- お役立ち記事
- Professional Techniques for Maintaining Quality in Rare Earth Magnet Processing
月間76,176名の
製造業ご担当者様が閲覧しています*
*2025年3月31日現在のGoogle Analyticsのデータより
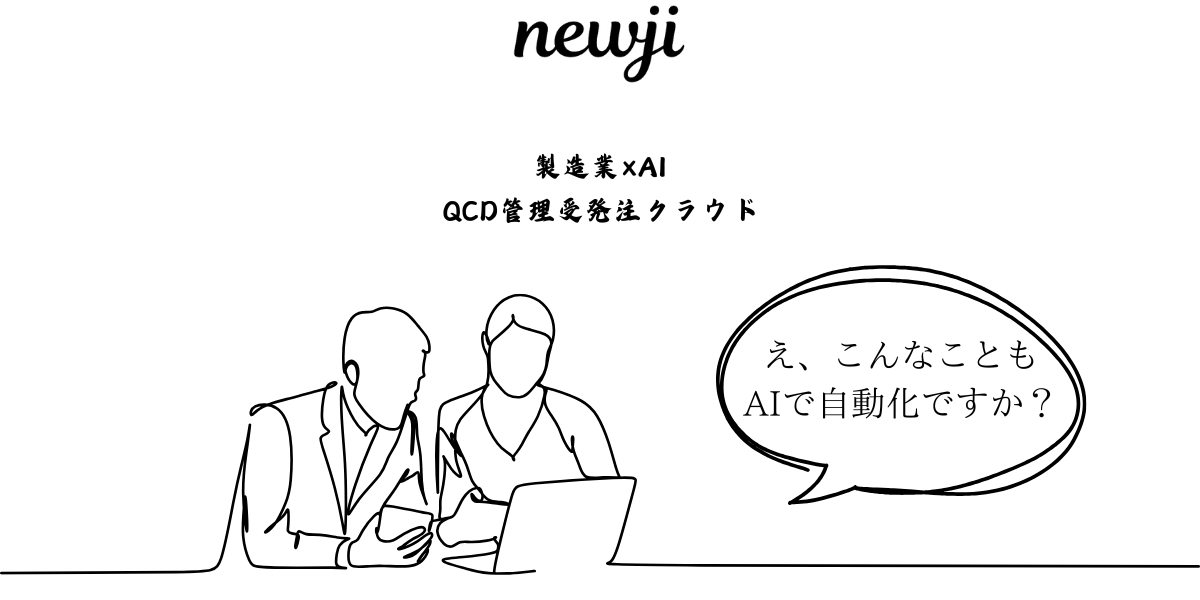
Professional Techniques for Maintaining Quality in Rare Earth Magnet Processing
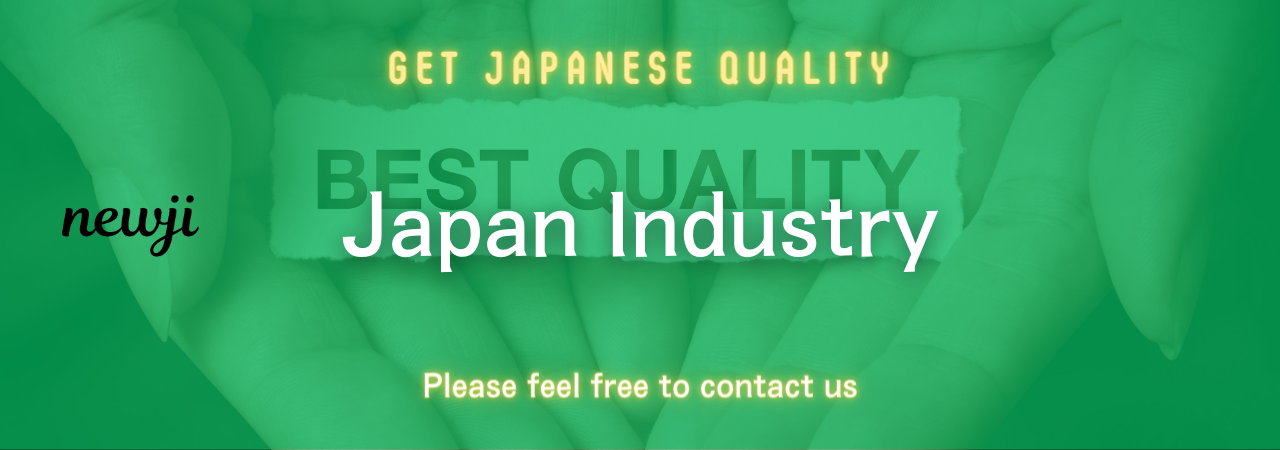
Rare earth magnets are incredibly powerful and have numerous industrial applications.
Ensuring quality during their processing can significantly impact their performance and longevity.
In this article, we will explore professional techniques for maintaining quality in rare earth magnet processing.
目次
Understanding Rare Earth Magnets
Rare earth magnets are made from rare earth elements, primarily neodymium, and samarium.
These elements are part of the lanthanide series in the periodic table.
Rare earth magnets are known for their strong magnetic fields and are used in various applications, such as electric vehicles, wind turbines, and consumer electronics.
Types of Rare Earth Magnets
There are two main types of rare earth magnets:
1. Neodymium-iron-boron (NdFeB) magnets: These are the strongest and most widely used type of rare earth magnets. They are highly susceptible to corrosion and must be coated with protective materials such as nickel, zinc, or epoxy.
