- お役立ち記事
- Prototype of medical medication robot: Development process that balances sensor interlocking and machine safety
月間76,176名の
製造業ご担当者様が閲覧しています*
*2025年3月31日現在のGoogle Analyticsのデータより
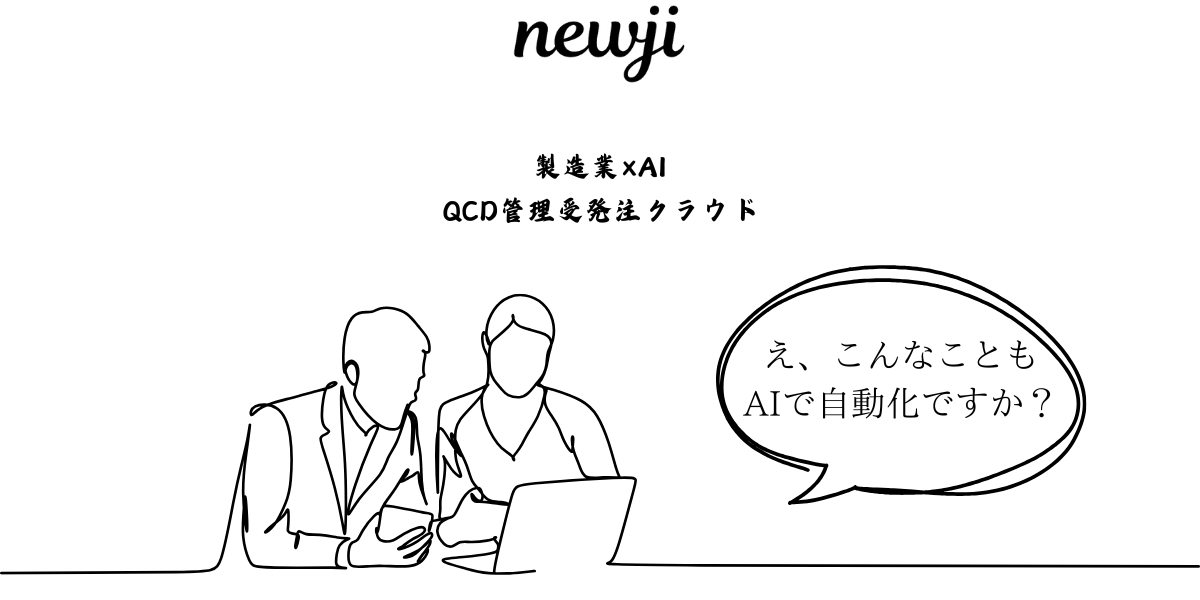
Prototype of medical medication robot: Development process that balances sensor interlocking and machine safety
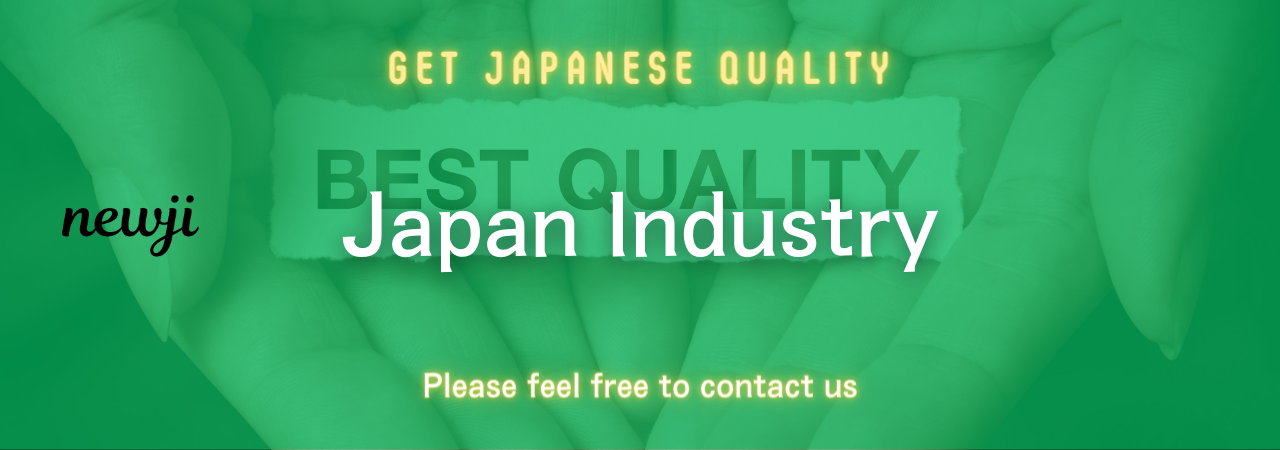
目次
Introduction to Medical Medication Robots
In today’s rapidly advancing technological landscape, the medical field is not left behind.
One of the most promising innovations is the development of medical medication robots.
These robots are designed to accurately dispense medications to patients, ensuring precision, safety, and efficiency.
The prototype development of such a robot involves overcoming several challenges, including balancing sensor interlocking with machine safety.
Understanding Sensor Interlocking
Sensor interlocking is a critical component in the design of medical medication robots.
It involves the integration of sensory systems that enable the robot to detect and adapt to changes in the environment.
