- お役立ち記事
- Publishes a successful example of a rapid improvement process based on initial sample evaluation that can be achieved by the client on a low budget when requesting a prototype.
月間76,176名の
製造業ご担当者様が閲覧しています*
*2025年3月31日現在のGoogle Analyticsのデータより
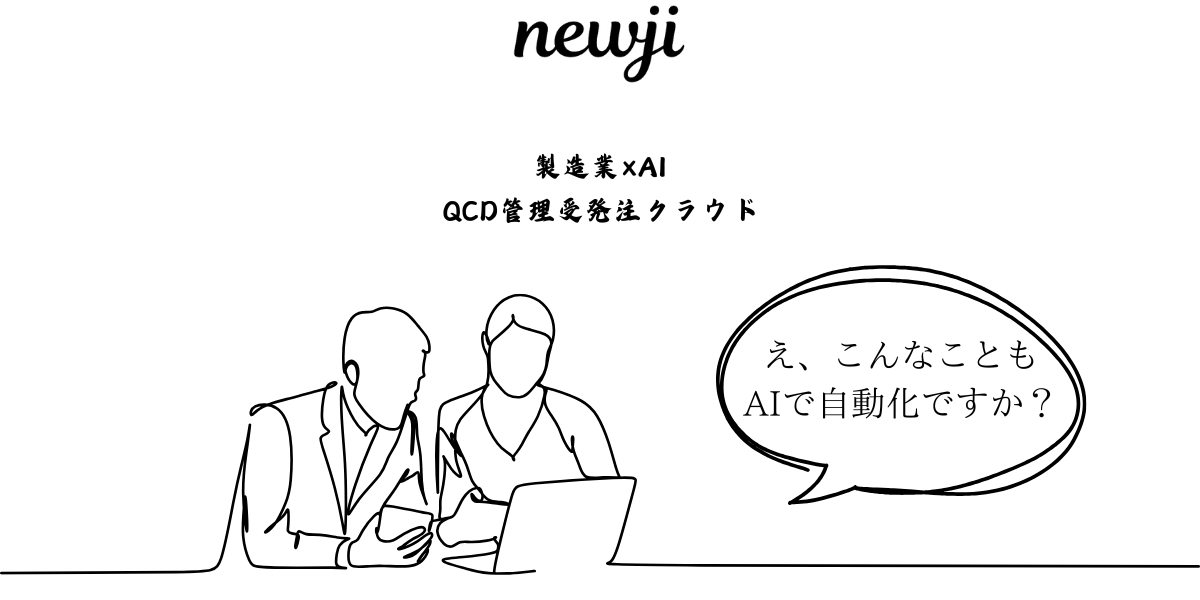
Publishes a successful example of a rapid improvement process based on initial sample evaluation that can be achieved by the client on a low budget when requesting a prototype.
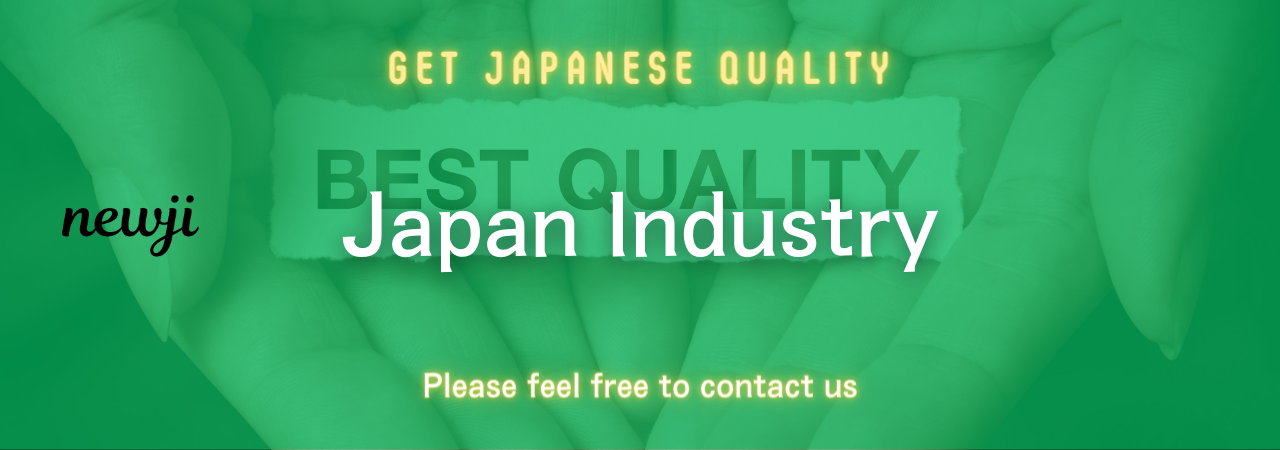
目次
Understanding the Rapid Improvement Process
The rapid improvement process is an approach that helps companies make quick and meaningful changes, especially when developing prototypes on a limited budget.
