- お役立ち記事
- Promotion method for process improvement/production line standardization and productivity improvement for automation
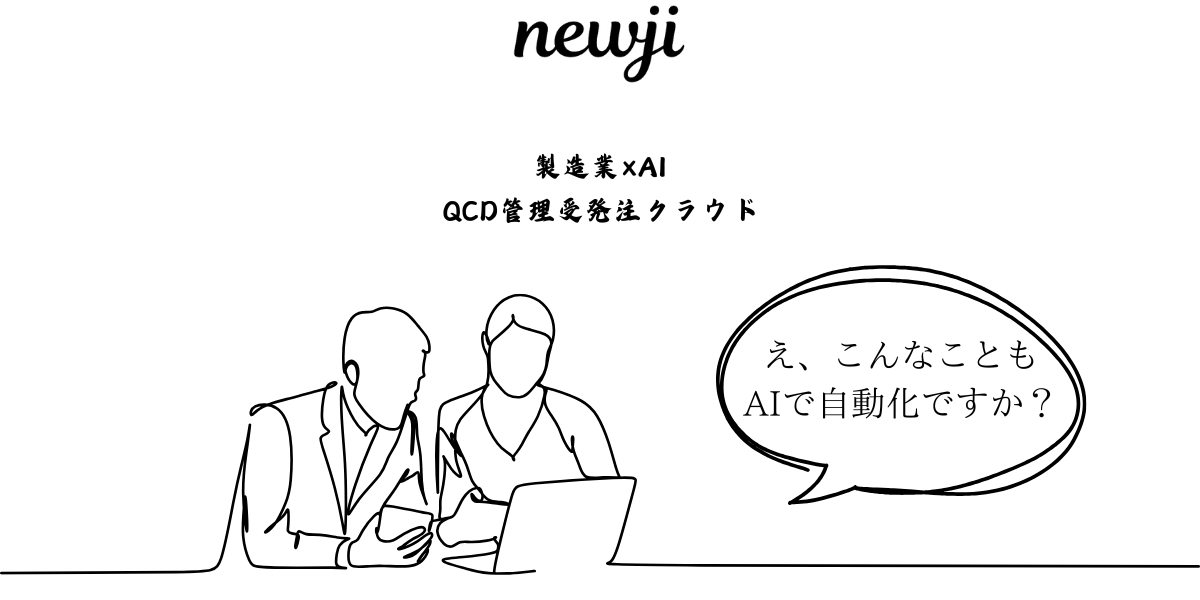
Promotion method for process improvement/production line standardization and productivity improvement for automation
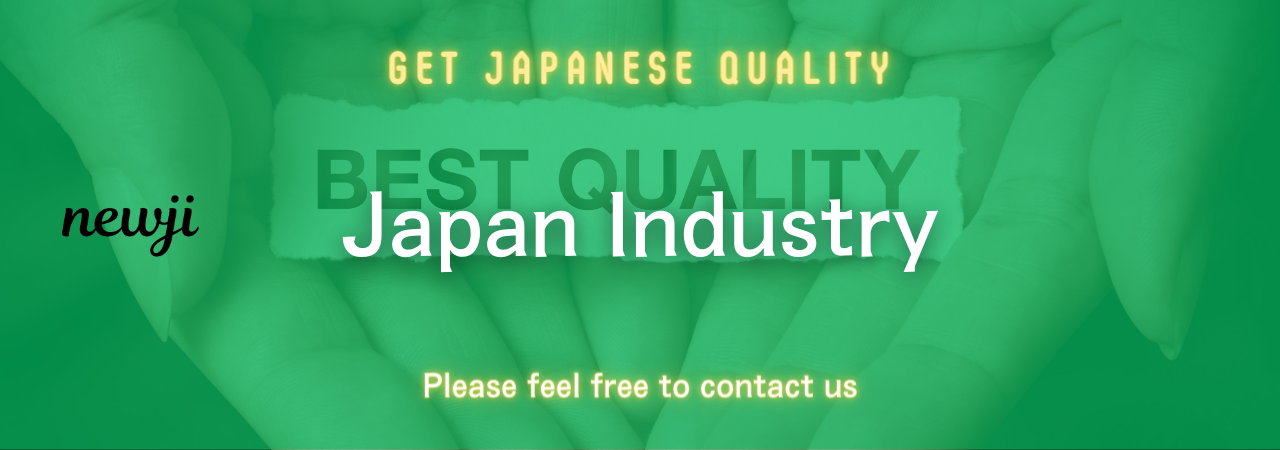
目次
Introduction to Process Improvement and Production Line Standardization
In today’s fast-paced industrial world, efficiency and productivity are at the forefront of every business strategy.
To remain competitive, companies must consistently seek ways to improve their processes and standardize production lines.
This focus not only enhances productivity but also lays the foundation for further automated solutions.
Standardizing production processes is essential for minimizing waste, reducing variability, and improving quality.
By ensuring that each step in the production line operates in harmony, businesses can more easily introduce automation and improve the overall output.
