- お役立ち記事
- Product design that takes into account the basics and workability of press working and molds, and effective defect countermeasures.
月間76,176名の
製造業ご担当者様が閲覧しています*
*2025年3月31日現在のGoogle Analyticsのデータより
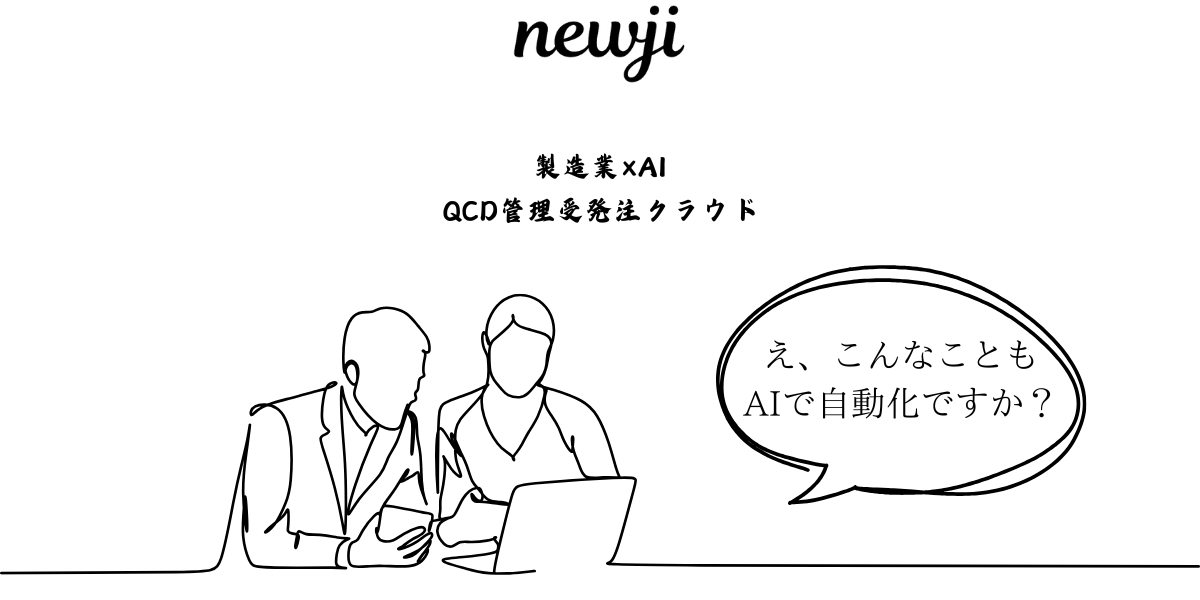
Product design that takes into account the basics and workability of press working and molds, and effective defect countermeasures.
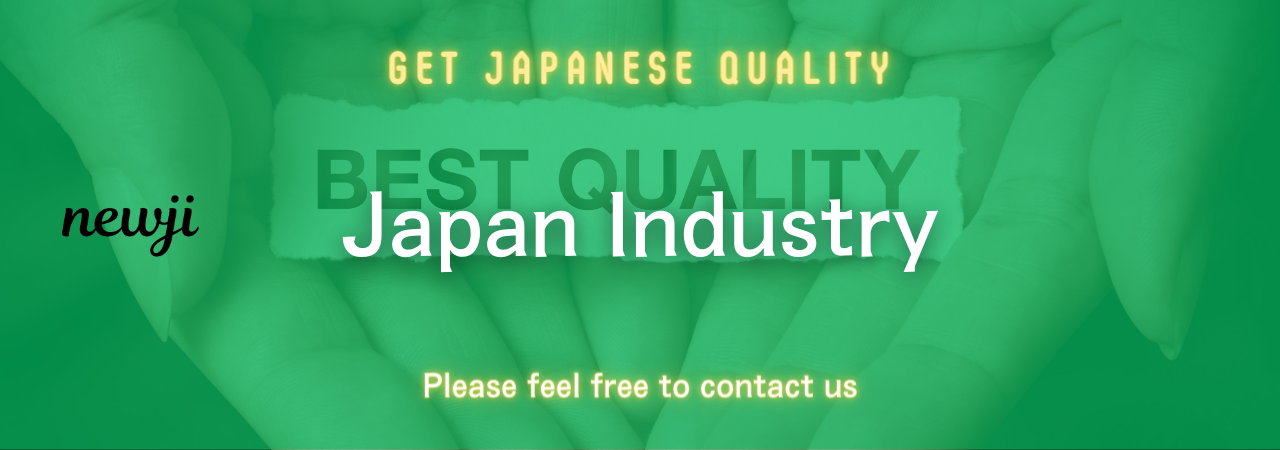
目次
Understanding the Basics of Press Working and Molds
Press working is a critical process in manufacturing that involves shaping metal sheets into desired forms using specialized machinery.
This shaping is often achieved through the application of pressure, hence the name “press working.”
Key components of this process include the press machine and molds, which are crafted to impart specific shapes to the metal workpieces.
The primary goal is to achieve efficient mass production while maintaining high precision and quality.
Molds, also known as dies, play a vital role in this process.
