- お役立ち記事
- Providing Superior Sealing with Rubber Seals through OEM Manufacturing
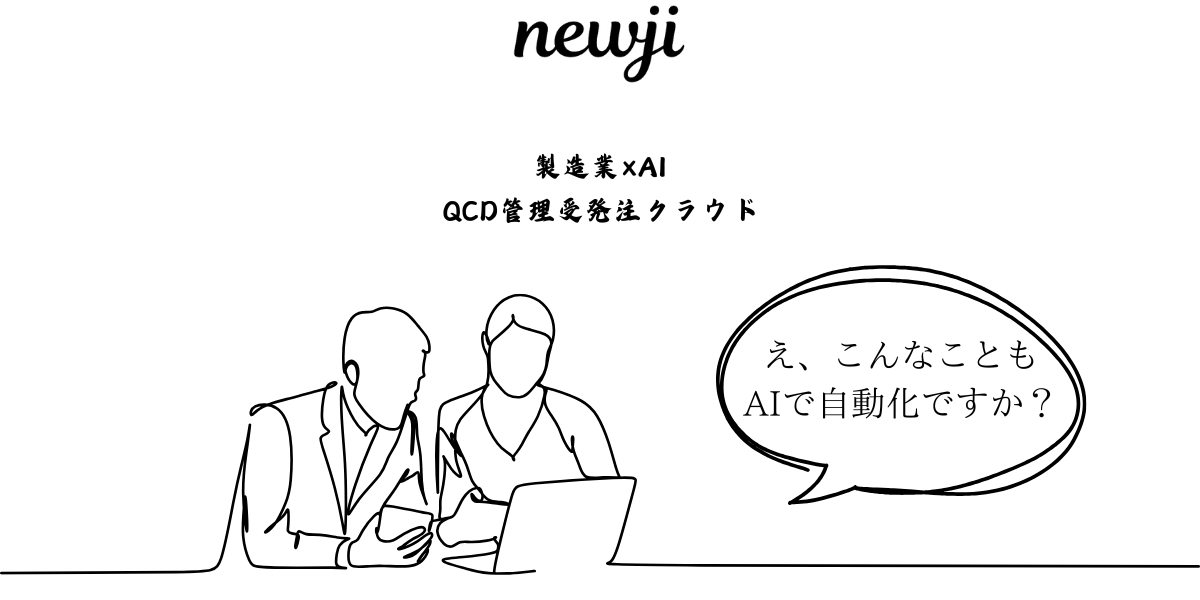
Providing Superior Sealing with Rubber Seals through OEM Manufacturing
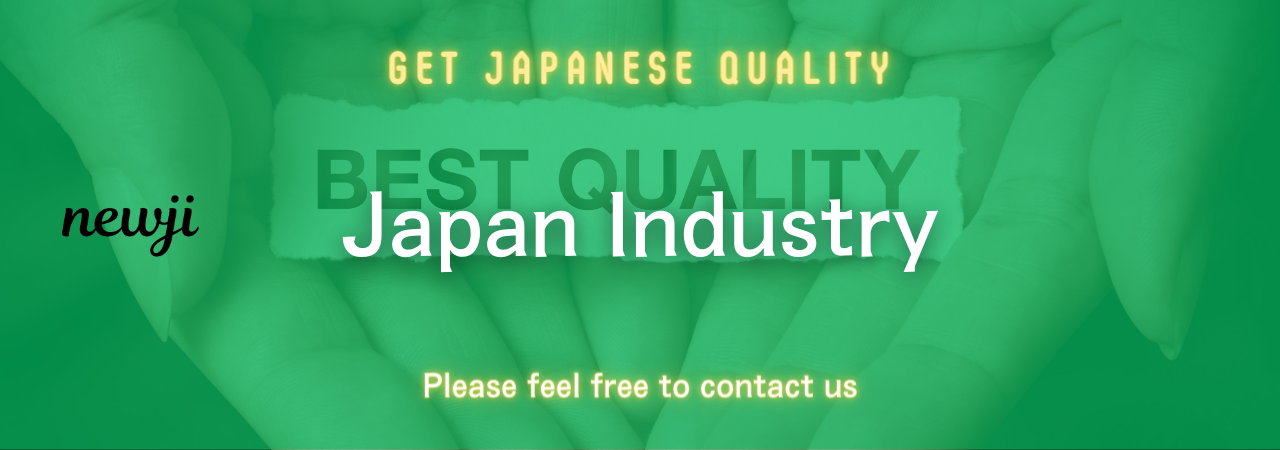
When it comes to keeping things sealed and secure, rubber seals play a crucial role in many industries.
From automotive to aerospace, rubber seals are essential for ensuring that components work correctly and efficiently.
Original Equipment Manufacturers (OEMs) are specialized in creating high-quality rubber seals tailored to specific applications.
目次
What is OEM Manufacturing?
OEM, or Original Equipment Manufacturing, refers to the process where a company produces parts or components that are used in another company’s end product.
In the context of rubber seals, OEM manufacturers design and produce seals that meet the precise specifications required by various industries.
The Importance of Customization
Different applications need different types of rubber seals.
For example, the seals required for automotive engines must withstand high temperatures and pressures.
In contrast, seals used in consumer electronics must be durable and flexible.
OEM manufacturers have the expertise to design custom seals that perfectly match these specific needs.
