- お役立ち記事
- Process Improvements to Achieve High Precision in Grinding
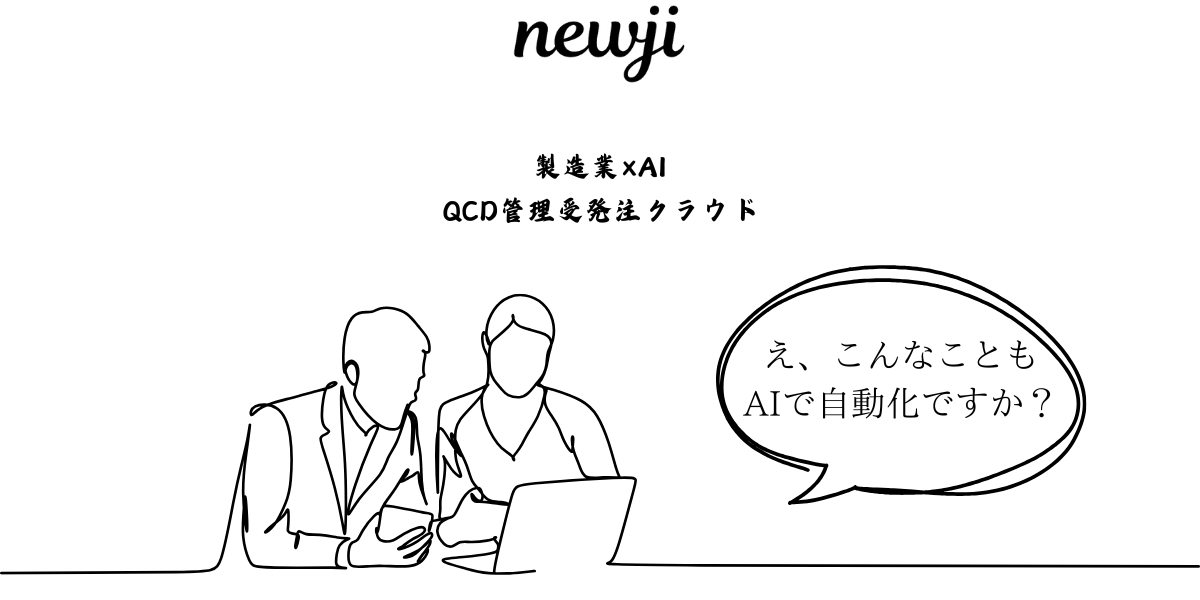
Process Improvements to Achieve High Precision in Grinding
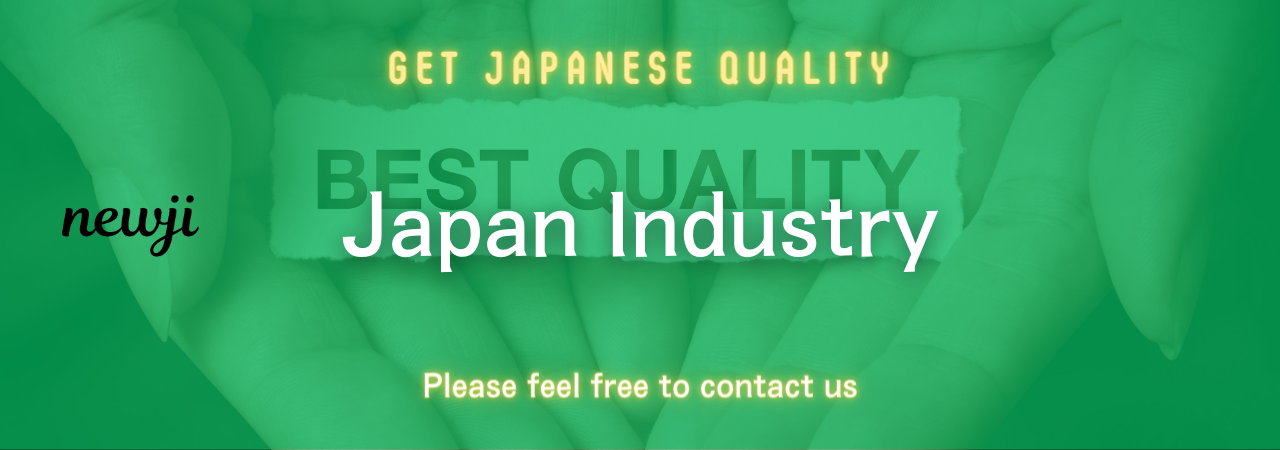
Precision grinding is a critical process used in various industries such as automotive, aerospace, and manufacturing.
Achieving high precision in grinding is essential for ensuring the quality and performance of the final product.
In this article, we will explore various process improvements that can lead to high precision in grinding, focusing on factors such as machine technology, tooling, and process optimization.
目次
Understanding the Basics of Precision Grinding
Precision grinding is a machining process that removes material from a workpiece to achieve the desired shape and surface finish.
The process involves the use of a grinding wheel, which is composed of abrasive particles bonded together.
The key factors that influence the precision of the grinding process include the type of grinding wheel, the machine used, and the skill of the operator.
The Role of Grinding Wheels
Grinding wheels come in various shapes and sizes, each designed for specific applications.
The choice of grinding wheel is crucial for achieving high precision in grinding.
Factors such as the abrasive material, grain size, and bonding type all play a role in determining the performance of the grinding wheel.
For example, finer grain sizes are typically used for finishing operations to achieve a smooth surface finish, while coarser grains are used for roughing operations to remove large amounts of material quickly.
