- お役立ち記事
- Purchasing department audit and inspection methods to ensure quality standards of imported products
Purchasing department audit and inspection methods to ensure quality standards of imported products
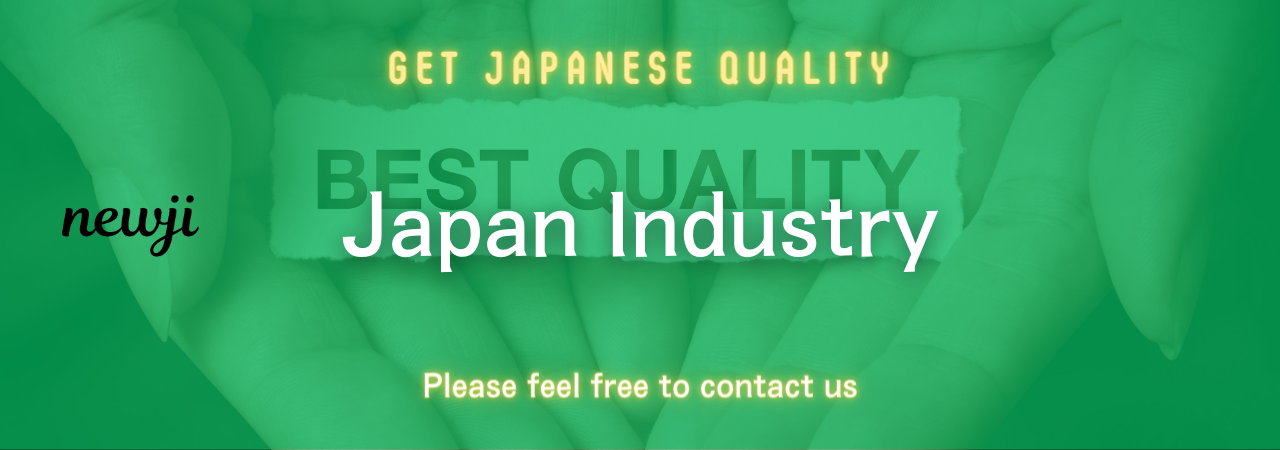
目次
Understanding the Role of the Purchasing Department
The purchasing department is a crucial component of any organization, particularly when it comes to maintaining the quality of imported products.
This department is responsible for sourcing, evaluating, and acquiring goods and services needed for business operations.
It plays a pivotal role in ensuring that the products procured meet specified quality standards.
Especially for imported items, where quality assurance can be more complex, the purchasing team’s efforts are integral to the company’s success.
The department not only seeks the best prices but also ensures that all purchases align with the company’s quality requirements and compliance standards, reducing the risk of defects and dissatisfaction.
The Importance of Audits in the Purchasing Process
Audits in the purchasing process serve as an essential tool to maintain and improve quality standards.
They offer a systematic examination of documents, performance, and procedures within the purchasing department.
Auditing helps identify areas where improvements can be made, ensuring that every action taken by the purchasing department aligns with the organizational objectives and quality standards.
Conducting regular audits helps maintain the consistency and reliability of imported products.
It allows a company to detect potential discrepancies early, reducing the risk of inferior quality products reaching the customers.
These audits also play a significant role in building trust with suppliers, as they demonstrate a commitment to maintaining high-quality standards.
Inspection Methods for Monitoring Quality
Several inspection methods are employed to ensure that imported goods meet the expected quality standards.
Some of the key methods include:
Pre-Production Inspection
This involves inspecting and verifying materials and components before the production process begins.
It ensures that the raw materials meet specific quality criteria, which in turn influences the overall quality of the final product.
The purchasing department works closely with suppliers to conduct these inspections, ensuring that any potential issues are addressed before production starts.
During Production Inspection
During production inspections take place while the manufacturing process is ongoing.
This method helps in monitoring and addressing any quality issues that may arise during production.
It involves inspecting the production facility and evaluating the manufacturing processes to ensure compliance with agreed quality standards.
