- お役立ち記事
- Purchasing department data integration strategy to ensure material supply reliability
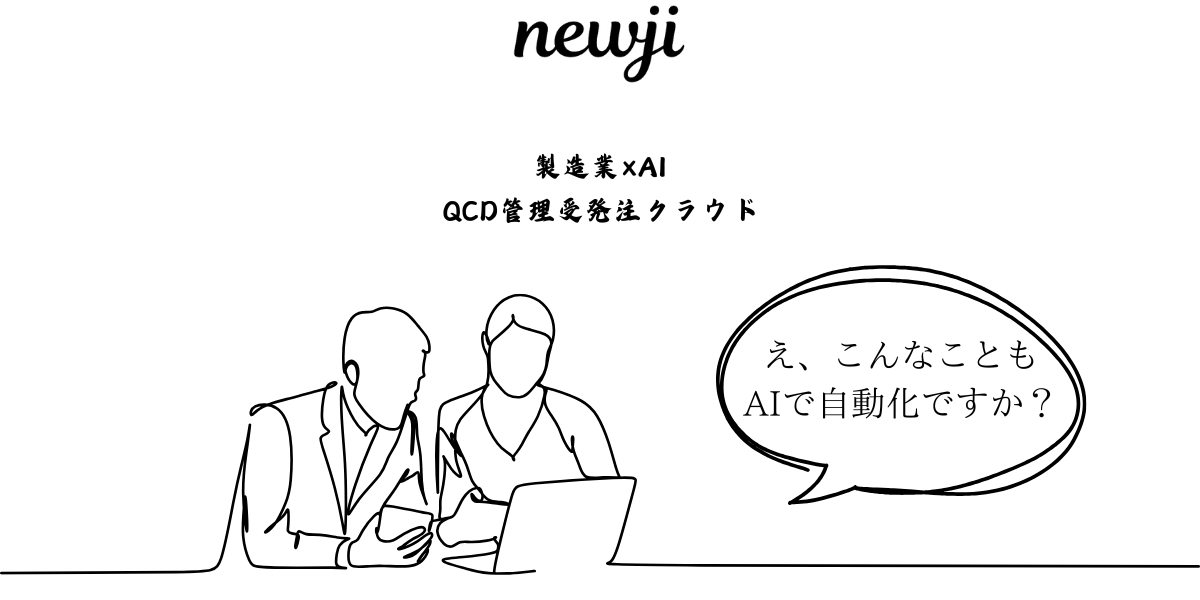
Purchasing department data integration strategy to ensure material supply reliability
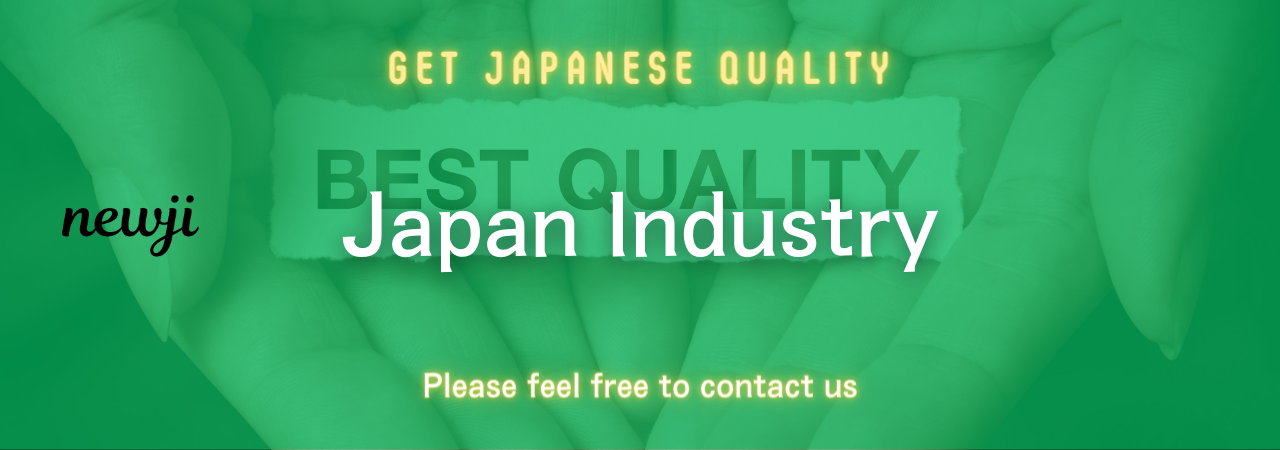
目次
Understanding the Importance of Data Integration
In today’s fast-paced business environment, the purchasing department plays a critical role in ensuring a company’s operations run smoothly.
One of the key responsibilities is to guarantee a reliable supply of materials necessary for production and services.
To achieve this, the integration of data across various systems is essential.
Data integration enables the purchasing department to have a comprehensive view of supply chain activities, vendor performance, and inventory levels.
Efficient data integration ensures that the right materials are available at the right time, minimizing delays and disruptions.
