- お役立ち記事
- Prototyping and steps towards mass production of metal connectors for optical cables
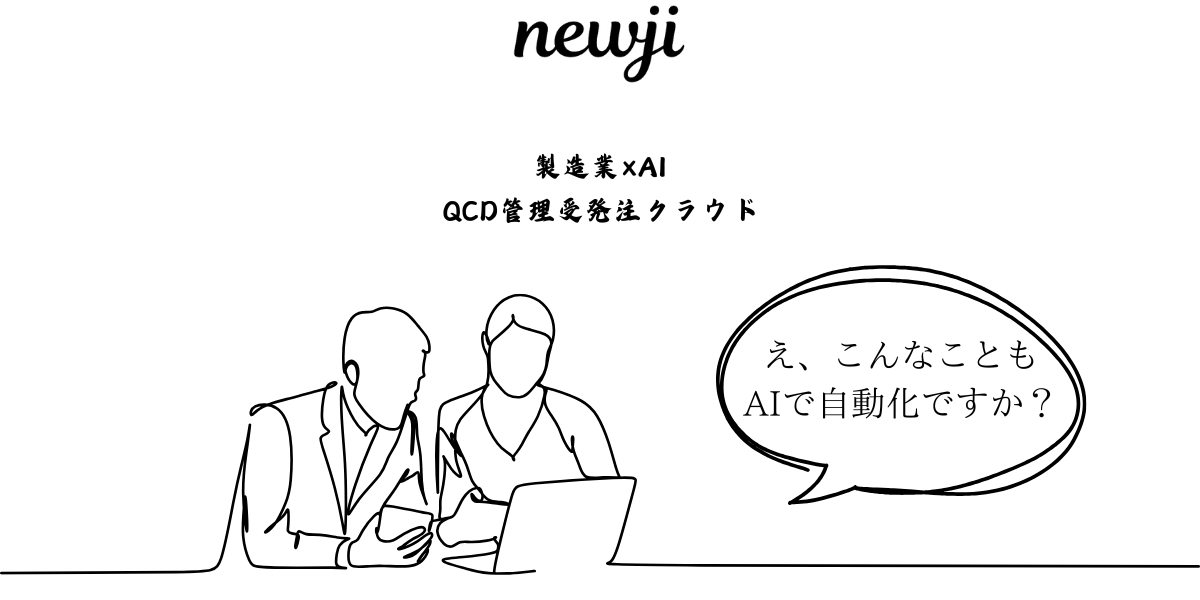
Prototyping and steps towards mass production of metal connectors for optical cables
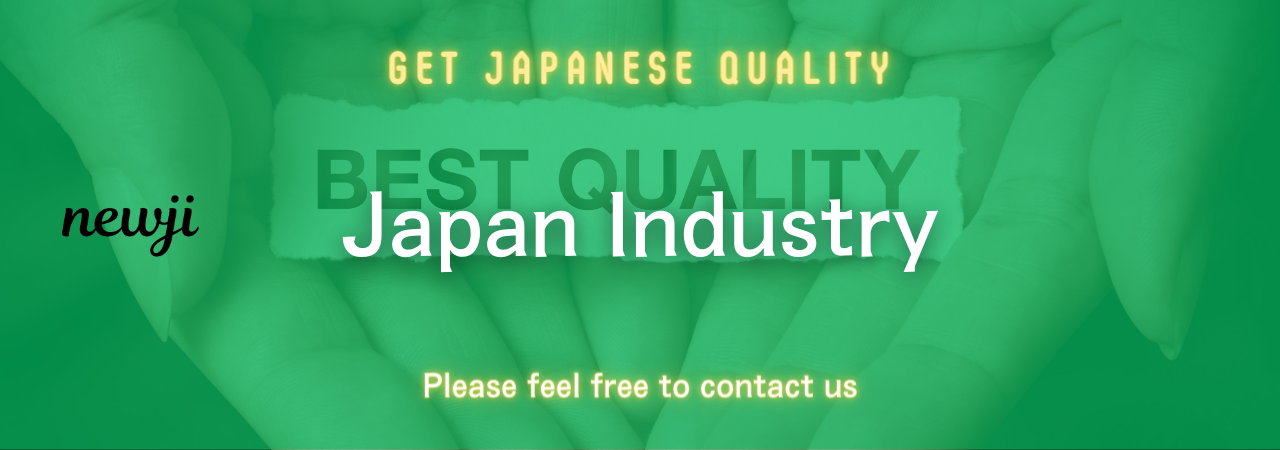
目次
Understanding Metal Connectors for Optical Cables
Optical cables are essential in today’s digital age, providing fast and reliable data transmission across long distances.
