- お役立ち記事
- Purchasing audit guidelines to check supplier quality control system
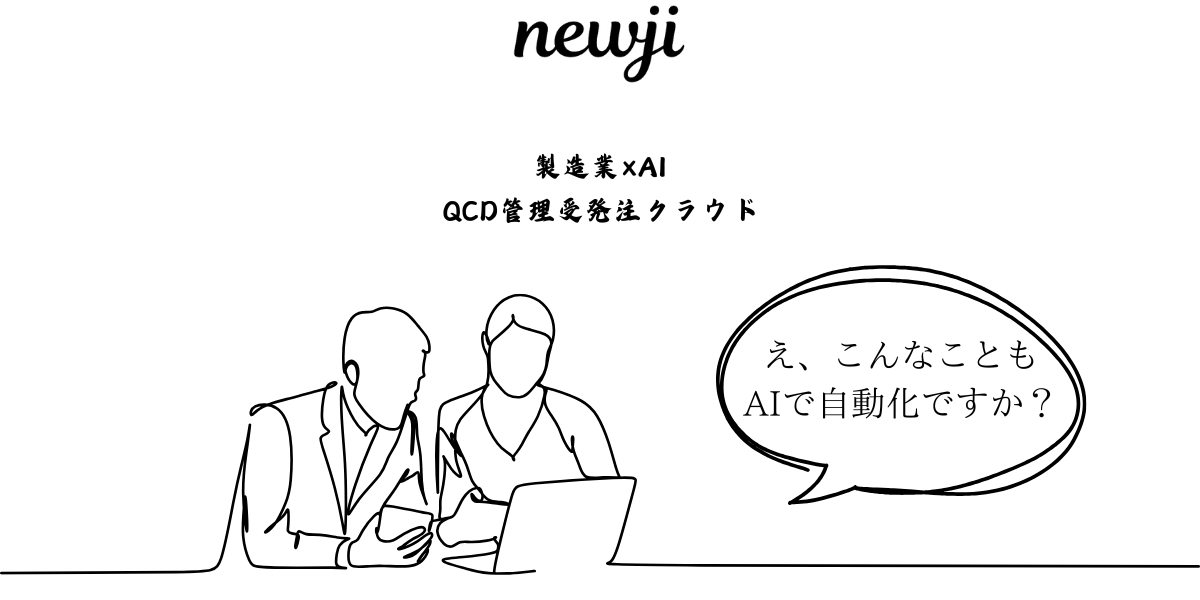
Purchasing audit guidelines to check supplier quality control system
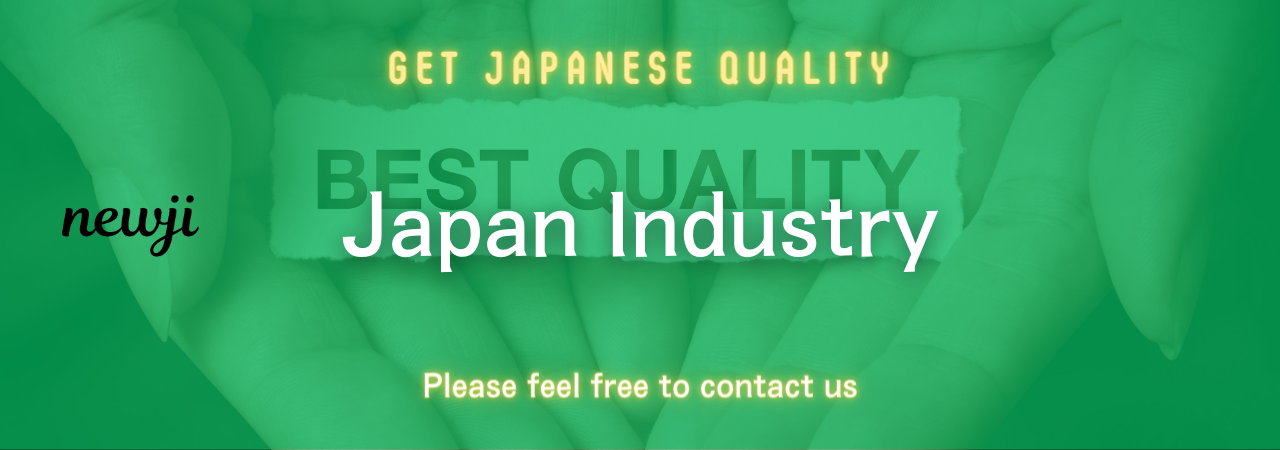
目次
Introduction to Purchasing Audit Guidelines
In the realm of procurement and supply chain management, ensuring the supplier’s quality control system is paramount.
A purchasing audit is a vital process that helps organizations evaluate the effectiveness and reliability of their suppliers.
The audit guidelines act as a framework to assess how well suppliers are maintaining quality standards.
Through this process, businesses can identify potential risks, improve supply chain reliability, and enhance overall product quality.
Understanding Supplier Quality Control Systems
Supplier quality control systems play a crucial role in maintaining the integrity of the products or services procured by a business.
These systems comprise various practices, methods, and procedures that suppliers use to ensure their outputs meet predetermined quality standards.
