- お役立ち記事
- Profit Analysis Through Separation of Manufacturing Costs and Selling, General and Administrative Expenses
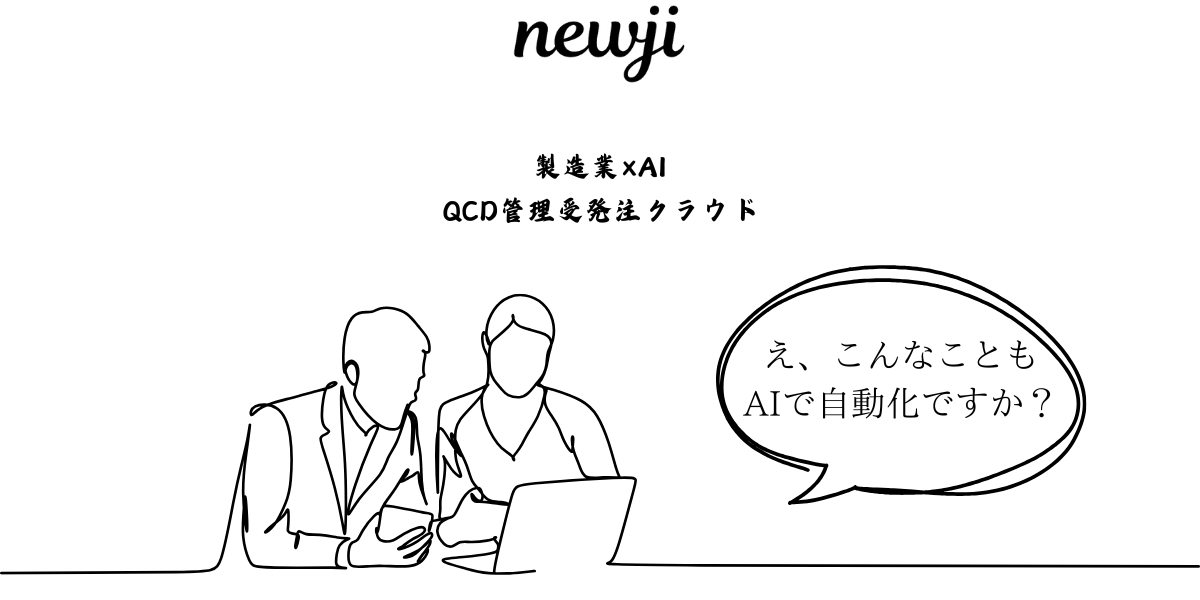
Profit Analysis Through Separation of Manufacturing Costs and Selling, General and Administrative Expenses
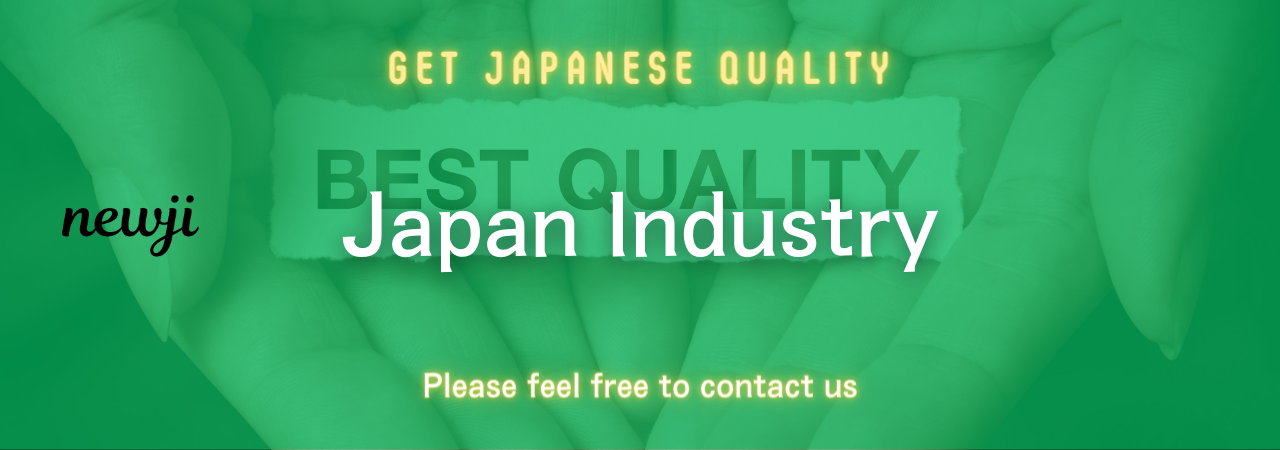
Effective financial management is crucial for any business aiming to thrive in today’s competitive market.
A key aspect of this management is the separation of manufacturing costs and selling, general, and administrative (SG&A) expenses.
Understanding these expenses can provide insightful data for profit analysis, leading to better business decisions.
Manufacturing costs are those related directly to creating a product.
In contrast, SG&A expenses are the costs incurred from all other aspects of running a business that are not tied directly to production.
A clear distinction between these two can illuminate areas where efficiency can be improved and more focused strategies developed.
目次
What are Manufacturing Costs?
Manufacturing costs encompass all expenses associated with producing a product.
They are typically broken down into three categories: direct materials, direct labor, and manufacturing overhead.
Direct Materials
Direct materials are the raw materials that are converted into the final product.
These can include anything from steel used in car manufacturing to flour used in baking bread.
