- お役立ち記事
- Processing/assembly points necessary for machine designers, design techniques and practical know-how to prevent problems.
月間76,176名の
製造業ご担当者様が閲覧しています*
*2025年3月31日現在のGoogle Analyticsのデータより
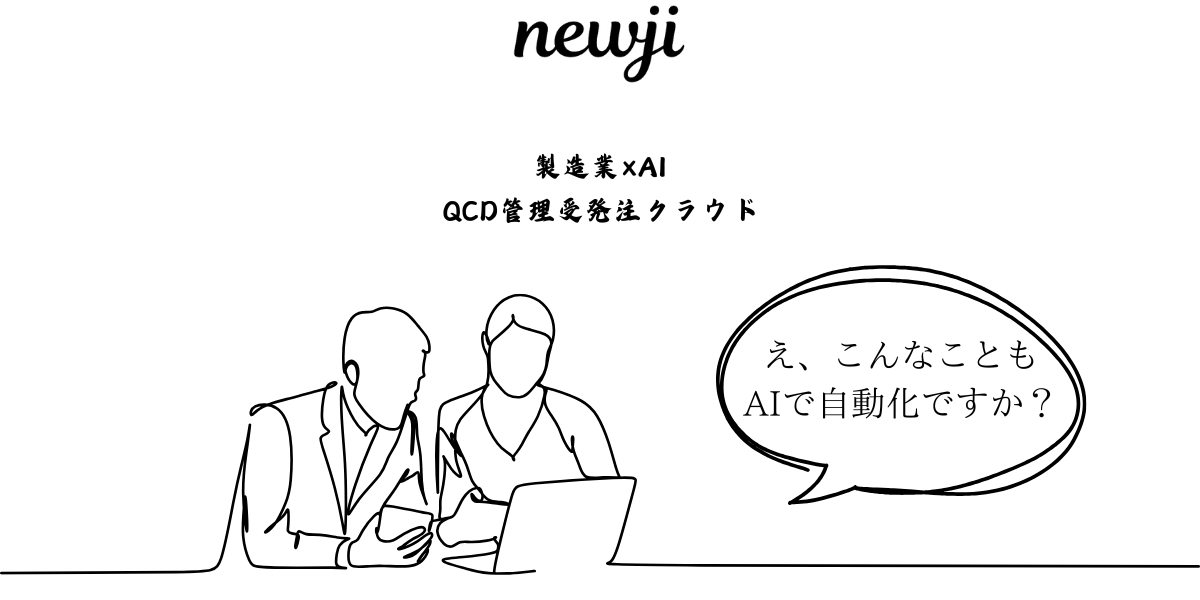
Processing/assembly points necessary for machine designers, design techniques and practical know-how to prevent problems.
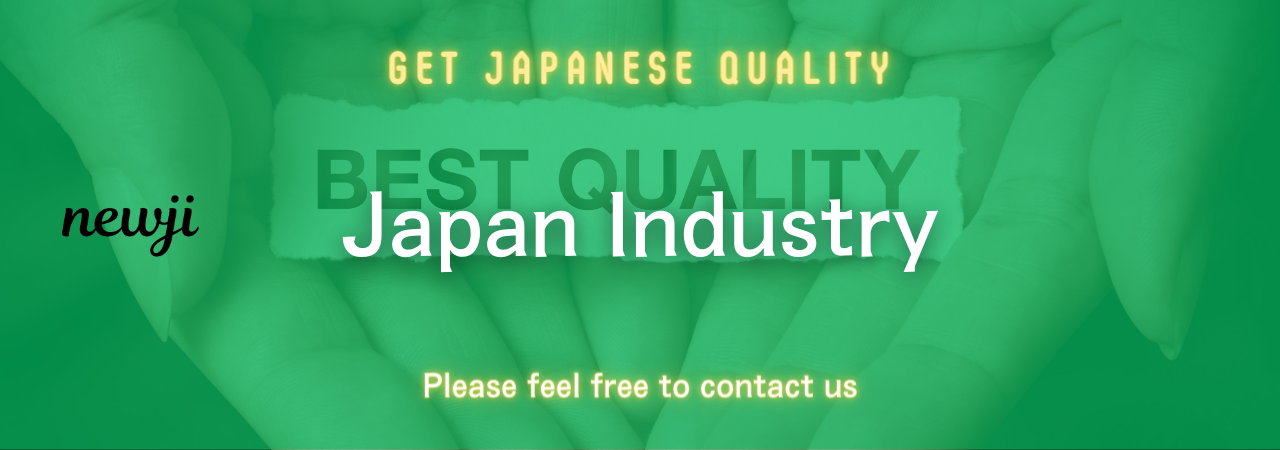
Understanding the Basics of Machine Design
Machine design is a critical field that involves creating machinery capable of performing specific tasks efficiently and safely.
Understanding the basics of machine design is essential for anyone looking to enter this field or improve their skills.
A machine designer must consider several factors, including functionality, safety, efficiency, and cost-effectiveness.
Designers work on creating blueprints and plans that lead to the production of machines that meet desired specifications.