The purchasing department leverages this method to ensure that any deviations are corrected promptly, preventing quality issues from escalating.
Pre-Shipment Inspection
Pre-shipment inspection involves a comprehensive assessment of finished products before they are shipped from the supplier’s facility.
This is a critical step in ensuring that the final product matches the quality specifications mentioned in the purchase order.
The purchasing department, often with the help of third-party inspection companies, conducts these inspections to verify product quality, quantity, packaging, and labeling.
Container Loading Inspection
This inspection is conducted during the container loading process.
It ensures that the goods are loaded correctly and securely to avoid any damage during transit.
The purchasing department oversees this process to ensure that the supplier adheres to the company’s shipping and packaging standards.
Using Quality Control Platforms
Many companies today integrate technology into their quality control processes through quality control platforms.
These platforms offer several advantages:
Real-Time Tracking
With quality control platforms, the purchasing department can track the inspection process in real-time.
This allows for immediate responses to any issues, minimizing the risk of delivering substandard products.
Comprehensive Reporting
Quality control platforms provide detailed reports on each inspection.
Having access to comprehensive documentation helps the purchasing department make informed decisions and facilitates better communication with suppliers.
These reports also serve as a valuable resource during audits.
Streamlined Communication
Using a centralized platform enhances communication between the purchasing department, suppliers, and inspectors.
This ensures that everyone is on the same page and reduces the likelihood of any miscommunications regarding quality expectations.
Selecting Reliable Suppliers
Selecting reliable suppliers is a fundamental step in ensuring the quality of imported products.
The purchasing department must perform due diligence when choosing suppliers, which involves evaluating their capabilities, quality control processes, and reputation in the market.
Supplier Evaluation Criteria
The evaluation criteria should include the supplier’s past performance, production capacity, financial stability, and compliance with international quality standards.
Building long-term relationships with trustworthy suppliers can significantly reduce the risk of quality issues.
Regular Supplier Audits
Conducting regular audits of supplier facilities helps maintain product quality.
These audits provide insights into the supplier’s working conditions, production processes, and adherence to quality standards.
They help identify potential risks and areas for improvement, ensuring that suppliers continue to meet the company’s expectations.
Conclusion
The purchasing department plays a vital role in ensuring the quality of imported products.
Through regular audits and inspections, as well as leveraging technology and selecting reliable suppliers, the department can maintain high standards and foster trust with consumers.
Implementing thorough audit and inspection processes is not only about preventing defects but also about protecting the company’s reputation and sustaining consumer confidence in its products.
By prioritizing quality control from start to finish, companies can ensure the delivery of top-quality products to their customers, thereby strengthening their market position and enhancing overall business success.
資料ダウンロード
QCD調達購買管理クラウド「newji」は、調達購買部門で必要なQCD管理全てを備えた、現場特化型兼クラウド型の今世紀最高の購買管理システムとなります。
ユーザー登録
調達購買業務の効率化だけでなく、システムを導入することで、コスト削減や製品・資材のステータス可視化のほか、属人化していた購買情報の共有化による内部不正防止や統制にも役立ちます。
NEWJI DX
製造業に特化したデジタルトランスフォーメーション(DX)の実現を目指す請負開発型のコンサルティングサービスです。AI、iPaaS、および先端の技術を駆使して、製造プロセスの効率化、業務効率化、チームワーク強化、コスト削減、品質向上を実現します。このサービスは、製造業の課題を深く理解し、それに対する最適なデジタルソリューションを提供することで、企業が持続的な成長とイノベーションを達成できるようサポートします。
オンライン講座
製造業、主に購買・調達部門にお勤めの方々に向けた情報を配信しております。
新任の方やベテランの方、管理職を対象とした幅広いコンテンツをご用意しております。
お問い合わせ
コストダウンが利益に直結する術だと理解していても、なかなか前に進めることができない状況。そんな時は、newjiのコストダウン自動化機能で大きく利益貢献しよう!
(Β版非公開)