- お役立ち記事
- Process improvement measures to reduce lead time in purchasing planning
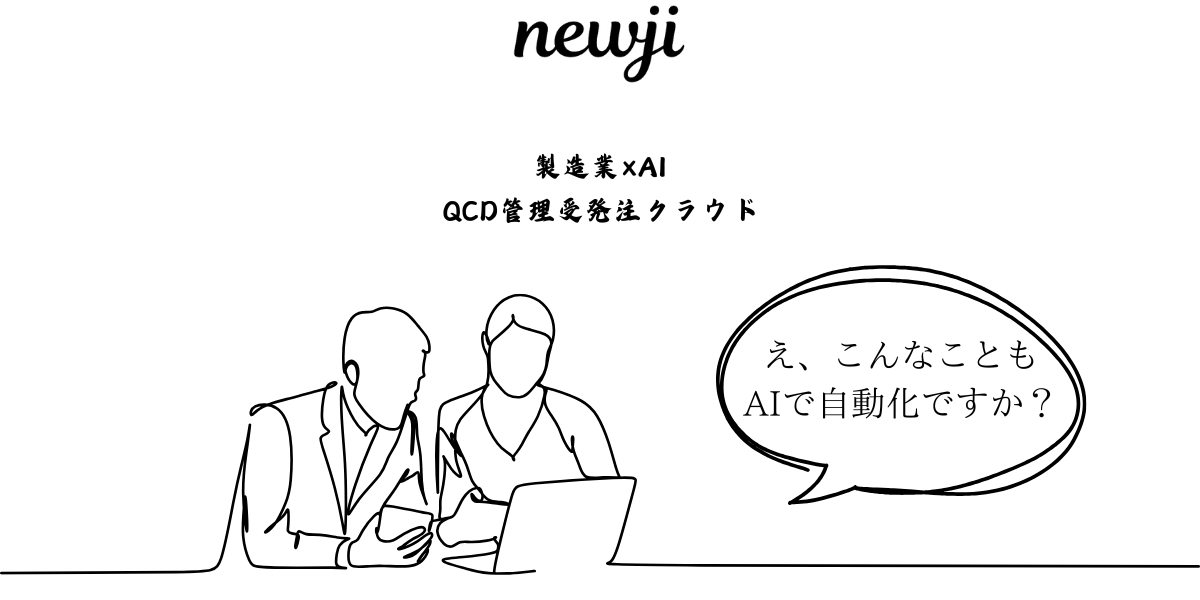
Process improvement measures to reduce lead time in purchasing planning
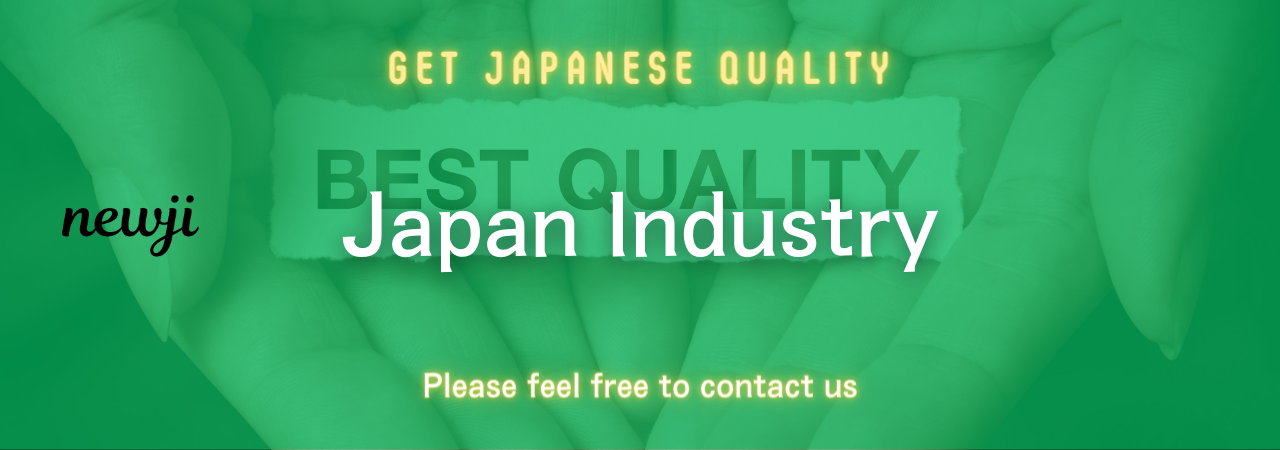
目次
Understanding Lead Time in Purchasing Planning
Lead time in purchasing planning is the amount of time that passes from the moment an order is placed until the moment it is received and ready for use or sale.
It encompasses several stages, including procurement, manufacturing, shipping, and delivery.
Managing lead time is crucial for maintaining inventory levels, meeting customer demands, and improving operational efficiency.
When lead times are optimized, businesses can better align supply with demand and avoid the pitfalls of stockouts or overstocking.
Why Reducing Lead Time Matters
Reducing lead time is vital because it can lead to improved customer satisfaction, cost savings, and better resource utilization.
