- お役立ち記事
- Prototype of turbine impeller using particle-reinforced PEEK material achieves both wear resistance and weight reduction
月間76,176名の
製造業ご担当者様が閲覧しています*
*2025年3月31日現在のGoogle Analyticsのデータより
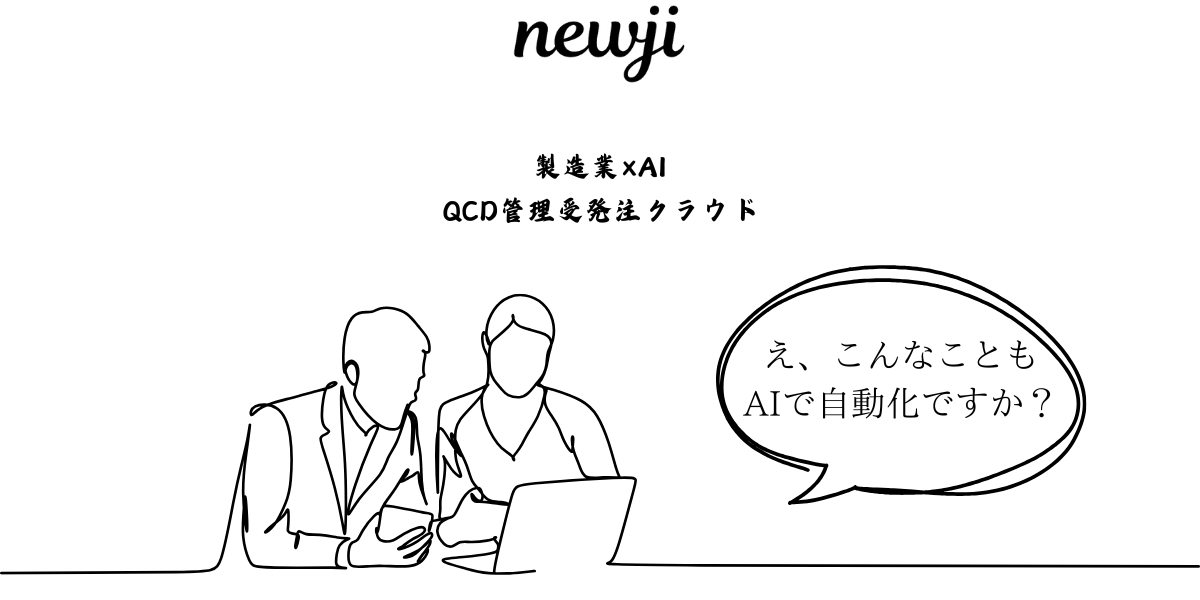
Prototype of turbine impeller using particle-reinforced PEEK material achieves both wear resistance and weight reduction
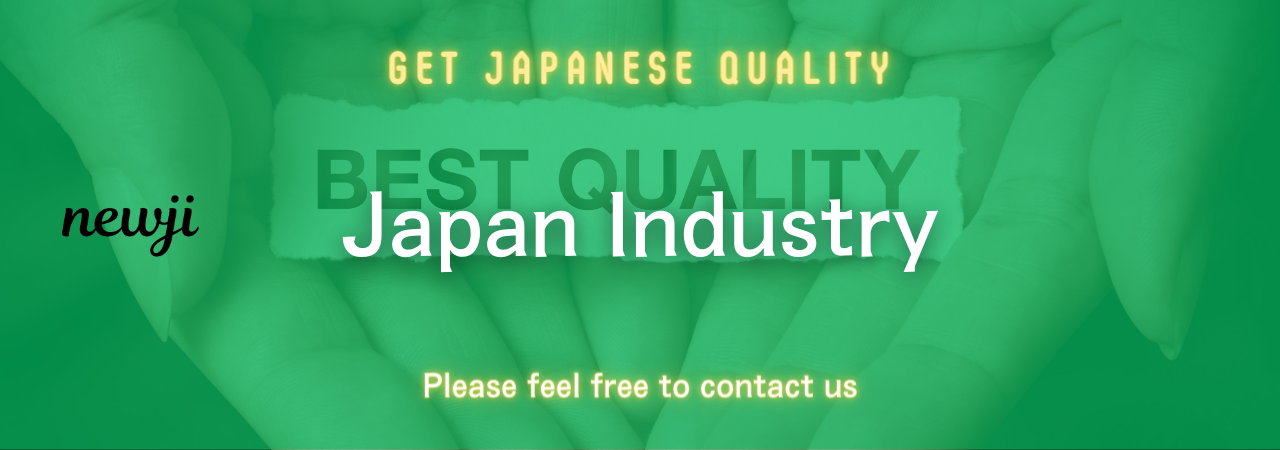
目次
Understanding PEEK Material
Polyether ether ketone, commonly known as PEEK, is a high-performance engineering thermoplastic.
It is renowned for its excellent mechanical and chemical resistance properties.
PEEK is particularly useful in applications that demand durability, such as aerospace, automotive, and medical industries.
