- お役立ち記事
- Purchasing department challenges multiple supplier strategy to optimize manufacturing costs
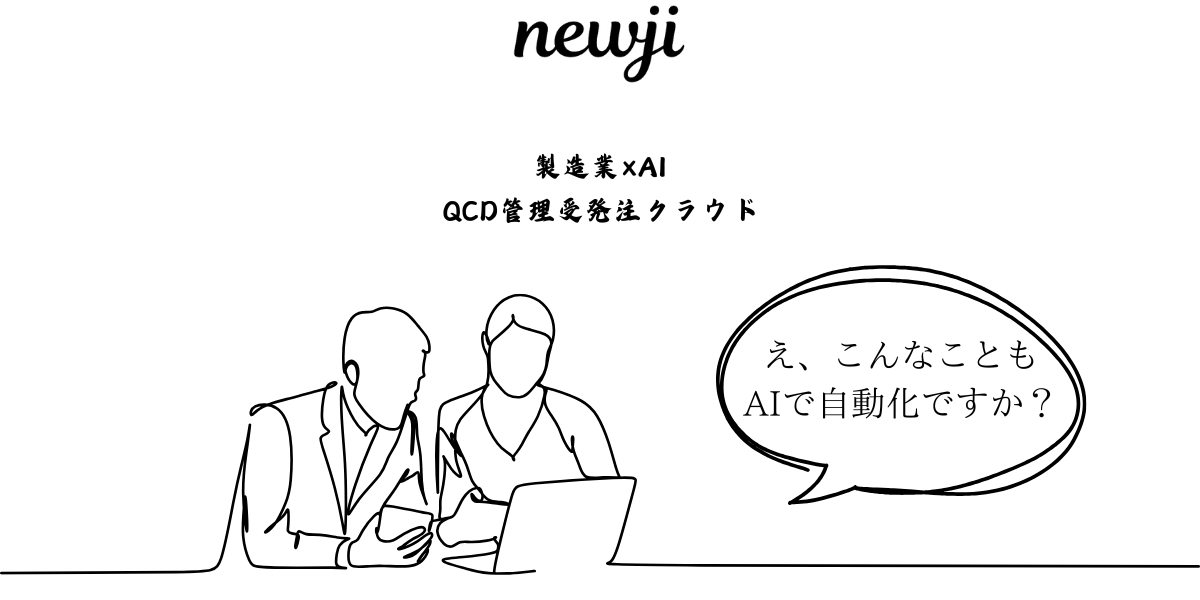
Purchasing department challenges multiple supplier strategy to optimize manufacturing costs
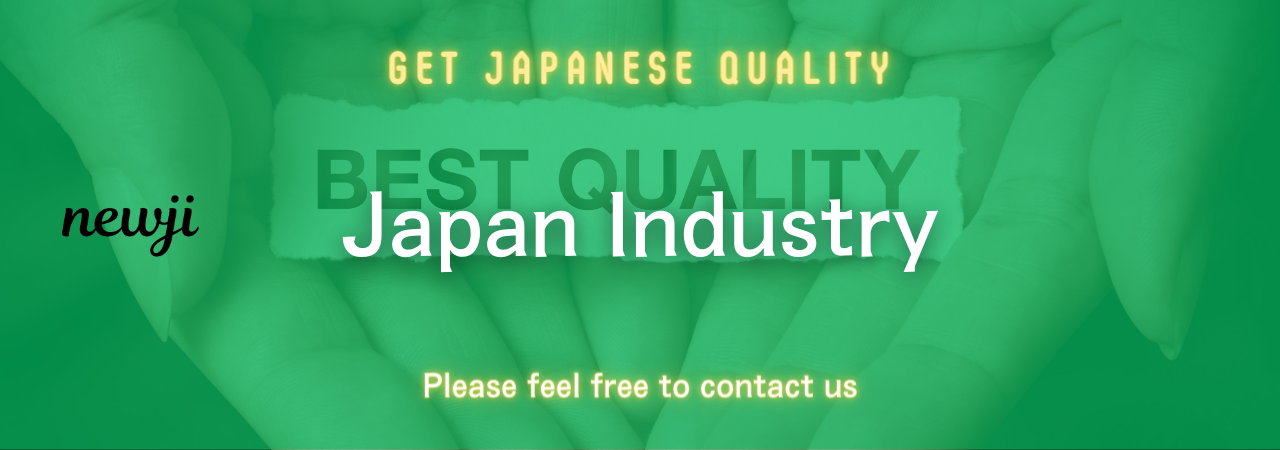
目次
Understanding the Challenges of a Multiple Supplier Strategy
A multiple supplier strategy, as the name suggests, involves sourcing materials and components from several suppliers rather than relying on a single source.
While this approach can offer numerous advantages, such as increased flexibility and reduced dependency on a single supplier, it also presents distinct challenges.
Understanding these challenges is crucial for a purchasing department aiming to optimize manufacturing costs effectively.
One of the primary challenges is managing supplier relationships efficiently.
With multiple suppliers, the purchasing department must maintain consistent communication and negotiate terms with each entity.
This can be time-consuming and might require additional resources to ensure that each supplier meets the company’s standards for quality and delivery timelines.
Additionally, the complexity of logistics increases with multiple suppliers.
Coordinating deliveries from various locations can lead to potential inefficiencies and increased transportation costs.
To counteract this, the purchasing department must implement robust supply chain management practices.
Furthermore, differing pricing models and contract terms can lead to financial complications.
