- お役立ち記事
- Procurement issues for plastic substitute materials in the food industry
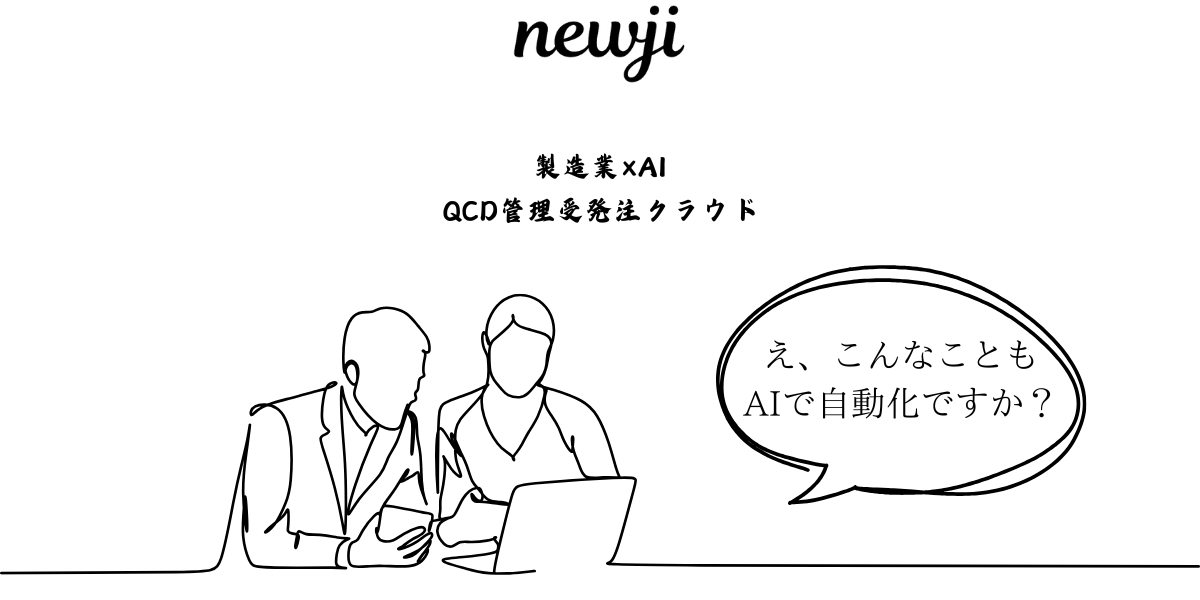
Procurement issues for plastic substitute materials in the food industry
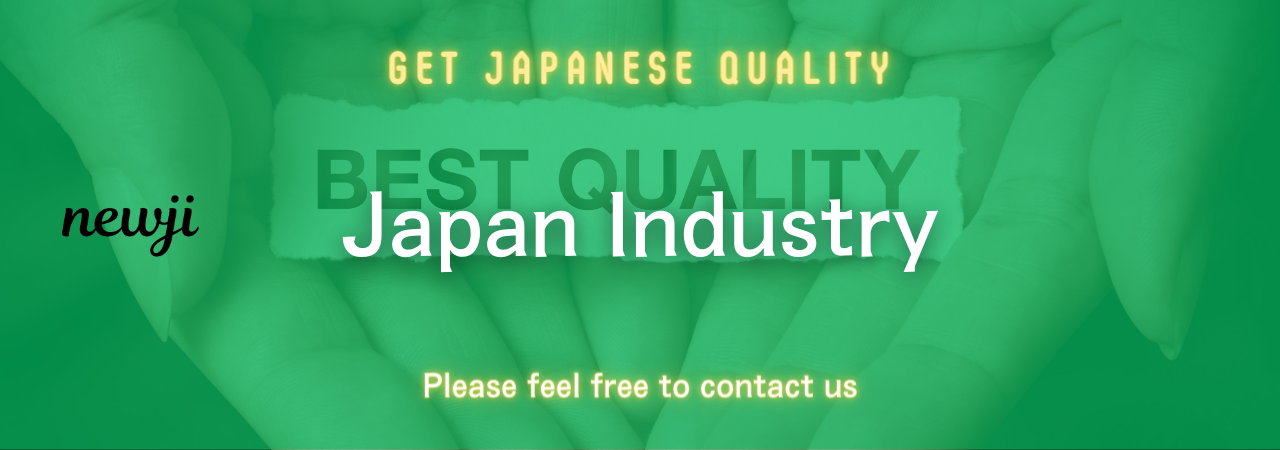
目次
Introduction to Plastic Substitute Materials
In recent years, the food industry has been under increasing pressure to reduce its reliance on plastic packaging due to environmental concerns.
Plastic waste contributes significantly to pollution, prompting the need for alternative materials.
As a result, many companies are turning towards plastic substitute materials to address the environmental impact.
However, while this shift is beneficial for the environment, it presents several procurement challenges that need to be addressed.
The Need for Alternatives to Plastic
Plastic has been a staple in the food industry for decades due to its durability, flexibility, and affordability.
