- お役立ち記事
- Procurement risks faced by purchasing departments and examples of how to overcome them
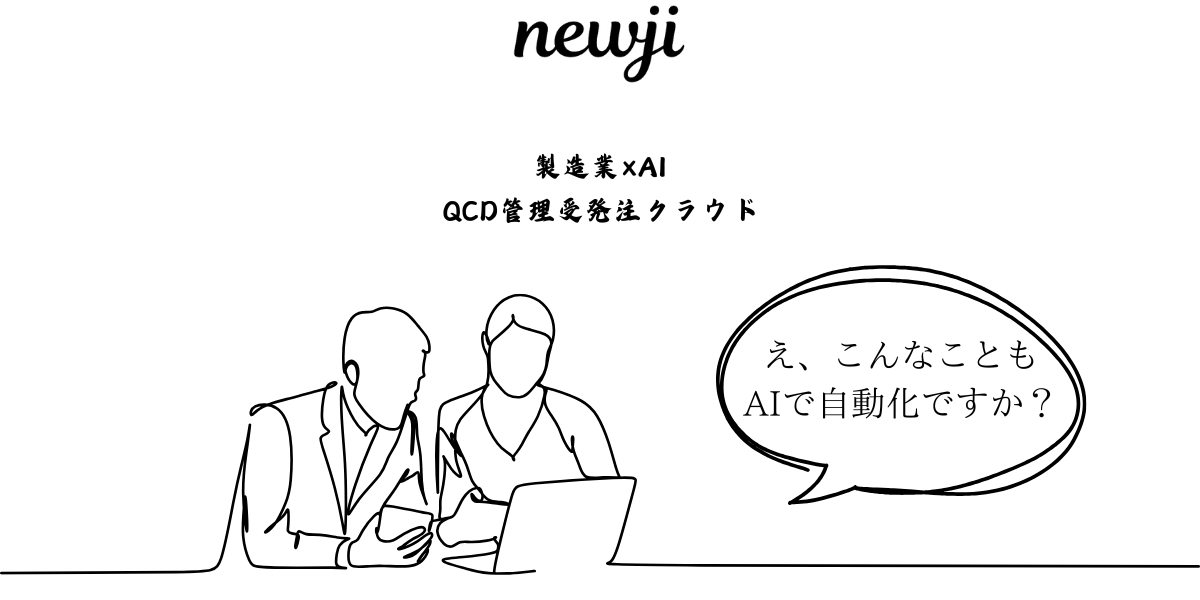
Procurement risks faced by purchasing departments and examples of how to overcome them
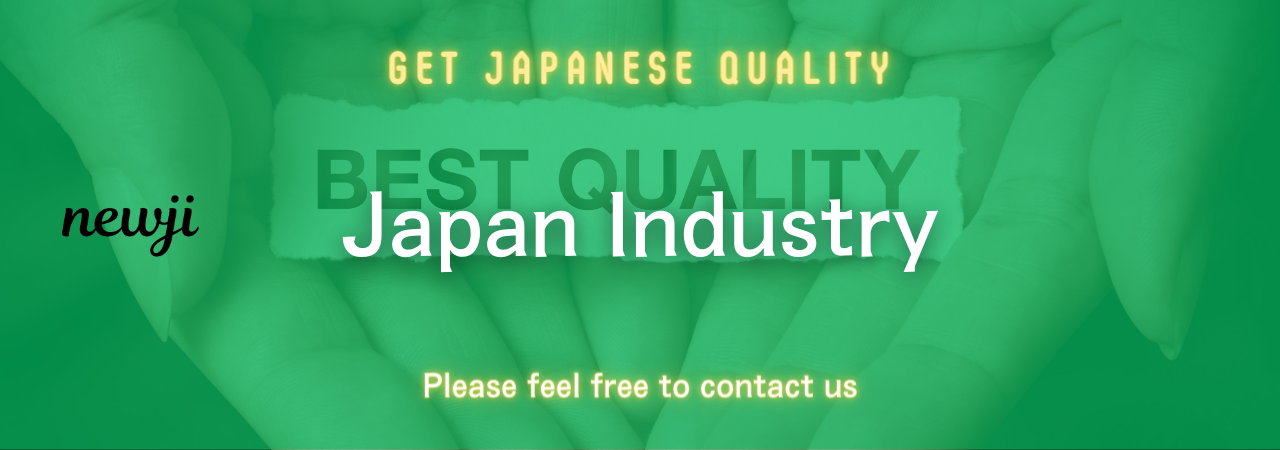
目次
Understanding Procurement Risks
Procurement is a critical function within any organization, ensuring that materials and services are acquired efficiently and cost-effectively.
However, purchasing departments face a multitude of risks that can impact their operations and the overall success of the business.
Understanding these risks allows organizations to better prepare and mitigate potential issues that may arise.
Supplier Reliability
One of the most significant risks is supplier reliability.
A dependable supplier relationship is vital for maintaining a consistent supply of goods.
Disruptions such as production delays, quality issues, or financial instability on the part of suppliers can significantly impact the purchasing department’s ability to meet the organization’s needs.
