- お役立ち記事
- Purchasing department efficiency strategy aimed at improving productivity
月間77,185名の
製造業ご担当者様が閲覧しています*
*2025年2月28日現在のGoogle Analyticsのデータより
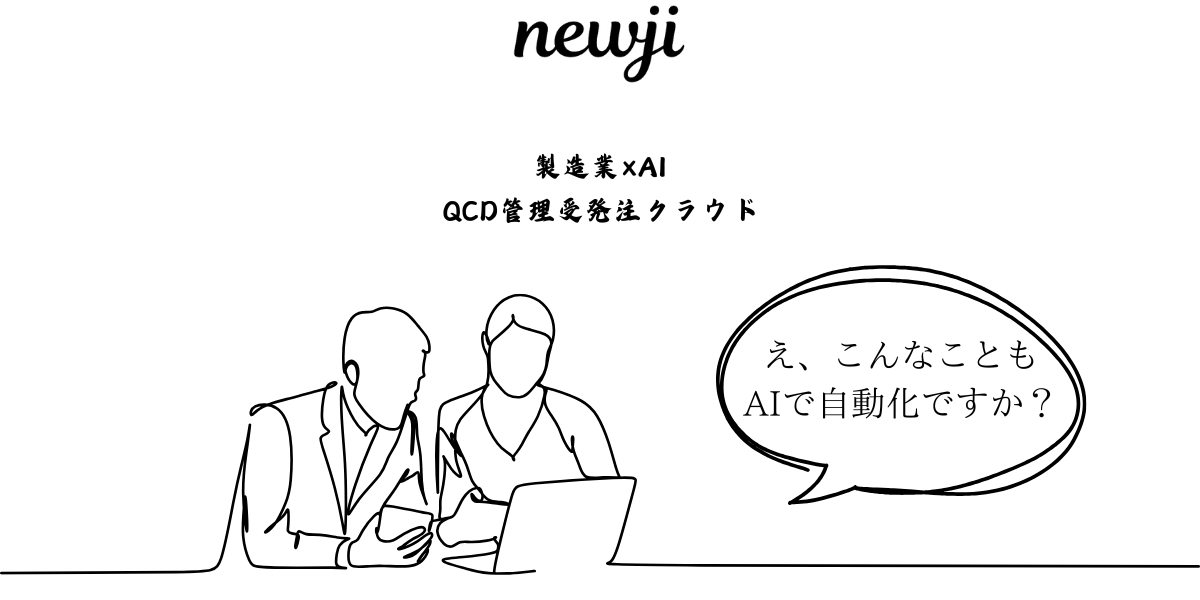
Purchasing department efficiency strategy aimed at improving productivity
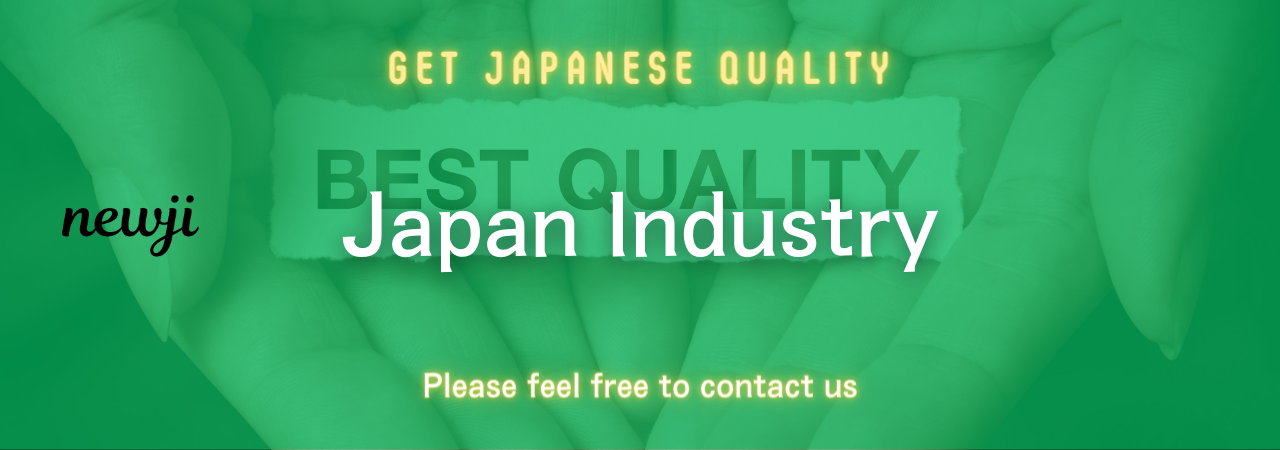
目次
Introduction to Purchasing Department Efficiency
Every company, regardless of its size, strives for efficiency and productivity.
In particular, the purchasing department plays a significant role in optimizing the overall operational success of a business.
This department is responsible for acquiring essential materials, supplies, and services that keep the company running smoothly.
Improving the efficiency of the purchasing department is more than just a matter of convenience.
It’s a vital strategy aimed at reducing costs, ensuring the timely delivery of materials, and enhancing the quality of the products or services offered by the company.
In this article, we’ll explore various strategies to boost the efficiency of your purchasing department.
Streamlining the Purchasing Process
A streamlined purchasing process can significantly improve productivity.
