- お役立ち記事
- Process optimization solutions for manufacturing results
月間76,176名の
製造業ご担当者様が閲覧しています*
*2025年3月31日現在のGoogle Analyticsのデータより
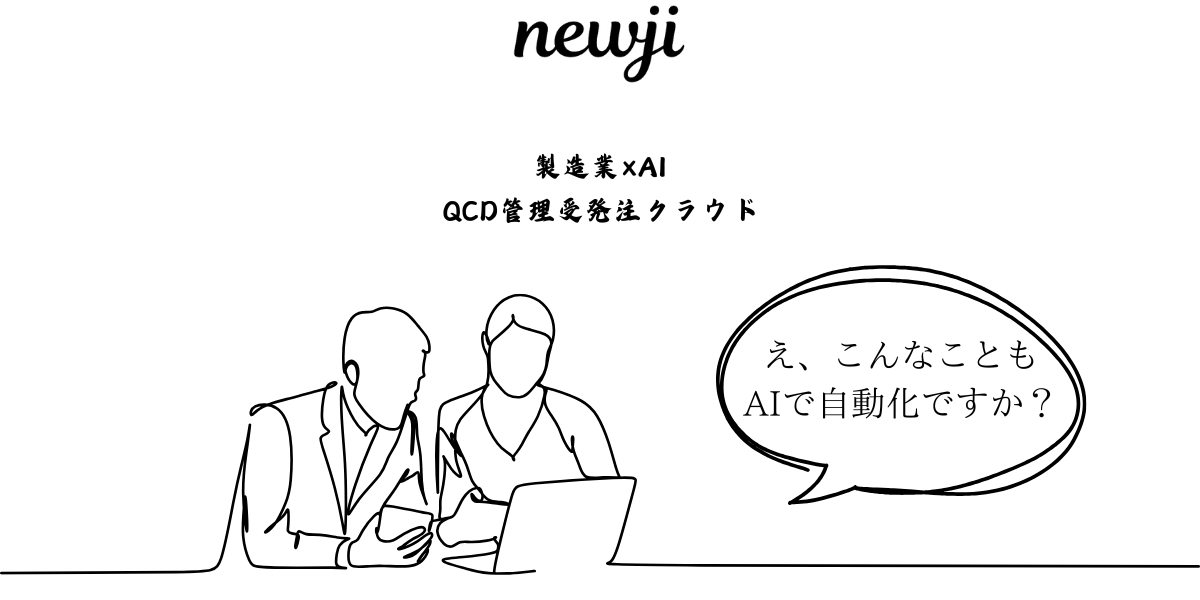
Process optimization solutions for manufacturing results
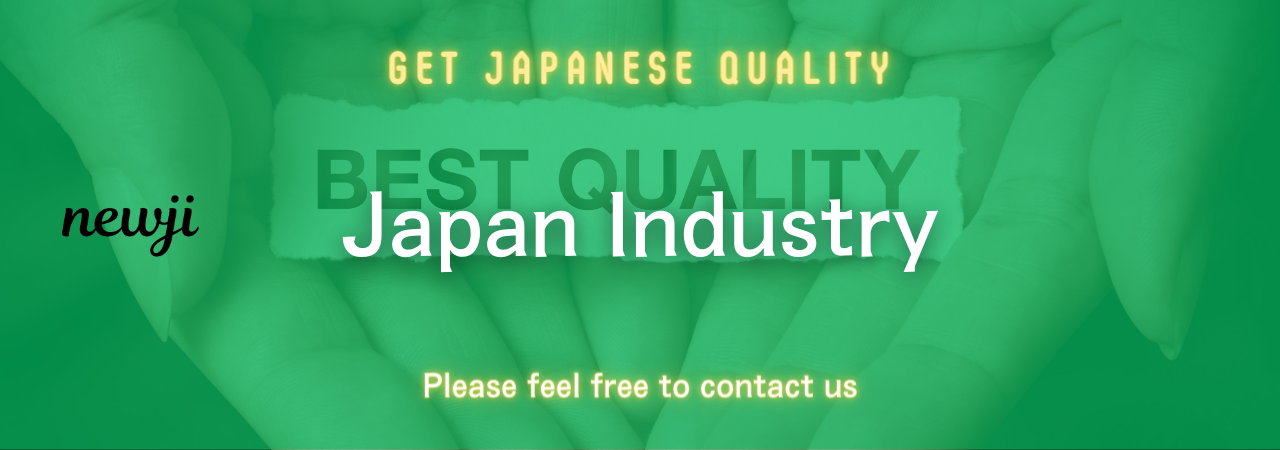
目次
Understanding Process Optimization in Manufacturing
Process optimization in manufacturing is all about making production processes more efficient, cost-effective, and reliable.
This encompasses a wide range of strategies and tools that aim to improve the quality of products, reduce production times, and cut costs.
Manufacturing companies are always looking for ways to optimize their processes to remain competitive in the market.
By embracing process optimization, manufacturers can enhance their operational results and improve overall productivity.
Why is Process Optimization Important?
Process optimization is essential for several reasons.
First and foremost, it helps in reducing waste, a critical factor for any manufacturing company looking to minimize costs.
By streamlining processes, manufacturers can eliminate unnecessary steps, leading to less material and resource wastage.
Additionally, process optimization increases efficiency, leading to faster production cycles and improved throughput.
Moreover, it plays a crucial role in maintaining quality.
An optimized process ensures consistent output, reducing the number of defects and enhancing customer satisfaction.
Finally, process optimization is vital for staying competitive.
As technologies and market demands evolve, manufacturers must continually refine their processes to stay ahead of the competition.