These sensors help the robot to navigate, identify obstacles, and perform tasks with great precision.
For a medication robot, sensor interlocking ensures that it administers the correct dosage of medication to the right patient.
Sensors such as RFID tags, barcode readers, and vision systems are utilized to verify patient information and medication details.
The Role of RFID Technology
RFID (Radio Frequency Identification) technology is used extensively in medical medication robots.
It enables wireless communication between the robot and RFID tags placed on medication packaging or patient identification wristbands.
This communication ensures the robot dispenses the correct medication by matching the RFID data with the patient’s prescription details.
Furthermore, RFID technology enhances the traceability and tracking of medications, reducing the risk of errors and ensuring that the right patient receives the correct treatment.
Incorporating Vision Systems
Vision systems provide robots with the ability to interpret visual information.
In the context of medical medication robots, these systems allow the robot to identify medications based on size, shape, and packaging.
This information is crucial for verifying that the correct medication is being dispensed.
Additionally, vision systems can be employed to ascertain the surroundings, ensuring the robot navigates safely in environments such as a hospital or pharmacy setting.
Ensuring Machine Safety
While sensor interlocking provides accuracy and functionality, ensuring machine safety is paramount in the development of medical medication robots.
Safety mechanisms must be in place to protect both patients and healthcare workers from potential accidents or malfunctions.
Designing for Fail-Safe Operations
To maintain safety, medical medication robots are designed with fail-safe operations.
These are backup systems or protocols that automatically activate in the event of a malfunction or unexpected situation.
For example, if a sensor fails to read information accurately, the robot can halt operations and alert human operators for intervention.
Fail-safe operations minimize risks, enabling safe and reliable medication dispensing even under unexpected circumstances.
Implementing Emergency Stop Functions
An emergency stop function is another critical safety feature integrated into medical medication robots.
This allows operators to immediately cease robot operation if a dangerous situation is detected.
Easy-to-access emergency stop buttons or switches enable quick responses, ensuring the safety of all individuals in the vicinity.
By combining advanced sensor technologies with protective safety measures, developers create a balanced system that prioritizes both efficacy and user safety.
The Development Process of Medical Medication Robots
Developing a prototype of a medical medication robot requires a collaborative effort.
It involves multiple stages from initial concept to testing and refinement.
This comprehensive process helps bring ideas to reality while ensuring that the finished product meets industry standards.
Conceptualization and Design
The first phase in the development process is conceptualization and design.
This stage involves identifying the specific needs the robot must address and designing a robot capable of meeting those needs.
Designers and engineers work closely with healthcare professionals to understand requirements and constraints.
During this phase, considerations such as size, maneuverability, and capacity are evaluated while ensuring the design accommodates the necessary technological components effectively.
Prototyping and Testing
After the design is finalized, the prototyping phase begins.
Initial prototypes are created to test and evaluate various aspects of the robot’s functionality.
These prototypes enable developers to identify any issues or improvements needed before final production.
Testing is rigorous, involving simulations and real-world scenarios to ensure the robot performs accurately and consistently.
Feedback from healthcare professionals during testing is critical in making necessary adjustments.
Iterative Refinement and Validation
The iterative refinement and validation phase follow prototyping and testing.
This involves multiple cycles of making improvements, retesting, and refining the robot’s design and functionality.
The goal is to optimize performance, enhance safety, and ensure compliance with regulatory standards.
Validation ensures that the robot meets all the necessary criteria for reliable and safe operation, readying it for integration within medical environments.
Conclusion
The prototype development of medical medication robots involves a complex, dynamic process.
By balancing sensor interlocking with machine safety, these robots promise to revolutionize the way medications are dispensed, providing accurate and efficient solutions that enhance patient care in the medical field.
As technology continues to evolve, so will the capabilities of these robots, leading to even greater advancements in healthcare automation and improving patient outcomes globally.
資料ダウンロード
QCD管理受発注クラウド「newji」は、受発注部門で必要なQCD管理全てを備えた、現場特化型兼クラウド型の今世紀最高の受発注管理システムとなります。
ユーザー登録
受発注業務の効率化だけでなく、システムを導入することで、コスト削減や製品・資材のステータス可視化のほか、属人化していた受発注情報の共有化による内部不正防止や統制にも役立ちます。
NEWJI DX
製造業に特化したデジタルトランスフォーメーション(DX)の実現を目指す請負開発型のコンサルティングサービスです。AI、iPaaS、および先端の技術を駆使して、製造プロセスの効率化、業務効率化、チームワーク強化、コスト削減、品質向上を実現します。このサービスは、製造業の課題を深く理解し、それに対する最適なデジタルソリューションを提供することで、企業が持続的な成長とイノベーションを達成できるようサポートします。
製造業ニュース解説
製造業、主に購買・調達部門にお勤めの方々に向けた情報を配信しております。
新任の方やベテランの方、管理職を対象とした幅広いコンテンツをご用意しております。
お問い合わせ
コストダウンが利益に直結する術だと理解していても、なかなか前に進めることができない状況。そんな時は、newjiのコストダウン自動化機能で大きく利益貢献しよう!
(β版非公開)