This step involves analyzing each stage of the purchasing cycle, identifying bottlenecks, and eliminating unnecessary steps.
Start by mapping out the current purchasing process, including requisition, approval, ordering, receiving, and payment.
One approach to streamline the process is automating repetitive tasks using procurement software.
Automation minimizes human errors, speeds up transaction times, and frees up human resources for more strategic activities.
The shift from manual paperwork to digital solutions ensures better tracking and traceability of orders.
Supplier Relationship Management
Building solid relationships with suppliers is crucial in enhancing purchasing department efficiency.
When buyers and suppliers develop mutual trust, communication becomes smoother, and potential issues can be resolved quickly.
Evaluate suppliers periodically to measure their performance regarding delivery time, quality of goods, and pricing.
Maintaining a shortlist of preferred vendors based on their reliability can simplify the purchasing decisions and negotiation processes.
A good practice is to involve suppliers in the company’s strategic planning, sharing forecasts and production schedules.
This allows suppliers to prepare and meet your production requirements effectively, reducing downtime and unexpected shortages.
Optimizing Inventory Management
Effective inventory management ensures that the right amount of stock is available at the right time.
An excess inventory ties up capital, while insufficient inventory can halt production.
Implementing a just-in-time inventory system can strike a balance by receiving goods only as they are needed for production.
Use inventory management software to track inventory levels in real-time, order histories, and lead times.
These insights help in making informed purchasing decisions, adjusting order quantities, and improving demand forecasting.
Cost Reduction Strategies
A major focus for any purchasing department is to reduce costs while maintaining quality.
Consistently assess and analyze spending patterns to identify potential areas for savings.
Negotiating better terms with suppliers or seeking alternative suppliers can lower the prices of goods and services.
Consider purchasing in bulk to avail of discounts, but ensure that it doesn’t lead to excessive inventory.
Additionally, fostering competition among suppliers can help in acquiring better deals and favorable terms.
Training and Development
Equipping your purchasing team with the right skills and knowledge can boost efficiency significantly.
Continuous training programs enable the team to stay updated with the latest industry trends, negotiation techniques, and procurement technologies.
Empower your team to make informed decisions by providing them with sufficient information about product specifications, market conditions, and supplier capabilities.
Encourage a culture of continuous learning and improvement, where team members share insights and learn from each other’s experiences.
Implementing Performance Metrics
Performance metrics are essential for measuring the efficiency of your purchasing department.
Establish clear key performance indicators (KPIs) such as cost savings, order accuracy, supplier lead times, and inventory turnover rates.
Regularly review these metrics to identify areas that require improvement.
Provide feedback to your team based on the data collected and set realistic targets to achieve better outcomes.
Use these metrics to align the purchasing department’s goals with the company’s broader objectives, creating a cohesive effort towards reaching strategic milestones.
Leveraging Technology and Data Analysis
The advancement of technology offers a plethora of tools to enhance purchasing efficiency.
Procuring software solutions like ERP systems can integrate purchasing with other business units, ensuring a seamless flow of information.
Data analysis plays a vital role in making informed purchasing decisions.
Use data analytics to understand trends, predict future demands, analyze supplier performance, and monitor spending patterns.
These insights lead to more strategic and effective procurement practices.
Risk Management in Procurement
Identifying and managing risks in procurement is essential for maintaining smooth operations.
Potential risks include supplier insolvency, price volatility, and supply chain disruptions.
Develop a risk management strategy that evaluates these risks and plans contingencies.
Diversify your supplier base to reduce reliance on a single source, conduct regular supplier audits, and maintain open communication to anticipate and mitigate risks.
Conclusion
Improving the efficiency of the purchasing department involves a combination of strategy, technology, and people management.
By focusing on streamlining processes, managing supplier relationships, optimizing inventory, and leveraging technology, companies can enhance productivity and drive cost savings.
Remember, the purchasing department is integral to the company’s success, and investing in its efficiency is essential for achieving long-term strategic objectives.
Implement these strategies to see significant improvements in your purchasing operations and overall business performance.
資料ダウンロード
QCD管理受発注クラウド「newji」は、受発注部門で必要なQCD管理全てを備えた、現場特化型兼クラウド型の今世紀最高の受発注管理システムとなります。
ユーザー登録
受発注業務の効率化だけでなく、システムを導入することで、コスト削減や製品・資材のステータス可視化のほか、属人化していた受発注情報の共有化による内部不正防止や統制にも役立ちます。
NEWJI DX
製造業に特化したデジタルトランスフォーメーション(DX)の実現を目指す請負開発型のコンサルティングサービスです。AI、iPaaS、および先端の技術を駆使して、製造プロセスの効率化、業務効率化、チームワーク強化、コスト削減、品質向上を実現します。このサービスは、製造業の課題を深く理解し、それに対する最適なデジタルソリューションを提供することで、企業が持続的な成長とイノベーションを達成できるようサポートします。
製造業ニュース解説
製造業、主に購買・調達部門にお勤めの方々に向けた情報を配信しております。
新任の方やベテランの方、管理職を対象とした幅広いコンテンツをご用意しております。
お問い合わせ
コストダウンが利益に直結する術だと理解していても、なかなか前に進めることができない状況。そんな時は、newjiのコストダウン自動化機能で大きく利益貢献しよう!
(β版非公開)