- お役立ち記事
- Process for prompt response to quality problems in the manufacturing industry and planning measures to prevent recurrence
月間76,176名の
製造業ご担当者様が閲覧しています*
*2025年3月31日現在のGoogle Analyticsのデータより
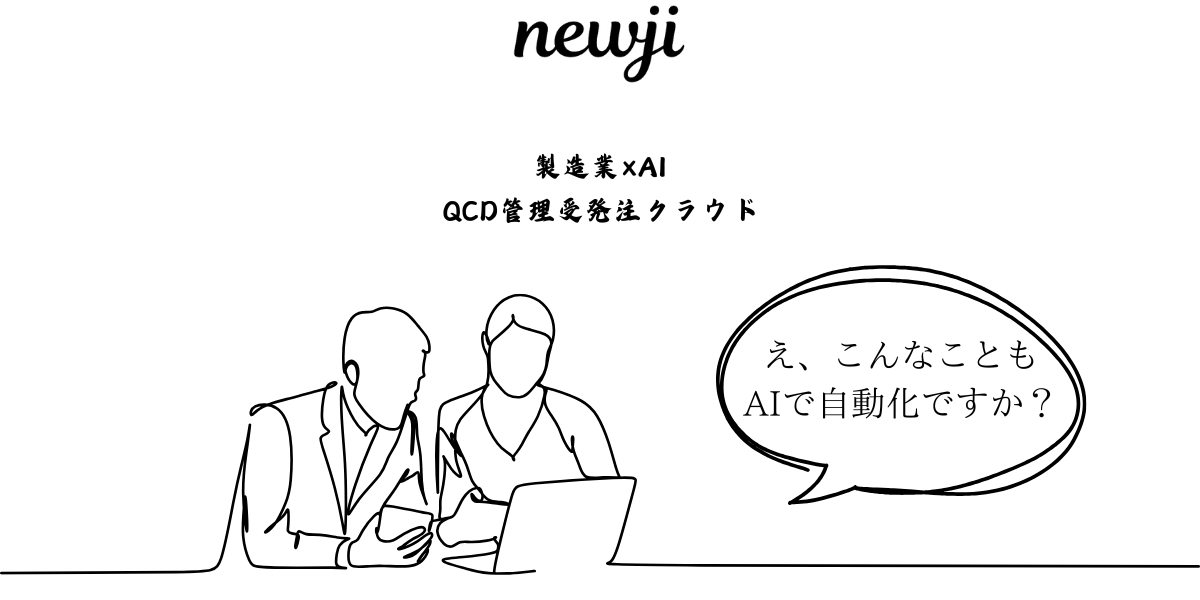
Process for prompt response to quality problems in the manufacturing industry and planning measures to prevent recurrence
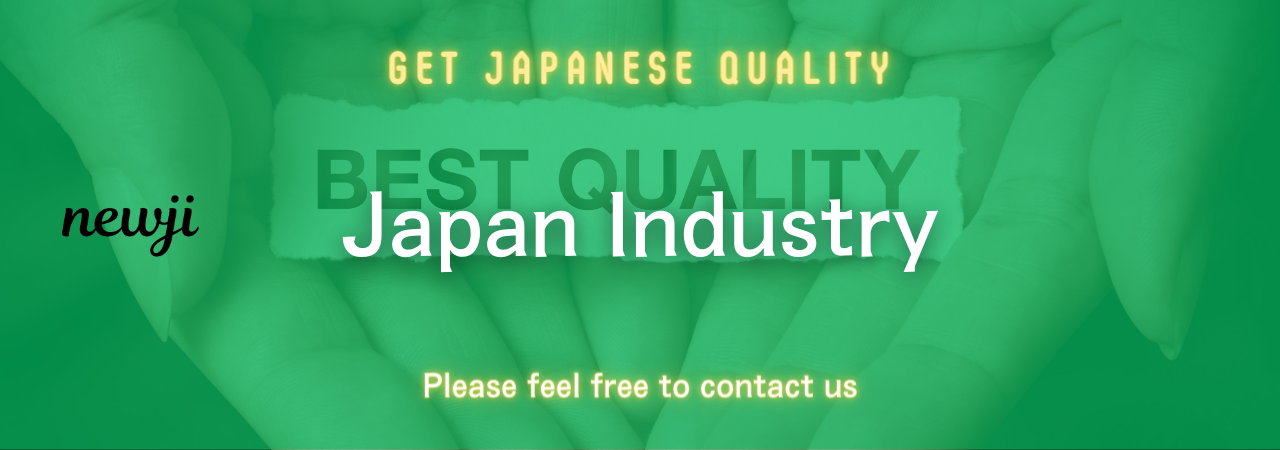
In the manufacturing industry, quality problems can arise unexpectedly, leading to disrupted production schedules and financial losses.
Responding promptly and effectively to these issues is crucial to maintaining operational efficiency and customer satisfaction.
