- お役立ち記事
- Production line layout design for automation and design know-how to improve productivity
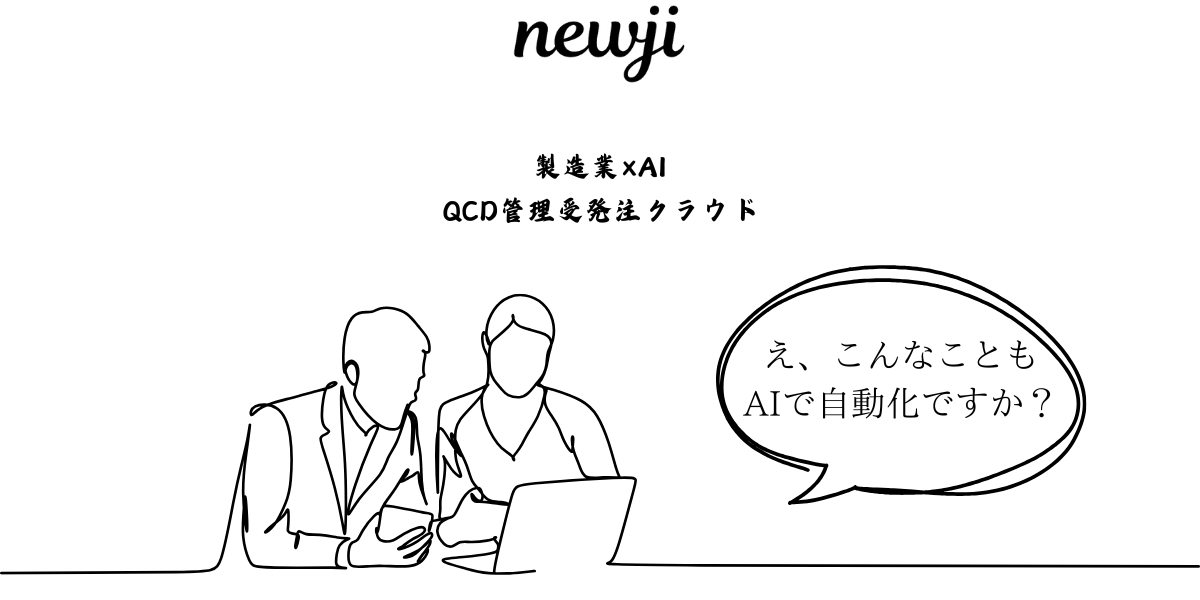
Production line layout design for automation and design know-how to improve productivity
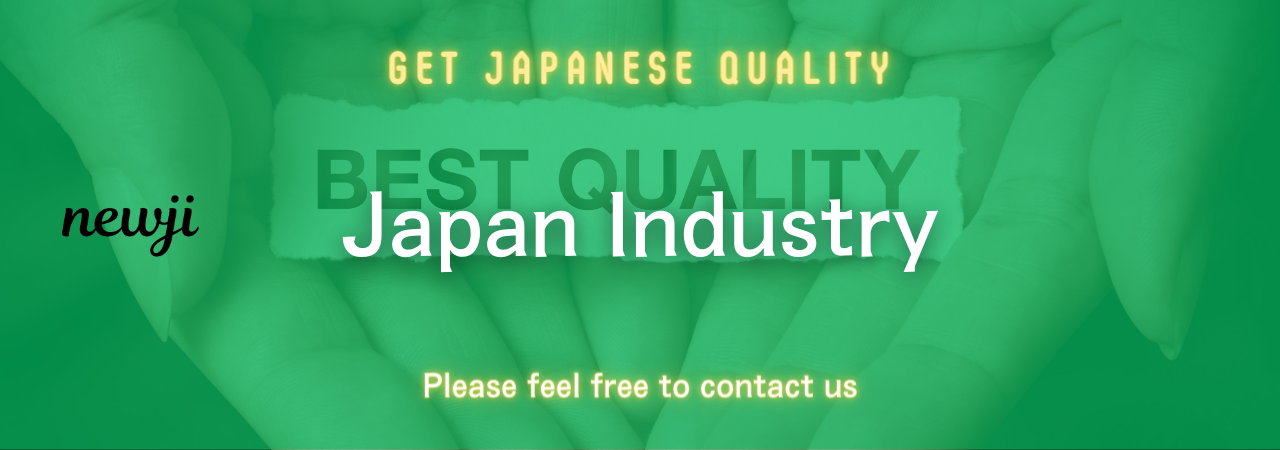
目次
Introduction to Production Line Layout Design
In today’s fast-paced industrial world, optimizing production processes is key to staying competitive.
One crucial aspect of this optimization is the design of the production line layout.
This involves arranging equipment, workstations, and materials for maximum efficiency and productivity.
When executed well, it can significantly enhance workflow, reduce costs, and ensure flexibility in adapting to new products or technologies.
