- お役立ち記事
- Providing High-Precision Joining Parts with Spot Welding OEM
Providing High-Precision Joining Parts with Spot Welding OEM
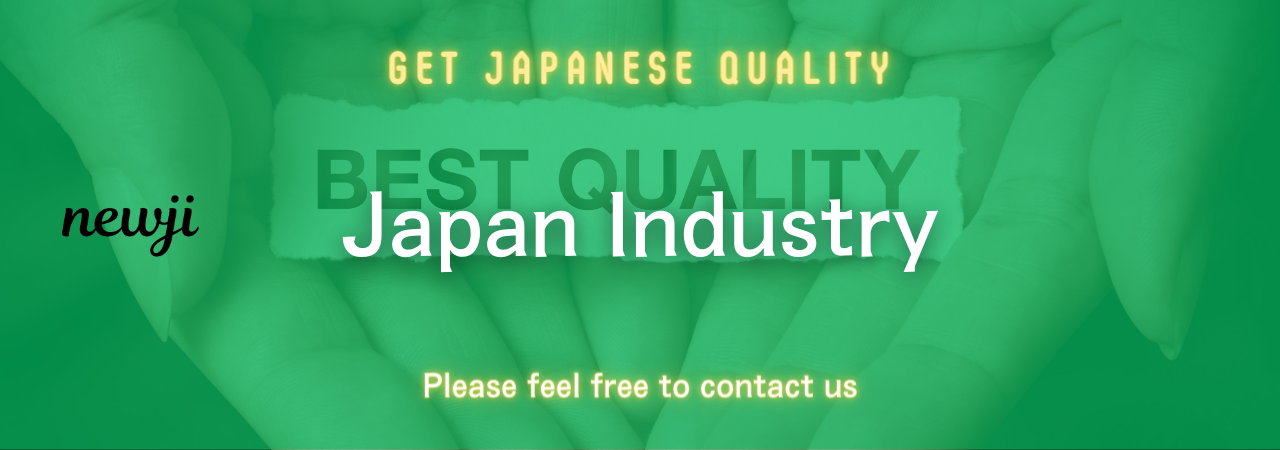
Spot welding is a process that involves joining two metal pieces together by applying pressure and heat from an electric current to the weld area.
This technique is widely used in various industries due to its efficiency and reliability.
High-precision spot welding ensures that the final products are durable and of high quality.
In this article, we will discuss the benefits of providing high-precision joining parts with spot welding OEM.
目次
Understanding Spot Welding OEM
OEM stands for Original Equipment Manufacturer.
When it comes to spot welding, an OEM is responsible for producing high-precision parts for various applications.
These applications range from automotive to electronics and even aerospace industries.
OEMs that specialize in spot welding must maintain stringent quality standards to meet the specific needs of their clients.
This ensures that the joining parts are of superior quality and can withstand the rigorous demands of their respective industries.
Benefits of High-Precision Spot Welding
There are several advantages to utilizing high-precision spot welding in manufacturing processes.
Let’s explore some of these benefits in detail.
1. Enhanced Durability
High-precision spot welding provides a strong bond between metal parts.
This bond enhances the durability of the final product, ensuring it can endure significant stress and wear and tear.
Whether it’s for automotive components or electronic devices, the durability of welded joints is crucial for the overall reliability and longevity of the product.
2. Improved Efficiency
Spot welding is a rapid process, which significantly reduces production time compared to other welding methods.
The high precision involved ensures that the welding is done correctly the first time, minimizing the need for rework and thus boosting overall efficiency.
This efficiency translates to cost savings for manufacturers and faster delivery times for clients.
3. Consistent Quality
One of the primary benefits of high-precision spot welding is the consistency in the quality of the welds.
Automated spot welding systems ensure that each weld is made with the same parameters, resulting in a uniform and high-quality finish.
Consistent quality is vital in industries where precision and reliability are non-negotiable.
4. Versatility in Application
High-precision spot welding is versatile and can be used on various metals, including steel, aluminum, and copper.
This versatility makes spot welding OEMs an invaluable asset in multiple industries.
For example, the automotive industry relies heavily on spot welding for assembling car body parts, while the electronics industry uses it for making battery packs and other components.
Applications of Spot Welding in Different Industries
Spot welding OEMs cater to a diverse range of industries.
Let’s take a closer look at some of the key sectors where high-precision spot welding is indispensable.
1. Automotive Industry
The automotive industry is one of the largest users of spot welding.
Cars are constructed from numerous metal components that need to be securely joined.