This process focuses on evaluating initial samples to identify potential improvements swiftly.
The goal is to create a cycle of continuous improvement that accelerates product development without incurring high costs.
Initial Sample Evaluation
Initial sample evaluation is a crucial step in the rapid improvement process.
This involves examining early prototypes to find strengths and areas for enhancement.
By conducting a thorough evaluation, companies can gather critical insights that inform the next stages of development.
Teams typically assess the prototype’s functionality, usability, and overall performance during this phase.
Feedback is collected from stakeholders to ensure that the prototype aligns with client expectations and project goals.
This feedback loop is vital in identifying issues early, making it easier to address them without expending additional resources.
Implementing Cost-Effective Strategies
Developing prototypes can often be expensive, particularly when multiple iterations are needed.
However, when utilizing rapid improvement techniques, it is possible to minimize expenses while maintaining quality.
One key strategy is prioritizing changes that promise the most impact with the least effort.
By focusing on high-value improvements, companies can optimally utilize their resources.
Moreover, leveraging existing technology and tools can help keep costs down.
Instead of developing new solutions from scratch, businesses often benefit from modifying existing platforms or integrating off-the-shelf components.
This not only reduces the overall cost but also shortens development time.
Successful Examples of Rapid Improvement
Several companies have successfully implemented the rapid improvement process with remarkable results.
For instance, a start-up company recently used this approach to develop a prototype for a new kitchen appliance.
By swiftly evaluating and iterating on their prototype, they were able to move from concept to a market-ready product in a matter of months.
The team utilized 3D printing technology to create initial samples, allowing them to make adjustments quickly and affordably.
Throughout the process, they engaged customers early, incorporating feedback from focus groups to refine their product.
This not only ensured that the final prototype met consumer needs but also allowed the company to address potential issues before they became costly problems.
Collaboration and Communication
Another critical factor in successful rapid improvement processes is effective collaboration and communication.
Involving a diverse team of experts from various fields can provide invaluable insights into the prototype’s development.
Each team member brings a unique perspective, which can lead to more innovative solutions and improvements.
Transparent communication within the team and with stakeholders ensures everyone is aligned on goals and progress.
Regular meetings and updates help keep the project on track and allow for real-time problem-solving when challenges arise.
Benefits of a Low-Budget Approach
Opting for a low-budget approach when creating prototypes is not just about saving money.
It encourages creativity and forces teams to think outside the box, often leading to more innovative solutions.
Additionally, it allows businesses to take more calculated risks since the stakes are lower.
With less financial pressure, companies can be more flexible and open to experimentation.
This environment fosters a positive culture of learning and adaptation where new ideas can be tested and iterated rapidly.
Adopting a Low-Budget Mindset
Adopting a low-budget mindset doesn’t mean compromising on quality.
Instead, it involves being resourceful and maximizing the value of every dollar spent.
For instance, organizing cross-functional workshops can generate a wealth of creative ideas without additional cost.
Incorporating customer feedback at every stage reduces the risk of expensive redesigns after the product is launched.
By working closely with users, companies ensure that the final product meets actual market needs, maximizing return on investment.
Conclusion
The rapid improvement process, using initial sample evaluations and a focus on cost-effectiveness, provides a viable path for businesses to develop prototypes efficiently.
With careful planning, a commitment to collaboration, and an openness to feedback, even companies with limited budgets can achieve impressive results.
When executed well, this process can lead to innovative products that meet market demands and drive business success.
資料ダウンロード
QCD管理受発注クラウド「newji」は、受発注部門で必要なQCD管理全てを備えた、現場特化型兼クラウド型の今世紀最高の受発注管理システムとなります。
ユーザー登録
受発注業務の効率化だけでなく、システムを導入することで、コスト削減や製品・資材のステータス可視化のほか、属人化していた受発注情報の共有化による内部不正防止や統制にも役立ちます。
NEWJI DX
製造業に特化したデジタルトランスフォーメーション(DX)の実現を目指す請負開発型のコンサルティングサービスです。AI、iPaaS、および先端の技術を駆使して、製造プロセスの効率化、業務効率化、チームワーク強化、コスト削減、品質向上を実現します。このサービスは、製造業の課題を深く理解し、それに対する最適なデジタルソリューションを提供することで、企業が持続的な成長とイノベーションを達成できるようサポートします。
製造業ニュース解説
製造業、主に購買・調達部門にお勤めの方々に向けた情報を配信しております。
新任の方やベテランの方、管理職を対象とした幅広いコンテンツをご用意しております。
お問い合わせ
コストダウンが利益に直結する術だと理解していても、なかなか前に進めることができない状況。そんな時は、newjiのコストダウン自動化機能で大きく利益貢献しよう!
(β版非公開)