- お役立ち記事
- Process control to prevent short shots that quality control department leaders in the plastic molding industry should know
Process control to prevent short shots that quality control department leaders in the plastic molding industry should know
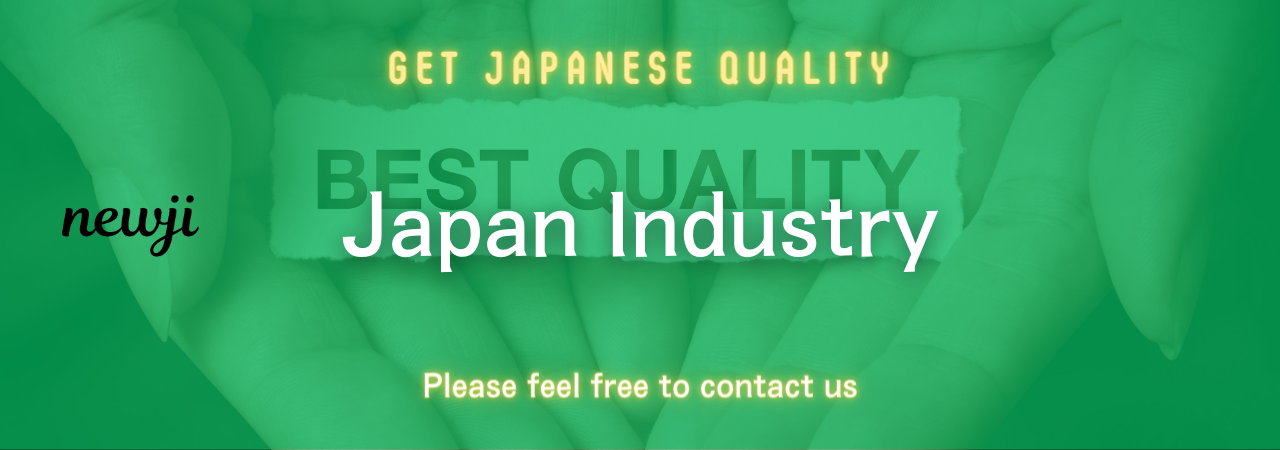
目次
Understanding Short Shots in Plastic Molding
Short shots in plastic molding are a common issue faced in the industry, and they occur when a molded part is incomplete because the plastic material did not completely fill the mold cavity.
This can lead to defective products, increased waste, and higher costs.
To effectively prevent short shots, it’s crucial for quality control department leaders to understand the root causes of this problem and implement effective process control measures.
Identifying the Root Causes
There are several factors that can contribute to short shots, and identifying these can help in devising strategies to prevent them.
One common cause is inadequate material flow within the mold.
If the plastic material cannot reach all parts of the mold before it starts to solidify, a short shot can occur.
Another potential culprit is insufficient mold temperature.
When the mold is not heated properly, the plastic material may solidify too quickly, preventing it from fully filling the mold.
In addition, improper venting in the mold can also result in short shots.
Air trapped in the mold can create resistance, hindering the complete flow of plastic material.
Recognizing these factors can help you pinpoint the specific issues within your production process that might be causing short shots.
Implementing Effective Process Control
Process control is the practice of managing and regulating the conditions within the manufacturing process to ensure consistent quality output.
Preventing short shots requires implementing robust process control measures tailored specifically to the factors identified as causing the issue.
Optimizing Material Flow
Maximizing material flow is one of the primary steps toward preventing short shots.
This can be achieved by ensuring that the plastic material is at the correct viscosity.
Proper temperature control of both the material and the mold is necessary to maintain the right viscosity.
Adjusting the injection speed can also optimize material flow.
A higher injection speed might be required to ensure that the material fills the mold before solidification occurs.
Use scientific molding techniques to assess and adjust these parameters accurately.
Ensuring Proper Mold Heating
Maintaining the correct mold temperature is crucial for preventing short shots.
Use temperature controls to ensure that the mold is evenly heated.
Regularly calibrate your heating equipment to prevent deviations from the desired temperature settings.
Monitoring thermal imaging of molds can help in identifying cold spots, which might hinder the flow of the material.
By addressing these cold areas, you can promote even material flow within the mold.
Improving Mold Ventilation
Ensuring that your molds have adequate venting can greatly reduce the risk of short shots.
If air trapped within the mold hinders plastic flow, venting should be evaluated and adapted to allow for the smooth expulsion of air.
Regularly check and clean vents to prevent blockages that could interfere with venting functions.
Consider using vacuum venting systems for molds with complex geometries where traditional venting may not be sufficient.
Training and Monitoring
Empower your team with comprehensive training and ongoing monitoring to further safeguard against short shots.
Training should emphasize the importance of process control and offer guidance on identifying and responding to potential short shot scenarios quickly.
Document and follow a standard operating procedure (SOP) that covers all aspects of process control related to short shots.
Use data from monitoring systems to track performance metrics related to mold filling.
Analyze these metrics regularly to detect trends or variations that could indicate a risk of short shots.
Leveraging Technology
Advanced technology can play a vital role in preventing short shots by offering precise control and insight into the process.
Utilize simulation software to predict and troubleshoot potential short shot scenarios before they occur on the production line.
This allows you to optimize your process settings and identify potential problem areas in the mold and material selection stages.
Implement automated process control systems that can adjust parameters in real time based on data feedback, ensuring a consistent and controlled molding environment.
Conclusion
Short shots are a challenge in the plastic molding industry, but with a solid understanding of their causes and a commitment to process control, quality control department leaders can effectively prevent them.
Optimize material flow, ensure proper mold heating, and improve ventilation to mitigate the risk factors of short shots.
Incorporate training, monitoring, and technology solutions to maintain a high standard of quality control, leading to fewer defects and more efficient production.
資料ダウンロード
QCD調達購買管理クラウド「newji」は、調達購買部門で必要なQCD管理全てを備えた、現場特化型兼クラウド型の今世紀最高の購買管理システムとなります。
ユーザー登録
調達購買業務の効率化だけでなく、システムを導入することで、コスト削減や製品・資材のステータス可視化のほか、属人化していた購買情報の共有化による内部不正防止や統制にも役立ちます。
NEWJI DX
製造業に特化したデジタルトランスフォーメーション(DX)の実現を目指す請負開発型のコンサルティングサービスです。AI、iPaaS、および先端の技術を駆使して、製造プロセスの効率化、業務効率化、チームワーク強化、コスト削減、品質向上を実現します。このサービスは、製造業の課題を深く理解し、それに対する最適なデジタルソリューションを提供することで、企業が持続的な成長とイノベーションを達成できるようサポートします。
オンライン講座
製造業、主に購買・調達部門にお勤めの方々に向けた情報を配信しております。
新任の方やベテランの方、管理職を対象とした幅広いコンテンツをご用意しております。
お問い合わせ
コストダウンが利益に直結する術だと理解していても、なかなか前に進めることができない状況。そんな時は、newjiのコストダウン自動化機能で大きく利益貢献しよう!
(Β版非公開)