- お役立ち記事
- Process Design Strategies Combining Safety Engineering and Risk Assessment
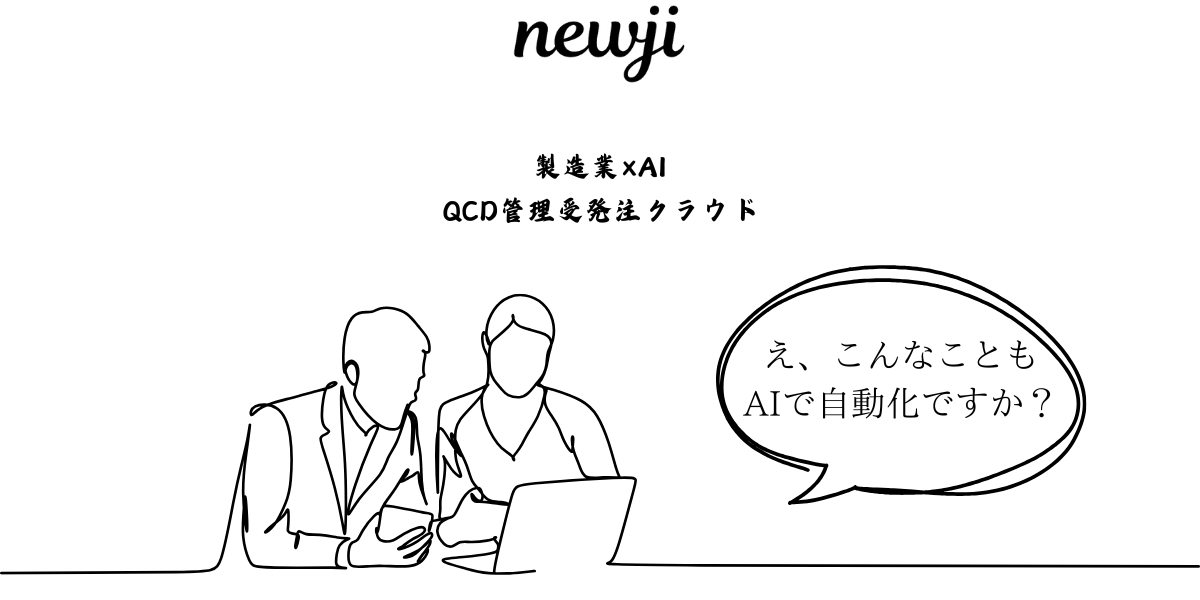
Process Design Strategies Combining Safety Engineering and Risk Assessment
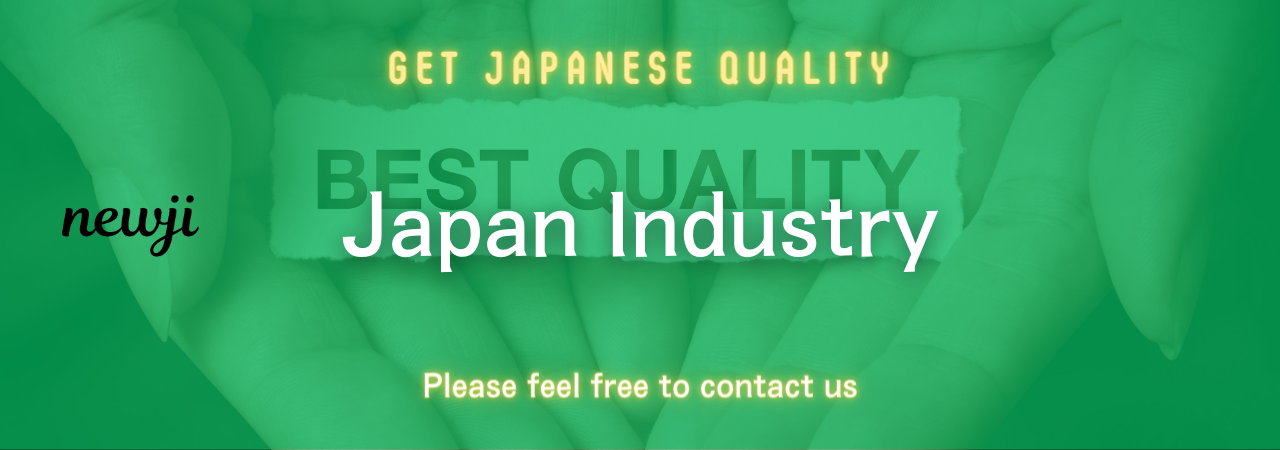
目次
Understanding Process Design Strategies
Process design is an essential aspect of engineering that ensures the smooth operation of systems by integrating safety measures and risk management.
Combining safety engineering and risk assessment within process design strategies is necessary because it minimizes potential hazards and optimizes system efficiency.
By understanding these strategies, industries can achieve their operational goals while maintaining a high standard of safety.