This article outlines a robust process for addressing quality problems quickly and discusses strategies to prevent their recurrence.
目次
Identifying Quality Problems
The first step in addressing quality issues is accurate identification.
Manufacturers must employ rigorous monitoring techniques to spot defects early.
This involves the use of automated systems and human inspection at various production stages.
Quality problems could range from material defects to inconsistencies in the production process.
Data Collection and Analysis
Gathering data is essential to understand the scope and nature of the quality problem.
This may include production reports, inspection logs, and customer feedback.
Once collected, data analysis tools can help identify patterns and root causes.
This step ensures the problem is understood fully before corrective actions are initiated.
Immediate Response to Quality Problems
When a quality issue is identified, the immediate goal is to contain the problem and minimize its impact.
This involves halting production if necessary to prevent further defects.
Containment Measures
Containment involves isolating defective products and stopping their distribution.
Affected lots should be quarantined, and a review of production batches should be conducted to determine the extent of the problem.
Prompt communication with all stakeholders, including suppliers and customers, is essential to maintain transparency and address concerns.
Root Cause Analysis (RCA)
A thorough investigation is needed to pinpoint the root cause of the quality problem.
Techniques such as the 5 Whys, Fishbone Diagram, and Failure Mode and Effects Analysis (FMEA) can be used to identify fundamental issues.
Understanding the root cause is critical to developing effective corrective actions.
Implementing Corrective Actions
Developing and implementing corrective actions to address the root cause of a quality problem ensures it does not recur.
This phase involves both short-term fixes and long-term improvements.
Short-Term Corrective Actions
Short-term actions may include immediate adjustments to the production process, equipment calibrations, or changes in material handling.
Temporary solutions help resume production quickly while longer-term strategies are developed.
Long-Term Preventative Measures
Long-term measures involve comprehensive changes to processes, equipment, or materials to prevent the recurrence of the issue.
This may include:
– Redesigning components
– Updating standard operating procedures
– Enhancing employee training programs
– Implementing more rigorous quality control checks
Monitoring and Reviewing Effectiveness
Once corrective and preventative actions are in place, continuous monitoring is essential to ensure their effectiveness.
This involves regular inspections, audits, and feedback loops.
Regular Audits
Conducting regular audits helps ensure that new procedures are followed and that improvements are maintained.
Audit findings should be documented, and any deviations should be addressed immediately.
Feedback Mechanisms
Establishing channels for feedback from production teams and customers provides additional data on the effectiveness of corrective measures.
This feedback can highlight areas for further improvement.
Planning for Future Issues
Even with the best processes in place, quality problems can still occur.
Manufacturers must be prepared to respond swiftly to any future issues.
Developing a Quality Risk Management Plan
A quality risk management plan involves identifying potential risks, assessing their impact, and developing mitigation strategies.
This proactive approach helps in anticipating problems before they arise and reducing their impact.
Investing in Technology
Advanced technologies such as IoT, machine learning, and AI can aid in early detection and prevention of quality issues.
Investing in these technologies ensures better accuracy in monitoring and quicker responses to problems.
Conclusion
In the manufacturing industry, a prompt response to quality problems and planning measures to prevent their recurrence are crucial.
By employing a structured approach to identifying, responding to, and preventing quality issues, manufacturers can maintain high standards and customer satisfaction.
Investing in continuous improvement and advanced technology further strengthens a company’s ability to handle quality challenges efficiently.
Effective quality management is not just about fixing problems; it’s about building resilient processes that minimize the chances of issues occurring in the first place.
By embedding quality into every step of the manufacturing process, companies can achieve long-term success and sustain their competitive edge.
資料ダウンロード
QCD管理受発注クラウド「newji」は、受発注部門で必要なQCD管理全てを備えた、現場特化型兼クラウド型の今世紀最高の受発注管理システムとなります。
ユーザー登録
受発注業務の効率化だけでなく、システムを導入することで、コスト削減や製品・資材のステータス可視化のほか、属人化していた受発注情報の共有化による内部不正防止や統制にも役立ちます。
NEWJI DX
製造業に特化したデジタルトランスフォーメーション(DX)の実現を目指す請負開発型のコンサルティングサービスです。AI、iPaaS、および先端の技術を駆使して、製造プロセスの効率化、業務効率化、チームワーク強化、コスト削減、品質向上を実現します。このサービスは、製造業の課題を深く理解し、それに対する最適なデジタルソリューションを提供することで、企業が持続的な成長とイノベーションを達成できるようサポートします。
製造業ニュース解説
製造業、主に購買・調達部門にお勤めの方々に向けた情報を配信しております。
新任の方やベテランの方、管理職を対象とした幅広いコンテンツをご用意しております。
お問い合わせ
コストダウンが利益に直結する術だと理解していても、なかなか前に進めることができない状況。そんな時は、newjiのコストダウン自動化機能で大きく利益貢献しよう!
(β版非公開)