Why Data Integration Matters
Data integration combines information from different sources into a single, unified view.
For the purchasing department, this means consolidating data from suppliers, warehouses, production schedules, and market forecasts.
Without proper integration, supply chain data remains fragmented, leading to inefficiencies and increased risk of stockouts or overstocking.
Effective data integration provides timely insights that support decision-making, helping purchasing managers optimize procurement processes and enhance supply reliability.
Strategies for Successful Data Integration
For a purchasing department to successfully integrate data, several strategies can be implemented.
1. Adopt a Centralized Data Platform
Implementing a centralized data platform is a crucial step.
This platform should seamlessly connect with existing systems, such as ERP (Enterprise Resource Planning) and CRM (Customer Relationship Management), to consolidate data in one place.
A centralized platform allows for real-time data updates and ensures that all stakeholders access the same, accurate information.
2. Standardize Data Formats
Standardizing data formats across systems and vendors is necessary to facilitate easy integration.
By ensuring consistency in how data is formatted and categorized, the purchasing department can effectively combine and analyze information from multiple sources.
This standardization reduces errors and improves communication with vendors and other departments.
3. Use Data Integration Tools
There are various data integration tools available that can automate the process of combining data.
These tools offer features like data mapping, transformation, and cleansing to ensure that the integrated data is accurate and reliable.
Investing in these tools can save time and reduce the burden on IT resources, allowing the purchasing department to focus on strategic tasks.
4. Implement Strong Data Governance
Establishing strong data governance policies is essential to managing integrated data effectively.
This involves defining data ownership, access controls, and quality standards to ensure data integrity and security.
Data governance policies also involve regular audits and updates to maintain the reliability of the integrated data.
Pillars of Reliable Material Supply
To ensure the reliability of material supply, several key factors should be considered.
1. Comprehensive Supplier Management
A purchasing department must have a comprehensive supplier management strategy.
This includes assessing supplier performance, evaluating risks, and maintaining strong relationships.
With integrated data, purchasing managers can track vendor performance metrics and make informed decisions about which suppliers to prioritize.
2. Real-Time Inventory Monitoring
Real-time inventory monitoring allows the purchasing department to keep track of material levels and detect any potential shortages.
Through data integration, inventory data is continuously updated, enabling proactive responses to changes in demand or supply constraints.
This helps avoid production delays and ensures uninterrupted operations.
3. Demand Forecasting Accuracy
Accurate demand forecasting is vital to supply reliability.
By integrating data from sales, marketing, and supply chain systems, the purchasing department can predict future demand trends more accurately.
This allows for better planning and allocation of resources, ensuring materials are procured in the right quantities and at the right time.
Challenges in Data Integration
Despite its benefits, data integration poses certain challenges that the purchasing department must navigate.
1. Data Silos
Data silos occur when information is isolated within specific departments or systems, hindering effective integration.
Breaking down these silos requires collaboration across different functions and a commitment to sharing data for the greater benefit.
2. Data Security
Integrating data often raises concerns about security and privacy.
It is vital to implement robust security measures, such as encryption and access controls, to protect sensitive information from unauthorized access.
3. Resource Constraints
Integrating data can be resource-intensive, requiring significant time and financial investment.
To overcome this, a phased approach to data integration can be adopted, prioritizing the most critical data sources first.
Conclusion
An effective data integration strategy is crucial for the purchasing department to ensure material supply reliability.
By adopting centralized data platforms, standardizing data formats, using integration tools, and implementing strong governance policies, organizations can overcome the challenges of data integration.
It enables more informed decision-making, enhances supplier management, and improves demand forecasting accuracy.
With these strategies in place, companies can maintain seamless operations and a reliable supply of materials necessary for success.
資料ダウンロード
QCD調達購買管理クラウド「newji」は、調達購買部門で必要なQCD管理全てを備えた、現場特化型兼クラウド型の今世紀最高の購買管理システムとなります。
ユーザー登録
調達購買業務の効率化だけでなく、システムを導入することで、コスト削減や製品・資材のステータス可視化のほか、属人化していた購買情報の共有化による内部不正防止や統制にも役立ちます。
NEWJI DX
製造業に特化したデジタルトランスフォーメーション(DX)の実現を目指す請負開発型のコンサルティングサービスです。AI、iPaaS、および先端の技術を駆使して、製造プロセスの効率化、業務効率化、チームワーク強化、コスト削減、品質向上を実現します。このサービスは、製造業の課題を深く理解し、それに対する最適なデジタルソリューションを提供することで、企業が持続的な成長とイノベーションを達成できるようサポートします。
オンライン講座
製造業、主に購買・調達部門にお勤めの方々に向けた情報を配信しております。
新任の方やベテランの方、管理職を対象とした幅広いコンテンツをご用意しております。
お問い合わせ
コストダウンが利益に直結する術だと理解していても、なかなか前に進めることができない状況。そんな時は、newjiのコストダウン自動化機能で大きく利益貢献しよう!
(Β版非公開)