This customization ensures that the seals perform optimally, thereby enhancing the overall performance and lifespan of the final product.
High-Quality Materials for Superior Sealing
Quality materials are the foundation of effective rubber seals.
OEM manufacturers typically use a variety of high-performance materials to ensure durability and reliability.
Types of Rubber Compounds
Several types of rubber compounds are used in the manufacturing of seals, each with its unique properties:
– **Nitrile Rubber (NBR):** Excellent oil and fuel resistance, commonly used in automotive applications.
– **Silicone Rubber:** High flexibility and resistance to extreme temperatures, suitable for a wide range of industrial uses.
– **EPDM Rubber:** Great resistance to weather, ozone, and aging, often used in outdoor applications.
– **Fluorocarbon (Viton):** Exceptional chemical and heat resistance, ideal for aerospace and high-tech industries.
Choosing the right material is crucial.
OEM manufacturers have the knowledge to select and process these materials to create seals that meet stringent quality standards.
Advanced Manufacturing Techniques
To provide superior sealing, OEM manufacturers employ advanced manufacturing techniques.
These techniques ensure the precision and consistency required for high-quality seals.
Compression Molding
Compression molding is a widely used technique in rubber seal manufacturing.
In this process, raw rubber material is placed in a mold cavity.
The mold is then closed and heated, causing the rubber to soften and flow, filling the mold and forming the desired shape.
This method is particularly effective for producing large quantities of uniform seals.
Injection Molding
Injection molding involves injecting molten rubber material into a mold.
This technique allows for the production of highly intricate and complex shapes.
Injection molding is ideal for applications that demand tight tolerances and precise dimensions.
Extrusion
Extrusion is another common technique used in the production of rubber seals.
In this process, rubber material is forced through a die, forming a continuous shape such as tubing or a gasket.
Extruded seals are often used in applications requiring long and continuous sealing solutions.
Ensuring Quality and Reliability
Quality assurance is a critical aspect of OEM manufacturing.
Rigorous testing and inspection processes ensure that every seal meets or exceeds industry standards.
Testing for Durability
Rubber seals must endure various environmental conditions, including temperature fluctuations, pressure changes, and exposure to chemicals.
OEM manufacturers conduct extensive durability tests to ensure their seals can withstand these challenges.
These tests may include thermal cycling, chemical exposure, and mechanical stress tests.
Inspection for Precision
Precision is vital for rubber seals to function correctly.
OEM manufacturers employ advanced inspection techniques, such as laser scanning and coordinate measuring machines (CMM), to verify the dimensions and integrity of each seal.
This meticulous inspection process ensures that every seal fits perfectly and performs reliably.
The Benefits of High-Quality Rubber Seals
Using high-quality rubber seals from OEM manufacturers offers numerous benefits for end products and industries.
Enhanced Performance
Customized rubber seals improve the performance of the components they are employed in.
For example, in automotive engines, high-quality seals minimize oil and fuel leaks, ensuring efficient engine operation.
In industrial machinery, they prevent contamination and protect sensitive components, thereby boosting overall productivity.
Increased Durability
Rubber seals manufactured with premium materials and advanced techniques have a longer lifespan.
They can endure harsh conditions without degrading, resulting in fewer replacements and lower maintenance costs.
This increased durability translates to significant cost savings over time.
Safety and Compliance
In industries like aerospace and medical devices, safety is paramount.
OEM manufacturers adhere to strict industry standards and regulations, ensuring that their seals meet all necessary safety and compliance requirements.
Using these high-quality seals provides peace of mind and reduces the risk of equipment failure or accidents.
Conclusion
Rubber seals are a vital component in many industries, ensuring the efficient and reliable operation of various machines and devices.
OEM manufacturing offers the advantage of customization, high-quality materials, and advanced manufacturing techniques.
These factors combine to produce superior rubber seals that enhance performance, increase durability, and meet stringent safety standards.
When choosing rubber seals for your applications, partnering with a reputable OEM manufacturer ensures you receive the best possible sealing solutions tailored to your specific needs.
資料ダウンロード
QCD調達購買管理クラウド「newji」は、調達購買部門で必要なQCD管理全てを備えた、現場特化型兼クラウド型の今世紀最高の購買管理システムとなります。
ユーザー登録
調達購買業務の効率化だけでなく、システムを導入することで、コスト削減や製品・資材のステータス可視化のほか、属人化していた購買情報の共有化による内部不正防止や統制にも役立ちます。
NEWJI DX
製造業に特化したデジタルトランスフォーメーション(DX)の実現を目指す請負開発型のコンサルティングサービスです。AI、iPaaS、および先端の技術を駆使して、製造プロセスの効率化、業務効率化、チームワーク強化、コスト削減、品質向上を実現します。このサービスは、製造業の課題を深く理解し、それに対する最適なデジタルソリューションを提供することで、企業が持続的な成長とイノベーションを達成できるようサポートします。
オンライン講座
製造業、主に購買・調達部門にお勤めの方々に向けた情報を配信しております。
新任の方やベテランの方、管理職を対象とした幅広いコンテンツをご用意しております。
お問い合わせ
コストダウンが利益に直結する術だと理解していても、なかなか前に進めることができない状況。そんな時は、newjiのコストダウン自動化機能で大きく利益貢献しよう!
(Β版非公開)