- お役立ち記事
- Production line layout design and productivity improvement know-how
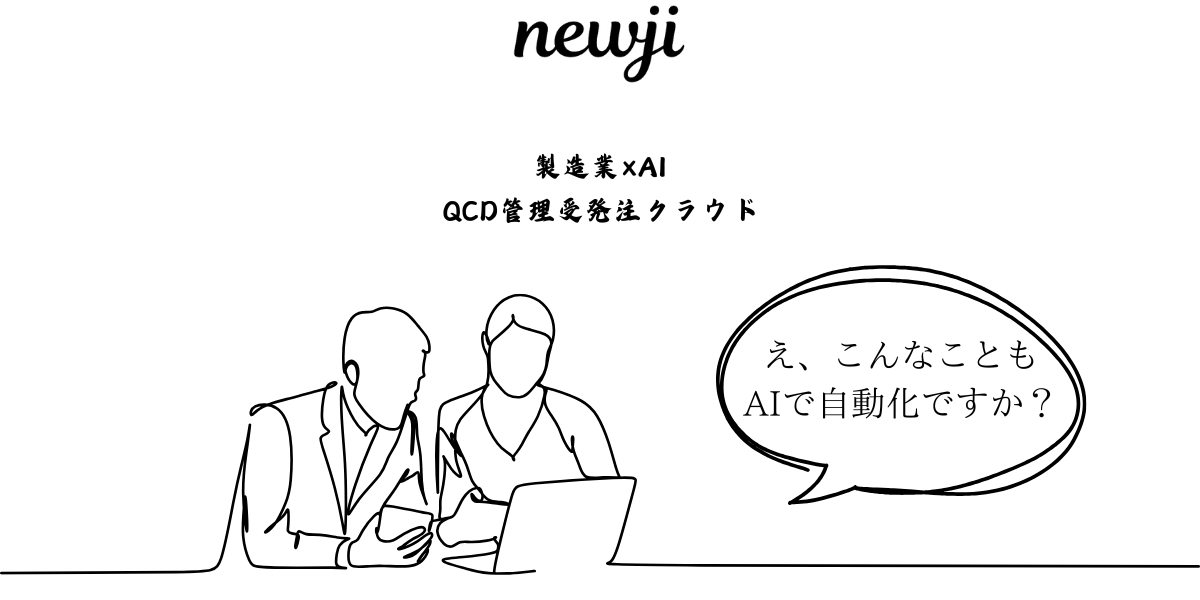
Production line layout design and productivity improvement know-how
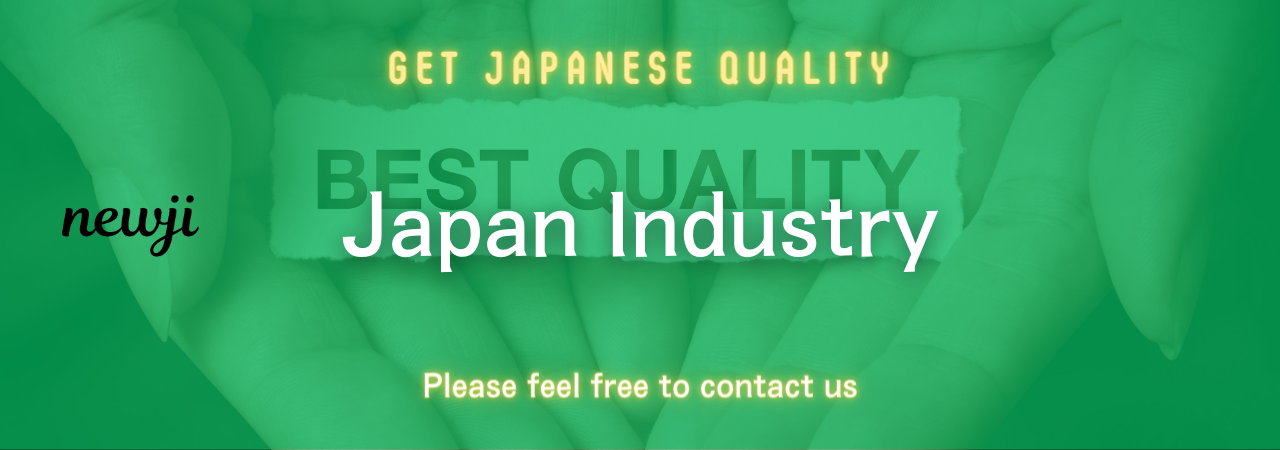
目次
Understanding Production Line Layout
A production line layout is a vital component of manufacturing processes, determining how different workstations are arranged and how materials flow between them.
An effective layout can streamline operations, reduce waste, and enhance productivity.
When setting up a production line, it’s important to consider product types, volumes, and the processes required.
