- お役立ち記事
- Proposal for improving productivity and efficiency through automation and mechanization of folding small boxes for dried noodles
月間76,176名の
製造業ご担当者様が閲覧しています*
*2025年3月31日現在のGoogle Analyticsのデータより
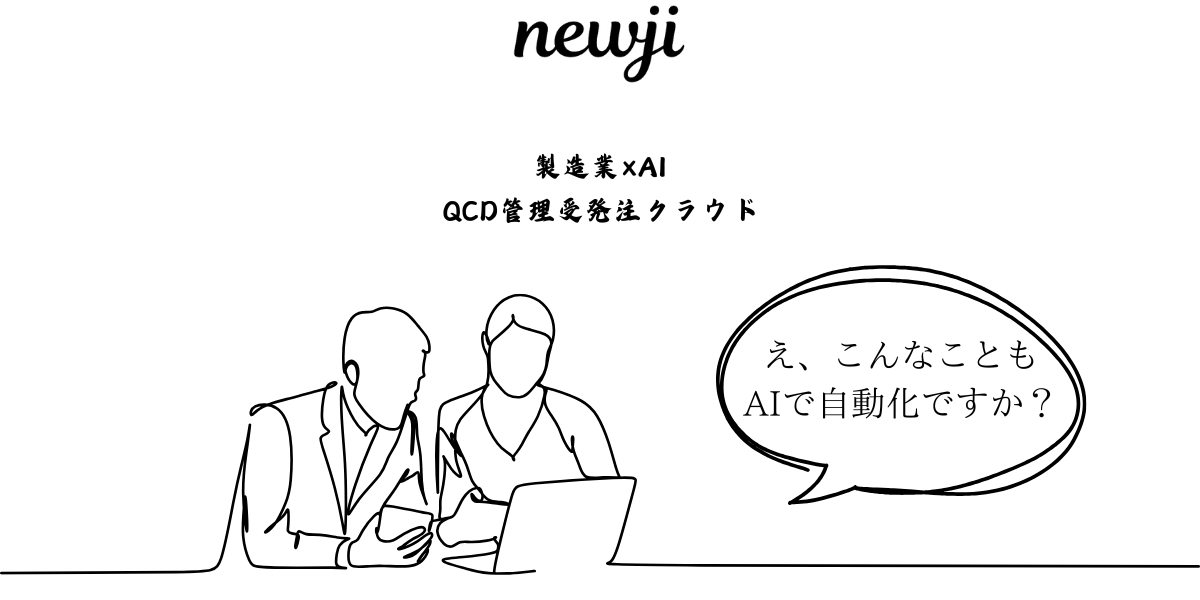
Proposal for improving productivity and efficiency through automation and mechanization of folding small boxes for dried noodles
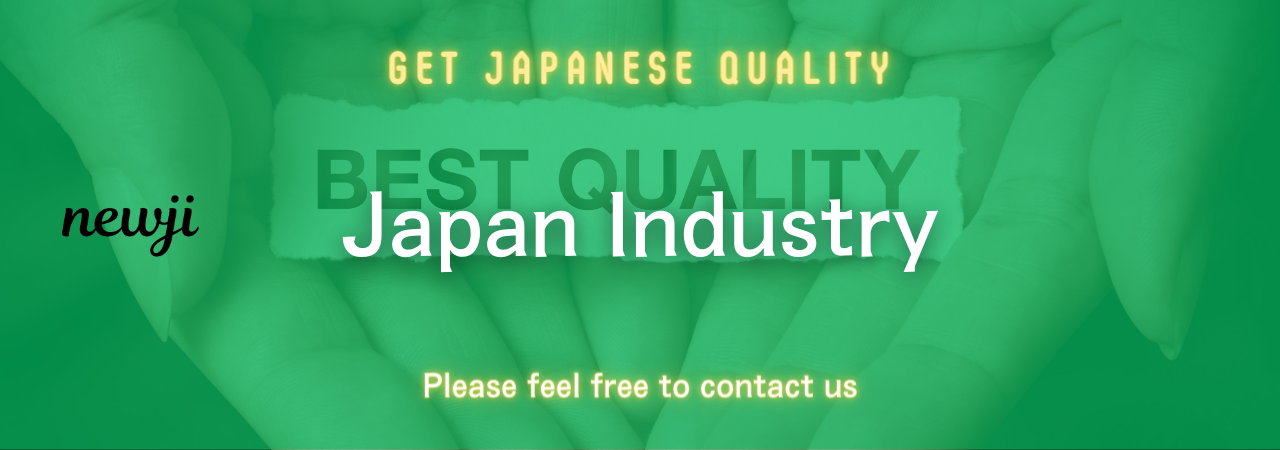
目次
Understanding the Need for Automation in Folding Small Boxes
The world of packaging is evolving, driven by the need for increased productivity and efficiency.
In industries dealing with dried noodles, manually folding small boxes can be a time-consuming task.
This manual process not only increases labor costs but also runs the risk of errors that can affect the quality of the final product.