High-precision spot welding is used to assemble car bodies, frames, and other critical parts.
This ensures that the vehicles are safe, reliable, and meet stringent quality standards.
2. Electronics Industry
In the electronics industry, spot welding is used for assembling battery packs, wiring harnesses, and other small components.
High-precision welding is essential to ensure the reliability and efficiency of electronic devices.
Given the small and delicate nature of electronic parts, precision in welding is crucial to avoid damage and ensure optimal performance.
3. Aerospace Industry
The aerospace industry requires exceptionally high-quality welding due to the extreme conditions that aircraft components must withstand.
High-precision spot welding is used in manufacturing various aircraft parts, including structural components and engine parts.
This ensures that the parts are robust and can endure the high stresses encountered during flight.
4. Medical Devices
Medical devices often contain metal components that require precise and durable joining.
High-precision spot welding ensures that these devices are safe and reliable.
From surgical instruments to implants, the quality of welds in medical devices can directly impact patient safety and treatment effectiveness.
Technological Advancements in Spot Welding OEM
Innovation and technology play a pivotal role in enhancing the precision and efficiency of spot welding.
Let’s explore some of the technological advancements that are shaping the future of spot welding OEM.
1. Automation and Robotics
The integration of automation and robotics in spot welding has revolutionized the manufacturing process.
Automated spot welding systems offer unmatched precision and consistency.
Robots can perform repetitive tasks with high accuracy, ensuring that each weld is identical.
This not only enhances the quality but also speeds up the production process.
2. Laser Spot Welding
Laser spot welding is a relatively new technology that offers several advantages over traditional spot welding.
It provides more precise control over the welding parameters, resulting in cleaner and stronger welds.
Laser spot welding is particularly beneficial in industries where high precision is critical, such as electronics and aerospace.
3. Advanced Monitoring Systems
Modern spot welding systems are equipped with advanced monitoring technologies that can detect and correct any deviations in real time.
These systems ensure that each weld meets the required standards, thus maintaining high quality throughout the production process.
Such technology aids in reducing defects and enhancing the overall reliability of the welded parts.
Choosing the Right Spot Welding OEM
Selecting the right spot welding OEM is crucial for ensuring the quality and reliability of your products.
Here are some factors to consider when choosing an OEM for high-precision spot welding.
1. Industry Experience
Experience in your specific industry is an important consideration.
An OEM with a proven track record in your industry will understand the particular challenges and requirements, ensuring that they can meet your needs.
2. Quality Assurance
Look for an OEM that has robust quality assurance processes in place.
This includes certifications such as ISO standards, which indicate that the company adheres to high quality and process standards.
3. Technological Capabilities
Ensure that the OEM utilizes advanced technologies and equipment for spot welding.
This includes automation, robotics, and modern monitoring systems that enhance precision and efficiency.
4. Customization Options
Each project may have unique requirements.
Choose an OEM that offers customization options to tailor their services to fit your exact specifications.
In conclusion, high-precision spot welding is a critical process in many industries, providing durable, efficient, and high-quality joining parts.
As technology continues to advance, the capabilities of spot welding OEMs will only improve, offering even greater benefits to manufacturers and their clients.
By understanding the advantages and applications of high-precision spot welding, you can make informed decisions for your manufacturing needs.
資料ダウンロード
QCD調達購買管理クラウド「newji」は、調達購買部門で必要なQCD管理全てを備えた、現場特化型兼クラウド型の今世紀最高の購買管理システムとなります。
ユーザー登録
調達購買業務の効率化だけでなく、システムを導入することで、コスト削減や製品・資材のステータス可視化のほか、属人化していた購買情報の共有化による内部不正防止や統制にも役立ちます。
NEWJI DX
製造業に特化したデジタルトランスフォーメーション(DX)の実現を目指す請負開発型のコンサルティングサービスです。AI、iPaaS、および先端の技術を駆使して、製造プロセスの効率化、業務効率化、チームワーク強化、コスト削減、品質向上を実現します。このサービスは、製造業の課題を深く理解し、それに対する最適なデジタルソリューションを提供することで、企業が持続的な成長とイノベーションを達成できるようサポートします。
オンライン講座
製造業、主に購買・調達部門にお勤めの方々に向けた情報を配信しております。
新任の方やベテランの方、管理職を対象とした幅広いコンテンツをご用意しております。
お問い合わせ
コストダウンが利益に直結する術だと理解していても、なかなか前に進めることができない状況。そんな時は、newjiのコストダウン自動化機能で大きく利益貢献しよう!
(Β版非公開)