- お役立ち記事
- Prototype of dust collector with particulate explosion-proof measures ensures safety of powder production line
月間76,176名の
製造業ご担当者様が閲覧しています*
*2025年3月31日現在のGoogle Analyticsのデータより
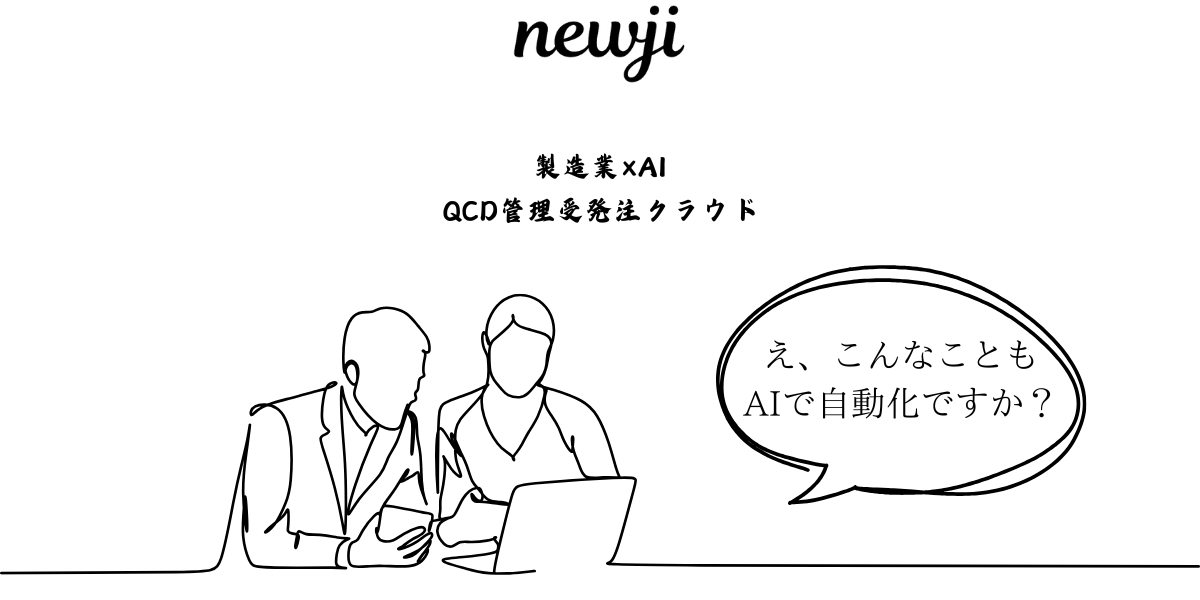
Prototype of dust collector with particulate explosion-proof measures ensures safety of powder production line
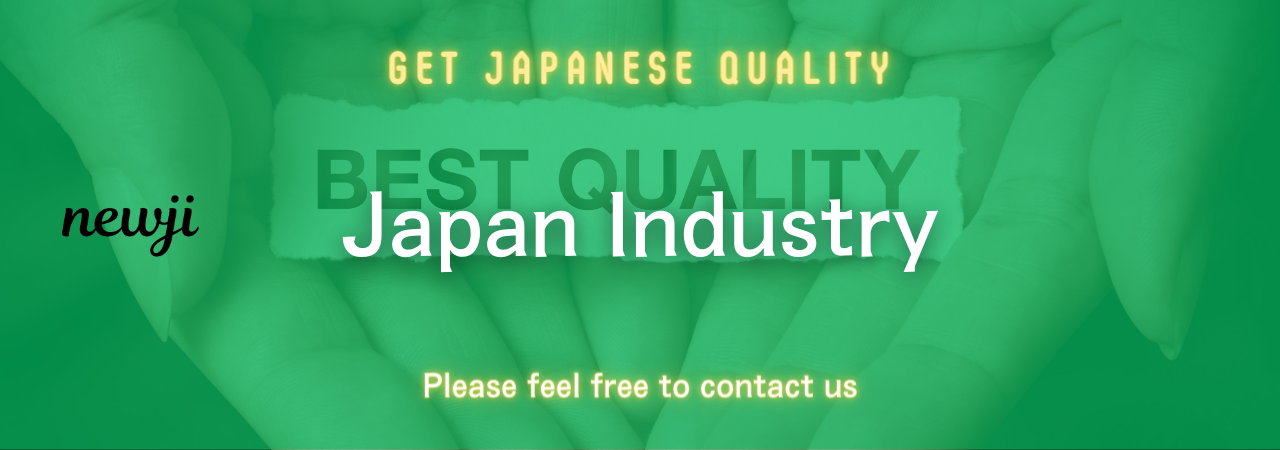
目次
Understanding the Need for Dust Collectors in Powder Production
In various industries, especially in the powder production sector, managing dust is a critical concern.