The Importance of Automation in Production Lines
Automation in production lines plays a pivotal role in enhancing productivity.
By employing automated machinery and technology, manufacturers can produce goods at a faster rate with consistent quality.
Automation reduces the dependency on manual labor, minimizes human error, and allows for the continuity of operations without the constraints of human fatigue.
Moreover, automated systems can be programmed for complex tasks that would be challenging for human operators.
This not only increases efficiency but also helps in maintaining safety standards by handling hazardous or repetitive tasks.
Key Elements in Designing an Automated Production Line
1. Workflow Optimization
The first step in production line design is optimizing the workflow.
The layout should facilitate a seamless flow of materials and products from one stage to the next.
This involves minimizing unnecessary movements and ensuring that each component is located where it needs to be to reduce bottlenecks and improve efficiency.
2. Flexibility and Scalability
An effective production line design should accommodate changes in production requirements.
This includes being scalable for increases in production volume and flexible enough to adapt to new products or processes.
Designing modular systems with interchangeable parts can help in achieving these goals.
3. Space Utilization
Maximizing the use of available space is critical in any production line layout.
Efficient use of space can reduce the need for larger facilities and allow for more streamlined operations.
This involves careful planning to ensure that every piece of equipment is ideally placed for optimal function.
4. Safety Considerations
Safety should never be compromised in a production line.
Designing with safety in mind involves placing safety barriers, emergency stops, and easy access points for maintenance.
Ensuring operators are trained to interact safely with automated systems is also essential.
Step-by-Step Process of Designing a Production Line
1. Assessing Current Capabilities
Before embarking on a new design, it’s vital to understand the current production capabilities and limitations.
This assessment will highlight areas of improvement and set realistic goals for the new layout.
2. Defining Objectives and Requirements
Clear objectives need to be set for what the production line redesign aims to achieve.
These can include increased output, reduced costs, improved safety, or enhanced flexibility.
Understanding these requirements will guide the entire design process.
3. Developing a Design Concept
With objectives in mind, the next step is to create a draft of the new layout.
This includes selecting the types of automation technology to be used, determining the optimal arrangement of equipment, and planning the flow of materials.
4. Simulation and Testing
Before full-scale implementation, it’s crucial to simulate the new layout through computer models or small-scale prototypes.
Testing the design helps identify potential issues and allows for adjustments before making significant investments.
5. Implementation and Monitoring
Once the design is finalized, executing the plan involves careful project management to ensure minimal disruption to operations.
After implementation, ongoing monitoring and evaluation are essential to ensure the new layout meets the desired productivity improvements.
Tips for Successful Production Line Design
Prioritize Communication
Clear communication between design teams, engineers, and operators is crucial for a successful design.
Involving all stakeholders from the beginning ensures buy-in and reduces misunderstandings.
Embrace Technological Advances
Staying abreast of the latest technological advancements can provide opportunities to integrate state-of-the-art solutions into your design.
This could range from advanced robotics to sophisticated data analytics systems.
Continuous Improvement
Production line design is not a one-time effort.
Regular reviews and updates should be conducted to ensure the system remains efficient as production needs change or new technology becomes available.
Conclusion
Designing a production line layout for automation is a complex but rewarding process.
When done correctly, it enhances productivity, ensures quality, and can even reduce operational costs.
By focusing on optimizing workflows, embracing automation, and making space and safety a priority, manufacturers can create a robust and efficient production environment.
As technology continues to evolve, staying flexible and open to continuous improvement will be key to future success.
資料ダウンロード
QCD調達購買管理クラウド「newji」は、調達購買部門で必要なQCD管理全てを備えた、現場特化型兼クラウド型の今世紀最高の購買管理システムとなります。
ユーザー登録
調達購買業務の効率化だけでなく、システムを導入することで、コスト削減や製品・資材のステータス可視化のほか、属人化していた購買情報の共有化による内部不正防止や統制にも役立ちます。
NEWJI DX
製造業に特化したデジタルトランスフォーメーション(DX)の実現を目指す請負開発型のコンサルティングサービスです。AI、iPaaS、および先端の技術を駆使して、製造プロセスの効率化、業務効率化、チームワーク強化、コスト削減、品質向上を実現します。このサービスは、製造業の課題を深く理解し、それに対する最適なデジタルソリューションを提供することで、企業が持続的な成長とイノベーションを達成できるようサポートします。
オンライン講座
製造業、主に購買・調達部門にお勤めの方々に向けた情報を配信しております。
新任の方やベテランの方、管理職を対象とした幅広いコンテンツをご用意しております。
お問い合わせ
コストダウンが利益に直結する術だと理解していても、なかなか前に進めることができない状況。そんな時は、newjiのコストダウン自動化機能で大きく利益貢献しよう!
(Β版非公開)