- お役立ち記事
- Prototype development using 3D printing that new leaders of design departments in medical device manufacturing industries should know
Prototype development using 3D printing that new leaders of design departments in medical device manufacturing industries should know
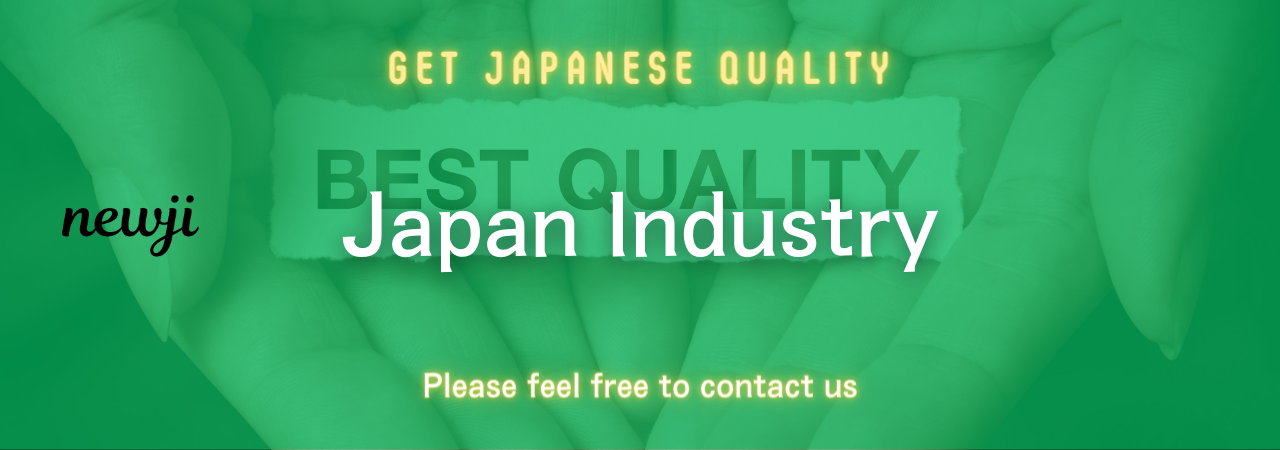
目次
Introduction to 3D Printing in Medical Device Manufacturing
In recent years, 3D printing has revolutionized many industries, with medical device manufacturing being no exception.
As a new leader in the design department, it is crucial to understand how 3D printing can benefit prototype development.
This technology offers innovative solutions, allowing for faster, more efficient creation of medical devices, which can significantly shorten the production cycle and enhance design precision.
The Basics of 3D Printing Technology
3D printing, also known as additive manufacturing, involves creating three-dimensional objects from digital files.
This is done by adding material layer by layer until the desired shape is achieved.
This approach contrasts with traditional manufacturing methods that often involve subtractive processes, such as cutting or drilling, which remove material to achieve the same goal.
The materials used in 3D printing can vary widely.
In medical device manufacturing, common materials include plastics, resins, metals, and biocompatible materials.
These materials are chosen for their compatibility with human tissues and the specific requirements of various medical applications.
Types of 3D Printing Technologies in Medicine
Several 3D printing technologies are available for medical applications, each offering unique advantages:
1. **Fused Deposition Modeling (FDM):** This is one of the most widely used methods because of its low cost and versatility. It is ideal for creating basic prototypes and model designs.
2. **Selective Laser Sintering (SLS):** SLS uses a laser to sinter powdered material into a solid structure. It is useful for producing complex shapes and is suitable for high-performance materials.
3. **Stereolithography (SLA):** SLA uses a laser to cure liquid resin into hardened plastic. It is known for its high accuracy and smooth surface finish, making it suitable for detailed prototypes.
4. **Direct Metal Laser Sintering (DMLS):** This method involves sintering metal powder with a laser to create parts with metal properties, ideal for durable and functional parts.
Benefits of 3D Printing in Prototype Development
The integration of 3D printing into prototype development offers several benefits, particularly in the fast-paced medical devices industry.
Rapid Prototyping
One of the most significant advantages of 3D printing is its ability to produce prototypes quickly.
Rapid prototyping reduces the time from design to production, allowing design teams to test and adjust their designs in a much shorter timeframe.