Tracking the exact cost of these materials is essential in determining the overall cost of production.
Direct Labor
Direct labor costs include wages and benefits for the employees directly involved in manufacturing the product.
These expenses focus on the time and effort put in by workers to turn raw materials into finished goods.
Manufacturing Overhead
Manufacturing overhead includes all other costs that are necessary to run the manufacturing process that aren’t directly tied to labor or materials.
This can include costs such as utility bills, maintenance of equipment, and factory rent.
These costs are often allocated to products based on a predetermined overhead rate, ensuring they are appropriately accounted for in product pricing.
Understanding SG&A Expenses
SG&A expenses, unlike manufacturing costs, are associated with the day-to-day operations of a business outside of producing goods.
These expenses are crucial for supporting the business and driving sales.
Selling Expenses
Selling expenses are costs directly related to the sale of products.
This includes advertising, sales commissions, and distribution costs.
Effective management of selling expenses is key to maintaining profitability, as excessive spending in this area can erode margins.
General Expenses
General expenses cover the administrative functions of a business.
They include costs such as office supplies, accounting, and human resources.
These expenses are necessary to ensure the smooth operation of a business and support its overall functions.
Administrative Expenses
Administrative expenses are those associated with the general management of the company.
This includes executive salaries, legal fees, and other costs related to overall administration.
Keeping these expenses in check can prevent unnecessary overhead and improve the company’s financial health.
Importance of Separating Manufacturing Costs and SG&A Expenses
Properly separating manufacturing costs and SG&A expenses allows businesses to gain clearer insights into their financial operations.
This separation makes it easier to identify cost-saving opportunities and streamline operations.
Accurate Profit Margins
By isolating manufacturing costs from SG&A expenses, companies can generate accurate product costing, which is essential for determining true profit margins.
This enables better pricing strategies and ensures products are not under or over-priced.
Budgeting and Financial Planning
Separating these costs assists in more accurate budgeting and financial planning.
It aids in forecasting future expenses and setting realistic financial targets.
Businesses can allocate resources more effectively and avoid over-spending in non-essential areas.
Performance Analysis
Clear differentiation between manufacturing and SG&A expenses facilitates a deeper performance analysis.
It becomes easier to pinpoint which areas are driving costs and where efficiencies can be improved.
Regularly reviewing these expenses can highlight trends and inform strategic decisions.
Steps for Accurate Separation of Costs
Accurate separation of manufacturing costs and SG&A expenses requires a systematic approach.
Here are essential steps to ensure precision:
Detailed Data Collection
Collect comprehensive data on all costs.
This involves meticulously tracking every expense associated with manufacturing as well as SG&A.
Use accounting software to help segregate costs in real-time.
Cost Allocation Methods
Implement standardized cost allocation methods.
For manufacturing overhead, use techniques such as job costing or process costing to distribute costs accurately across various products.
Ensure SG&A expenses are allocated based on their direct impact on sales and operations.
Regular Reviews and Adjustments
Continuously review and adjust cost allocation methods.
Business dynamics can change, requiring periodic updates to how costs are allocated.
Regular audits help maintain accuracy and adapt to shifting business needs.
Using Separated Costs to Improve Profitability
Once manufacturing costs and SG&A expenses are accurately separated, use the insights gained to enhance profitability.
Cost Control
Analyze the detailed cost reports to identify areas where spending can be reduced without impacting quality or performance.
Implement cost-control measures that target inefficiencies and waste.
Strategic Decision Making
Use the information from separated costs to make strategic decisions.
This can involve pricing adjustments, process improvements, or reallocating resources to higher-value areas.
Optimize operations by focusing on profitable products and services.
Improving Operational Efficiency
Use the insights to identify bottlenecks and inefficiencies in the manufacturing process.
Streamline operations to reduce production costs and enhance overall efficiency.
Review SG&A expenses to ensure they are justified and contributing to the business goals.
Understanding and effectively managing both manufacturing costs and SG&A expenses provide a solid foundation for profit analysis.
Through strategic allocation, regular review, and data-driven decisions, businesses can uncover opportunities for improvement and enhance profitability.
By implementing these practices, companies can achieve a competitive edge and sustainable growth.
資料ダウンロード
QCD調達購買管理クラウド「newji」は、調達購買部門で必要なQCD管理全てを備えた、現場特化型兼クラウド型の今世紀最高の購買管理システムとなります。
ユーザー登録
調達購買業務の効率化だけでなく、システムを導入することで、コスト削減や製品・資材のステータス可視化のほか、属人化していた購買情報の共有化による内部不正防止や統制にも役立ちます。
NEWJI DX
製造業に特化したデジタルトランスフォーメーション(DX)の実現を目指す請負開発型のコンサルティングサービスです。AI、iPaaS、および先端の技術を駆使して、製造プロセスの効率化、業務効率化、チームワーク強化、コスト削減、品質向上を実現します。このサービスは、製造業の課題を深く理解し、それに対する最適なデジタルソリューションを提供することで、企業が持続的な成長とイノベーションを達成できるようサポートします。
オンライン講座
製造業、主に購買・調達部門にお勤めの方々に向けた情報を配信しております。
新任の方やベテランの方、管理職を対象とした幅広いコンテンツをご用意しております。
お問い合わせ
コストダウンが利益に直結する術だと理解していても、なかなか前に進めることができない状況。そんな時は、newjiのコストダウン自動化機能で大きく利益貢献しよう!
(Β版非公開)