- お役立ち記事
- Proper tolerance calculation and quality prediction
月間76,176名の
製造業ご担当者様が閲覧しています*
*2025年3月31日現在のGoogle Analyticsのデータより
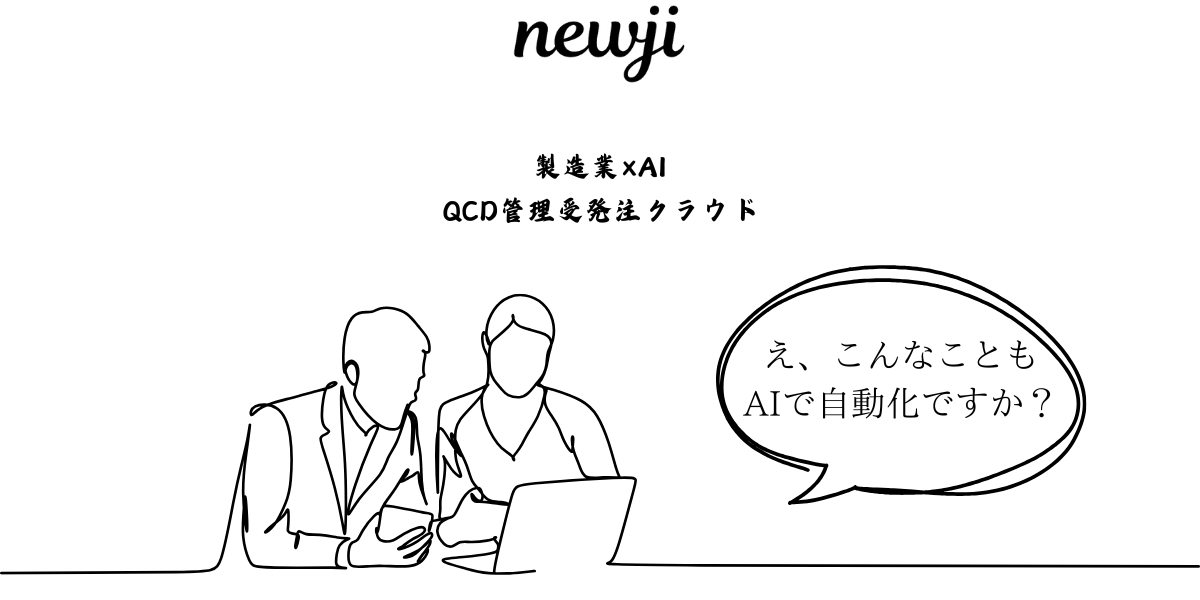
Proper tolerance calculation and quality prediction
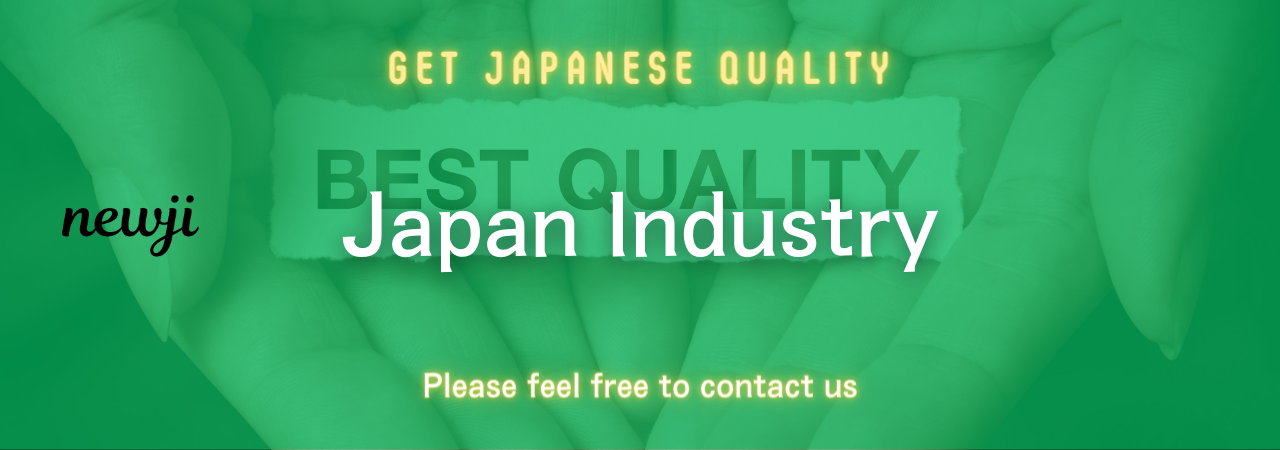
目次
Understanding Tolerance in Manufacturing
Tolerance plays a crucial role in the manufacturing industry as it defines the allowable limits of variation in a physical dimension.
In simple terms, it helps determine the extent to which a particular component or product can deviate from its ideal shape or size while still fitting or functioning properly in its intended assembly or application.
The Importance of Tolerance
The primary purpose of setting tolerance in manufacturing is to ensure quality and functionality.
Parts that do not meet tolerance specifications can lead to poor performance, functional failure, or other issues in the completed product.