2. Samarium-cobalt (SmCo) magnets: These are more resistant to corrosion and can withstand higher temperatures than NdFeB magnets. However, they are more brittle and expensive.
Common Challenges in Rare Earth Magnet Processing
Ensuring high-quality rare earth magnets involves navigating various challenges during their processing:
Material Quality and Purity
The quality of the raw materials directly affects the properties of the final magnets.
Impurities can weaken the magnets’ strength and durability.
Thus, sourcing high-purity rare earth materials is crucial.
Precision in Manufacturing
Rare earth magnets require precise manufacturing techniques to achieve the desired shape and size.
Inaccuracies in cutting, grinding, or sintering can lead to performance issues and higher rejection rates.
Using advanced machinery and quality control measures can mitigate these risks.
Temperature Sensitivity
Rare earth magnets can be sensitive to high temperatures.
NdFeB magnets, in particular, can lose their magnetic properties if exposed to temperatures above 80°C (176°F).
Implementing proper cooling and temperature control during processing is essential to maintain the magnets’ integrity.
Corrosion Resistance
NdFeB magnets are prone to oxidation and corrosion.
Applying protective coatings or incorporating corrosion-resistant materials into the manufacturing process is necessary to enhance their longevity.
Professional Techniques for Maintaining Quality
Let’s delve into some of the professional techniques that can help maintain quality in rare earth magnet processing.
Sourcing High-Quality Raw Materials
One of the first steps in ensuring quality is sourcing high-purity rare earth elements.
Working with reputable suppliers and conducting thorough quality checks on raw materials can prevent impurities from compromising the magnets’ properties.
Implementing Advanced Manufacturing Processes
Using advanced manufacturing techniques can significantly improve the precision and consistency of rare earth magnets.
Computer numerical control (CNC) machining, laser cutting, and waterjet cutting are some of the processes that offer high accuracy and minimal waste.
Adopting Stringent Quality Control Measures
Quality control is integral to maintaining the high standards of rare earth magnets.
This involves regular inspections, material testing, and process monitoring.
Non-destructive testing methods, such as X-ray and ultrasonic testing, can detect defects without damaging the magnets.
Applying Protective Coatings
To combat corrosion, protective coatings are applied to NdFeB magnets.
Common coatings include nickel, zinc, and epoxy.
These coatings provide a barrier against moisture and other corrosive elements.
It’s essential to select the appropriate coating based on the application and environmental conditions.
Utilizing Proper Sintering Techniques
Sintering is a critical step in the manufacturing process of rare earth magnets.
It involves compacting and heating the powdered materials to form a solid structure.
Proper sintering techniques ensure uniformity and reduce the formation of micro-cracks, enhancing the magnets’ strength and durability.
Controlling Temperature During Processing
Maintaining optimal temperature conditions during processing is vital for preserving the magnets’ properties.
For instance, using advanced cooling systems during machining and sintering can prevent overheating and thermal damage.
Additionally, selecting binding materials that can withstand high temperatures can improve the magnets’ performance in harsh environments.
Environmental and Safety Considerations
Ensuring quality during rare earth magnet processing also involves adherence to environmental and safety standards.
Minimizing Waste and Recycling
Efficient use of materials and recycling can contribute to sustainable manufacturing practices.
By minimizing waste during production and recycling scrap materials, manufacturers can reduce their environmental footprint and lower costs.
Implementing Safe Handling Practices
Rare earth elements can pose health and safety risks to workers.
Proper handling and storage practices, along with the use of personal protective equipment (PPE), are essential to ensure a safe working environment.
Regular training and awareness programs can further enhance safety standards.
Addressing Environmental Regulations
Manufacturers must comply with environmental regulations governing the use and disposal of rare earth elements.
Adhering to these regulations helps minimize environmental impact and fosters sustainable production practices.
Conclusion
Maintaining quality in rare earth magnet processing involves a combination of sourcing high-purity materials, implementing advanced manufacturing techniques, and adhering to stringent quality control measures.
By addressing challenges such as temperature sensitivity, corrosion resistance, and precision in manufacturing, professionals can ensure the production of high-performance rare earth magnets.
Additionally, considering environmental and safety aspects during processing contributes to sustainable and responsible manufacturing practices.
With these professional techniques, manufacturers can continue to meet the growing demand for rare earth magnets while maintaining the highest standards of quality.
資料ダウンロード
QCD管理受発注クラウド「newji」は、受発注部門で必要なQCD管理全てを備えた、現場特化型兼クラウド型の今世紀最高の受発注管理システムとなります。
ユーザー登録
受発注業務の効率化だけでなく、システムを導入することで、コスト削減や製品・資材のステータス可視化のほか、属人化していた受発注情報の共有化による内部不正防止や統制にも役立ちます。
NEWJI DX
製造業に特化したデジタルトランスフォーメーション(DX)の実現を目指す請負開発型のコンサルティングサービスです。AI、iPaaS、および先端の技術を駆使して、製造プロセスの効率化、業務効率化、チームワーク強化、コスト削減、品質向上を実現します。このサービスは、製造業の課題を深く理解し、それに対する最適なデジタルソリューションを提供することで、企業が持続的な成長とイノベーションを達成できるようサポートします。
製造業ニュース解説
製造業、主に購買・調達部門にお勤めの方々に向けた情報を配信しております。
新任の方やベテランの方、管理職を対象とした幅広いコンテンツをご用意しております。
お問い合わせ
コストダウンが利益に直結する術だと理解していても、なかなか前に進めることができない状況。そんな時は、newjiのコストダウン自動化機能で大きく利益貢献しよう!
(β版非公開)