- お役立ち記事
- Procurement strategy promoted by purchasing department to reduce inventory and shorten lead time
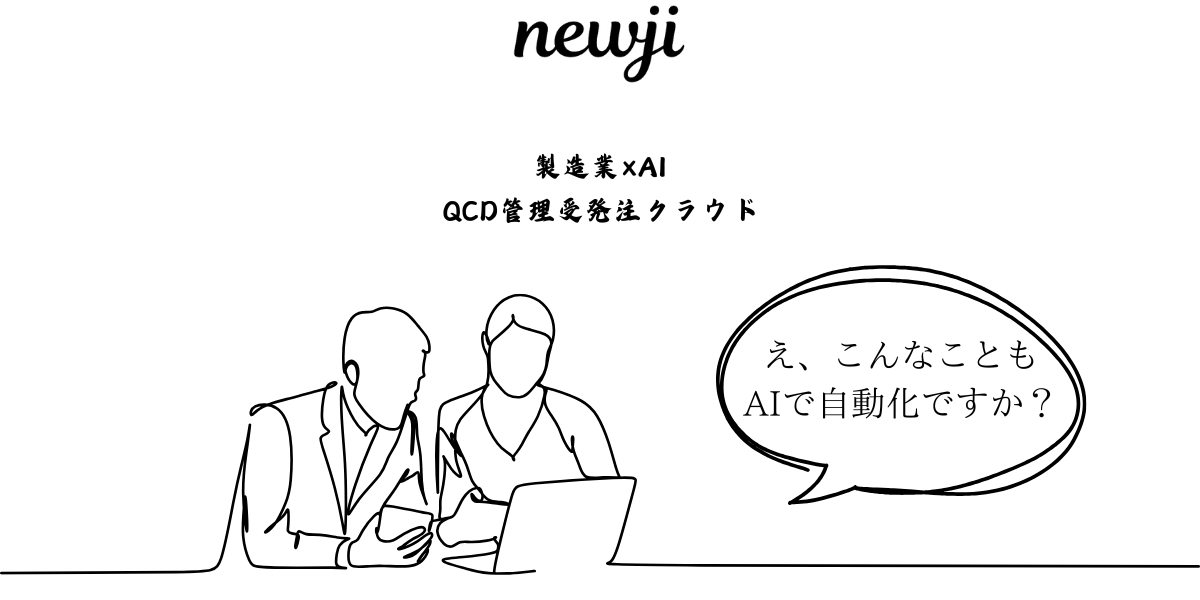
Procurement strategy promoted by purchasing department to reduce inventory and shorten lead time
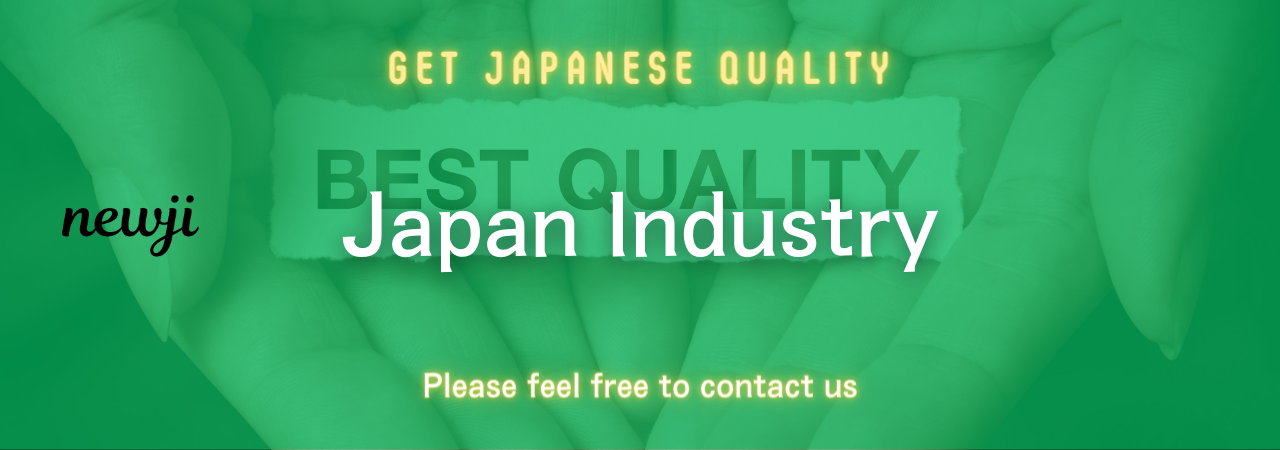
目次
Understanding Procurement Strategy
Procurement strategy is a plan implemented by a company to manage its purchasing activity.
It plays a significant role in reducing inventory and shortening lead times.
The purchasing department is at the core of this strategy, ensuring that the company efficiently acquires goods and services to meet its operational needs.
A well-designed procurement strategy helps companies achieve cost savings, improve supplier relationships, and enhance the overall supply chain performance.
By carefully selecting suppliers and negotiating favorable terms, businesses can reduce excess inventory and avoid stockouts.