For example, if a car engine part is not within its specified tolerance, it could lead to engine failure and potentially dangerous situations for drivers.
In addition, proper tolerance ensures that parts are interchangeable.
This interchangeability allows for easier maintenance and repair, as replacement parts can fit properly without the need for custom modifications.
Thus, maintaining proper tolerance in manufacturing processes is essential for product reliability and customer satisfaction.
Calculating Tolerance
Calculating tolerance involves determining the upper and lower limits for the acceptable size or shape of a component.
This calculation may vary depending on the materials used, the function of the component, and its relationship with other components in a system.
Types of Tolerances
There are several types of tolerances that manufacturers might take into consideration:
1. **Dimensional Tolerances**: These refer to the permissible limits concerning a physical dimension, such as length, width, height, diameter, or thickness.
2. **Geometric Tolerances**: This further breaks down into attributes like flatness, straightness, roundness, and more.
Geometric tolerances describe the allowable variation in geometry and can be more complex to calculate than dimensional tolerances.
3. **Surface Finish Tolerances**: This pertains to the texture of the surface of a component.
A certain level of smoothness or roughness may be necessary for a part to function correctly or to meet aesthetic requirements.
Using Tolerance Calculators
Tolerance calculators are tools that help manufacturers and engineers quickly determine the acceptable range for component dimensions.
By inputting basic information such as the nominal size and desired precision, these calculators can provide the appropriate tolerance levels based on industry standards.
Such tools improve efficiency and ensure that calculations are both accurate and consistent across different manufacturing scenarios.
Predicting Quality with Tolerance Data
Accurate prediction of product quality and performance is essential for maintaining high standards in manufacturing.
Tolerance data serves as a valuable source of information for predicting potential quality issues in production.
Analyzing Variability
Manufacturers can leverage tolerance data to analyze variability and identify patterns that might indicate a drift in production quality.
By using statistical tools and techniques, manufacturers can measure the variation in components and assess whether it stays within acceptable limits.
Identifying and addressing these patterns before they result in defective products can save company resources and help maintain a reputation for quality.
Quality Control Processes
Tolerance assessments are integral to implementing effective quality control processes.
Manufacturers can develop predictive models using historical tolerance data to forecast the likelihood of defects or failures in the production process.
These models can guide decision-making, enabling quick adjustments to maintain product quality.
Quality control teams may conduct regular assessments of tolerance data to ensure that production stays within established limits.
Regular monitoring allows for timely interventions and the implementation of corrective actions when necessary.
Improving Process Capabilities
The data collected from tolerance calculations and quality predictions is invaluable for continuous improvement efforts within a manufacturing process.
By analyzing this data, manufacturers can identify areas requiring process enhancement or optimization.
Lean Manufacturing Approaches
Incorporating lean manufacturing principles can help manufacturers reduce waste, streamline production, and ensure precise adherence to tolerance requirements.
Through continuous evaluations and adjustments, manufacturers can improve process capability and minimize the risk of defects.
Additionally, implementing lean strategies can promote a culture of quality consciousness and collaboration among teams, ultimately contributing to higher product standards.
Six Sigma Methodologies
Six Sigma methodologies are another approach that can help enhance process capabilities.
This data-driven management method can improve the output of a process by identifying and removing causes of defects and minimizing variability.
Using Six Sigma tools alongside tolerance data allows manufacturers to make well-informed choices that lead to quality improvements and cost reductions.
Conclusion
Proper tolerance calculation and quality prediction are essential for ensuring the production of reliable, functional, and high-quality products in the manufacturing industry.
By understanding tolerance types, using calculators strategically, conducting thorough analyses, and applying continuous improvement methods like lean manufacturing and Six Sigma, manufacturers can efficiently maintain product quality and boost customer satisfaction.
Through proactive management of tolerance limits and quality assurance processes, companies can cultivate a reputation for excellence and maintain a competitive edge in their respective markets.
資料ダウンロード
QCD管理受発注クラウド「newji」は、受発注部門で必要なQCD管理全てを備えた、現場特化型兼クラウド型の今世紀最高の受発注管理システムとなります。
ユーザー登録
受発注業務の効率化だけでなく、システムを導入することで、コスト削減や製品・資材のステータス可視化のほか、属人化していた受発注情報の共有化による内部不正防止や統制にも役立ちます。
NEWJI DX
製造業に特化したデジタルトランスフォーメーション(DX)の実現を目指す請負開発型のコンサルティングサービスです。AI、iPaaS、および先端の技術を駆使して、製造プロセスの効率化、業務効率化、チームワーク強化、コスト削減、品質向上を実現します。このサービスは、製造業の課題を深く理解し、それに対する最適なデジタルソリューションを提供することで、企業が持続的な成長とイノベーションを達成できるようサポートします。
製造業ニュース解説
製造業、主に購買・調達部門にお勤めの方々に向けた情報を配信しております。
新任の方やベテランの方、管理職を対象とした幅広いコンテンツをご用意しております。
お問い合わせ
コストダウンが利益に直結する術だと理解していても、なかなか前に進めることができない状況。そんな時は、newjiのコストダウン自動化機能で大きく利益貢献しよう!
(β版非公開)