One of the standout characteristics of PEEK is its ability to maintain stiffness at high temperatures, making it a preferred material for components subjected to harsh environments.
Moreover, it possesses low moisture absorption and good resistance to various solvents.
Why Use PEEK in Turbine Impellers?
In the design and manufacturing of turbine impellers, materials that offer both strength and lightweight properties are highly sought after.
Traditionally, metals like aluminum and titanium are used due to their robustness.
However, metals add significant weight, which can impact the efficiency of turbines.
This is where PEEK comes into play.
Its lightweight nature significantly reduces the overall weight of the impeller, contributing to enhanced turbine efficiency.
Additionally, by incorporating particle reinforcement in the PEEK material, engineers can further improve its wear resistance, which is crucial for extending the lifespan of turbine components.
Developing the Prototype
Creating a prototype using particle-reinforced PEEK involves a meticulous process to ensure the material’s integrity and performance.
Firstly, the development begins with selecting the appropriate particle reinforcement that complements PEEK’s inherent properties.
Typically, materials like carbon fibers or glass fibers are used as reinforcements.
These particles help increase the tensile strength and wear resistance of the base PEEK material.
Next, the composite material is processed using methods such as injection molding or compression molding.
These processes ensure the fibers are evenly distributed within the PEEK matrix, resulting in a uniform microstructure.
The prototype is then fabricated to adhere to the specific design parameters of a turbine impeller, requiring precision to achieve optimal aerodynamic performance.
Testing and Evaluation
Once the prototype is developed, rigorous testing is necessary to evaluate its performance.
Wear resistance is one of the primary factors to assess.
The prototype is subjected to conditions that mimic real-life operational environments.
Simulations and physical tests determine how well the PEEK impeller can withstand friction, high pressure, and temperature changes.
Weight reduction is another key metric.
The prototype is compared against traditional metal impellers to quantify the potential weight savings.
In tests, prototypes made from particle-reinforced PEEK have shown notable efficiency improvements due to reduced rotational mass.
Advantages of Using Particle-Reinforced PEEK
The use of PEEK not only offers performance and durability but also promises a greener alternative to metals.
The production of thermoplastics generally requires less energy and emits fewer pollutants compared to metal processing.
Moreover, the lightweight characteristics of PEEK significantly lower fuel consumption in applications like turbines, contributing to reduced greenhouse gas emissions over the component’s life cycle.
Another advantage is the reduction in maintenance costs.
The enhanced wear resistance means that components last longer, requiring fewer replacements and less frequent maintenance, which translates to cost savings.
Applications Beyond Turbine Impellers
While the current focus is on turbine impellers, the successful implementation of particle-reinforced PEEK can be extended to other components and industries.
In the automotive sector, this material could potentially replace metal parts in engines or high-stress areas, providing the benefit of weight reduction without compromising strength.
In the medical field, PEEK’s biocompatibility makes it suitable for implants and surgical instruments where wear resistance is crucial.
Challenges and Future Prospects
Despite the advantages, there are challenges in transitioning from traditional materials to particle-reinforced PEEK.
One significant hurdle is the initial cost of the material.
PEEK and its reinforced variants are generally more expensive than common metals, which can be a barrier for widespread adoption.
However, as technology advances and production scales up, costs are anticipated to decrease, making it more accessible.
Looking ahead, further research and development will focus on enhancing the properties of PEEK composites.
Innovation in manufacturing processes could lead to even more versatile applications, reinforcing the role of PEEK as a pivotal material in engineering solutions.
Researchers are also exploring combinations of various particle types to tailor the properties of PEEK to suit specific needs better.
In conclusion, the development of turbine impellers using particle-reinforced PEEK exemplifies a significant stride towards efficient, durable, and eco-friendly engineering solutions.
As industries continue to aim for sustainability and performance, the role of advanced materials like PEEK will become increasingly prominent.
資料ダウンロード
QCD管理受発注クラウド「newji」は、受発注部門で必要なQCD管理全てを備えた、現場特化型兼クラウド型の今世紀最高の受発注管理システムとなります。
ユーザー登録
受発注業務の効率化だけでなく、システムを導入することで、コスト削減や製品・資材のステータス可視化のほか、属人化していた受発注情報の共有化による内部不正防止や統制にも役立ちます。
NEWJI DX
製造業に特化したデジタルトランスフォーメーション(DX)の実現を目指す請負開発型のコンサルティングサービスです。AI、iPaaS、および先端の技術を駆使して、製造プロセスの効率化、業務効率化、チームワーク強化、コスト削減、品質向上を実現します。このサービスは、製造業の課題を深く理解し、それに対する最適なデジタルソリューションを提供することで、企業が持続的な成長とイノベーションを達成できるようサポートします。
製造業ニュース解説
製造業、主に購買・調達部門にお勤めの方々に向けた情報を配信しております。
新任の方やベテランの方、管理職を対象とした幅広いコンテンツをご用意しております。
お問い合わせ
コストダウンが利益に直結する術だと理解していても、なかなか前に進めることができない状況。そんな時は、newjiのコストダウン自動化機能で大きく利益貢献しよう!
(β版非公開)