With multiple suppliers, it becomes necessary to continually assess and compare pricing structures to ensure cost-effectiveness.
This requires sophisticated analytical tools and strategies to identify the most beneficial supplier arrangements.
Balancing Supplier Competition and Collaboration
Balancing competition and collaboration among suppliers is another significant challenge.
While having multiple suppliers can foster healthy competition, encouraging better pricing and service levels, it can also create conflicts of interest.
Suppliers may become less inclined to share valuable insights or collaborate on improvements if they perceive other suppliers as direct competitors.
To navigate this, purchasing departments often adopt a strategic approach that encourages collaboration where possible.
This might involve supplier development programs or incentives for suppliers who contribute innovative solutions to manufacturing challenges.
At the same time, maintaining a level of competition helps ensure that suppliers remain proactive and committed to delivering value.
Quality Control and Consistency Concerns
Ensuring consistent product quality is a crucial aspect of any manufacturing process.
With multiple suppliers, there is a heightened risk of variability in the quality of materials or components provided.
Each supplier may have different production processes, quality standards, and oversight mechanisms.
To mitigate these risks, the purchasing department must establish stringent quality control protocols.
This often involves regular audits, supplier assessments, and clearly defined quality expectations.
By setting these standards, companies can maintain the consistency necessary to produce high-quality products.
In addition, contingency plans should be put in place to handle instances where a supplier fails to meet quality expectations.
Having backup suppliers or alternative solutions can minimize disruptions to the manufacturing process and avoid costly delays.
Leveraging Technology for Effective Supplier Management
The challenges associated with a multiple supplier strategy can be significantly reduced through the use of advanced technologies.
Supply chain management software and procurement systems can streamline the process of managing supplier relationships and contracts.
These tools provide real-time insights into supplier performance, allowing the purchasing department to make data-driven decisions.
Moreover, technologies like artificial intelligence (AI) and machine learning (ML) can enhance forecasting and demand planning.
By predicting potential supply chain disruptions or shifts in demand, companies can proactively adjust their sourcing strategies.
This ensures that manufacturing costs remain optimized while minimizing the risks associated with supplier variability.
Developing a Comprehensive Supplier Evaluation System
Implementing a comprehensive supplier evaluation system is essential for companies employing a multiple supplier strategy.
This involves assessing suppliers based on various criteria, including quality, delivery, financial stability, and innovation capability.
Regular assessments help identify top-performing suppliers and those that may need improvement.
Having such a system in place enables purchasing departments to make informed decisions about supplier selection and retention.
It also provides the necessary feedback to suppliers, encouraging continuous improvement and alignment with the company’s goals.
Prioritizing Risk Management in Supplier Strategy
Risk management is a critical component of a multiple supplier strategy.
With multiple suppliers, there is an increased risk of supply disruptions due to factors such as geopolitical issues, natural disasters, or financial instability.
Developing a risk management plan involves identifying potential risks and implementing measures to mitigate them.
For instance, companies might diversify their supplier base by selecting suppliers from different geographical locations.
This geographical diversification reduces the risk of region-specific disruptions affecting the entire supply chain.
Additionally, maintaining strategic inventory levels can buffer against unforeseen supply interruptions.
The Role of Collaboration and Communication
Effective collaboration and communication are vital for the success of a multiple supplier strategy.
Establishing clear lines of communication between the purchasing department and suppliers can prevent misunderstandings and promote transparency.
Regular meetings, performance reviews, and open dialogues help foster strong relationships with suppliers.
Collaboration also extends to sharing forecasts and production plans with suppliers.
By aligning on future needs and expectations, companies can ensure that suppliers are prepared to meet their demands efficiently.
This proactive approach assists in maintaining a stable and cost-effective supply chain.
Conclusion: A Balancing Act
Implementing a multiple supplier strategy in the purchasing department is a complex yet rewarding endeavor.
By addressing key challenges such as supplier management, quality control, and risk mitigation, companies can optimize their manufacturing costs.
Leveraging technology and fostering collaboration further enhances the effectiveness of such a strategy.
Ultimately, the success of a multiple supplier strategy lies in carefully balancing competition and collaboration, consistently evaluating supplier performance, and embracing technology.
Through these efforts, the purchasing department can play a pivotal role in driving cost efficiency and ensuring the company’s competitive edge in the market.
資料ダウンロード
QCD調達購買管理クラウド「newji」は、調達購買部門で必要なQCD管理全てを備えた、現場特化型兼クラウド型の今世紀最高の購買管理システムとなります。
ユーザー登録
調達購買業務の効率化だけでなく、システムを導入することで、コスト削減や製品・資材のステータス可視化のほか、属人化していた購買情報の共有化による内部不正防止や統制にも役立ちます。
NEWJI DX
製造業に特化したデジタルトランスフォーメーション(DX)の実現を目指す請負開発型のコンサルティングサービスです。AI、iPaaS、および先端の技術を駆使して、製造プロセスの効率化、業務効率化、チームワーク強化、コスト削減、品質向上を実現します。このサービスは、製造業の課題を深く理解し、それに対する最適なデジタルソリューションを提供することで、企業が持続的な成長とイノベーションを達成できるようサポートします。
オンライン講座
製造業、主に購買・調達部門にお勤めの方々に向けた情報を配信しております。
新任の方やベテランの方、管理職を対象とした幅広いコンテンツをご用意しております。
お問い合わせ
コストダウンが利益に直結する術だと理解していても、なかなか前に進めることができない状況。そんな時は、newjiのコストダウン自動化機能で大きく利益貢献しよう!
(Β版非公開)