A thorough understanding of mechanical principles, material properties, and manufacturing processes is necessary to ensure that the design is viable and practical.
The Significance of Processing/Assembly Points
One of the most crucial aspects of machine design is the processing and assembly points.
These are the stages where different components of a machine are pieced together to create the final product.
The design process needs to account for these points to ensure that assembly is straightforward and cost-effective.
Processing and assembly points influence how quickly and efficiently a product can be manufactured.
By optimizing these points, designers can minimize delays and reduce overall production costs.
An efficient assembly plan also enhances the quality and reliability of the final machine, reducing the likelihood of problems during operation.
Key Design Techniques to Optimize Assembly Points
To optimize processing and assembly points, machine designers can utilize several design techniques.
One effective approach is modular design.
This involves breaking down the machine into smaller, independently functioning units or modules.
These modules can be assembled separately and then joined together in the final assembly process.
Modular design simplifies assembly and allows for easy maintenance and upgrades.
Another technique is to design for manufacturability (DFM).
DFM focuses on designing components in a way that makes them easy to manufacture.
By considering manufacturing constraints early in the design process, designers can create parts that are not only easy to produce but also reduce waste and cost.
This involves specifying tolerances, selecting appropriate materials, and designing for standard manufacturing processes like injection molding or CNC machining.
Furthermore, implementing design for assembly (DFA) principles can enhance the efficiency of the assembly process.
DFA involves designing parts that are easy to handle and fit together, minimizing the number of steps required in the assembly process.
This can include using fewer fasteners and simplifying the design of interfaces between components.
Practical Know-How to Prevent Problems
In addition to employing effective design techniques, acquiring practical know-how is essential to prevent problems during machine assembly and operation.
One key aspect is thorough testing and validation of prototypes before mass production.
By creating and testing prototypes, designers can identify potential issues and rectify them before full-scale manufacturing begins.
Moreover, effective communication with manufacturing teams is vital.
Machine designers must ensure that their designs are clearly understood by the team responsible for bringing them to life.
Providing comprehensive documentation and engaging in regular discussions with the production team can prevent misunderstandings and implementation errors.
Utilizing computer-aided design (CAD) software can also help in visualizing and simulating the assembly process.
CAD tools allow designers to create detailed 3D models of the machine, enabling them to identify any potential conflicts or inefficiencies in the assembly sequence.
This facilitates adjustments before physical components are produced, saving time and resources.
Additionally, maintaining quality through stringent quality control measures is crucial.
Establishing robust quality control protocols can help detect defects early in the production process.
This ensures that only components that meet the required standards proceed to assembly, preventing problems that could result in machine failure or reduced lifespan.
The Role of Experience and Continuous Learning
Machine design is a dynamic field that continues to evolve with advancements in technology and manufacturing processes.
Thus, experience and continuous learning play a significant role in the success of a machine designer.
Experienced designers draw from past projects to anticipate challenges and develop efficient solutions.
Continuous learning ensures that designers stay updated with new techniques and tools.
By attending workshops, seminars, and courses, designers can enhance their skills and incorporate new methodologies into their work.
This adaptability is crucial for innovating and improving designs in line with current industry standards and expectations.
Conclusion
Designing machines is a complex process that requires a deep understanding of multiple engineering principles and practical considerations.
Optimizing processing and assembly points can significantly impact the efficiency and cost-effectiveness of machine production.
By employing design techniques like modular design, DFM, and DFA, along with effective communication and testing protocols, designers can mitigate issues and enhance assembly processes.
The value of experience and continuous learning cannot be overstated.
They are vital in adapting to changing trends and maintaining the highest standards of machine design.
Ultimately, through careful planning and execution, machine designers can create robust, reliable machines that perform efficiently and safely.
資料ダウンロード
QCD管理受発注クラウド「newji」は、受発注部門で必要なQCD管理全てを備えた、現場特化型兼クラウド型の今世紀最高の受発注管理システムとなります。
ユーザー登録
受発注業務の効率化だけでなく、システムを導入することで、コスト削減や製品・資材のステータス可視化のほか、属人化していた受発注情報の共有化による内部不正防止や統制にも役立ちます。
NEWJI DX
製造業に特化したデジタルトランスフォーメーション(DX)の実現を目指す請負開発型のコンサルティングサービスです。AI、iPaaS、および先端の技術を駆使して、製造プロセスの効率化、業務効率化、チームワーク強化、コスト削減、品質向上を実現します。このサービスは、製造業の課題を深く理解し、それに対する最適なデジタルソリューションを提供することで、企業が持続的な成長とイノベーションを達成できるようサポートします。
製造業ニュース解説
製造業、主に購買・調達部門にお勤めの方々に向けた情報を配信しております。
新任の方やベテランの方、管理職を対象とした幅広いコンテンツをご用意しております。
お問い合わせ
コストダウンが利益に直結する術だと理解していても、なかなか前に進めることができない状況。そんな時は、newjiのコストダウン自動化機能で大きく利益貢献しよう!
(β版非公開)