This accelerates the entire development process and brings products to market faster.
Cost Efficiency
3D printing significantly reduces material waste compared to traditional subtractive manufacturing techniques.
This efficiency in material usage translates to cost savings, especially for small production runs or one-off prototypes.
Moreover, 3D printing reduces the need for expensive tooling, further cutting project costs.
Design Flexibility and Complexity
Medical device designs often require precise and intricate details.
3D printing can produce complex geometries that would be difficult or impossible to achieve with traditional methods.
Designers can easily adjust and customize prototypes according to specific medical needs, resulting in more innovative and effective devices.
Customization
Patient-specific medical devices are becoming increasingly important in sectors such as orthopedics and prosthetics.
3D printing allows for the creation of tailored devices that perfectly match an individual’s anatomy.
This level of customization can lead to better patient outcomes and increased satisfaction.
Challenges in 3D Printing for Medical Devices
While 3D printing brings numerous benefits, certain challenges must be addressed to ensure successful implementation in medical device manufacturing.
Regulatory Compliance
Regulatory compliance is one of the most significant hurdles in adopting 3D printing for medical devices.
Devices must meet strict standards set by organizations such as the FDA and ISO.
This requires thorough testing and validation to ensure patient safety and device efficacy, which can be time-consuming and complex.
Material Limitations
Not all materials used in 3D printing are suitable for medical applications.
Ensuring biocompatibility and structural integrity while selecting materials is crucial.
Ongoing research and development are expanding the range of viable materials, but limitations remain a concern.
Quality Assurance
Consistency and repeatability in 3D printing processes are essential for quality assurance.
Slight variations can lead to defects, which are unacceptable in medical device manufacturing.
Implementing stricter controls and robust inspection processes can mitigate this challenge.
Future of 3D Printing in Medical Device Prototyping
The future of 3D printing in medical device prototyping looks promising, with continuous advancements and innovations expected to enhance its capabilities further.
Integration with Advanced Technologies
Integrating 3D printing with other advanced technologies, such as AI and machine learning, could revolutionize medical device design.
These technologies can optimize designs, predict failures, and improve the overall production process.
Expansion of Biocompatible Materials
Research into new biocompatible materials will expand the possibilities of what can be manufactured.
This will enable the development of more complex and functional medical devices that are safe for human use.
Improved Speed and Efficiency
As 3D printing technologies evolve, improvements in printing speed and efficiency are expected.
This will further reduce development timelines, enabling more responsive and adaptive production strategies.
Conclusion
For leaders in the medical device manufacturing industry, understanding the advantages and challenges of 3D printing for prototype development is crucial.
The ability to produce rapid, cost-effective, and customized prototypes can set a company apart in this competitive field.
By staying informed about the latest advancements in 3D printing technology, design teams can harness its full potential, ensuring that they remain at the forefront of innovation and deliver better patient outcomes.
資料ダウンロード
QCD調達購買管理クラウド「newji」は、調達購買部門で必要なQCD管理全てを備えた、現場特化型兼クラウド型の今世紀最高の購買管理システムとなります。
ユーザー登録
調達購買業務の効率化だけでなく、システムを導入することで、コスト削減や製品・資材のステータス可視化のほか、属人化していた購買情報の共有化による内部不正防止や統制にも役立ちます。
NEWJI DX
製造業に特化したデジタルトランスフォーメーション(DX)の実現を目指す請負開発型のコンサルティングサービスです。AI、iPaaS、および先端の技術を駆使して、製造プロセスの効率化、業務効率化、チームワーク強化、コスト削減、品質向上を実現します。このサービスは、製造業の課題を深く理解し、それに対する最適なデジタルソリューションを提供することで、企業が持続的な成長とイノベーションを達成できるようサポートします。
オンライン講座
製造業、主に購買・調達部門にお勤めの方々に向けた情報を配信しております。
新任の方やベテランの方、管理職を対象とした幅広いコンテンツをご用意しております。
お問い合わせ
コストダウンが利益に直結する術だと理解していても、なかなか前に進めることができない状況。そんな時は、newjiのコストダウン自動化機能で大きく利益貢献しよう!
(Β版非公開)