- お役立ち記事
- Process improvement method for streamlining and optimizing FA equipment design work
月間76,176名の
製造業ご担当者様が閲覧しています*
*2025年3月31日現在のGoogle Analyticsのデータより
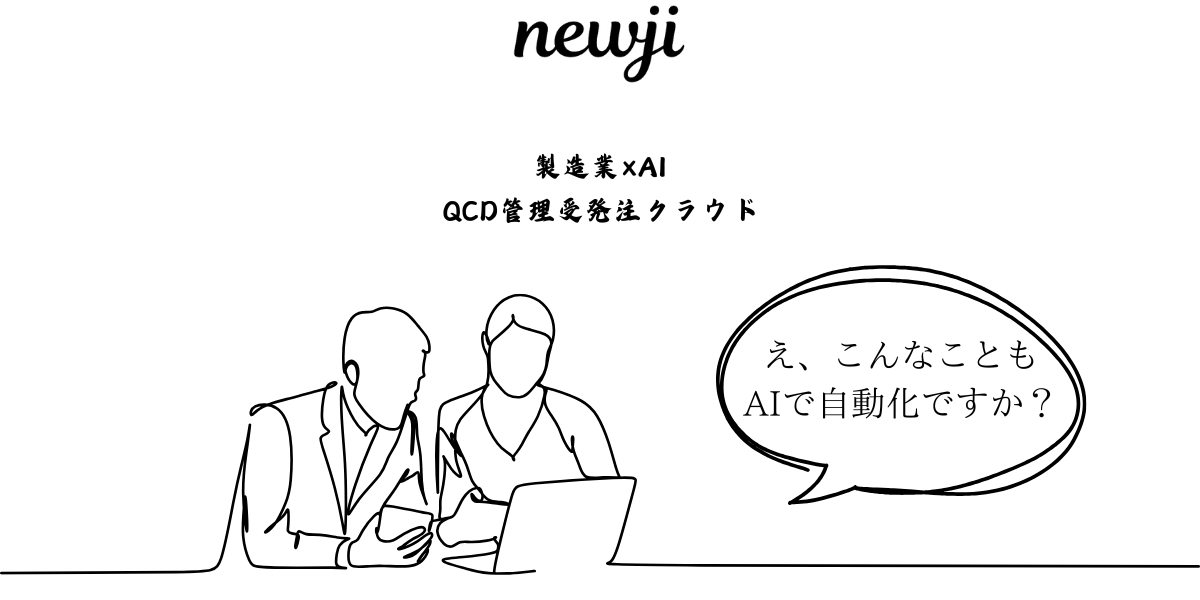
Process improvement method for streamlining and optimizing FA equipment design work
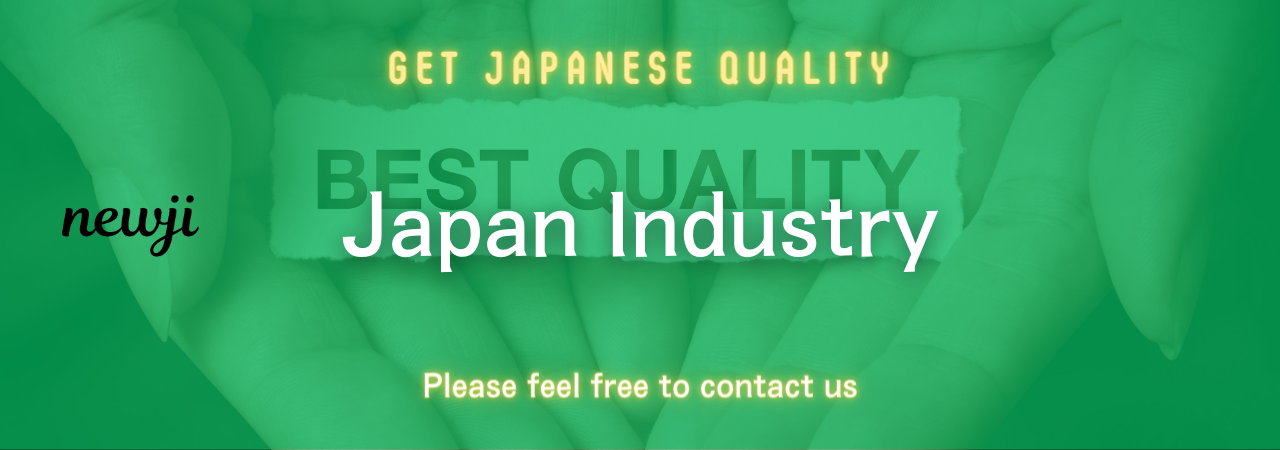
目次
Understanding the Basics of FA Equipment Design
The design of Factory Automation (FA) equipment plays a vital role in manufacturing processes.
FA equipment streamlines production, reduces human error, and enhances efficiency.
However, designing such equipment can be complex and time-consuming.
To optimize the design process, understanding the fundamentals of FA equipment is essential.
Factory Automation involves using control systems for operating equipment, processes in factories, and other industrial automation areas.
This technology encompasses programmable logic controllers, computers, and robots to handle processes or machinery.