However, its environmental impact is undeniable, with millions of tons ending up in oceans and landfills each year.
As awareness grows, both consumers and regulators are demanding more sustainable packaging solutions.
This has led the industry to explore alternatives such as biodegradable plastics, glass, paper, and plant-based materials.
Challenges in Procuring Plastic Substitute Materials
Switching from traditional plastics to alternative materials is not a straightforward process.
Several procurement issues arise that companies must navigate efficiently.
Availability of Materials
One of the primary challenges in procuring plastic substitute materials is their availability.
Unlike conventional plastics, which have a well-established supply chain, alternative materials are still developing their networks.
This can lead to supply shortages and longer lead times.
For instance, biodegradable options might not be produced in the quantities required to meet industry demands.
High Costs Involved
Another significant challenge is cost.
Plastic substitutes often come with a higher price tag compared to traditional plastics.
Biodegradable plastics, glass, and plant-based materials usually involve more complex production processes or limited availability, driving up costs.
This financial factor can be a deterrent for companies, particularly smaller businesses operating on tight margins.
Ensuring Quality and Safety
Ensuring that plastic substitute materials meet quality and safety standards is also a crucial procurement challenge.
Food packaging must adhere to strict safety regulations to avoid contamination and maintain product integrity.
Alternative materials need to be rigorously tested to ensure they do not interact negatively with food products or degrade under specific storage conditions.
Adapting to Design and Functional Changes
The shift to alternative materials often requires changes in packaging design and function.
Different materials can alter the appearance and practicality of packaging, influencing consumer acceptance and usability.
Impact on Brand Perception
When transitioning to new materials, companies must consider the impact on brand perception.
Consumers expect certain standards from brands, and any negative change in packaging quality or appearance can affect customer satisfaction and loyalty.
Investment in New Technologies
To incorporate plastic substitutes successfully, companies often need to invest in new technologies and equipment.
Existing machinery may not be suitable for the production processes required for alternative materials.
This investment represents a significant barrier for many businesses, necessitating careful financial planning and risk assessment.
Strategies for Overcoming Procurement Challenges
Despite these challenges, several strategies can help mitigate procurement issues related to plastic substitute materials.
Sourcing Widely and Forming Partnerships
To address availability issues, companies can expand their supplier networks by sourcing materials from multiple suppliers.
Forming partnerships with manufacturers of alternative materials can also provide more stable supply lines and enable more predictable procurement processes.
Cost Management through Economies of Scale
Companies can better manage the higher costs of alternative materials by leveraging economies of scale.
As demand for these materials rises, increased production can lead to cost reductions.
Businesses can collaborate within the industry to increase demand collectively, helping suppliers justify larger-scale production.
R&D and Innovation
Investing in research and development is crucial for addressing the quality and functionality challenges of alternative materials.
By innovating and testing new materials, food companies can find solutions that meet safety standards and consumer expectations, ensuring the newly adopted packaging fulfills its intended purposes effectively.
Consumer Education and Marketing
Educating consumers about the benefits of sustainable packaging can ease the transition to new materials.
Transparent communication regarding the environmental benefits and company commitments to sustainability can bolster consumer acceptance and brand loyalty.
Conclusion
While procurement issues pose significant challenges in the food industry’s shift to plastic substitute materials, these challenges are not insurmountable.
By strategically sourcing materials, managing costs, investing in innovation, and educating consumers, companies can successfully navigate the transition.
Embracing sustainable practices not only addresses environmental concerns but also positions businesses as forward-thinking and responsible in an increasingly eco-conscious market.
The road to reducing plastic dependency is paved with challenges, but the journey is essential for achieving long-term sustainability in the food industry.
資料ダウンロード
QCD調達購買管理クラウド「newji」は、調達購買部門で必要なQCD管理全てを備えた、現場特化型兼クラウド型の今世紀最高の購買管理システムとなります。
ユーザー登録
調達購買業務の効率化だけでなく、システムを導入することで、コスト削減や製品・資材のステータス可視化のほか、属人化していた購買情報の共有化による内部不正防止や統制にも役立ちます。
NEWJI DX
製造業に特化したデジタルトランスフォーメーション(DX)の実現を目指す請負開発型のコンサルティングサービスです。AI、iPaaS、および先端の技術を駆使して、製造プロセスの効率化、業務効率化、チームワーク強化、コスト削減、品質向上を実現します。このサービスは、製造業の課題を深く理解し、それに対する最適なデジタルソリューションを提供することで、企業が持続的な成長とイノベーションを達成できるようサポートします。
オンライン講座
製造業、主に購買・調達部門にお勤めの方々に向けた情報を配信しております。
新任の方やベテランの方、管理職を対象とした幅広いコンテンツをご用意しております。
お問い合わせ
コストダウンが利益に直結する術だと理解していても、なかなか前に進めることができない状況。そんな時は、newjiのコストダウン自動化機能で大きく利益貢献しよう!
(Β版非公開)