- お役立ち記事
- Procurement strategy and transportation planning to achieve both efficient logistics and quality control
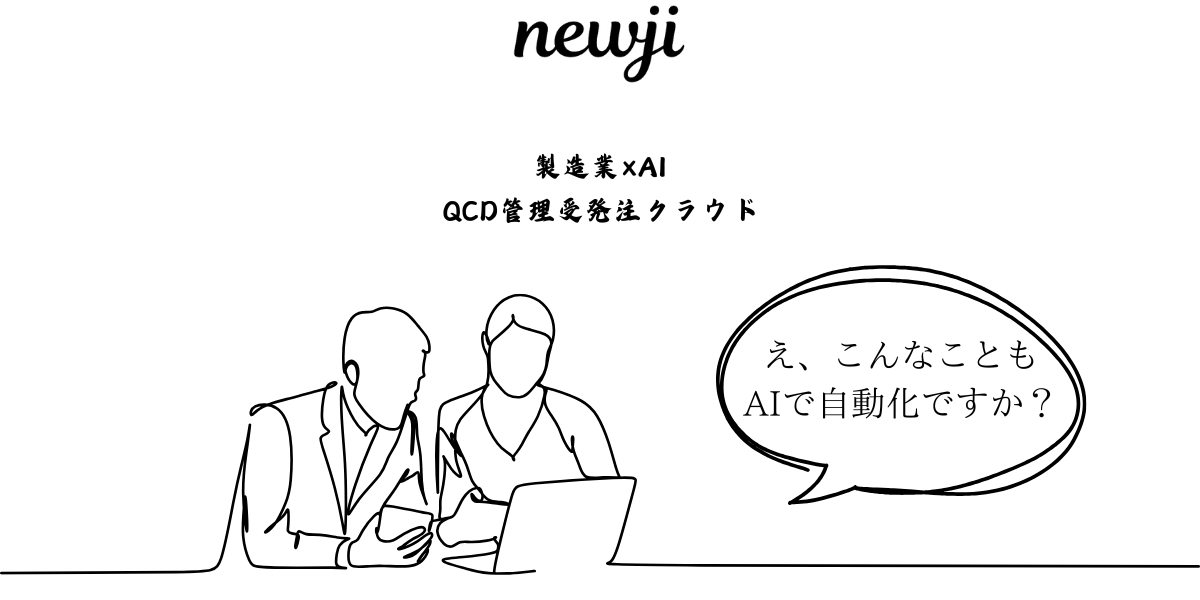
Procurement strategy and transportation planning to achieve both efficient logistics and quality control
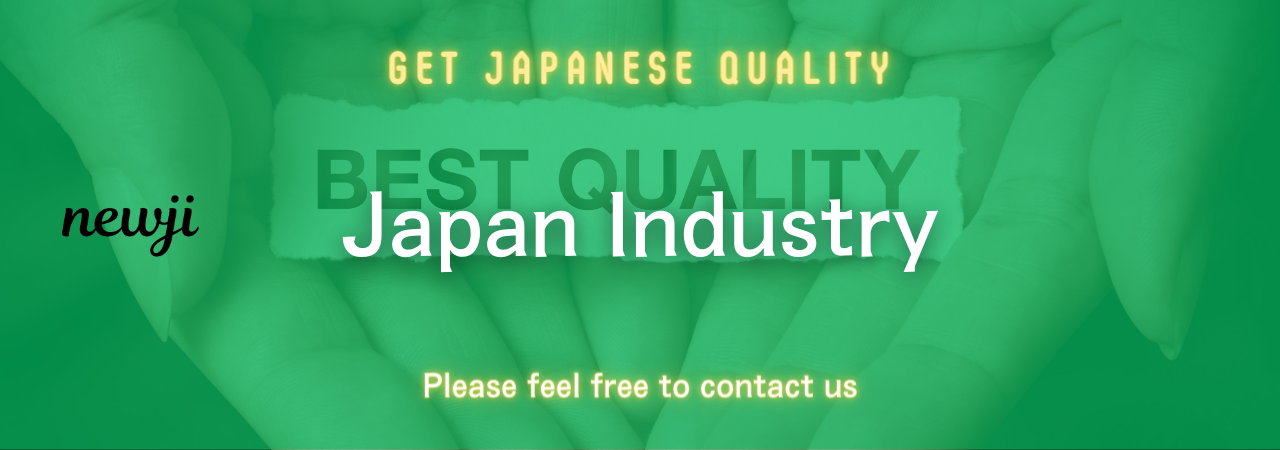
目次
Understanding Procurement Strategy
Procurement strategy is a critical component of any business seeking to streamline operations and enhance supply chain efficiency.
It involves the process of selecting suppliers, establishing payment terms, negotiating contracts, and managing supplier relationships.
A well-crafted procurement strategy helps businesses minimize costs, ensure the quality of goods and services, and meet delivery timelines.
A successful procurement strategy begins with a thorough analysis of the company’s needs and the markets where suppliers operate.
The goal is to align procurement activities with the broader business objectives, such as increasing market share, improving profit margins, and delivering top-notch products to customers.
It’s important to consider the type of procurement strategy that fits your organization’s needs.
Some strategies focus on cost reduction, while others emphasize building long-term supplier relationships or ensuring the diversity of the supplier base.