Common Process Optimization Techniques
There are several widely used techniques in manufacturing process optimization.
Understanding and implementing these can significantly enhance manufacturing results.
Lean Manufacturing
Lean manufacturing is a methodology focused on minimizing waste without sacrificing productivity.
Originating from Toyota’s production system, the principle of lean manufacturing is to do more with less.
By identifying and eliminating non-value-added activities, manufacturers can streamline their processes, improve product quality, and reduce lead times.
Six Sigma
Six Sigma is a data-driven approach that aims to improve the quality of outputs by identifying and removing causes of defects and minimizing variability in manufacturing processes.
The methodology uses statistical methods and quality management tools to achieve operational excellence.
It employs a structured strategy – DMAIC (Define, Measure, Analyze, Improve, Control) – to enhance process efficiency.
Kaizen
Kaizen, a Japanese term meaning “continuous improvement,” is a strategy where employees at all levels of a company work together proactively to achieve regular, incremental improvements in the manufacturing process.
Kaizen focuses on small, sustainable changes over time that result in significant long-term improvements.
Total Quality Management (TQM)
Total Quality Management (TQM) is a comprehensive approach that involves everyone in the organization in the process of improving product quality and customer satisfaction.
It emphasizes continuous improvement and the use of data to drive decision-making.
TQM aims to systematically manage and improve the quality of products and services through collective efforts.
The Role of Technology in Process Optimization
Advancements in technology have significantly augmented process optimization efforts in manufacturing.
Let’s explore how technology plays a role in enhancing manufacturing processes.
Automation
Automation streamlines processes by reducing the need for human intervention in repetitive tasks.
It increases efficiency, speed, and accuracy while minimizing errors.
Robots and automated machinery can perform tasks faster and with greater precision than human workers, boosting overall productivity.
IoT and Data Analytics
The Internet of Things (IoT) and data analytics are powerful tools for process optimization.
IoT devices collect data from manufacturing machines, providing real-time insights into their operational performance.
Data analytics analyzes this data, identifying patterns and inefficiencies that can be addressed to improve processes.
Predictive analytics, in particular, can anticipate potential issues before they occur, allowing proactive measures.
Digital Twins
Digital twins are virtual models of physical systems used to simulate and analyze manufacturing processes.
They provide a comprehensive view of production operations, enabling manufacturers to test various scenarios and optimize processes without disrupting actual operations.
Digital twins enhance decision-making by allowing manufacturers to predict the outcomes of changes before implementing them.
Steps to Implement Process Optimization
Implementing process optimization requires a systematic approach.
Here are some critical steps manufacturers can take to optimize their processes effectively.
Identify Objectives
The first step is to clearly define the objectives of the optimization process.
This involves determining the key areas that require improvement and setting measurable goals for the optimization initiative.
Whether it’s reducing costs, improving product quality, or increasing production speed, having clear objectives guides the process.
Analyze Current Processes
Before implementing any changes, it’s crucial to analyze the existing processes to understand their strengths and weaknesses.
Using tools like process mapping or flowcharts, manufacturers can visualize the entire production process and identify areas that need improvement.
Data collection and analysis play a critical role in this phase.
Develop and Implement Solutions
Once the analysis is complete, the next step is to develop solutions tailored to address the identified issues.
This might involve redesigning workflows, employing new technologies, or adopting specific optimization methodologies like Lean or Six Sigma.
Implementing these solutions requires careful planning and execution to minimize disruptions.
Monitor and Measure Outcomes
After implementation, it’s essential to monitor the outcomes closely.
This involves measuring the performance of optimized processes against the set objectives.
Key metrics should be tracked regularly to assess the impact of the optimization efforts and identify further improvement opportunities.
Continuous Improvement
Process optimization is not a one-time project but an ongoing effort.
Embracing a culture of continuous improvement ensures that processes remain efficient and responsive to changing demands.
Regular evaluations and feedback loops help identify new areas for optimization and keep manufacturers ahead of the competition.
Conclusion
In summary, process optimization is an indispensable strategy for manufacturers aiming to boost their operational efficiency and competitiveness.
By understanding common optimization techniques, leveraging technology, and following a systematic implementation process, manufacturers can achieve significant improvements in their manufacturing outcomes.
Embracing a continuous improvement mindset ensures that these gains are sustained over time, leading to lasting profits and success in the ever-evolving manufacturing landscape.
資料ダウンロード
QCD管理受発注クラウド「newji」は、受発注部門で必要なQCD管理全てを備えた、現場特化型兼クラウド型の今世紀最高の受発注管理システムとなります。
ユーザー登録
受発注業務の効率化だけでなく、システムを導入することで、コスト削減や製品・資材のステータス可視化のほか、属人化していた受発注情報の共有化による内部不正防止や統制にも役立ちます。
NEWJI DX
製造業に特化したデジタルトランスフォーメーション(DX)の実現を目指す請負開発型のコンサルティングサービスです。AI、iPaaS、および先端の技術を駆使して、製造プロセスの効率化、業務効率化、チームワーク強化、コスト削減、品質向上を実現します。このサービスは、製造業の課題を深く理解し、それに対する最適なデジタルソリューションを提供することで、企業が持続的な成長とイノベーションを達成できるようサポートします。
製造業ニュース解説
製造業、主に購買・調達部門にお勤めの方々に向けた情報を配信しております。
新任の方やベテランの方、管理職を対象とした幅広いコンテンツをご用意しております。
お問い合わせ
コストダウンが利益に直結する術だと理解していても、なかなか前に進めることができない状況。そんな時は、newjiのコストダウン自動化機能で大きく利益貢献しよう!
(β版非公開)