This, in turn, helps minimize holding costs and improve cash flow.
The Role of the Purchasing Department
The purchasing department is crucial in implementing an effective procurement strategy.
This department is responsible for sourcing, negotiating, and purchasing goods needed for production and operations.
They ensure that the company gets the best value for its money while maintaining quality and reliability.
One of the primary functions of the purchasing department is to develop supplier relationships.
Strong, beneficial partnerships can lead to better prices, improved quality, and shorter lead times.
By working closely with suppliers, the purchasing department can negotiate favorable contracts and establish trust, which is essential for efficient procurement.
Additionally, the purchasing department continuously monitors market trends and supplier performance.
This ongoing evaluation allows them to identify opportunities for improvement and adjust strategies accordingly.
By staying informed, the department ensures that the procurement strategy aligns with the company’s goals and market conditions.
Strategies to Reduce Inventory
Reducing inventory is a key goal for many companies, as it helps decrease storage costs and minimizes the risk of obsolescence.
The purchasing department employs various strategies to achieve this goal.
One effective strategy is implementing a just-in-time (JIT) inventory system.
JIT ensures that materials and products are only ordered and received as needed for production.
This approach reduces excess inventory, as items are not stored for extended periods.
The purchasing department works closely with suppliers to schedule deliveries that align with production timelines.
Another strategy is demand forecasting.
By analyzing historical data and market trends, the purchasing department can predict future demand with greater accuracy.
This information allows them to order the right quantities of materials and avoid overstocking or understocking.
A third strategy involves optimizing order quantities.
The purchasing department analyzes order patterns and adjusts the amount ordered based on factors like supplier lead times, purchase frequency, and production needs.
By finding the optimal order size, they can reduce carrying costs and improve efficiency.
Ways to Shorten Lead Time
Shortening lead time is another critical objective of the procurement strategy.
Lead time refers to the time it takes from placing an order to receiving the goods or services.
Reducing this time frame enhances the company’s responsiveness and agility.
Supplier selection is pivotal in shortening lead time.
The purchasing department identifies suppliers that can meet deadlines and deliver consistently.
They evaluate a supplier’s delivery performance, production capacity, and reliability before forming a partnership.
Additionally, the purchasing department employs strategic sourcing.
Through strategic sourcing, companies gain access to multiple suppliers for the same product or service.
This approach diversifies the supply base, mitigates risks, and allows for competitive bidding.
Consequently, it can help reduce lead times when one supplier faces delays.
Technology also plays a role in shortening lead times.
Implementing robust procurement software can streamline processes, automate order tracking, and enhance communication with suppliers.
With real-time data, the purchasing department can make informed decisions quickly, reducing the time taken to address issues or make changes.
The Impact of Procurement Strategy on Business Efficiency
An effective procurement strategy contributes significantly to overall business efficiency.
By reducing inventory and shortening lead times, companies can operate more smoothly and predictably.
These improvements lead to increased customer satisfaction as they result in timely deliveries and high-quality products or services.
Additionally, cost savings achieved through effective procurement can be reinvested into the business for growth and development.
Companies can use these resources to explore new markets, improve products, or enhance the work environment for employees.
Finally, the procurement strategy promotes sustainability in business operations.
By optimizing inventory levels and reducing waste, companies minimize their environmental impact.
Sustainable practices can enhance brand reputation and customer loyalty, providing an edge over competitors.
Conclusion
In summary, procurement strategy is vital for any company aiming to reduce inventory and shorten lead times.
The purchasing department plays a crucial role in developing and implementing strategies to improve efficiency and cost-effectiveness.
By forming strong supplier relationships, leveraging technology, and employing data-driven decision-making, companies can optimize their purchasing activities.
Ultimately, a well-executed procurement strategy enhances business performance and sustainability, positioning companies for long-term success.
資料ダウンロード
QCD調達購買管理クラウド「newji」は、調達購買部門で必要なQCD管理全てを備えた、現場特化型兼クラウド型の今世紀最高の購買管理システムとなります。
ユーザー登録
調達購買業務の効率化だけでなく、システムを導入することで、コスト削減や製品・資材のステータス可視化のほか、属人化していた購買情報の共有化による内部不正防止や統制にも役立ちます。
NEWJI DX
製造業に特化したデジタルトランスフォーメーション(DX)の実現を目指す請負開発型のコンサルティングサービスです。AI、iPaaS、および先端の技術を駆使して、製造プロセスの効率化、業務効率化、チームワーク強化、コスト削減、品質向上を実現します。このサービスは、製造業の課題を深く理解し、それに対する最適なデジタルソリューションを提供することで、企業が持続的な成長とイノベーションを達成できるようサポートします。
オンライン講座
製造業、主に購買・調達部門にお勤めの方々に向けた情報を配信しております。
新任の方やベテランの方、管理職を対象とした幅広いコンテンツをご用意しております。
お問い合わせ
コストダウンが利益に直結する術だと理解していても、なかなか前に進めることができない状況。そんな時は、newjiのコストダウン自動化機能で大きく利益貢献しよう!
(Β版非公開)