Particles generated during production can be hazardous, potentially causing explosions if not effectively controlled.
That’s where a robust dust collector becomes essential, especially one with particulate explosion-proof measures.
This article will explore the significance of these devices and how they contribute to safety on production lines.
The Dangers of Particulate Matter
Dust in powder production facilities can pose significant risks.
It’s not just a cleanliness issue; fine particles suspended in the air can lead to catastrophic explosions.
When the concentration of dust becomes high and meets an ignition source, it can trigger an explosion.
This poses dangers to both human life and the production infrastructure.
Ensuring that dust levels remain controlled is crucial to maintaining safety standards.
How Dust Collectors Work
Dust collectors are specialized devices designed to capture dust particles from air or gas streams.
The process typically involves drawing in contaminated air, filtering out the dust, and then releasing clean air back into the environment.
A prototype dust collector incorporates advanced measures to minimize the risk of particles causing explosions.
This includes utilizing explosion-proof materials and designs that prevent the buildup of ignitable dust levels.
Explosion-Proof Measures in Dust Collectors
To be explosion-proof, dust collectors must meet specific safety standards.
These include using materials that are resistant to sparks and high temperatures and designing equipment to withstand the pressures of an explosion, should one occur.
The prototype of a dust collector engineered with these considerations ensures that any ignition will not result in catastrophic failure.
Materials and Design Innovations
Engineers have introduced several design innovations in these dust collectors.
For instance, using antistatic materials helps to reduce the risk of static electricity igniting the dust.
Additionally, advanced filtration systems can capture even the finest particles, preventing them from accumulating to dangerous levels.
Field trials of these prototypes have shown that they significantly enhance safety on production lines.
Benefits for the Powder Production Industry
Implementing explosion-proof dust collectors offers several benefits to the powder production industry.
First, it creates a safer work environment, which is critical for employee safety and compliance with industry regulations.
Moreover, by reducing the risk of explosions, companies can minimize downtime and potential damages, leading to cost savings.
Additionally, these systems often improve the overall air quality within facilities, which can enhance both product quality and employee health.
Regulatory Compliance and Industry Standards
Safety regulations related to dust and particulate matter are stringent, especially in industries dealing with combustible materials.
Adopting dust collectors that incorporate explosion-proof measures helps companies comply with these regulations.
This includes meeting standards set by organizations such as the Occupational Safety and Health Administration (OSHA) and the National Fire Protection Association (NFPA).
Conclusion: Ensuring Safety and Efficiency
The development of explosion-proof dust collectors marks a significant step forward for the powder production industry.
These systems not only protect against explosions but also enhance the overall efficiency of production processes by ensuring a cleaner and safer work environment.
As industries continue to prioritize safety and efficiency, the role of these innovative dust collectors will undoubtedly become even more pivotal.
Investing in such technology is not just about compliance; it’s about proactively protecting people, equipment, and the future of the production line.
資料ダウンロード
QCD管理受発注クラウド「newji」は、受発注部門で必要なQCD管理全てを備えた、現場特化型兼クラウド型の今世紀最高の受発注管理システムとなります。
ユーザー登録
受発注業務の効率化だけでなく、システムを導入することで、コスト削減や製品・資材のステータス可視化のほか、属人化していた受発注情報の共有化による内部不正防止や統制にも役立ちます。
NEWJI DX
製造業に特化したデジタルトランスフォーメーション(DX)の実現を目指す請負開発型のコンサルティングサービスです。AI、iPaaS、および先端の技術を駆使して、製造プロセスの効率化、業務効率化、チームワーク強化、コスト削減、品質向上を実現します。このサービスは、製造業の課題を深く理解し、それに対する最適なデジタルソリューションを提供することで、企業が持続的な成長とイノベーションを達成できるようサポートします。
製造業ニュース解説
製造業、主に購買・調達部門にお勤めの方々に向けた情報を配信しております。
新任の方やベテランの方、管理職を対象とした幅広いコンテンツをご用意しております。
お問い合わせ
コストダウンが利益に直結する術だと理解していても、なかなか前に進めることができない状況。そんな時は、newjiのコストダウン自動化機能で大きく利益貢献しよう!
(β版非公開)