- お役立ち記事
- Purchase Order (PO) Management for Production Planning Optimization in Manufacturing
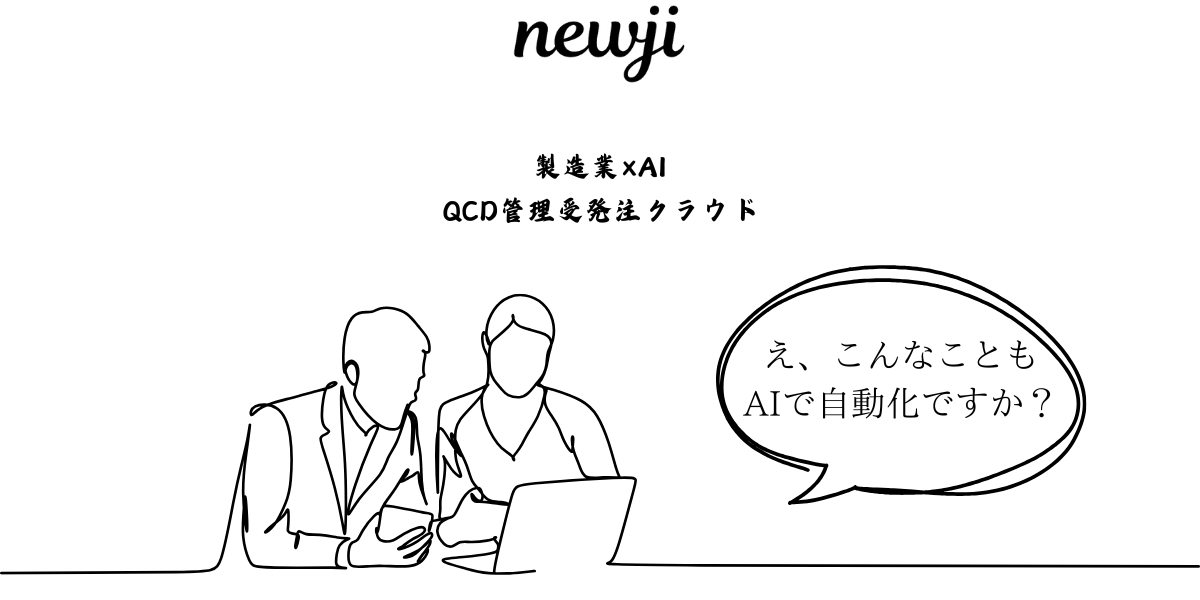
Purchase Order (PO) Management for Production Planning Optimization in Manufacturing
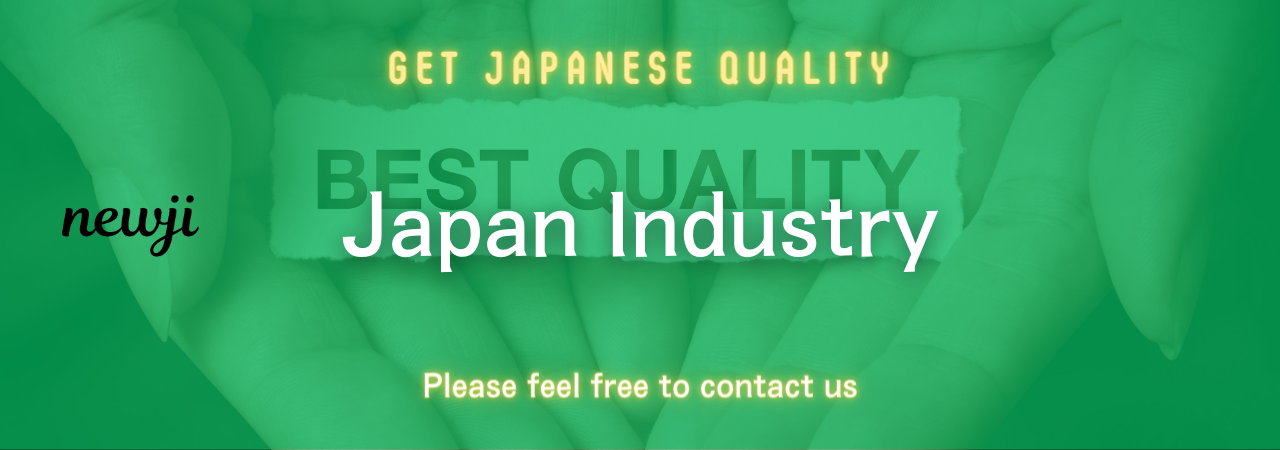
Efficient production planning is critical for the success of any manufacturing business.
One important element often overlooked is purchase order (PO) management.
When mastered, PO management can transform your production process, ensuring you meet deadlines and optimize resources.
This article will explore the importance of PO management and how to optimize it for better production planning in the manufacturing industry.
目次
Understanding Purchase Order Management
Purchase orders (POs) are formal documents issued by buyers to sellers, indicating the type, quantity, and agreed price for products or services.
Managing these orders efficiently is crucial for maintaining a seamless supply chain.
The Importance of POs in Manufacturing
Purchase orders serve multiple roles in manufacturing.
They act as a legal contract between the buyer and the seller.
They provide a clear record of what has been ordered, helping in inventory management and accounting.
