- お役立ち記事
- Process improvement of wax melt mixing and coarse graining technology
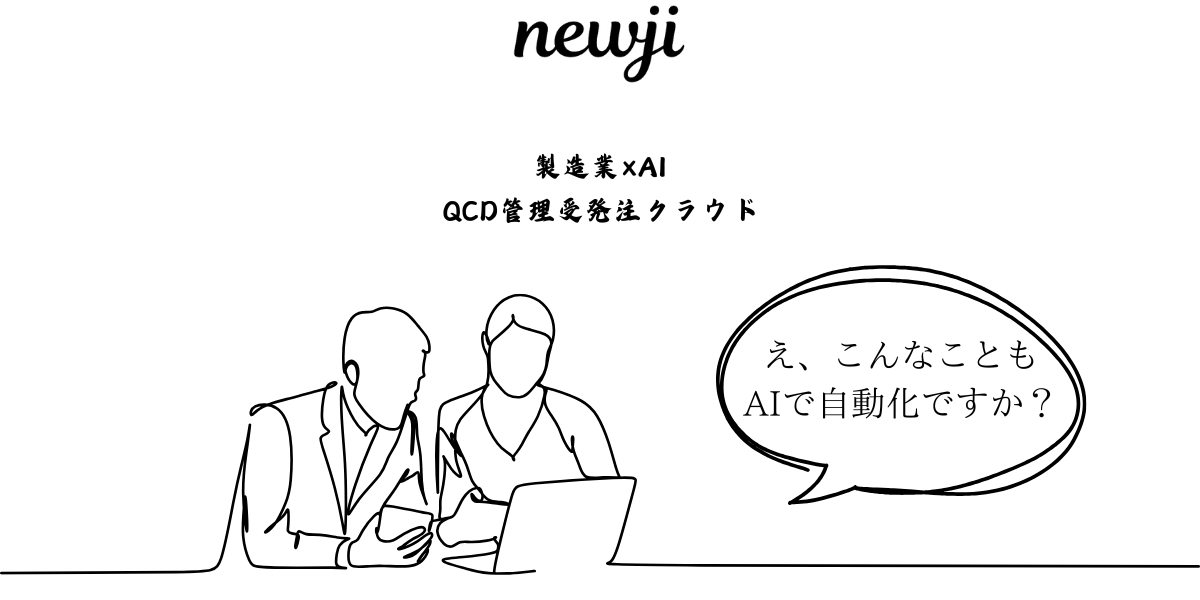
Process improvement of wax melt mixing and coarse graining technology
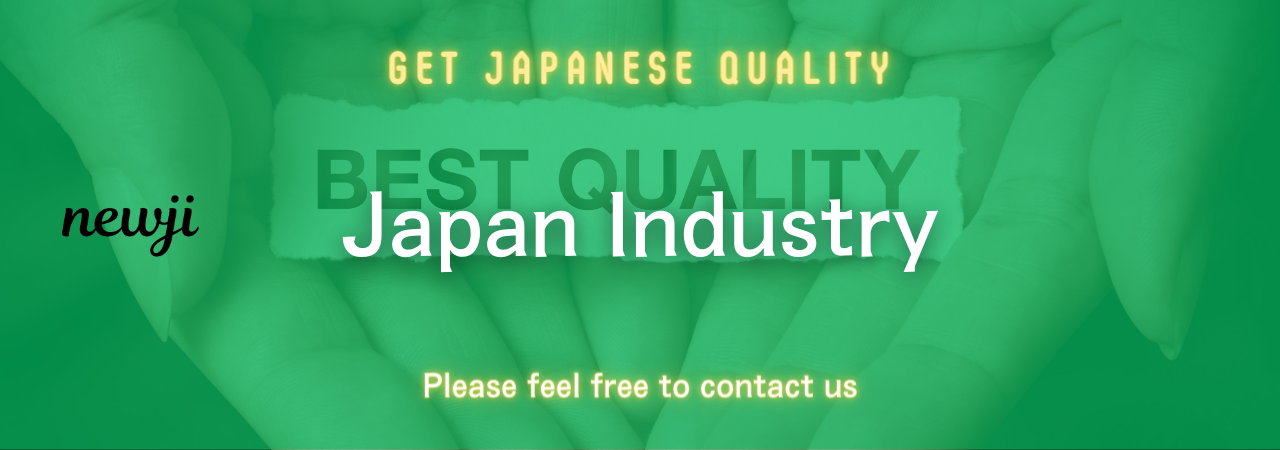
目次
Understanding Wax Melt Mixing and Coarse Graining
Wax melts have become increasingly popular in recent years as a safer and more customizable alternative to traditional candles.
These fragrant cubes, often used with electric warmers, release aromatic scents without the need for an open flame.
At the heart of creating high-quality wax melts is the process of mixing and coarse graining.
Understanding and improving this process is essential for manufacturers looking to enhance product quality and production efficiency.
The Basics of Wax Melt Mixing
Wax melt mixing involves combining various ingredients to create a uniform mixture that can be molded into individual wax melts.
Typically, the main ingredients include wax, fragrance oils, dyes, and sometimes other additives to alter texture or color.
Each component must be measured precisely to ensure consistency in each batch produced.