Automation and mechanization present a remarkable opportunity to address these challenges.
By adopting advanced technologies, companies can streamline their operations, reduce manual labor, and improve precision, leading to higher productivity levels.
Benefits of Automating the Folding Process
Increased Efficiency
When small boxes for dried noodles are folded manually, the process can be slow and laborious.
Automation ensures that these boxes are folded quickly and accurately, drastically reducing the time required.
With automated systems, production lines run smoothly, without the disruptions common in manual processes.
As a result, companies can fulfill orders more rapidly, enhancing their ability to meet customer demands.
Cost Reduction
Labor costs can significantly impact a company’s bottom line.
By automating the folding process, businesses can save on the expenses associated with hiring multiple workers to handle the task.
Moreover, mechanization minimizes the risk of errors such as misfolding or damage, which can lead to costly waste and rework.
Consistency and Quality
Human errors can lead to inconsistencies in the folding of boxes, impacting the overall appearance and quality of packaging.
Automation guarantees precision and uniformity, ensuring each box is folded to the exact specifications required.
This consistency not only enhances the aesthetic appeal of the packaging but also ensures that the product is well-protected during transportation and storage.
Safety Improvements
Manual folding tasks can be repetitive and physically demanding, potentially leading to workplace injuries.
Automated systems reduce the need for manual labor, minimizing the risk of strain and injury among workers.
This leads to a safer working environment and reduces downtime related to employee injuries.
Implementing Automation in Folding Processes
Choosing the Right Equipment
When considering automation, it’s crucial to select equipment that integrates seamlessly into existing production lines.
Options abound, from fully automated folding machines to robotic arms that handle specific tasks.
Companies should evaluate their specific needs, considering factors such as production volume and budget, to determine the most suitable solution.
Training and Workforce Adaptation
Introducing automation doesn’t mean the end of human participation.
Instead, it transforms the nature of work.
Employees need training to operate and maintain automated systems, ensuring their smooth functioning and minimizing downtime.
This transition also grants workers the opportunity to focus on more skilled tasks, enhancing their job satisfaction and career development.
Monitoring and Maintenance
Regular monitoring and maintenance of automated systems are essential to keep them functioning at optimal levels.
Predictive maintenance technologies can be employed to identify potential issues before they escalate, minimizing disruptions in production.
An effective maintenance schedule helps maximize the lifespan of the equipment, ensuring a robust return on investment.
Overcoming Challenges in Automation Implementation
Initial Investment Costs
One of the primary concerns for businesses considering automation is the upfront investment required.
While the initial costs can be significant, the long-term savings in labor and improved efficiency often justify the expenditure.
Moreover, there are options available for financing and leasing that can make the transition more financially manageable.
Integration with Existing Systems
Integrating new automated systems with existing production lines can present challenges, especially in older setups.
It’s important to work with integration specialists who can ensure a seamless transition, minimizing disruptions during the implementation phase.
The goal is to achieve synergy between the new systems and legacy processes.
Resistance to Change
Employees accustomed to traditional methods may resist the introduction of automation.
Clear communication about the benefits and training opportunities is vital to ensure employee buy-in.
Highlighting the potential for skill development and a safer work environment can help overcome reluctance and foster enthusiasm for the new technology.
The Future of Automated Folding in Packaging
The move towards automation in folding small boxes for dried noodles is not just a trend but a necessity in the competitive landscape of modern manufacturing.
As technology continues to evolve, we can anticipate even more sophisticated and efficient systems.
These advancements will allow businesses to further enhance their productivity, reduce costs, and maintain high-quality standards.
In a rapidly changing world, the adoption of automation and mechanization in packaging processes is a vital strategy for staying ahead and thriving in the industry.
資料ダウンロード
QCD管理受発注クラウド「newji」は、受発注部門で必要なQCD管理全てを備えた、現場特化型兼クラウド型の今世紀最高の受発注管理システムとなります。
ユーザー登録
受発注業務の効率化だけでなく、システムを導入することで、コスト削減や製品・資材のステータス可視化のほか、属人化していた受発注情報の共有化による内部不正防止や統制にも役立ちます。
NEWJI DX
製造業に特化したデジタルトランスフォーメーション(DX)の実現を目指す請負開発型のコンサルティングサービスです。AI、iPaaS、および先端の技術を駆使して、製造プロセスの効率化、業務効率化、チームワーク強化、コスト削減、品質向上を実現します。このサービスは、製造業の課題を深く理解し、それに対する最適なデジタルソリューションを提供することで、企業が持続的な成長とイノベーションを達成できるようサポートします。
製造業ニュース解説
製造業、主に購買・調達部門にお勤めの方々に向けた情報を配信しております。
新任の方やベテランの方、管理職を対象とした幅広いコンテンツをご用意しております。
お問い合わせ
コストダウンが利益に直結する術だと理解していても、なかなか前に進めることができない状況。そんな時は、newjiのコストダウン自動化機能で大きく利益貢献しよう!
(β版非公開)