- お役立ち記事
- Procurement Standards for Housing Manufacturing SMEs to Know
Procurement Standards for Housing Manufacturing SMEs to Know
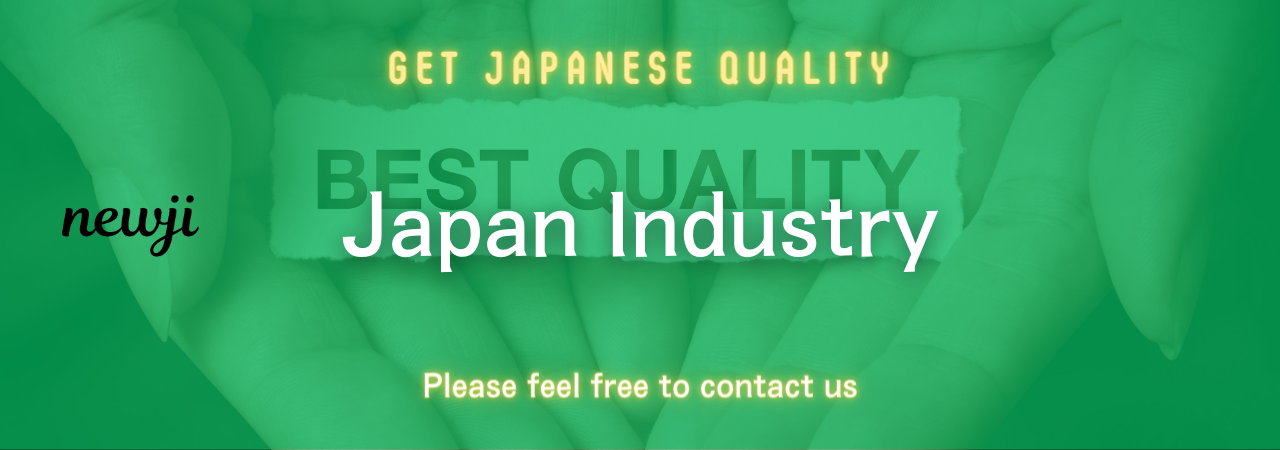
When running a small or medium enterprise (SME) in the housing manufacturing industry, understanding procurement standards is crucial for success.
Procurement is the process of obtaining goods and services, and following the right standards ensures efficiency, cost-effectiveness, and compliance with regulations.
This article will explore essential procurement standards that housing manufacturing SMEs need to know.
目次
Understanding Procurement Standards
Procurement standards outline the procedures and guidelines for acquiring products and services.
For SMEs in the housing manufacturing sector, these standards help in managing supply chains, selecting suppliers, and ensuring quality materials.
Knowing these standards can significantly improve business operations and customer satisfaction.
Importance of Procurement Standards
Procurement standards are essential for several reasons.
Firstly, they ensure that all materials and services acquired meet the necessary quality requirements.
This is vital in maintaining the integrity and safety of housing projects.
Secondly, these standards help in achieving cost efficiency.
By following specific guidelines, SMEs can avoid overpaying for materials and services, leading to better financial management.
Additionally, adhering to procurement standards ensures compliance with legal and regulatory requirements.
Not following the rules can result in fines and legal complications, which can be detrimental to the business.
Lastly, these standards help in building reputable relationships with suppliers.
When suppliers know that an SME follows rigorous procurement protocols, they are more likely to engage in long-term partnerships.
Key Procurement Standards for Housing Manufacturing SMEs
Understanding the critical procurement standards can help SMEs streamline their operations and achieve better results.
Here are some of the fundamental standards that housing manufacturing SMEs should follow.
Supplier Selection and Evaluation
Selecting the right supplier is one of the most crucial procurement decisions.
SMEs should establish a robust supplier selection process that includes evaluating the supplier’s reliability, quality of materials, and cost.
It is essential to conduct thorough background checks and assessments to ensure that the supplier can meet the required standards.
Additionally, regular supplier evaluations can help in maintaining consistent quality.
Setting up performance metrics and conducting periodic reviews will ensure that suppliers adhere to the agreed terms and conditions.
This helps in identifying any issues early and taking corrective measures promptly.
Quality Assurance
Quality assurance is a vital aspect of procurement in the housing manufacturing industry.
SMEs should implement stringent quality control measures to ensure that all materials and services meet the required standards.
This includes inspecting materials upon delivery and conducting regular quality audits.
Having a quality management system (QMS) in place can help in standardizing quality assurance procedures.
A QMS outlines the policies, processes, and procedures necessary for planning and execution.
It ensures consistency and helps in identifying areas that need improvement.