The most common types of waxes used in manufacturing wax melts are paraffin, soy, and beeswax.
Each type of wax has its own properties that affect the melting point, scent retention, and overall performance of the finished product.
During the mixing phase, it’s crucial to thoroughly blend these components to achieve a homogeneous mixture that guarantees the desired aromatic experience for the end-user.
Importance of Coarse Graining
Coarse graining is an important step in the production of wax melts, involving the breaking down of the wax mixture into smaller particles before shaping.
This step can significantly influence the melting rate, fragrance dispersion, and overall quality of the wax melt.
Achieving the right particle size is vital for ensuring uniform melting.
An effective coarse graining process helps to distribute the fragrance evenly throughout the wax.
By churning the wax into more granular forms, companies ensure that their wax melts burn evenly and release scents consistently during use.
Inconsistent particle size can lead to uneven melting, which impacts both scent intensity and duration.
Challenges in Wax Melt Production
Manufacturers face several challenges in improving the process of wax melt mixing and coarse graining.
Fluctuations in raw material quality, variations in temperature and environmental conditions, and equipment limitations can affect the efficiency and quality of production.
One key difficulty is achieving and maintaining the perfect balance of fragrance oil and wax.
Too much fragrance oil can make the wax melt feel oily and affect its solidifying process, while too little renders it ineffective as a scent-delivery product.
Striking the right balance can be challenging, particularly when dealing with different wax types and scents.
Another common challenge is dealing with the variability in raw materials.
Since natural waxes like soy and beeswax can have varying characteristics depending on harvest conditions, manufacturers often need to adjust their processes to ensure consistency in the final product.
Innovations in Wax Mixing Technology
In recent years, technology has played a huge role in resolving many of these manufacturing challenges.
One major advancement is the use of automated mixing systems which help ensure consistent mixing and reduce human error.
These systems can precisely measure and dispense ingredients, enhance blending, and maintain constant temperatures during the mix.
The implementation of these automated systems can dramatically improve the efficiency of wax melt production.
They allow for greater control and precision, leading to enhanced product quality and consistency from batch to batch.
Furthermore, they reduce waste and optimize the use of raw materials, contributing to cost-effective production.
Improving Coarse Graining Technology
In terms of coarse graining, advancements have also been made with new cutting and grinding technologies.
Modern machinery is designed to handle a range of wax consistencies and densities, providing manufacturers with adaptable solutions for varying production needs.
Enhanced grinding technology not only improves the uniformity of particle sizes but also increases the speed of production.
This means faster turnaround times and the ability to scale up production without compromising product quality.
Computer-aided design (CAD) software is also being used to optimize the design of molds, ensuring efficient shaping and cooling of the wax melts.
Steps Toward Process Improvement
Manufacturers seeking to improve their wax melt mixing and coarse graining processes should begin by conducting a thorough analysis of their current systems.
Data-driven approaches can help identify inefficiencies and areas for improvement in current production workflows.
Consider investing in new technology that enhances precision and automation in both mixing and coarse graining stages.
This investment can be justified by the long-term benefits of increased efficiency, reduced waste, and superior product quality.
Furthermore, maintaining rigorous quality control processes at every stage of production is essential.
Regular testing and analysis can help ensure that each batch meets the desired standards for scent, texture, and melting properties.
Engaging with suppliers to ensure consistent quality of raw materials and staying updated on the latest developments in wax technology will also contribute to continuous improvement.
By focusing on the entire production chain, from raw materials to finished product, manufacturers can achieve notable enhancements in their wax melt production processes.
Conclusion
Improving the process of wax melt mixing and coarse graining technology is a vital task for manufacturers who wish to stay competitive in the market.
By embracing technological advancements and refining production techniques, manufacturers can produce high-quality, consistent, and aromatic wax melts that resonate with consumers.
The journey toward optimization may require investment, but the return in terms of efficiency, cost savings, and customer satisfaction is well worth the effort.
資料ダウンロード
QCD調達購買管理クラウド「newji」は、調達購買部門で必要なQCD管理全てを備えた、現場特化型兼クラウド型の今世紀最高の購買管理システムとなります。
ユーザー登録
調達購買業務の効率化だけでなく、システムを導入することで、コスト削減や製品・資材のステータス可視化のほか、属人化していた購買情報の共有化による内部不正防止や統制にも役立ちます。
NEWJI DX
製造業に特化したデジタルトランスフォーメーション(DX)の実現を目指す請負開発型のコンサルティングサービスです。AI、iPaaS、および先端の技術を駆使して、製造プロセスの効率化、業務効率化、チームワーク強化、コスト削減、品質向上を実現します。このサービスは、製造業の課題を深く理解し、それに対する最適なデジタルソリューションを提供することで、企業が持続的な成長とイノベーションを達成できるようサポートします。
オンライン講座
製造業、主に購買・調達部門にお勤めの方々に向けた情報を配信しております。
新任の方やベテランの方、管理職を対象とした幅広いコンテンツをご用意しております。
お問い合わせ
コストダウンが利益に直結する術だと理解していても、なかなか前に進めることができない状況。そんな時は、newjiのコストダウン自動化機能で大きく利益貢献しよう!
(Β版非公開)