- お役立ち記事
- Production planning techniques to shorten lead times that purchasing departments should know
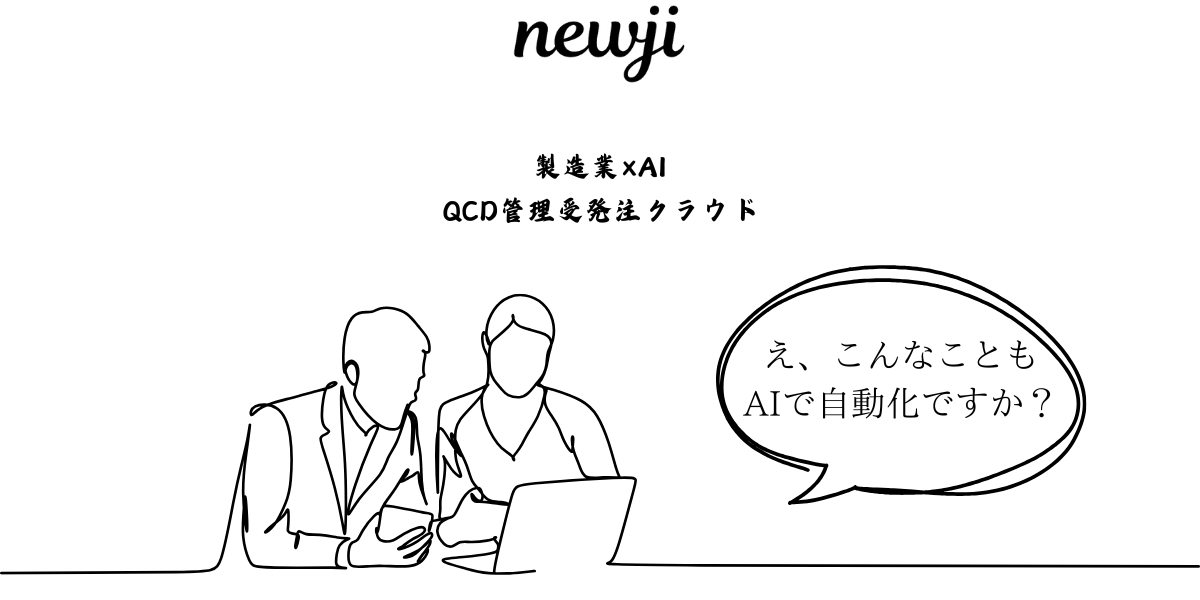
Production planning techniques to shorten lead times that purchasing departments should know
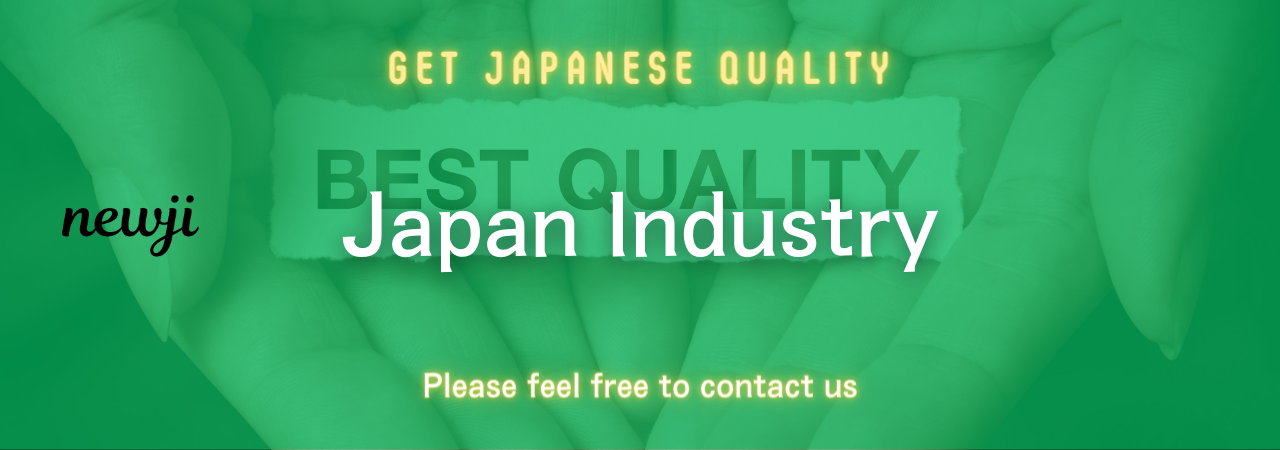
目次
Understanding Lead Times
Production planning is an essential aspect of any manufacturing process, aiming to optimize efficiency and reduce the time it takes to produce and deliver goods.
For purchasing departments, understanding and implementing techniques to shorten lead times can significantly impact overall productivity and customer satisfaction.
Lead time is the period it takes from the initiation of a process until its completion, specifically in the context of manufacturing and supply chain management.
Reducing lead times can improve a company’s competitiveness by enabling faster delivery of products to market and reducing inventory costs.
Importance of Shortening Lead Times
For any business dealing with manufacturing, shorter lead times translate to increased flexibility and responsiveness to market demands.
