- お役立ち記事
- Production schedule adjustment integrated with suppliers Practical example of purchasing department
月間76,176名の
製造業ご担当者様が閲覧しています*
*2025年3月31日現在のGoogle Analyticsのデータより
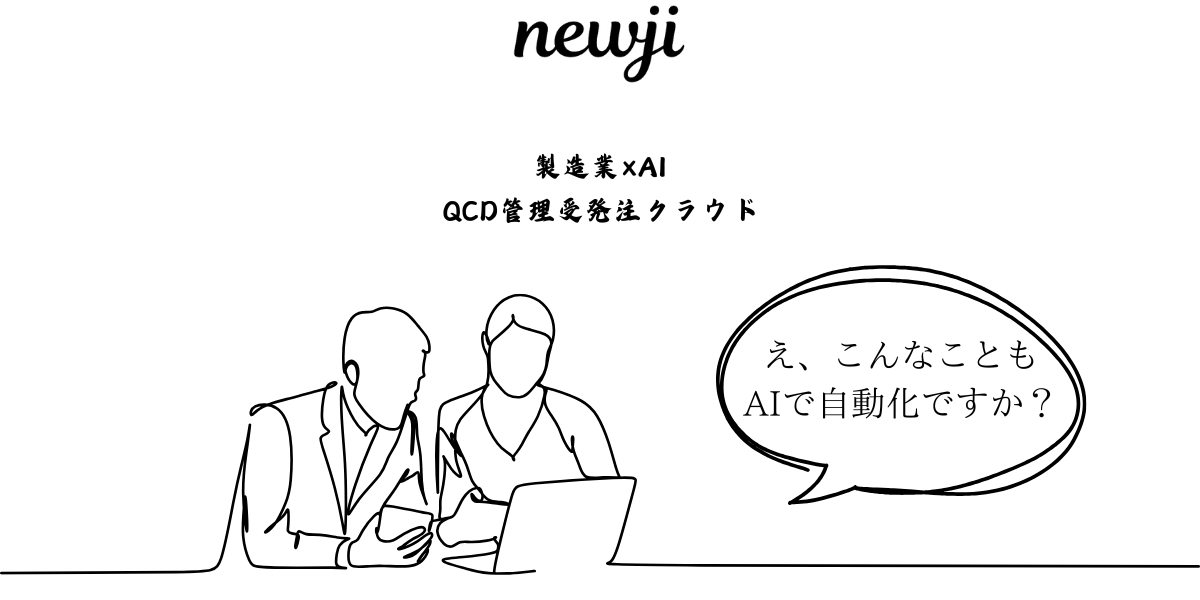
Production schedule adjustment integrated with suppliers Practical example of purchasing department
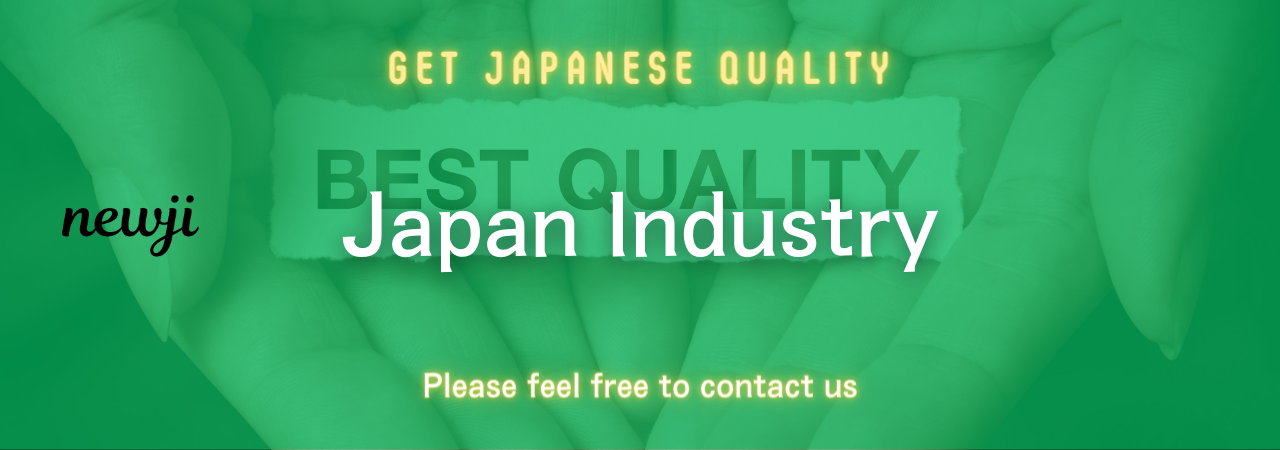
目次
Understanding Production Schedule Adjustment
Production schedule adjustment is a critical process within any manufacturing or production setting.
It involves the planning and re-aligning of production activities to ensure that products are manufactured efficiently, cost-effectively, and on time.
For purchasing departments, linking production schedules with suppliers is crucial.
This ensures that materials and components arrive when needed, keeping the production line running smoothly.
The Role of the Purchasing Department
The purchasing department plays a pivotal role in managing production schedules.
Their responsibilities include sourcing materials, negotiating with suppliers, and ensuring timely deliveries.
