- お役立ち記事
- Processing methods for titanium alloys and their increasing demand in the precision equipment market
月間76,176名の
製造業ご担当者様が閲覧しています*
*2025年3月31日現在のGoogle Analyticsのデータより
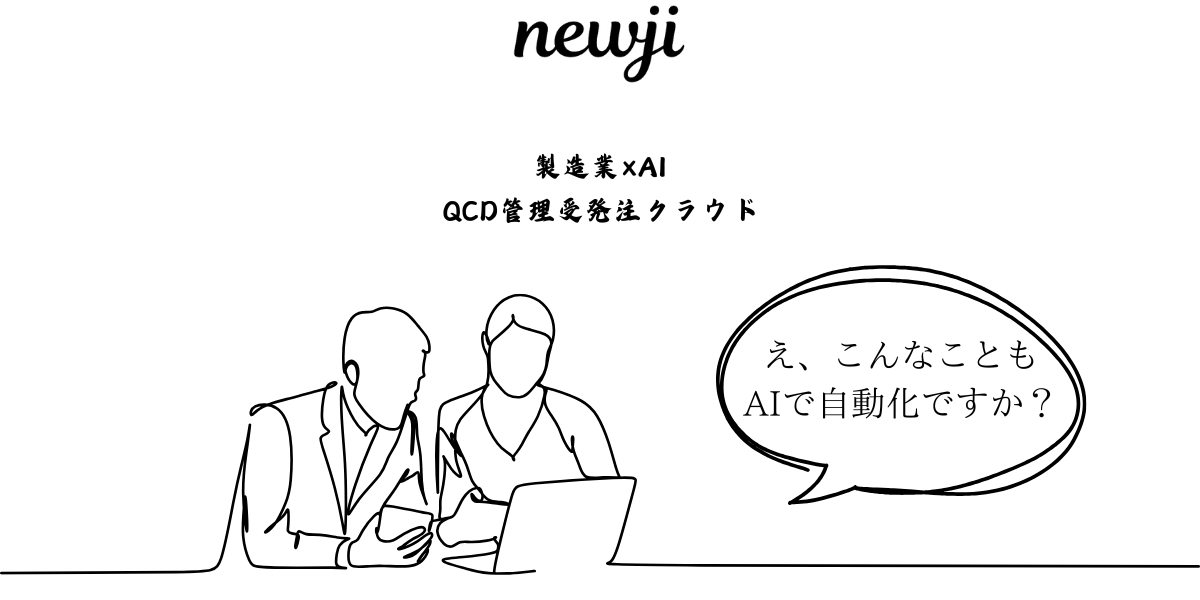
Processing methods for titanium alloys and their increasing demand in the precision equipment market
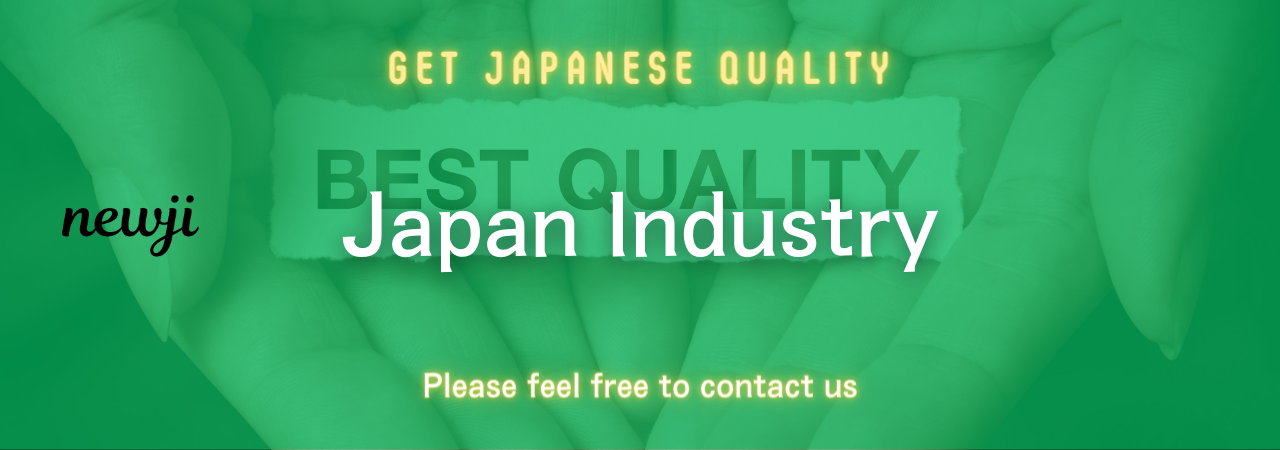
目次
What are Titanium Alloys?
Titanium alloys are a blend of titanium with other elements such as aluminum, vanadium, and molybdenum.
These blends enhance properties like strength, corrosion resistance, and stability even in high-temperature environments.