With shorter lead times, companies can respond more quickly to market changes and customer needs.
This agility can provide a competitive edge in an increasingly dynamic business landscape.
Moreover, reduced lead time can lower carrying costs, minimize the risk of inventory obsolescence, and improve cash flow by speeding up the time between investment and return.
Identifying Bottlenecks in the Purchasing Process
The first step in improving lead time is to identify bottlenecks within the purchasing process.
Bottlenecks are stages in the process where delays occur, affecting the overall lead time.
Analyzing Supplier Performance
One common area of concern is supplier performance.
Delays in the supply chain often begin with suppliers who fail to deliver materials on time.
It is essential to evaluate suppliers based on their reliability, quality, and lead time performance.
Working proactively with suppliers to address any issues or negotiating terms might help streamline this part of the process.
Assessing Internal Processes
Internal processes can also contribute to lead time delays.
Inefficiencies in order processing, approval workflows, or communication channels can result in unnecessary waiting times.
Conducting a thorough review of these areas can highlight inefficiencies that need addressing.
Implementing a project management approach, where processes are clearly mapped and responsibilities assigned, can help mitigate these internal delays.
Strategies for Reducing Lead Time
Once bottlenecks are identified, the next step is to implement strategies to reduce lead time.
Optimizing Inventory Management
Effective inventory management is central to reducing lead time.
Implementing an inventory management system that provides real-time data can significantly boost efficiency.
This allows businesses to track inventory levels, set reorder points, and predict future needs with greater accuracy.
Leveraging Technology
Technology can be a powerful ally in reducing lead time.
Implementing ERP (Enterprise Resource Planning) systems can integrate different processes and provide a comprehensive overview of operations.
These systems help automate various tasks, reducing manual errors and enhancing the speed and precision of order processing.
Building Strong Supplier Relationships
Establishing strong relationships with suppliers can lead to better terms and quicker lead times.
Regular communication and collaboration with suppliers can ensure they understand your expectations and the impact of lead time on your business.
In some cases, strategic partnerships or contracts can be developed to align supplier activities closely with business needs.
Monitoring and Continuous Improvement
Optimizing lead time is not a one-time task but an ongoing process.
Continuous monitoring and improvement efforts are essential to ensure long-term success.
Evaluating Performance with Metrics
Measuring performance through Key Performance Indicators (KPIs) can provide valuable insights into lead time reduction efforts.
KPIs such as Order Cycle Time, Fill Rate, and Supplier Lead Time can help track improvements or highlight areas for further enhancement.
Conducting Regular Reviews
Regular reviews of the purchasing processes and performance metrics can identify new potential bottlenecks or inefficiencies.
By continuously assessing both supplier performance and internal processes, businesses can make informed decisions to maintain or further reduce lead times.
The Role of Flexibility and Resilience
In today’s rapidly changing business environment, flexibility and resilience are more essential than ever.
Adapting to Changing Circumstances
Being able to adapt quickly to changes in supply or demand is vital for maintaining optimized lead times.
This may involve using flexible contracts with suppliers, maintaining backup suppliers, or employing agile methodologies within the purchasing department.
Resilience Planning
Building resilience into purchasing planning can help a business withstand unexpected disruptions.
Strategies such as diversifying suppliers, maintaining a buffer stock, or adopting just-in-time purchasing can reduce vulnerability and ensure continuity of operations even when external challenges arise.
Conclusion
Reducing lead time in purchasing planning is a multifaceted challenge that requires a strategic and ongoing approach.
By identifying bottlenecks, leveraging technology, and fostering strong supplier relationships, businesses can optimize their lead times.
Ensuring continuous improvement and building flexibility and resilience into the purchasing process will equip companies to thrive in a competitive marketplace.
Ultimately, these efforts not only enhance operational efficiency and customer satisfaction but also contribute significantly to the company’s bottom line.
資料ダウンロード
QCD調達購買管理クラウド「newji」は、調達購買部門で必要なQCD管理全てを備えた、現場特化型兼クラウド型の今世紀最高の購買管理システムとなります。
ユーザー登録
調達購買業務の効率化だけでなく、システムを導入することで、コスト削減や製品・資材のステータス可視化のほか、属人化していた購買情報の共有化による内部不正防止や統制にも役立ちます。
NEWJI DX
製造業に特化したデジタルトランスフォーメーション(DX)の実現を目指す請負開発型のコンサルティングサービスです。AI、iPaaS、および先端の技術を駆使して、製造プロセスの効率化、業務効率化、チームワーク強化、コスト削減、品質向上を実現します。このサービスは、製造業の課題を深く理解し、それに対する最適なデジタルソリューションを提供することで、企業が持続的な成長とイノベーションを達成できるようサポートします。
オンライン講座
製造業、主に購買・調達部門にお勤めの方々に向けた情報を配信しております。
新任の方やベテランの方、管理職を対象とした幅広いコンテンツをご用意しております。
お問い合わせ
コストダウンが利益に直結する術だと理解していても、なかなか前に進めることができない状況。そんな時は、newjiのコストダウン自動化機能で大きく利益貢献しよう!
(Β版非公開)