By integrating with suppliers, purchasing managers can anticipate supply chain disruptions and adjust schedules accordingly.
This collaboration is essential to maintain inventory levels that align with production needs without overstocking or understocking.
Key Benefits of Integrating with Suppliers
When a purchasing department works closely with suppliers to adjust production schedules, several benefits emerge.
Improved Efficiency
By having a clear understanding of supplier capabilities and lead times, the purchasing team can optimize production schedules.
This reduces downtime caused by waiting for materials, thus enhancing overall operational efficiency.
Cost Savings
Effective schedule adjustments can lead to cost savings in multiple ways.
Ordering materials in alignment with production needs can prevent excess inventory, which ties up capital.
Moreover, minimizing rush orders reduces additional transportation fees and potential premium prices for last-minute procurement.
Better Supplier Relationships
Regular communication and collaboration with suppliers foster stronger relationships.
Suppliers appreciate transparency and predictability, which leads to improved service and potential priority treatment, such as faster deliveries.
Risk Mitigation
Integrated systems allow for better risk assessment and mitigation.
Should a disruption occur, such as a delay in raw material availability, both the purchasing department and suppliers can collaborate on alternative solutions quickly.
Steps for Effective Production Schedule Adjustment
For a purchasing department to efficiently adjust production schedules, several steps should be followed.
Assess Current Production Needs
Begin by thoroughly understanding the production needs.
This involves reviewing sales forecasts, understanding existing inventory levels, and identifying any upcoming production spikes.
It’s crucial to ascertain how these factors impact material requirements.
Collaborate with Suppliers
Open lines of communication with suppliers are imperative.
Discuss potential changes in production schedules and understand the supplier’s lead times and constraints.
It’s beneficial to involve suppliers in the planning process to achieve mutual benefits.
Utilize Technological Tools
Employ software solutions that provide real-time insights into inventory levels, supplier lead times, and production schedules.
These technologies help in predicting future needs and adjusting orders accordingly.
Advanced analytics can also forecast potential disruptions, giving purchasing teams more time to react.
Implement a Flexible Strategy
Flexibility is key to maintaining an adaptive production schedule.
Have contingency plans in place for scenarios such as supplier delays or sudden changes in demand.
A flexible approach ensures that the production line can quickly respond to unexpected changes without significant setbacks.
Case Study: Purchasing Department Success
Consider the example of XYZ Manufacturing, a mid-sized electronics manufacturer.
XYZ faced challenges with frequent production halts due to delayed deliveries.
The purchasing department decided to integrate its production schedules more closely with its top five suppliers.
They began by initiating weekly meetings with suppliers to discuss potential disruptions and required delivery adjustments.
Utilizing advanced planning software, they shared forecasts and production adjustments directly with suppliers, aiding in transparency and preparedness.
The results were significant.
Production efficiency improved by 20%, and inventory costs reduced by nearly 15%, as materials were ordered just in time for production runs.
Relationships strengthened with suppliers, leading to more favorable terms and the ability to negotiate better prices.
Challenges in Schedule Adjustment
While there are clear benefits, purchasing departments also face challenges when adjusting production schedules with suppliers.
Communication Barriers
Miscommunications can lead to misunderstandings regarding orders and deliveries.
It is crucial to establish clear communication protocols and utilize shared platforms for exchanging information.
Supplier Limitations
Suppliers may have constraints that limit their flexibility.
It’s important to understand these boundaries and work collaboratively to find solutions that work for both parties.
Data Integration
Integrating data from various sources into a coherent system can be challenging.
Companies must invest in technology that allows seamless information exchange and real-time updates.
Conclusion
Integrating production schedule adjustments with suppliers is not merely beneficial but essential for the success of the purchasing department.
By focusing on collaboration, utilizing technology, and embracing flexibility, businesses can achieve greater efficiency, cost savings, and stronger supplier relationships.
The path, though fraught with challenges, offers substantial rewards for those who master it.
Purchasing departments that can seamlessly adjust their production schedules set themselves apart in today’s competitive market landscape.
資料ダウンロード
QCD管理受発注クラウド「newji」は、受発注部門で必要なQCD管理全てを備えた、現場特化型兼クラウド型の今世紀最高の受発注管理システムとなります。
ユーザー登録
受発注業務の効率化だけでなく、システムを導入することで、コスト削減や製品・資材のステータス可視化のほか、属人化していた受発注情報の共有化による内部不正防止や統制にも役立ちます。
NEWJI DX
製造業に特化したデジタルトランスフォーメーション(DX)の実現を目指す請負開発型のコンサルティングサービスです。AI、iPaaS、および先端の技術を駆使して、製造プロセスの効率化、業務効率化、チームワーク強化、コスト削減、品質向上を実現します。このサービスは、製造業の課題を深く理解し、それに対する最適なデジタルソリューションを提供することで、企業が持続的な成長とイノベーションを達成できるようサポートします。
製造業ニュース解説
製造業、主に購買・調達部門にお勤めの方々に向けた情報を配信しております。
新任の方やベテランの方、管理職を対象とした幅広いコンテンツをご用意しております。
お問い合わせ
コストダウンが利益に直結する術だと理解していても、なかなか前に進めることができない状況。そんな時は、newjiのコストダウン自動化機能で大きく利益貢献しよう!
(β版非公開)