Titanium, by itself, is already known for its strength-to-weight ratio and durability, making these alloys valuable in various industries.
They find extensive applications in aerospace, military, automotive, and increasingly in precision equipment due to these enhanced properties.
Why the Demand for Titanium Alloys is Rising
The demand for titanium alloys in the precision equipment market is on the rise for several reasons.
First, their lightweight nature makes them ideal for applications where weight reduction is crucial without compromising strength.
In sectors like healthcare, titanium alloys are used in the production of surgical instruments and implants due to their biocompatibility and non-toxic nature.
Similarly, in the aerospace industry, these materials are used due to their resistance to corrosion and ability to withstand high temperatures, essential for aircraft performance.
Innovations Driven by Titanium Alloys
Technological advancements have revolutionized modern industries, and titanium alloys are at the forefront of this revolution.
Improvements in manufacturing technologies such as 3D printing with titanium powders now make it possible to create complex shapes and structures that were previously difficult to produce.
This has opened up new possibilities in the design and manufacturing of precision equipment, leading to components that are lighter, stronger, and more efficient.
These innovations directly contribute to the growing demand.
Processing Techniques for Titanium Alloys
Several techniques are employed in processing titanium alloys to tailor their mechanical properties for specific applications.
Understanding these methods is crucial for industries looking to leverage the full potential of these materials.
Traditional Machining
Traditional machining techniques like milling and turning are commonly used for shaping titanium alloys.
However, machining titanium can be challenging due to its high strength and low thermal conductivity.
Special cutting tools and cooling methods are employed to effectively manage the heat generated during the machining process.
This ensures the material does not degrade or become deformed.
3D Printing
Additive manufacturing, particularly 3D printing, has significantly impacted the processing of titanium alloys.
Powdered forms of the alloy are utilized to build layers in creating a component.
This method is advantageous for producing complex geometries that are difficult or impossible to achieve with conventional machining.
Furthermore, 3D printing reduces waste, making it a more sustainable option.
Forging and Casting
Forging involves shaping the titanium alloy using compressive forces, providing high strength and structural integrity.
This method is widely used for load-bearing applications.
Casting, on the other hand, involves pouring molten titanium alloy into a mold to achieve the desired shape.
This method is suitable for producing parts that require complex shapes with uniform properties.
Heat Treatment
Heat treatment processes such as annealing and solution treating are used to enhance the mechanical properties of titanium alloys.
These processes can increase toughness, reduce stress, and improve corrosion resistance.
Controlling the temperature and duration of the heat treatment effectively tailors the alloy’s characteristics to meet specific application demands.
Challenges in Processing Titanium Alloys
Despite the numerous advantages that titanium alloys offer, there are challenges in their processing.
Their high reactivity at elevated temperatures requires protective atmospheres or specialized environments to prevent contamination during processes like welding.
Additionally, the high cost of raw materials and energy-intensive processing methods can be a barrier for some manufacturers.
Environmental Considerations
As industries push for sustainable practices, the environmental impact of processing techniques is an area of focus.
While 3D printing reduces material waste, other methods like machining can generate significant scrap.
Effective recycling programs and improved efficiency in processing can help mitigate these environmental concerns.
Conclusion
As the precision equipment market continues to expand, the demand for titanium alloys is set to increase.
Their unparalleled properties and the continuous advancement in processing technologies make them indispensable in industries ranging from healthcare to aerospace.
Overcoming the challenges and focusing on sustainable processing methods will be crucial in harnessing the full potential of titanium alloys.
This may lead to even greater innovations, further solidifying their place in the future of material science.
資料ダウンロード
QCD管理受発注クラウド「newji」は、受発注部門で必要なQCD管理全てを備えた、現場特化型兼クラウド型の今世紀最高の受発注管理システムとなります。
ユーザー登録
受発注業務の効率化だけでなく、システムを導入することで、コスト削減や製品・資材のステータス可視化のほか、属人化していた受発注情報の共有化による内部不正防止や統制にも役立ちます。
NEWJI DX
製造業に特化したデジタルトランスフォーメーション(DX)の実現を目指す請負開発型のコンサルティングサービスです。AI、iPaaS、および先端の技術を駆使して、製造プロセスの効率化、業務効率化、チームワーク強化、コスト削減、品質向上を実現します。このサービスは、製造業の課題を深く理解し、それに対する最適なデジタルソリューションを提供することで、企業が持続的な成長とイノベーションを達成できるようサポートします。
製造業ニュース解説
製造業、主に購買・調達部門にお勤めの方々に向けた情報を配信しております。
新任の方やベテランの方、管理職を対象とした幅広いコンテンツをご用意しております。
お問い合わせ
コストダウンが利益に直結する術だと理解していても、なかなか前に進めることができない状況。そんな時は、newjiのコストダウン自動化機能で大きく利益貢献しよう!
(β版非公開)