At the heart of these cables are the metal connectors, which play a critical role in ensuring optimal performance.
In this article, we will explore the prototyping process and steps taken towards mass production of these metal connectors.
The Importance of Metal Connectors
Metal connectors serve as the vital link between optical cables and various networking devices.
They enable secure and efficient data transfer, minimizing signal loss and interference.
The design and quality of these connectors directly affect the overall performance of the optical network.
Therefore, it is crucial to focus on developing connectors that are both durable and reliable.
Prototyping Process of Metal Connectors
The first step in creating metal connectors for optical cables is the prototyping phase.
This process involves several key stages, including design, material selection, and initial testing.
Design and Conceptualization
Before any physical prototype can be developed, a comprehensive design needs to be created.
This involves careful planning and conceptualization to ensure the connector will function as intended.
Engineers and designers work together to produce detailed schematics and 3D models of the connector.
Material Selection
Choosing the right material is vital for the success of the prototype.
Metal connectors must be made from materials that are strong, conductive, and resistant to corrosion.
Common materials used include stainless steel, brass, and aluminum.
Each of these materials offers unique properties that contribute to the connector’s performance.
Initial Testing and Evaluation
Once a prototype is created, it undergoes rigorous testing to evaluate its performance.
This involves checking its conductivity, strength, and resistance to various environmental factors.
Any flaws or weaknesses are identified and addressed to refine the design.
Steps Towards Mass Production
After a successful prototype is developed, the focus shifts to preparing for mass production.
This involves several critical steps to ensure the final product meets industry standards and customer demands.
Streamlining the Manufacturing Process
To achieve efficient mass production, the manufacturing process must be streamlined.
This is done by optimizing production lines and automating key tasks where possible.
Automation not only enhances efficiency but also ensures consistency in the quality of the connectors.
Quality Control Measures
Quality control is essential in mass production to ensure each connector meets the required standards.
This includes regular inspections and testing of random samples from each production batch.
Advanced technologies such as X-ray inspection and 3D imaging are often employed to detect any defects.
Meeting Industry Standards
Compliance with industry standards is mandatory for the production of metal connectors.
Standards such as ISO and ANSI provide guidelines that manufacturers must follow to ensure product quality and safety.
Adhering to these standards not only assures customers of the product’s reliability but also helps build trust in the market.
Challenges in Prototyping and Mass Production
The journey from prototyping to mass production is not without its challenges.
There are several hurdles that manufacturers must overcome to deliver a high-quality product.
Technical Challenges
One of the main challenges is ensuring the connector’s compatibility with various optical cables and devices.
This requires constant refinement and adaptation of the design to meet evolving technological requirements.
Cost Management
Managing costs is another significant challenge in the production process.
From material acquisition to labor and manufacturing, controlling expenses while maintaining quality is crucial for profitability.
Environmental Considerations
Manufacturers are increasingly focusing on sustainability and minimizing environmental impact.
This involves using eco-friendly materials and reducing waste throughout the production process.
Conclusion
The journey from designing prototypes to achieving mass production of metal connectors for optical cables is a meticulous process.
It involves careful planning, rigorous testing, and adherence to industry standards to ensure each connector performs optimally.
Overcoming challenges such as technical compatibility and cost management is key to success.
By focusing on these aspects, manufacturers can produce high-quality connectors that support the growing demands of the digital age.
資料ダウンロード
QCD調達購買管理クラウド「newji」は、調達購買部門で必要なQCD管理全てを備えた、現場特化型兼クラウド型の今世紀最高の購買管理システムとなります。
ユーザー登録
調達購買業務の効率化だけでなく、システムを導入することで、コスト削減や製品・資材のステータス可視化のほか、属人化していた購買情報の共有化による内部不正防止や統制にも役立ちます。
NEWJI DX
製造業に特化したデジタルトランスフォーメーション(DX)の実現を目指す請負開発型のコンサルティングサービスです。AI、iPaaS、および先端の技術を駆使して、製造プロセスの効率化、業務効率化、チームワーク強化、コスト削減、品質向上を実現します。このサービスは、製造業の課題を深く理解し、それに対する最適なデジタルソリューションを提供することで、企業が持続的な成長とイノベーションを達成できるようサポートします。
オンライン講座
製造業、主に購買・調達部門にお勤めの方々に向けた情報を配信しております。
新任の方やベテランの方、管理職を対象とした幅広いコンテンツをご用意しております。
お問い合わせ
コストダウンが利益に直結する術だと理解していても、なかなか前に進めることができない状況。そんな時は、newjiのコストダウン自動化機能で大きく利益貢献しよう!
(Β版非公開)