- お役立ち記事
- Process Improvement to Eliminate Waste Through Time Analysis
Process Improvement to Eliminate Waste Through Time Analysis
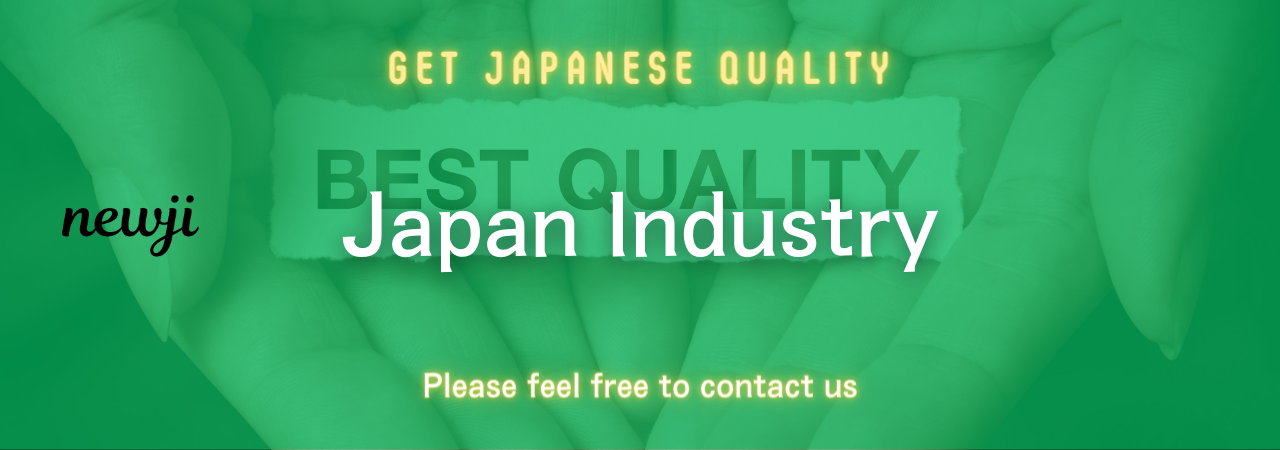
Process improvement through time analysis is a powerful method to enhance efficiency and eliminate waste in any business operation.
By analyzing the time spent on various tasks and processes, you can identify bottlenecks, redundancies, and opportunities for improvement.
This article will explore the key steps and benefits of using time analysis to streamline your business processes.
目次
Understanding Time Analysis
Time analysis involves examining how time is utilized within a process or workflow.
It provides insights into the duration of tasks, waiting times, and any delays that occur.
This data can then be used to identify inefficiencies and areas where time savings can be achieved.
Data Collection
Start by collecting data on how long each step of the process takes.
This can be done through time tracking software, manual time logs, or a combination of both.
Ensure that data collection is accurate and covers sufficient timeframe to give a realistic picture.
Mapping the Process
Once you have gathered the data, map out the entire process from start to finish.
This visual representation allows you to see where each task fits into the overall workflow.
Flowcharts or process maps are effective tools for this purpose.
Identifying Inefficiencies
With a mapped-out process and time data in hand, you can start to pinpoint inefficiencies.
These could be steps that take longer than necessary, periods of inactivity, or repetitive actions.
Identifying Bottlenecks
Bottlenecks are stages in the process where work accumulates, causing delays and increased lead times.
Identifying these points is crucial, as they often represent the most significant source of inefficiency.
Recognizing Redundancies
Redundancies occur when tasks are duplicated or unnecessary.
By eliminating these, you can streamline the process and reduce wasted time.
Implementing Solutions
Once inefficiencies have been identified, the next step is to implement solutions.
This may involve re-engineering the process, implementing new tools and technologies, or reallocating resources.
Process Re-engineering
Re-engineering involves fundamentally changing the way a process is carried out.
This could mean rearranging tasks, combining steps, or eliminating unnecessary actions altogether.
The goal is to create a more efficient and effective workflow.
Utilizing Technology
Incorporating technology can provide significant time savings.
Automation tools, for example, can handle repetitive tasks more quickly and accurately than humans.
Software solutions can also streamline communication and data management.
Resource Allocation
Sometimes, inefficiencies arise from improper allocation of resources.
By redistributing tasks among your team or investing in new tools and equipment, you can improve overall efficiency.
Monitoring and Continuous Improvement
Process improvement is not a one-time activity but an ongoing effort.
Regular monitoring and updating of processes ensure that they remain efficient over time.
Regular Reviews
Conduct regular reviews of your processes to identify new inefficiencies or areas that need improvement.
These reviews can be scheduled quarterly, biannually, or annually, depending on the complexity and importance of the process.
Employee Feedback
Your employees are on the front lines and often have valuable insights into where improvements can be made.
Encourage them to provide feedback and suggestions for process improvements.
Performance Metrics
Establish performance metrics to measure the effectiveness of your improvements.
These could include reduced lead times, increased output, or improved quality.
Regularly review these metrics to gauge the success of your efforts and make necessary adjustments.
Benefits of Process Improvement Through Time Analysis
Using time analysis for process improvement offers numerous benefits to your business.
Increased Efficiency
By streamlining processes and eliminating waste, you can perform tasks more quickly and with fewer resources.
This leads to increased productivity and reduced operational costs.
Improved Quality
Removing inefficiencies often results in higher quality work.
Tasks are completed more consistently and with fewer errors, leading to better outcomes for your business and customers.
Enhanced Employee Satisfaction
When processes are efficient, your employees can focus on high-value tasks rather than tedious or redundant activities.
This can lead to greater job satisfaction and reduced turnover.
Better Customer Experience
Efficient processes lead to faster and more reliable services or products.
This can enhance customer satisfaction and loyalty, giving your business a competitive edge.
Conclusion
Process improvement through time analysis is a valuable strategy for any business looking to enhance efficiency and eliminate waste.
By carefully analyzing how time is spent on various tasks, identifying areas of inefficiency, and implementing targeted solutions, you can achieve significant improvements in productivity, quality, and employee satisfaction.
Regular monitoring and continuous improvement ensure that your processes remain effective over time, providing lasting benefits for your business.
資料ダウンロード
QCD調達購買管理クラウド「newji」は、調達購買部門で必要なQCD管理全てを備えた、現場特化型兼クラウド型の今世紀最高の購買管理システムとなります。
ユーザー登録
調達購買業務の効率化だけでなく、システムを導入することで、コスト削減や製品・資材のステータス可視化のほか、属人化していた購買情報の共有化による内部不正防止や統制にも役立ちます。
NEWJI DX
製造業に特化したデジタルトランスフォーメーション(DX)の実現を目指す請負開発型のコンサルティングサービスです。AI、iPaaS、および先端の技術を駆使して、製造プロセスの効率化、業務効率化、チームワーク強化、コスト削減、品質向上を実現します。このサービスは、製造業の課題を深く理解し、それに対する最適なデジタルソリューションを提供することで、企業が持続的な成長とイノベーションを達成できるようサポートします。
オンライン講座
製造業、主に購買・調達部門にお勤めの方々に向けた情報を配信しております。
新任の方やベテランの方、管理職を対象とした幅広いコンテンツをご用意しております。
お問い合わせ
コストダウンが利益に直結する術だと理解していても、なかなか前に進めることができない状況。そんな時は、newjiのコストダウン自動化機能で大きく利益貢献しよう!
(Β版非公開)