Additionally, the bonding type, whether it is vitrified, resin, or metal bond, can affect the wheel’s durability and cutting efficiency.
Advanced Machine Technology
Modern grinding machines are equipped with advanced technology that enhances their precision and accuracy.
These machines often feature computer numerical control (CNC) systems that allow for precise control of the grinding process.
CNC grinding machines can perform complex operations with high repeatability and minimal human intervention.
Importance of Machine Rigidity
The rigidity of the grinding machine is another critical factor in achieving high precision.
A rigid machine minimizes vibrations and deflections during the grinding process, resulting in better surface finishes and tighter dimensional tolerances.
To enhance machine rigidity, manufacturers use high-quality materials and robust construction techniques.
Temperature Control in Grinding
Temperature control is essential for maintaining precision in grinding.
Excessive heat generated during the grinding process can lead to thermal expansion of the workpiece, causing dimensional inaccuracies.
Modern grinding machines are equipped with coolant systems that help dissipate heat and maintain a stable grinding temperature.
Using a proper coolant and maintaining an optimal flow rate can significantly improve the grinding process.
Coolants also help to remove chips and debris from the grinding zone, preventing wheel loading and improving the overall quality of the grind.
Tooling and Dressing Techniques
The choice of tooling and dressing techniques has a significant impact on the precision of the grinding process.
Dressing is the process of conditioning the grinding wheel to restore its cutting ability and maintain its shape.
Importance of Dressing
Regular dressing of the grinding wheel ensures that it remains sharp and free from loading.
A well-dressed wheel produces better surface finishes and maintains dimensional accuracy.
Several dressing techniques are available, including diamond dressing and rotary dressing.
Diamond dressing involves using a single-point or multi-point diamond tool to remove a small layer of abrasive material from the wheel’s surface.
Rotary dressing, on the other hand, uses a rotating dressing tool to condition the grinding wheel.
Both methods have their advantages and are chosen based on the specific requirements of the grinding process.
Tooling Selection
Selecting the right tooling for the grinding operation is essential for achieving high precision.
Tooling options include various types of grinding wheels, fixtures, and adapters.
The choice of tooling depends on factors such as the material being ground, the required surface finish, and the complexity of the workpiece geometry.
For example, cubic boron nitride (CBN) grinding wheels are ideal for grinding hard materials like hardened steel, while aluminum oxide wheels are suitable for softer materials like cast iron.
Proper tooling selection can significantly enhance the grinding process’s efficiency and precision.
Process Optimization Strategies
Process optimization involves fine-tuning various parameters to achieve the best possible results in the grinding process.
Several strategies can be used to optimize the grinding process and achieve high precision.
Parameter Optimization
Optimizing grinding parameters such as feed rate, wheel speed, and depth of cut is essential for achieving high precision.
Experimenting with different parameter settings and analyzing their effects on the grinding process can help identify the optimal conditions.
Using process monitoring systems can provide real-time feedback and enable operators to make adjustments on the fly.
Automation and Robotics
Automation and robotics are increasingly being used in precision grinding to enhance process control and consistency.
Automated grinding systems can perform repetitive tasks with high accuracy and minimal variation.
Robotic arms can be used to handle workpieces, load and unload machines, and perform in-process inspections.
Integrating automation into the grinding process can reduce human error, improve productivity, and achieve consistent high-quality results.
Automated systems can also collect data and provide insights for further process improvement.
Quality Control and Inspection
Implementing robust quality control measures is critical for ensuring that the grinding process consistently produces high-precision parts.
In-process and post-process inspections can help identify deviations and enable corrective actions.
Using advanced inspection tools such as coordinate measuring machines (CMMs) and surface profilometers can provide accurate measurements of dimensional tolerances and surface finishes.
Regular calibration of inspection equipment and adherence to quality standards can further enhance the precision of the grinding process.
By continuously monitoring and improving quality control practices, manufacturers can achieve higher levels of precision and reliability.
Achieving high precision in grinding requires a combination of advanced technology, skilled operators, and optimized processes.
By focusing on factors such as grinding wheel selection, machine rigidity, temperature control, tooling, and process optimization, manufacturers can produce high-quality parts with tight tolerances and superior surface finishes.
Continuous improvement and innovation in precision grinding techniques will ensure that industries can meet the demanding requirements of modern manufacturing.
資料ダウンロード
QCD調達購買管理クラウド「newji」は、調達購買部門で必要なQCD管理全てを備えた、現場特化型兼クラウド型の今世紀最高の購買管理システムとなります。
ユーザー登録
調達購買業務の効率化だけでなく、システムを導入することで、コスト削減や製品・資材のステータス可視化のほか、属人化していた購買情報の共有化による内部不正防止や統制にも役立ちます。
NEWJI DX
製造業に特化したデジタルトランスフォーメーション(DX)の実現を目指す請負開発型のコンサルティングサービスです。AI、iPaaS、および先端の技術を駆使して、製造プロセスの効率化、業務効率化、チームワーク強化、コスト削減、品質向上を実現します。このサービスは、製造業の課題を深く理解し、それに対する最適なデジタルソリューションを提供することで、企業が持続的な成長とイノベーションを達成できるようサポートします。
オンライン講座
製造業、主に購買・調達部門にお勤めの方々に向けた情報を配信しております。
新任の方やベテランの方、管理職を対象とした幅広いコンテンツをご用意しております。
お問い合わせ
コストダウンが利益に直結する術だと理解していても、なかなか前に進めることができない状況。そんな時は、newjiのコストダウン自動化機能で大きく利益貢献しよう!
(Β版非公開)