POs also ensure that goods are received as per the agreed terms, thus maintaining the quality and consistency of raw materials used in production.
Common Challenges in PO Management
Despite their importance, PO management can present challenges:
1. **Delayed Deliveries**: Suppliers may fail to deliver on time, causing production delays.
2. **Quantity Discrepancies**: Received goods may not match the quantities ordered, leading to inventory imbalances.
3. **Quality Issues**: Poor quality of received goods can disrupt the production process.
4. **Communication Gaps**: Lack of clear communication between purchasing and manufacturing departments can affect production schedules.
Steps to Optimize PO Management
Effective PO management calls for strategic planning and the right tools.
Here are some steps to optimize your PO management system:
Streamline Your Ordering Process
A streamlined ordering process reduces the time and effort required for placing orders.
Automated systems can assist in generating POs quickly and accurately.
These systems can also track orders, ensuring that they are processed in a timely manner.
Set Clear Vendor Performance Metrics
Evaluating vendors based on their performance is essential.
Establish criteria such as delivery time, quality of goods, and accuracy in fulfilling orders.
Maintain a vendor scorecard to regularly assess each supplier.
This can help you identify reliable vendors and negotiate better terms.
Enhance Communication
Good communication between the purchasing and manufacturing departments is vital.
Implement regular meetings to discuss upcoming orders, potential delays, and inventory levels.
This real-time exchange of information ensures that everyone is on the same page.
Implement Inventory Management Systems
An inventory management system (IMS) can monitor stock levels in real-time.
With an IMS, you can predict when to place orders based on current inventory and production needs.
This reduces the risk of overstocking or running out of essential materials.
Use Just-In-Time (JIT) Inventory
Just-In-Time inventory management aligns raw material orders with production schedules.
Instead of maintaining large stockpiles, order materials just before they are needed.
This minimizes storage costs and reduces waste.
Regularly Review and Update Order Quantities
Regularly reviewing order quantities ensures that they align with current production needs.
Use historical data and sales forecasts to adjust quantities.
This prevents over-ordering or under-ordering, thus optimizing your inventory levels.
Leveraging Technology for Better PO Management
Modern technology offers various tools to simplify PO management.
Here’s how technology can assist:
Enterprise Resource Planning (ERP) Systems
ERP systems integrate all facets of your business operations, including PO management.
With an ERP, you can track orders, manage inventory, and analyze vendor performance all in one place.
This holistic view aids in making informed decisions.
Electronic Data Interchange (EDI)
EDI automates the exchange of business documents between you and your suppliers.
It speeds up the ordering process, reduces errors, and provides real-time order tracking.
This ensures that you receive your goods promptly and accurately.
Supply Chain Management Software
Supply chain management software offers tools specifically for managing POs.
Features such as automatic order generation, delivery tracking, and analytics make PO management more efficient.
This means less manual work and fewer chances of error.
Benefits of Optimized PO Management
Implementing a robust PO management system offers several benefits:
Improved Production Planning
Efficient PO management ensures that materials are available when needed.
This minimizes production delays, helping you meet deadlines and maintain consistent output.
Cost Savings
Streamlined ordering processes and JIT inventory systems reduce storage and holding costs.
Efficient vendor management can lead to better pricing and reduced expenditures.
Enhanced Vendor Relationships
Clear and consistent communication with vendors builds trust.
Reliable vendors are more likely to offer better terms and prioritize your orders.
Better Decision Making
With real-time data from ERP and inventory management systems, you can make informed decisions.
This leads to improved forecasting, better resource allocation, and strategic planning.
Conclusion
Optimizing purchase order management is essential for effective production planning in manufacturing.
From setting clear vendor performance metrics to leveraging technology, each step plays a vital role.
By integrating these strategies, you can streamline your production process, reduce costs, and build stronger vendor relationships.
Investing time and resources into optimizing PO management may seem daunting.
However, the long-term benefits make it a worthwhile endeavor for any manufacturing business.
Take the first step today towards a more efficient and reliable production planning system.
資料ダウンロード
QCD調達購買管理クラウド「newji」は、調達購買部門で必要なQCD管理全てを備えた、現場特化型兼クラウド型の今世紀最高の購買管理システムとなります。
ユーザー登録
調達購買業務の効率化だけでなく、システムを導入することで、コスト削減や製品・資材のステータス可視化のほか、属人化していた購買情報の共有化による内部不正防止や統制にも役立ちます。
NEWJI DX
製造業に特化したデジタルトランスフォーメーション(DX)の実現を目指す請負開発型のコンサルティングサービスです。AI、iPaaS、および先端の技術を駆使して、製造プロセスの効率化、業務効率化、チームワーク強化、コスト削減、品質向上を実現します。このサービスは、製造業の課題を深く理解し、それに対する最適なデジタルソリューションを提供することで、企業が持続的な成長とイノベーションを達成できるようサポートします。
オンライン講座
製造業、主に購買・調達部門にお勤めの方々に向けた情報を配信しております。
新任の方やベテランの方、管理職を対象とした幅広いコンテンツをご用意しております。
お問い合わせ
コストダウンが利益に直結する術だと理解していても、なかなか前に進めることができない状況。そんな時は、newjiのコストダウン自動化機能で大きく利益貢献しよう!
(Β版非公開)