Thus, the design process must consider various components, including hardware, software, and integration systems.
The Importance of Process Improvement in FA Design
Process improvement involves analyzing and enhancing existing practices to boost efficiency and effectiveness.
In the context of FA equipment design, process improvement can lead to reduced costs, faster time-to-market, enhanced design quality, and decreased errors.
By refining the methods used in design work, companies can focus on delivering top-tier FA equipment.
This improvement ultimately benefits production lines, reduces downtime, and increases profitability.
Key Steps for Streamlining FA Equipment Design
Let’s delve into some practical steps to streamline and optimize FA equipment design work:
1. Conducting Thorough Research
Before starting the design process, gather detailed information about the equipment’s purpose and requirements.
Engage with clients and stakeholders to understand their needs and expectations.
Research existing solutions to identify what works well and what doesn’t, offering insight into potential design improvements.
2. Implementing Standardization
Standardization involves using uniform processes and components across various projects.
This practice decreases complexity, reduces costs, and shortens design timelines.
With standardized parts and processes, engineers can focus on customization where it matters most, enhancing design efficacy.
3. Using Advanced Software Tools
Leverage advanced design software to automate time-consuming tasks, ensuring higher precision and efficiency.
CAD software, for instance, allows engineers to visualize and modify designs with ease.
Simulation tools can test designs in virtual environments, predicting performance before physical prototypes are built.
4. Encouraging a Collaborative Work Environment
Foster a culture of collaboration among team members.
Cross-functional teams bring varied expertise to the table, enhancing creativity and problem-solving.
Use collaborative tools and platforms for better communication and information sharing, ensuring every member is aligned with project goals.
5. Adopting Agile Methodologies
Agile methodologies focus on iterative progress, flexibility, and customer feedback.
Break the design process into smaller, manageable tasks and deliver in increments.
Regular review meetings and client feedback ensure that designs remain aligned with customer expectations, and adjustments can be made efficiently.
Optimizing the Optimization Process
Effective process improvement can transform FA equipment design work.
However, the optimization process itself can benefit from continuous enhancement.
Here are ways to optimize the optimization process:
Evaluating and Measuring Performance
Regular assessment of the design processes ensures that improvements are effective.
Set Key Performance Indicators (KPIs) to measure success.
Performance metrics can include time-to-market, cost savings, error rates, and overall equipment effectiveness (OEE).
Continuous Training and Development
Invest in regular training and development programs for design engineers.
Keeping the team updated with the latest trends, tools, and technologies is crucial for staying competitive.
Training results in a more skilled workforce capable of innovative problem-solving.
Encouraging Innovation and Adaptability
Create an environment that encourages innovation by rewarding creative ideas and new approaches.
Adaptability is key in a dynamic industry; engineers should feel comfortable proposing novel solutions without fear of failure.
Challenges in FA Equipment Design
Despite well-laid plans, challenges in FA equipment design can arise:
Managing Complex Systems
The complexity of integrating different systems and components can lead to design bottlenecks.
Adequate planning and coordination with experienced engineers help mitigate these complexities.
Balancing Cost and Quality
While reducing costs is a primary goal, maintaining equipment quality is equally important.
Finding the balance between affordability and robustness requires strategic sourcing and design decisions.
Ensuring Compliance with Standards
FA equipment must comply with industry standards and regulations for safety and performance.
Regular audits and adherence to compliance protocols are necessary to avoid legal and operational setbacks.
Conclusion
Optimizing the design work of FA equipment involves a combination of strategic planning, innovative methodologies, and a commitment to continuous improvement.
By following the outlined steps, companies can ensure that their design processes are efficient, cost-effective, and capable of producing high-quality automation equipment.
Moreover, fostering a culture of collaboration and adaptability ensures that teams can address challenges and meet evolving market demands effectively.
資料ダウンロード
QCD管理受発注クラウド「newji」は、受発注部門で必要なQCD管理全てを備えた、現場特化型兼クラウド型の今世紀最高の受発注管理システムとなります。
ユーザー登録
受発注業務の効率化だけでなく、システムを導入することで、コスト削減や製品・資材のステータス可視化のほか、属人化していた受発注情報の共有化による内部不正防止や統制にも役立ちます。
NEWJI DX
製造業に特化したデジタルトランスフォーメーション(DX)の実現を目指す請負開発型のコンサルティングサービスです。AI、iPaaS、および先端の技術を駆使して、製造プロセスの効率化、業務効率化、チームワーク強化、コスト削減、品質向上を実現します。このサービスは、製造業の課題を深く理解し、それに対する最適なデジタルソリューションを提供することで、企業が持続的な成長とイノベーションを達成できるようサポートします。
製造業ニュース解説
製造業、主に購買・調達部門にお勤めの方々に向けた情報を配信しております。
新任の方やベテランの方、管理職を対象とした幅広いコンテンツをご用意しております。
お問い合わせ
コストダウンが利益に直結する術だと理解していても、なかなか前に進めることができない状況。そんな時は、newjiのコストダウン自動化機能で大きく利益貢献しよう!
(β版非公開)