The Role of Safety Engineering
Safety engineering is a discipline that focuses on identifying, analyzing, and mitigating risks in the design, production, and operational stages of products or systems.
The primary objective of safety engineering is to ensure that systems and processes do not pose a threat to people, equipment, or the environment.
Incorporating safety engineering into process design means taking a proactive approach to identify potential hazards.
By anticipating these risks, engineers can implement safety measures early in the design process.
This can include physical barriers, safety protocols, and redundant systems to prevent accidents.
The implementation of these systems helps reduce the likelihood of incidents that could jeopardize safety or operational continuity.
The Importance of Risk Assessment
Risk assessment is a systematic process used to identify and evaluate risks associated with a particular process or decision.
The process involves identifying potential hazards, assessing the likelihood and impact of these hazards, and developing strategies to manage and mitigate them effectively.
Incorporating risk assessment into process design strategies ensures that decision-makers are fully aware of potential risks before they become problems.
This is achieved by quantifying the risks and prioritizing them based on severity and probability.
Once risks are understood, strategies can be developed to reduce their impact or likelihood.
Integrating Safety Engineering and Risk Assessment
When designing a process, integrating safety engineering and risk assessment can result in a comprehensive approach to safety and efficiencies.
This combination allows for the identification of risks at every stage, from initial concept through to implementation and operation.
1. **Early Identification of Risks**: By identifying hazards early in the design phase, it is possible to avoid common pitfalls that can lead to safety concerns later.
2. **Holistic Safety Planning**: Integrating these methodologies allows for a seamless strategy where safety is considered in every aspect of the design.
3. **Improved Decision-Making**: With a thorough understanding of potential risks, engineers can make informed decisions that balance safety with operational effectiveness.
4. **Cost-Effectiveness**: Proactive risk management and safety design can reduce costs related to accidents, redesigns, and operational downtime.
Key Elements of Process Design Strategies
Certain key elements ensure effective and safe process design strategies integrating both safety engineering and risk assessment:
1. **Hazard Identification and Analysis**: This involves using techniques like Fault Tree Analysis (FTA) and Failure Mode and Effects Analysis (FMEA) to pinpoint potential hazards.
2. **Risk Evaluation and Prioritization**: Determine which risks are acceptable and which require mitigation.
3. **Designing for Safety**: Incorporate safety features and protective systems into the design, following principles such as inherent safety (designing out hazards rather than managing them).
4. **Continuous Monitoring and Review**: Systems should be continuously monitored and updated to accommodate new risks or changes in operational circumstances.
Implementing a Safety-First Culture
To successfully implement process design strategies that effectively incorporate safety engineering and risk assessment, companies must foster a culture that prioritizes safety above all.
– **Training and Education**: Regular training programs should be provided to ensure all employees understand safety processes and risk management principles.
– **Communication**: Open lines of communication encourage reporting of potential hazards or failures, promoting a culture of proactive risk management.
– **Leadership Support**: Leadership must visibly support safety initiatives and provide the necessary resources to implement safety measures effectively.
Benefits of Effective Process Design Strategies
The benefits of implementing these integrated strategies in process design include:
– **Enhanced Safety**: Fewer incidents and accidents result from a robust safety design approach.
– **Operational Efficiency**: Processes function more efficiently and effectively when potential disruptions are minimized.
– **Regulatory Compliance**: Ensures adherence to safety and environmental regulations, avoiding potential legal and financial penalties.
Ultimately, combining safety engineering with risk assessment in process design strategies leads to a safer, more efficient, and sustainable operational environment.
This integration not only protects personnel and assets but also enhances the overall productivity and reputation of the organization.
資料ダウンロード
QCD調達購買管理クラウド「newji」は、調達購買部門で必要なQCD管理全てを備えた、現場特化型兼クラウド型の今世紀最高の購買管理システムとなります。
ユーザー登録
調達購買業務の効率化だけでなく、システムを導入することで、コスト削減や製品・資材のステータス可視化のほか、属人化していた購買情報の共有化による内部不正防止や統制にも役立ちます。
NEWJI DX
製造業に特化したデジタルトランスフォーメーション(DX)の実現を目指す請負開発型のコンサルティングサービスです。AI、iPaaS、および先端の技術を駆使して、製造プロセスの効率化、業務効率化、チームワーク強化、コスト削減、品質向上を実現します。このサービスは、製造業の課題を深く理解し、それに対する最適なデジタルソリューションを提供することで、企業が持続的な成長とイノベーションを達成できるようサポートします。
オンライン講座
製造業、主に購買・調達部門にお勤めの方々に向けた情報を配信しております。
新任の方やベテランの方、管理職を対象とした幅広いコンテンツをご用意しております。
お問い合わせ
コストダウンが利益に直結する術だと理解していても、なかなか前に進めることができない状況。そんな時は、newjiのコストダウン自動化機能で大きく利益貢献しよう!
(Β版非公開)