They are specially designed tools that determine the final shape of the finished product.
When designing molds, engineers must consider factors such as material selection, dimensional accuracy, and cost-effectiveness.
The complexity of the mold design increases with the intricacies of the desired product form.
Importance of Material Selection
Choosing the right material for both the workpiece and the mold is fundamental to successful press working.
The workpiece material must be malleable enough to be shaped without breaking while retaining the desired properties of the final product.
Common materials include steel, aluminum, and copper, each offering different benefits such as strength, weight, and corrosion resistance.
Molds are generally made from durable materials like tool steels or carbides to withstand repeated use without wearing down quickly.
The hardness and toughness of mold materials are crucial as they influence the lifespan and maintenance needs of the molds.
Effective Product Design Strategies
Designing a product with press working and mold functionality in mind requires careful consideration of various factors to ensure feasibility and efficiency.
Simplifying Product Geometry
Simplified product designs can lead to more straightforward mold designs and press operations.
Reducing the complexity of shapes minimizes the risk of defects and lowers production costs.
Whenever possible, aim for symmetrical and uniform designs that are easier to manufacture.
Considering factors such as drawability and material flow helps in creating designs that adapt well to the press working process.
Ensuring Dimensional Accuracy and Tolerances
Precision is key in producing parts that fit and function correctly.
Designers must define precise dimensional specifications and tolerances to ensure parts meet the desired standards.
Accounting for changes that occur during the pressing process, such as spring-back and material thinning, can aid in accurate dimension control.
Using simulation software can help predict and adjust for these changes, improving the reliability of the final product.
Addressing Common Defects in Press Working
Despite careful planning and design, defects can still occur in the press working process.
Knowing how to anticipate and counter these defects is crucial for maintaining product quality.
Cracking and Fracture
Cracking is a common defect that arises when the material undergoes excessive stress during forming.
To prevent cracking, it’s important to maintain proper lubrication and select appropriate materials that have high ductility.
Adjusting the die design and optimizing the pressing speed can also help reduce the occurrence of cracks.
Wrinkling and Warping
Wrinkling occurs when material buckles due to compressive forces during shaping.
This can be minimized by increasing the material’s rigidity or using blank holders to apply pressure and maintain flatness during pressing.
Warping, on the other hand, is deformation caused by uneven cooling or stress distribution.
Proper cooling methods and uniform stress application are key to preventing warping.
Burrs and Sharp Edges
Burrs or sharp edges often appear at the edges of pressed parts where excess material is not properly sheared off.
Implementing effective cutting and trimming techniques in the mold design can help eliminate this issue.
Additionally, post-processing methods like deburring can be used to smooth out edges and ensure safe handling.
Employing Advanced Technologies
Modern advancements in technology offer additional avenues for enhancing the press working and mold design process.
Simulation and Modeling Tools
Simulation tools allow designers to visualize and test their designs virtually before physical production.
This helps identify potential design flaws and optimize the manufacturing process reducing the risk of defects.
Modeling the entire pressing operation with finite element analysis (FEA) software can yield insights into how materials might react under pressure and allow for tweaks to the design accordingly.
Automated and Robotic Systems
Automation in press working has significantly improved the efficiency and consistency of production.
Robotic systems can handle repetitive tasks with precision, reducing human error and speeding up the manufacturing process.
Supervising the production line with automated systems ensures that press operations are carried out consistently according to set parameters.
By integrating these technologies, manufacturers can achieve better control over production quality and reduce downtime.
Conclusion
Understanding the fundamentals of press working and mold design is essential for producing high-quality and defect-free products.
By selecting the right materials, simplifying designs, preparing for potential defects, and integrating advanced technologies, manufacturers can optimize their press working operations.
This results in products that not only meet the required specifications but also adhere to high standards of quality and reliability.
Employing these strategies ensures efficient use of resources, ultimately leading to more sustainable and cost-effective manufacturing practices.
資料ダウンロード
QCD管理受発注クラウド「newji」は、受発注部門で必要なQCD管理全てを備えた、現場特化型兼クラウド型の今世紀最高の受発注管理システムとなります。
ユーザー登録
受発注業務の効率化だけでなく、システムを導入することで、コスト削減や製品・資材のステータス可視化のほか、属人化していた受発注情報の共有化による内部不正防止や統制にも役立ちます。
NEWJI DX
製造業に特化したデジタルトランスフォーメーション(DX)の実現を目指す請負開発型のコンサルティングサービスです。AI、iPaaS、および先端の技術を駆使して、製造プロセスの効率化、業務効率化、チームワーク強化、コスト削減、品質向上を実現します。このサービスは、製造業の課題を深く理解し、それに対する最適なデジタルソリューションを提供することで、企業が持続的な成長とイノベーションを達成できるようサポートします。
製造業ニュース解説
製造業、主に購買・調達部門にお勤めの方々に向けた情報を配信しております。
新任の方やベテランの方、管理職を対象とした幅広いコンテンツをご用意しております。
お問い合わせ
コストダウンが利益に直結する術だと理解していても、なかなか前に進めることができない状況。そんな時は、newjiのコストダウン自動化機能で大きく利益貢献しよう!
(β版非公開)