Customers expect quick and reliable service, and fulfilling those expectations often relies on how effectively a company manages its lead times.
Streamlining production and supply chain processes can lead to better resource utilization, reduced manufacturing costs, and improved cash flow.
Furthermore, shorter lead times can make a company more responsive to unexpected changes in customer demand or market conditions, thereby maintaining or even enhancing business competitiveness.
Demand Forecasting and Planning
One effective technique for shortening lead times is robust demand forecasting and planning.
Accurate forecasting helps businesses predict customer demand more reliably, allowing them to adjust production schedules accordingly.
By aligning production with demand, companies can minimize delays and avoid overproduction, which can lead to increased inventory costs and wasted resources.
Sophisticated analytical tools combined with historical data and market trends can significantly enhance a company’s forecasting accuracy.
This, in turn, helps in planning material purchases more effectively, minimizing the waiting time for production to begin, and ensuring resources are available when needed.
Just-In-Time (JIT) Manufacturing
Another critical technique is the implementation of Just-In-Time (JIT) manufacturing, a strategy that focuses on reducing waste and enhancing production efficiency.
In JIT manufacturing, materials and components are ordered and received exactly when they are needed in the production process.
By reducing the inventory levels, companies can lower storage costs and minimize the risks related to obsolete stock.
Moreover, this approach ensures that production systems are lean and agile, facilitating quicker responses to changes in demand and reducing lead times significantly.
Streamlining Supplier Relationships
Effective supplier relationship management is crucial to shortening lead times.
By building strong partnerships with reliable suppliers, companies can ensure timely delivery of materials and components essential for production.
Establishing clear communication channels and set expectations with suppliers can enhance transparency throughout the supply chain.
Collaborative forecasting and inventory management can help synchronize operations, resulting in fewer delays and lead time reduction.
Moreover, businesses should evaluate and select suppliers based on their capability to deliver on time and meet quality standards consistently.
Automating Production Processes
The use of technology and automation is another powerful way to reduce lead times.
Implementing modern manufacturing technologies such as automation and robotics can streamline production processes, decreasing the cycle time and minimizing human error.
Automation technologies enable faster transitions between production stages, improve precision, and allow businesses to scale up production quickly without sacrificing quality.
Automating repetitive tasks frees up human resources to focus on more strategic activities, further enhancing operational efficiency.
Improving Internal Workflow
Internally, improving workflow processes can substantially reduce lead times.
Mapping and analyzing existing processes can help identify bottlenecks and inefficiencies, providing an opportunity to re-engineer them for enhanced performance.
Implementing continuous improvement methodologies such as Lean or Six Sigma can drive process optimization and eliminate waste, contributing to faster lead times.
Emphasizing employee training and development ensures that staff is equipped with the necessary skills to operate efficiently and adopt new technologies, further supporting lead time reductions.
Enhancing Communication Across Departments
Improving communication across various departments within an organization is crucial for shortening lead times.
Breaking down information silos ensures that all parts of the organization are aligned and working toward common goals.
Cross-departmental teams and regular meetings to discuss production schedules, demand forecasting, and inventory levels can facilitate better coordination and reduce miscommunications.
Adopting integrated software solutions that provide real-time data access for all relevant stakeholders can also enhance communication and decision-making processes.
Evaluating and Adjusting Production Capacity
Finally, regularly evaluating production capacity and making necessary adjustments can significantly reduce lead times.
Understanding the capacity limits and potential bottlenecks within the production process allows companies to make informed decisions about scaling operations or modifying production schedules.
Flexibility in adjusting production capacity in response to demand fluctuations can drastically improve lead times and maintain consistent service levels.
Investing in flexible manufacturing systems that can easily accommodate changes in product types and volumes without major downtimes is also beneficial.
By adopting these production planning techniques, purchasing departments can effectively work towards shortening lead times.
This results in faster order fulfillment, increased customer satisfaction, and ultimately, a stronger competitive position in the market.
資料ダウンロード
QCD調達購買管理クラウド「newji」は、調達購買部門で必要なQCD管理全てを備えた、現場特化型兼クラウド型の今世紀最高の購買管理システムとなります。
ユーザー登録
調達購買業務の効率化だけでなく、システムを導入することで、コスト削減や製品・資材のステータス可視化のほか、属人化していた購買情報の共有化による内部不正防止や統制にも役立ちます。
NEWJI DX
製造業に特化したデジタルトランスフォーメーション(DX)の実現を目指す請負開発型のコンサルティングサービスです。AI、iPaaS、および先端の技術を駆使して、製造プロセスの効率化、業務効率化、チームワーク強化、コスト削減、品質向上を実現します。このサービスは、製造業の課題を深く理解し、それに対する最適なデジタルソリューションを提供することで、企業が持続的な成長とイノベーションを達成できるようサポートします。
オンライン講座
製造業、主に購買・調達部門にお勤めの方々に向けた情報を配信しております。
新任の方やベテランの方、管理職を対象とした幅広いコンテンツをご用意しております。
お問い合わせ
コストダウンが利益に直結する術だと理解していても、なかなか前に進めることができない状況。そんな時は、newjiのコストダウン自動化機能で大きく利益貢献しよう!
(Β版非公開)