Understanding the specific needs and constraints of your organization is crucial in designing an effective procurement plan.
Components of a Robust Procurement Strategy
A comprehensive procurement strategy should include a variety of components.
Firstly, the identification and analysis of potential suppliers.
This means assessing the stability, reliability, and quality of products or services they offer.
Also, consider the ethical practices of suppliers and whether they align with your company values.
Secondly, a procurement strategy must include negotiation tactics.
Negotiations are not just about lowering prices but also ensuring that the terms are favorable for your long-term business goals.
Consider factors like delivery schedules, payment terms, and any penalties for non-compliance.
Finally, building and maintaining relationships with suppliers is crucial.
Relationships based on mutual trust and benefit can lead to more favorable terms and early access to new products.
Regular communication and feedback can help resolve potential issues before they become major problems.
Exploring Transportation Planning
Transportation planning is another vital aspect of logistics and supply chain management.
It involves designing and optimizing how goods move from suppliers to warehouses, between distribution centers, and finally to the end customers.
Effective transportation planning can significantly reduce costs, improve service quality, and enhance customer satisfaction by ensuring timely deliveries.
Transportation planning requires a firm grasp of team collaboration, route optimization, and real-time problem-solving skills.
Businesses must establish systems to oversee transportation networks, track shipments, and swiftly address any disruptions.
Key Elements of Transportation Planning
To achieve efficient logistics through transportation planning, consider the following elements:
1. **Selecting Suitable Carriers:** Understand the capabilities and reliability of transportation providers.
Evaluate whether their delivery networks match your geographic needs and if their services align with your operational requirements.
2. **Route Optimization:** Use modern technologies and software to find the most efficient routes for shipments.
Taking into account factors like traffic congestion, fuel costs, and delivery windows can help minimize delays and reduce transportation costs.
3. **Load Management:** Ensure that loads are maximally utilized without compromising the integrity of the goods.
Proper load management can lead to fewer trips and contribute to overall cost efficiency.
4. **Real-Time Tracking and Feedback:** Implement a system that allows for real-time tracking of shipments.
This can help anticipate potential delays and take corrective action promptly.
Clear communication channels with all parties involved ensure that critical issues are addressed swiftly.
Balancing Efficient Logistics with Quality Control
Balancing efficient logistics with quality control is a core challenge for any business.
While efficient logistics aim to minimize costs and improve delivery times, quality control ensures that the products meet the required standards and customer expectations.
When planning procurement and transportation strategies, it is essential to prioritize both efficiency and quality.
For instance, choosing a cheaper supplier might save costs initially, but could result in inferior products that affect customer satisfaction and return rates.
Similarly, optimizing routes for speed shouldn’t compromise the condition in which products are delivered.
Ensuring that your transportation methods maintain the quality of the goods is vital, especially for perishable items.
Strategies for Balancing the Two
1. **Vendor Evaluation and Quality Checks:** Conduct regular evaluations of suppliers to ensure they consistently meet quality standards.
Implement quality checks at various points of the supply chain to catch defects early.
2. **Advanced Planning Systems:** Utilize advanced software and planning systems to integrate procurement and transportation strategies.
These systems can offer valuable insights and forecast demands, optimizing both logistics and quality control in tandem.
3. **Invest in Staff Training:** Well-trained staff can adeptly manage both procurement and logistics operations.
Training programs can raise awareness of the importance of quality control alongside efficient logistics, fostering a culture of excellence.
4. **Feedback Loops:** Establish feedback mechanisms with both suppliers and customers.
This will help in identifying areas for improvement and ensuring that both logistics and quality control processes evolve with changing needs.
Conclusion
Achieving the perfect balance between efficient logistics and quality control requires strategic planning and a thorough understanding of procurement and transportation dynamics.
Businesses must adopt flexible and adaptive strategies that consider the complexities of modern supply chains.
By focusing on strong supplier relationships, advanced transportation planning, and a commitment to quality, companies can enhance their operational efficiency while delivering exceptional value to their customers.
資料ダウンロード
QCD調達購買管理クラウド「newji」は、調達購買部門で必要なQCD管理全てを備えた、現場特化型兼クラウド型の今世紀最高の購買管理システムとなります。
ユーザー登録
調達購買業務の効率化だけでなく、システムを導入することで、コスト削減や製品・資材のステータス可視化のほか、属人化していた購買情報の共有化による内部不正防止や統制にも役立ちます。
NEWJI DX
製造業に特化したデジタルトランスフォーメーション(DX)の実現を目指す請負開発型のコンサルティングサービスです。AI、iPaaS、および先端の技術を駆使して、製造プロセスの効率化、業務効率化、チームワーク強化、コスト削減、品質向上を実現します。このサービスは、製造業の課題を深く理解し、それに対する最適なデジタルソリューションを提供することで、企業が持続的な成長とイノベーションを達成できるようサポートします。
オンライン講座
製造業、主に購買・調達部門にお勤めの方々に向けた情報を配信しております。
新任の方やベテランの方、管理職を対象とした幅広いコンテンツをご用意しております。
お問い合わせ
コストダウンが利益に直結する術だと理解していても、なかなか前に進めることができない状況。そんな時は、newjiのコストダウン自動化機能で大きく利益貢献しよう!
(Β版非公開)