Cost Management
Effective cost management is crucial for the sustainability of any business.
SMEs should establish procurement budgets and track expenses to ensure that they stay within the allocated limits.
It is essential to implement cost control measures such as bulk purchasing and negotiating better terms with suppliers.
Additionally, conducting market research can help in understanding the price trends of materials and services.
This information can be used to make informed procurement decisions and avoid overpaying.
Automating the procurement process using digital tools can also help in cost savings by reducing manual errors and improving efficiency.
Compliance with Regulations
Housing manufacturing is heavily regulated, and non-compliance can have severe consequences.
SMEs should stay updated with the latest regulations and ensure that their procurement processes meet these requirements.
This includes following environmental standards, safety regulations, and obtaining necessary certifications.
Regular training and development programs can help employees stay informed about the regulatory changes and their implications on procurement.
Additionally, consulting with legal experts can provide insights into compliance requirements and help in implementing the necessary changes.
Supplier Relationship Management
Building and maintaining good relationships with suppliers is essential for successful procurement.
SMEs should focus on establishing trust and transparency with their suppliers.
Open communication and collaboration can help in addressing any issues and finding mutually beneficial solutions.
It is also important to recognize and reward good performance.
Acknowledging a supplier’s efforts can motivate them to maintain high standards and foster long-term partnerships.
Regular feedback sessions can help in understanding the supplier’s perspective and improving the procurement process.
Implementing Procurement Standards
Implementing procurement standards can seem daunting, but with the right approach, it is achievable.
Here are some steps that housing manufacturing SMEs can take to implement these standards effectively.
Develop a Procurement Policy
A well-documented procurement policy is the foundation for implementing procurement standards.
This policy should outline the objectives, procedures, and responsibilities related to procurement.
It should provide clear guidelines on supplier selection, quality assurance, cost management, compliance, and supplier relationship management.
The procurement policy should be communicated to all employees involved in the procurement process.
Regular training sessions can help in ensuring that everyone understands and follows the policy.
Invest in Technology
Technology can significantly improve the efficiency and accuracy of the procurement process.
Investing in procurement software can help in automating various tasks such as supplier evaluation, order processing, and expense tracking.
This can reduce manual errors and save time, allowing employees to focus on more strategic activities.
Additionally, data analytics can provide valuable insights into procurement trends and performance.
This information can be used to make data-driven decisions and improve the overall procurement process.
Monitor and Evaluate Performance
Regular monitoring and evaluation are essential to ensure that the procurement standards are being followed effectively.
SMEs should establish key performance indicators (KPIs) to measure the success of their procurement process.
These KPIs can include supplier performance, cost savings, compliance rates, and quality metrics.
Conducting regular audits and reviews can help in identifying any gaps and taking corrective actions.
Feedback from employees and suppliers can also provide insights into areas that need improvement.
Continuous Improvement
Procurement standards are not static, and continuous improvement is crucial for staying competitive.
SMEs should regularly review and update their procurement policies and procedures to reflect the latest industry trends and regulatory changes.
Encouraging innovation and creativity can also help in finding better ways to improve the procurement process.
In conclusion, understanding and implementing procurement standards is vital for the success of housing manufacturing SMEs.
By following these standards, SMEs can ensure quality, cost-effectiveness, and compliance in their procurement process.
With the right approach and continuous improvement, SMEs can build strong supplier relationships and achieve better business outcomes.
資料ダウンロード
QCD調達購買管理クラウド「newji」は、調達購買部門で必要なQCD管理全てを備えた、現場特化型兼クラウド型の今世紀最高の購買管理システムとなります。
ユーザー登録
調達購買業務の効率化だけでなく、システムを導入することで、コスト削減や製品・資材のステータス可視化のほか、属人化していた購買情報の共有化による内部不正防止や統制にも役立ちます。
NEWJI DX
製造業に特化したデジタルトランスフォーメーション(DX)の実現を目指す請負開発型のコンサルティングサービスです。AI、iPaaS、および先端の技術を駆使して、製造プロセスの効率化、業務効率化、チームワーク強化、コスト削減、品質向上を実現します。このサービスは、製造業の課題を深く理解し、それに対する最適なデジタルソリューションを提供することで、企業が持続的な成長とイノベーションを達成できるようサポートします。
オンライン講座
製造業、主に購買・調達部門にお勤めの方々に向けた情報を配信しております。
新任の方やベテランの方、管理職を対象とした幅広いコンテンツをご用意しております。
お問い合わせ
コストダウンが利益に直結する術だと理解していても、なかなか前に進めることができない状況。そんな時は、newjiのコストダウン自動化機能で大きく利益貢献しよう!
(Β版非公開)