By identifying these factors, manufacturers can choose an optimal layout type, whether it’s a product layout, process layout, cellular layout, or a combination of several types.
Types of Production Line Layouts
1. **Product Layout**: This layout is used when producing a single product in large volumes.
Workstations are arranged in a sequence where specific tasks are performed step-by-step, ideal for assembly lines.
2. **Process Layout**: Suitable for manufacturing different products with varying requirements.
Workstations are grouped according to the type of operation, giving flexibility to manage diverse production tasks.
3. **Cellular Layout**: Combines elements of both product and process layouts.
Workstations are arranged in cells, each capable of completing a product or a part, enhancing efficiency and flexibility.
Steps to Improve Layout for Enhanced Productivity
A well-thought-out production line can significantly boost productivity.
Here are practical steps to optimize your factory layout:
Conduct a Detailed Analysis
Begin with a thorough analysis of your current production processes and layouts.
Identify bottlenecks, redundant tasks, and areas that can be improved.
Mapping out the current workflow and gathering data on production times, delays, and equipment usage can offer insights into areas that need attention.
Engage Stakeholders
Incorporate input from employees, supervisors, and managers who are familiar with the daily operations.
Their feedback can provide valuable information on problems with the current setup and suggestions for improvement.
Collaboration is key to creating a layout that meets operational needs while also being user-friendly.
Utilize Technology
Integrate technology such as computer-aided design (CAD) tools to visualize potential layout changes before implementation.
Simulation software can model different scenarios, allowing you to see how each change might impact productivity and efficiency.
This tech-forward approach can reduce errors and enhance decision-making.
Prioritize Workflow Efficiency
Focus on creating a seamless workflow that minimizes unnecessary movement of materials and personnel.
Each station should be positioned to reduce the travel distance of workers and materials.
Consider how parts, inventory, and products move from one station to another.
Implement strategies like just-in-time inventory to reduce waste and ensure materials are available when needed.
Implement Lean Manufacturing Principles
Lean manufacturing principles aim to maximize value by eliminating waste.
Adopt practices like the 5S method (Sort, Set in order, Shine, Standardize, Sustain) to maintain an organized and efficient workspace.
Continuous improvement (Kaizen) encourages regular evaluation and improvement of workflows.
Regular Training and Development
Keeping your workforce trained on new technologies and practices ensures they are equipped to operate within updated layouts.
Training sessions can emphasize the importance of efficiency in production processes and cultivate a culture of ongoing improvement.
Measuring the Success of Your Layout
Once you’ve implemented new layout changes, it’s essential to measure their impact on productivity.
Key Performance Indicators (KPIs)
Track specific KPIs to gauge the effectiveness of your layout adjustments.
Consider metrics like production time, equipment downtime, defect rates, and employee efficiency.
Comparing before and after results can provide a clear picture of improvements.
Quality and Output
Improvement in product quality and overall output should be monitored closely.
Higher quality often indicates increased efficiency and better resource management.
Consistent output and reduced defects suggest that the new layout supports a higher level of productivity.
Feedback Loop
Regularly seek feedback from team members about the new layout.
Their firsthand experiences reveal crucial information about ongoing challenges or benefits.
Encourage open communication and be willing to make further adjustments based on this feedback.
Conclusion
Designing and implementing an effective production line layout requires careful planning, stakeholder engagement, and a willingness to adapt and optimize.
By focusing on efficiency, embracing technology, and fostering continuous improvement, manufacturers can significantly boost productivity and ensure a streamlined operation that meets their specific production goals.
資料ダウンロード
QCD調達購買管理クラウド「newji」は、調達購買部門で必要なQCD管理全てを備えた、現場特化型兼クラウド型の今世紀最高の購買管理システムとなります。
ユーザー登録
調達購買業務の効率化だけでなく、システムを導入することで、コスト削減や製品・資材のステータス可視化のほか、属人化していた購買情報の共有化による内部不正防止や統制にも役立ちます。
NEWJI DX
製造業に特化したデジタルトランスフォーメーション(DX)の実現を目指す請負開発型のコンサルティングサービスです。AI、iPaaS、および先端の技術を駆使して、製造プロセスの効率化、業務効率化、チームワーク強化、コスト削減、品質向上を実現します。このサービスは、製造業の課題を深く理解し、それに対する最適なデジタルソリューションを提供することで、企業が持続的な成長とイノベーションを達成できるようサポートします。
オンライン講座
製造業、主に購買・調達部門にお勤めの方々に向けた情報を配信しております。
新任の方やベテランの方、管理職を対象とした幅広いコンテンツをご用意しております。
お問い合わせ
コストダウンが利益に直結する術だと理解していても、なかなか前に進めることができない状況。そんな時は、newjiのコストダウン自動化機能で大きく利益貢献しよう!
(Β版非公開)