To overcome this, companies can perform thorough due diligence when choosing suppliers.
This includes evaluating their track record, financial health, and capacity to deliver consistently.
Additionally, developing multiple suppliers for critical items can reduce dependency on a single vendor, providing contingency options if issues arise with a primary supplier.
Cost Fluctuations
Market instability can lead to price fluctuations in raw materials and goods.
These changes can affect the budget and profitability of an organization, posing a significant risk to purchasing departments that operate under strict cost constraints.
To address cost fluctuations, businesses can engage in long-term contracts with fixed pricing.
Such agreements can provide predictability and protect against sudden market changes.
Moreover, purchasing departments can implement strategic sourcing and maintain a flexible procurement strategy to adapt to market trends and fluctuations.
Quality Assurance
Ensuring the quality of procured goods is paramount.
Low-quality materials can lead to production issues, increased costs, and customer dissatisfaction.
To mitigate this risk, businesses should establish stringent quality controls and standards.
Regular audits and evaluations of suppliers, alongside collaborative quality improvement plans, can help maintain high standards.
Additionally, fostering strong relationships with suppliers encourages commitment to quality and facilitates easier resolution of any issues that may arise.
Risk of Compliance Failures
Compliance with legal and regulatory standards is crucial in procurement.
Violating these can result in legal penalties, financial losses, and reputational damage.
Purchasing departments must keep abreast of changes in relevant laws and regulations, ensuring that procurement practices align with all requirements.
Implementing compliance checks and regular training for procurement personnel can further safeguard against potential compliance failures.
Supply Chain Disruptions
Unforeseen events such as natural disasters, political instability, or pandemics can cause significant disruptions in supply chains.
These disruptions can interfere with the timely delivery of goods, affecting the entire production process.
Developing a robust risk management strategy is vital to minimizing the impact of supply chain disruptions.
This includes creating contingency plans, identifying critical suppliers, and maintaining a stock of essential inventory.
Additionally, implementing digital supply chain management tools can provide real-time insights, allowing quicker response to unforeseen events.
Technological Threats
As procurement processes become increasingly digitalized, they are exposed to technological threats such as cyber attacks or system failures.
These threats can jeopardize the integrity of procurement data and disrupt operations.
Organizations should invest in robust cybersecurity measures to protect their procurement systems.
Regular software updates, data encryption, and cybersecurity training for employees can significantly reduce the risk of a cyber attack.
Furthermore, having a reliable IT support team can help quickly address any technological issues that may arise.
Managing Internal Risks
Internal risks such as inefficient processes, inadequate training, or lack of communication can lead to procurement failures.
These issues can result in missed deadlines, increased costs, and a decrease in overall procurement efficiency.
To overcome these internal risks, organizations should streamline procurement processes and invest in training for procurement staff.
Implementing automated systems can enhance efficiency and accuracy, reducing the potential for human error.
Moreover, fostering open communication within the procurement team and with other departments in the organization ensures alignment and a smoother procurement process.
Strategic Risk Management
A proactive approach to managing procurement risks involves strategic risk management.
This includes identifying potential risks, assessing their impact, and implementing measures to mitigate them.
Regular review and updates of risk management strategies ensure that organizations are prepared for any changes in the procurement landscape.
Risk management tools and technologies can assist in monitoring and averting potential procurement risks.
By adopting a strategic mindset, purchasing departments can not only manage risks effectively but also seize opportunities for continuous improvement and innovation.
Conclusion
Despite the numerous risks faced by purchasing departments, there are effective strategies to overcome them.
By understanding and proactively managing these risks, organizations can protect their operations and ensure a reliable and cost-effective procurement process.
Investing in technology, developing strong supplier relationships, and maintaining compliance are just a few ways to mitigate these risks effectively.
Ultimately, successful risk management in procurement not only safeguards the organization’s continuity but also enhances its competitive advantage.
資料ダウンロード
QCD調達購買管理クラウド「newji」は、調達購買部門で必要なQCD管理全てを備えた、現場特化型兼クラウド型の今世紀最高の購買管理システムとなります。
ユーザー登録
調達購買業務の効率化だけでなく、システムを導入することで、コスト削減や製品・資材のステータス可視化のほか、属人化していた購買情報の共有化による内部不正防止や統制にも役立ちます。
NEWJI DX
製造業に特化したデジタルトランスフォーメーション(DX)の実現を目指す請負開発型のコンサルティングサービスです。AI、iPaaS、および先端の技術を駆使して、製造プロセスの効率化、業務効率化、チームワーク強化、コスト削減、品質向上を実現します。このサービスは、製造業の課題を深く理解し、それに対する最適なデジタルソリューションを提供することで、企業が持続的な成長とイノベーションを達成できるようサポートします。
オンライン講座
製造業、主に購買・調達部門にお勤めの方々に向けた情報を配信しております。
新任の方やベテランの方、管理職を対象とした幅広いコンテンツをご用意しております。
お問い合わせ
コストダウンが利益に直結する術だと理解していても、なかなか前に進めることができない状況。そんな時は、newjiのコストダウン自動化機能で大きく利益貢献しよう!
(Β版非公開)