Understanding the Basics of Process Improvement
Process improvement is a continuous and systematic approach to refining and enhancing business operations.
The goal is to optimize workflows to yield better results.
It usually involves analyzing current processes, identifying areas where inefficiencies or bottlenecks occur, and implementing changes to improve them.
Lean manufacturing, Six Sigma, and Total Quality Management (TQM) are popular methodologies used to drive process improvement.
Lean Manufacturing
Lean manufacturing focuses on reducing waste and improving flow in production processes.
It emphasizes value from the customer’s perspective and strives to eliminate anything that does not add to that value.
By cutting down on waste, lean principles help in streamlining the operations, leading to increased productivity.
Six Sigma
Six Sigma is a data-driven methodology aimed at reducing defects and variability in processes.
It focuses on achieving near-perfect quality by applying statistical methods.
The primary objective of Six Sigma is to streamline production and minimize cost, while maintaining the highest quality standards.
Total Quality Management (TQM)
TQM is an organization-wide approach to embedding quality into every aspect of the operation.
It emphasizes customer satisfaction, employee involvement, and continuous improvement as the core elements for achieving overall quality in processes.
Implementing TQM leads to increased market share, reduced costs, and improved production efficiency.
Standardizing Production Lines
Standardization is the process of establishing uniform procedures and specifications across the production line.
This ensures consistency in the products or services provided, enhancing overall efficiency.
A standardized production line is easier to manage, monitor, and control.
Benefits of Standardization
1. **Consistency**: Ensures uniform quality and output, reducing errors and variations.
2. **Predictability**: Simplifies planning and forecasting, making it easier to meet customer demands.
3. **Scalability**: Facilitates scaling production up or down with ease, adapting to market changes.
4. **Efficiency**: Identifies best practices and implements them across all operations, leading to optimal use of resources.
Steps to Achieving Standardization
1. **Documenting Processes**: Write detailed documents outlining each step in the production process.
2. **Training Employees**: Ensure that all staff are trained in standardized procedures.
3. **Regular Monitoring**: Continuously monitor the system to ensure adherence to standards.
4. **Update and Refine**: Regularly review and update standards based on feedback and innovations.
The Role of Automation in Productivity Improvement
Automation involves using technology to automate tasks that were once performed manually, resulting in faster and more reliable production.
Automating processes in a standardized production line greatly enhances productivity, reduces labor costs, and decreases the risk of human error.
Advantages of Automation
1. **Increased Output**: Automation allows for faster completion of repetitive tasks, increasing overall production speed.
2. **Improved Quality**: Machines and systems are more precise, leading to fewer defects in products.
3. **Cost Reduction**: By minimizing manual labor and reducing errors, automation cuts down on waste and operational costs.
4. **Safety**: Automating hazardous tasks protects workers from potential harm.
Key Considerations for Implementing Automation
1. **Evaluate Processes**: Identify which processes can benefit most from automation.
2. **Technology Selection**: Choose the right technology or machinery that aligns with your production needs.
3. **Integration**: Ensure seamless integration with existing systems, maintaining process flow.
4. **Training**: Train employees to work alongside automated systems, ensuring smooth transitions.
5. **Maintenance**: Establish a routine maintenance schedule to avoid downtime and keep automated systems running efficiently.
Conclusion
Process improvement and production line standardization are crucial steps for any company aiming to boost productivity and remain competitive.
By adopting these methodologies, businesses can significantly cut down on waste, reduce costs, and improve quality.
Incorporating automation further enhances these benefits by accelerating production speeds and ensuring consistency.
As technologies continue to evolve, the interplay between process improvement, standardization, and automation will become even more integral to business success.
By committing to these strategies, companies are better positioned to meet their goals, delight their customers, and secure a prosperous future.
資料ダウンロード
QCD調達購買管理クラウド「newji」は、調達購買部門で必要なQCD管理全てを備えた、現場特化型兼クラウド型の今世紀最高の購買管理システムとなります。
ユーザー登録
調達購買業務の効率化だけでなく、システムを導入することで、コスト削減や製品・資材のステータス可視化のほか、属人化していた購買情報の共有化による内部不正防止や統制にも役立ちます。
NEWJI DX
製造業に特化したデジタルトランスフォーメーション(DX)の実現を目指す請負開発型のコンサルティングサービスです。AI、iPaaS、および先端の技術を駆使して、製造プロセスの効率化、業務効率化、チームワーク強化、コスト削減、品質向上を実現します。このサービスは、製造業の課題を深く理解し、それに対する最適なデジタルソリューションを提供することで、企業が持続的な成長とイノベーションを達成できるようサポートします。
オンライン講座
製造業、主に購買・調達部門にお勤めの方々に向けた情報を配信しております。
新任の方やベテランの方、管理職を対象とした幅広いコンテンツをご用意しております。
お問い合わせ
コストダウンが利益に直結する術だと理解していても、なかなか前に進めることができない状況。そんな時は、newjiのコストダウン自動化機能で大きく利益貢献しよう!
(Β版非公開)