- お役立ち記事
- Production Line Optimization Techniques Using Motion Analysis
月間76,176名の
製造業ご担当者様が閲覧しています*
*2025年3月31日現在のGoogle Analyticsのデータより
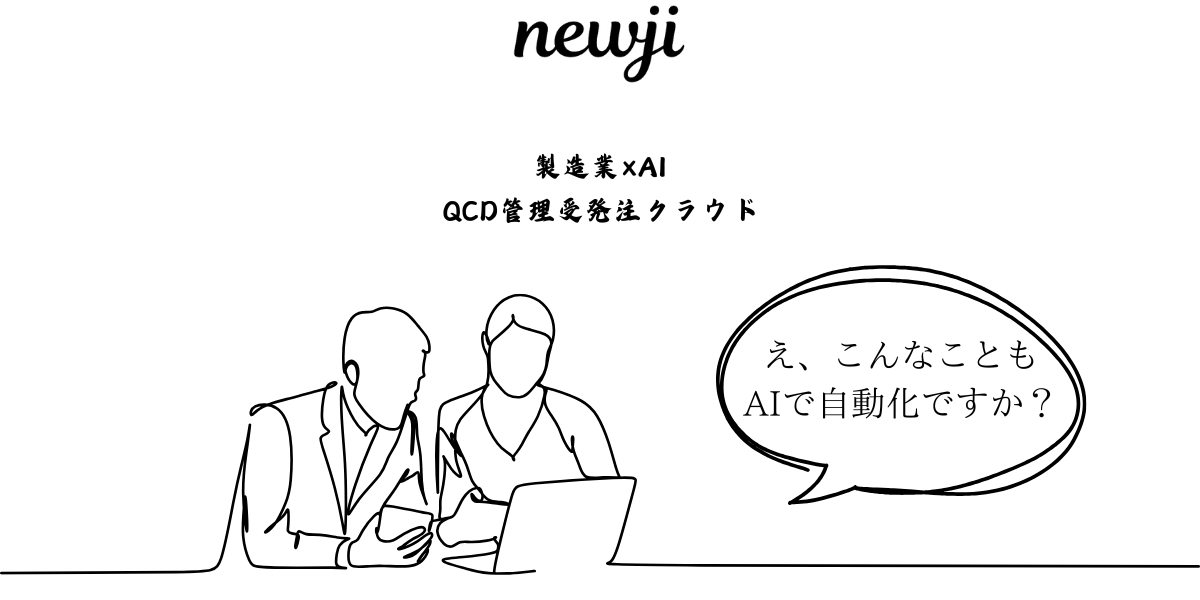
Production Line Optimization Techniques Using Motion Analysis
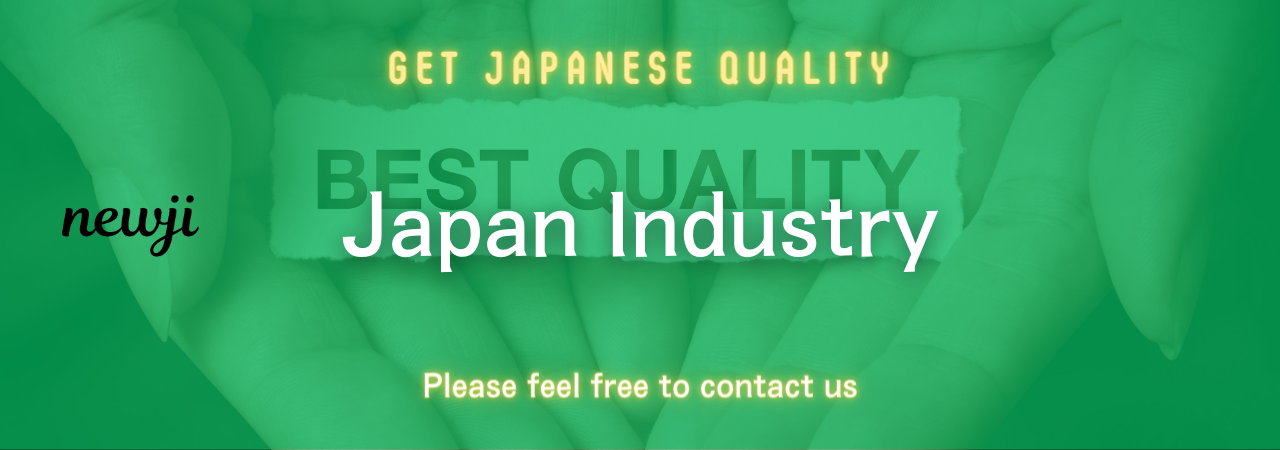
Production line optimization is essential for businesses to improve efficiency, reduce costs, and boost overall productivity.
One technique that has gained attention is motion analysis.
This technology helps in identifying inefficiencies and making informed decisions to enhance operations.
目次
What is Motion Analysis?
Motion analysis is a method of capturing and assessing the movements of workers, machines, or materials in a production line.
It uses specialized cameras and sensors to track the motion and provides data for further analysis.