A robust quality control system can help prevent defects, minimize errors, and ensure consistency in the final product.
To assess supplier quality effectively, organizations need a structured approach.
Purchasing audit guidelines provide this structure, enabling auditors to systematically evaluate the various aspects of a supplier’s quality control system.
Components of a Quality Control System
When auditing a supplier’s quality control system, it is essential to examine certain key components.
These components include:
1. Quality Management Policies
Suppliers should have clear and detailed quality management policies in place.
These policies should outline their commitment to quality, the standards they adhere to, and the goals they aim to achieve through their quality control measures.
2. Process Documentation
Proper documentation of processes is vital for maintaining consistency and traceability.
Suppliers should provide detailed documentation of their production or service processes, including standard operating procedures (SOPs), quality checklists, and records of quality tests conducted.
3. Employee Training and Competence
Well-trained employees are crucial to the effectiveness of a quality control system.
During an audit, it is important to examine the training programs in place for employees, as well as their knowledge and competence in managing quality standards.
4. Supplier Evaluation and Selection
A supplier’s method for evaluating and selecting its own suppliers can provide insight into its overall quality management strategy.
Ensuring that suppliers have rigorous criteria and a structured evaluation process can enhance the reliability of their quality control system.
5. Inspection and Testing
Regular inspection and testing are fundamental practices within any quality control system.
Auditors should look into how frequently tests are conducted, the types of tests carried out, and how results are documented and addressed.
Benefits of Conducting Purchasing Audits
Conducting purchasing audits offers numerous benefits to companies seeking to optimize their supply chain management.
These benefits include:
1. Risk Mitigation
Audits help identify potential risks within a supplier’s quality control system, allowing organizations to take proactive measures to mitigate these risks.
By addressing issues early, companies can prevent costly defects and supply chain disruptions.
2. Supplier Performance Improvement
Purchasing audits offer suppliers constructive feedback on areas where they can enhance their quality control.
This feedback fosters a culture of continuous improvement, leading to better performance and stronger relationships between suppliers and buyers.
3. Enhanced Customer Satisfaction
Consistently high-quality products and services lead to increased customer satisfaction.
By ensuring that suppliers adhere to stringent quality control measures, companies can meet and exceed customer expectations.
4. Cost Savings
Improvements in supplier quality control can lead to reduced waste, fewer returns, and less rework, resulting in significant cost savings.
By enhancing efficiency and reliability, organizations can achieve better financial outcomes.
Implementing a Successful Purchasing Audit
To ensure the success of purchasing audits, several best practices should be followed:
1. Define Clear Objectives
Before conducting an audit, it is vital to establish clear objectives.
Determine what aspects of the supplier’s quality control system need to be assessed and what outcomes are desired from the audit process.
2. Develop a Comprehensive Checklist
Creating a detailed checklist of items to review during the audit helps maintain a focused and systematic approach.
The checklist should cover all critical components of the supplier’s quality control system.
3. Engage Qualified Auditors
Choosing auditors with expertise in quality management and supply chain processes is crucial.
Qualified auditors possess the skills needed to conduct thorough evaluations and offer actionable insights.
4. Foster Open Communication
Effective communication between the auditing team and the supplier fosters transparency and cooperation.
Open dialogue ensures that both parties understand the audit’s purpose, process, and expected outcomes.
5. Provide Constructive Feedback
Following the completion of the audit, providing detailed and constructive feedback to the supplier is essential.
Discussing findings, recommendations, and areas for improvement facilitates mutual understanding and collaboration.
Conclusion
Purchasing audits are indispensable tools for evaluating supplier quality control systems.
By following established guidelines and implementing best practices, organizations can ensure their suppliers meet high-quality standards.
This not only mitigates risks and enhances supplier performance but also drives customer satisfaction and cost savings.
Ultimately, a proactive approach to quality control auditing strengthens the overall supply chain, paving the way for sustained business success.
資料ダウンロード
QCD調達購買管理クラウド「newji」は、調達購買部門で必要なQCD管理全てを備えた、現場特化型兼クラウド型の今世紀最高の購買管理システムとなります。
ユーザー登録
調達購買業務の効率化だけでなく、システムを導入することで、コスト削減や製品・資材のステータス可視化のほか、属人化していた購買情報の共有化による内部不正防止や統制にも役立ちます。
NEWJI DX
製造業に特化したデジタルトランスフォーメーション(DX)の実現を目指す請負開発型のコンサルティングサービスです。AI、iPaaS、および先端の技術を駆使して、製造プロセスの効率化、業務効率化、チームワーク強化、コスト削減、品質向上を実現します。このサービスは、製造業の課題を深く理解し、それに対する最適なデジタルソリューションを提供することで、企業が持続的な成長とイノベーションを達成できるようサポートします。
オンライン講座
製造業、主に購買・調達部門にお勤めの方々に向けた情報を配信しております。
新任の方やベテランの方、管理職を対象とした幅広いコンテンツをご用意しております。
お問い合わせ
コストダウンが利益に直結する術だと理解していても、なかなか前に進めることができない状況。そんな時は、newjiのコストダウン自動化機能で大きく利益貢献しよう!
(Β版非公開)