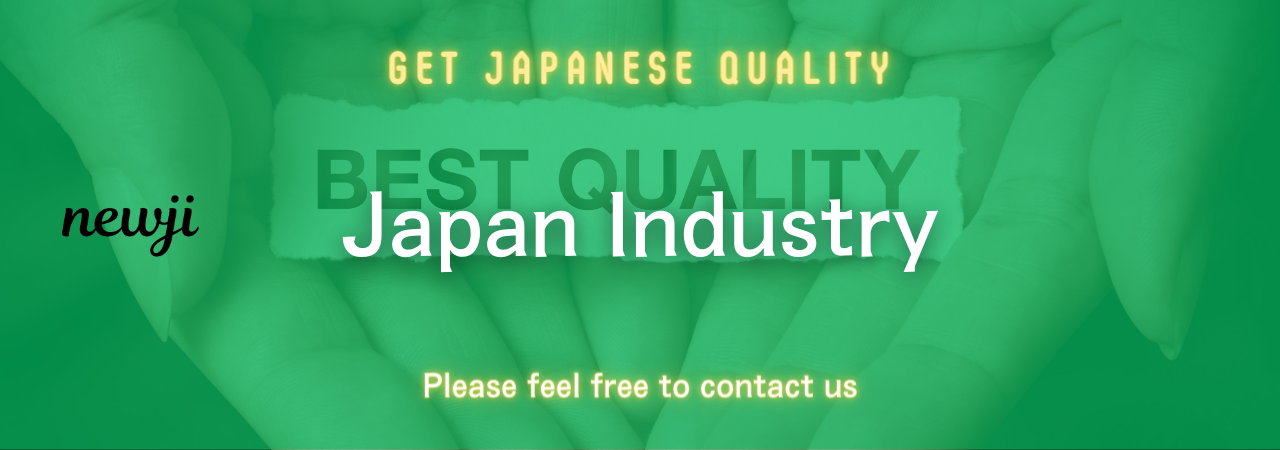
目次
Understanding Powder Processes
Powder processes play a crucial role in a variety of industries, from pharmaceuticals to food production, cosmetics, and beyond.
These processes involve handling fine particles, which are essential for creating products with the desired consistency, quality, and functionality.
However, managing powders effectively comes with a unique set of challenges that can affect the efficiency, cost, and safety of production.
Common Problems in Powder Processes
One of the most frequent problems in powder processing is segregation.
This occurs when particles of different sizes, shapes, or densities separate, leading to inconsistency in the final product.
Such inconsistencies can impact the effectiveness, appearance, and taste of products, particularly in the pharmaceutical and food industries.
Another problem is poor flowability, which can cause blockages in equipment, inconsistent filling of containers, and difficulties in transport.
This is particularly problematic for powders with irregular particle shapes or for those which tend to aggregate, forming clumps.
Dust formation is another significant issue.
It can pose health risks to workers, lead to product loss, and create hazardous environments due to the risk of dust explosions.
Effective dust control measures are critical in any powder processing operation to ensure safety and regulatory compliance.
Moreover, moisture sensitivity can seriously impact powder quality.
Excessive moisture can lead to clumping, spoilage, and reduced shelf life.
Conversely, too little moisture can lead to increased dust and electrostatic charges, complicating handling processes.
Case Studies of Powder Processing Challenges
It is beneficial to explore real-world scenarios to understand how powder processing challenges have been tackled successfully.
In one case study involving a pharmaceutical company, the issue of powder segregation was significantly affecting the dosage uniformity of a tablet product.
Through the use of particle size reduction techniques and blend uniformity testing, the company improved product consistency and compliance with regulatory requirements.
In another instance, a food processing company faced serious flowability issues with a new seasoning powder.
By implementing flow aids and aeration techniques, they managed to improve the powder’s flow characteristics, which increased efficiency and reduced downtime in the production line.
A third case study involved a cosmetic manufacturer dealing with dust formation during the production of a powdered foundation.
By installing dust collectors and using anti-dust additives, they were able to mitigate this issue, leading to a safer workplace and a cleaner production process.
Key Points of Troubleshooting Techniques
Effectively troubleshooting powder processing issues requires a systematic approach.
First, it’s essential to conduct thorough testing to identify the root cause of the problem.
This might involve analyzing the properties of the powder, such as particle size distribution, moisture content, and cohesive strength.
Once the issue is identified, modifications to the process or material can be considered.
For instance, altering the particle size through milling or employing different drying methods to manage moisture levels could resolve flowability and segregation issues.
Technological interventions, such as installing improved dust extraction systems or integrating real-time monitoring sensors, can significantly reduce dust formation and enhance safety.
Such investments not only resolve immediate issues but also improve overall operational efficiency.
Incorporating additives tailored to enhance flow or reduce electrostatic charge can also be effective.
These additives are particularly useful when dealing with powders known to agglomerate or when conditions fluctuate leading to inconsistent powder behavior.
Importance of Regular Maintenance and Training
Ensuring that equipment is regularly maintained and calibrated is a critical yet often overlooked aspect of effective powder processing.
Regular maintenance helps to detect wear and tear early, preventing breakdowns that can exacerbate process issues, such as blockages or inefficiencies.
Worker training is equally important, as it empowers employees to handle materials safely, recognize potential issues early, and follow the best practices for maintaining quality and safety standards.
Training can also foster a culture of continuous improvement within the workforce, encouraging proactive rather than reactive problem-solving.
Conclusion
Powder processes are an integral part of many industries, and understanding the common challenges and troubleshooting techniques is vital for maintaining efficiency, quality, and safety.
Through careful analysis, technological interventions, and proactive maintenance practices, many of the common problems associated with powder processing can be effectively managed.
Continuous innovation and adaptation to new technologies will further enhance the ability to deal with these challenges, securing a competitive edge in the market.
資料ダウンロード
QCD調達購買管理クラウド「newji」は、調達購買部門で必要なQCD管理全てを備えた、現場特化型兼クラウド型の今世紀最高の購買管理システムとなります。
ユーザー登録
調達購買業務の効率化だけでなく、システムを導入することで、コスト削減や製品・資材のステータス可視化のほか、属人化していた購買情報の共有化による内部不正防止や統制にも役立ちます。
NEWJI DX
製造業に特化したデジタルトランスフォーメーション(DX)の実現を目指す請負開発型のコンサルティングサービスです。AI、iPaaS、および先端の技術を駆使して、製造プロセスの効率化、業務効率化、チームワーク強化、コスト削減、品質向上を実現します。このサービスは、製造業の課題を深く理解し、それに対する最適なデジタルソリューションを提供することで、企業が持続的な成長とイノベーションを達成できるようサポートします。
オンライン講座
製造業、主に購買・調達部門にお勤めの方々に向けた情報を配信しております。
新任の方やベテランの方、管理職を対象とした幅広いコンテンツをご用意しております。
お問い合わせ
コストダウンが利益に直結する術だと理解していても、なかなか前に進めることができない状況。そんな時は、newjiのコストダウン自動化機能で大きく利益貢献しよう!
(Β版非公開)