This data helps in understanding the workflow and identifying areas for improvement.
Benefits of Using Motion Analysis in Production Lines
1. Enhanced Efficiency
By analyzing the movements in a production line, companies can pinpoint inefficiencies.
For instance, if certain tasks are taking longer than expected, it could be due to unnecessary movements or poorly designed workflows.
By addressing these issues, companies can enhance their overall efficiency.
2. Reduced Costs
Inefficient workflows often lead to wasted time and resources.
Motion analysis helps identify these inefficiencies, allowing companies to make necessary adjustments.
This leads to reduced operational costs and improved profit margins.
Cost savings can also be reinvested into the business for further improvements.
3. Improved Worker Safety
Motion analysis doesn’t just help with productivity; it also aids in improving workplace safety.
By monitoring how workers move and interact with equipment, potential hazards can be identified.
This information can be used to redesign workspaces or provide additional training to ensure that safety protocols are being followed.
4. Data-Driven Decision Making
With the detailed data provided by motion analysis, companies can make informed decisions.
Rather than relying on guesswork or anecdotal evidence, managers can now look at precise data to understand where changes need to be made.
This data-driven approach ensures that adjustments are effective and based on solid evidence.
Steps to Implement Motion Analysis in Production Lines
1. Identify Key Areas for Analysis
Begin by identifying areas within the production line that require optimization.
Focus on sections where delays or inefficiencies frequently occur.
This targeted approach ensures that efforts are concentrated on areas with the most potential for improvement.
2. Set Up the Necessary Equipment
Invest in the necessary cameras, sensors, and software to capture motion data.
Make sure the equipment is appropriately positioned to capture all crucial movements.
It may also be helpful to conduct a small trial run to ensure everything is working correctly before fully implementing the system.
3. Collect and Analyze Data
Once the equipment is set up, begin collecting data.
Allow the system to run for a sufficient period to gather enough information for analysis.
Use specialized software to interpret the collected data.
Look for patterns, bottlenecks, and areas where improvements can be made.
4. Make Necessary Adjustments
Based on the analysis, make the required adjustments to the workflow.
This might involve rearranging equipment, altering the steps in a task, or providing additional training to workers.
Continue monitoring the production line with motion analysis to ensure that the changes are effective.
5. Continuous Improvement
Motion analysis should not be a one-time effort.
It should be part of a continuous improvement strategy.
Regularly review the data, make necessary adjustments, and keep seeking ways to enhance the production line’s performance.
Challenges in Implementing Motion Analysis
1. Initial Investment
One of the biggest challenges is the initial investment in equipment and software.
While the long-term benefits often outweigh these costs, the upfront expenditure can be significant.
Companies need to carefully consider their budget and look for cost-effective solutions.
2. Resistance to Change
Employees may be resistant to new technologies or changes in their workflows.
It’s important to involve them in the process and explain how motion analysis will benefit them and the company as a whole.
Providing proper training and support can help in overcoming this resistance.
3. Data Privacy Concerns
With the increasing focus on data privacy, companies need to ensure that the data collected through motion analysis is handled responsibly.
This involves implementing robust data protection measures and ensuring compliance with relevant regulations.
Conclusion
Optimizing production lines through motion analysis offers numerous benefits, including enhanced efficiency, reduced costs, improved worker safety, and data-driven decision-making.
While there are challenges to implementing this technology, the potential gains make it a worthwhile investment.
By following the steps outlined to implement motion analysis, companies can make significant strides in improving their production processes.
Continuous improvement and regular analysis ensure that the production line remains efficient and effective in the long term.
Motion analysis represents a powerful tool in the quest for production line optimization.
Embracing this technology can help businesses stay competitive and meet the demands of modern manufacturing.
資料ダウンロード
QCD管理受発注クラウド「newji」は、受発注部門で必要なQCD管理全てを備えた、現場特化型兼クラウド型の今世紀最高の受発注管理システムとなります。
ユーザー登録
受発注業務の効率化だけでなく、システムを導入することで、コスト削減や製品・資材のステータス可視化のほか、属人化していた受発注情報の共有化による内部不正防止や統制にも役立ちます。
NEWJI DX
製造業に特化したデジタルトランスフォーメーション(DX)の実現を目指す請負開発型のコンサルティングサービスです。AI、iPaaS、および先端の技術を駆使して、製造プロセスの効率化、業務効率化、チームワーク強化、コスト削減、品質向上を実現します。このサービスは、製造業の課題を深く理解し、それに対する最適なデジタルソリューションを提供することで、企業が持続的な成長とイノベーションを達成できるようサポートします。
製造業ニュース解説
製造業、主に購買・調達部門にお勤めの方々に向けた情報を配信しております。
新任の方やベテランの方、管理職を対象とした幅広いコンテンツをご用意しております。
お問い合わせ
コストダウンが利益に直結する術だと理解していても、なかなか前に進めることができない状況。そんな時は、newjiのコストダウン自動化機能で大きく利益貢献しよう!
(β版非公開)