- お役立ち記事
- Purchasing department initiatives to support improved traceability throughout the supply chain
Purchasing department initiatives to support improved traceability throughout the supply chain
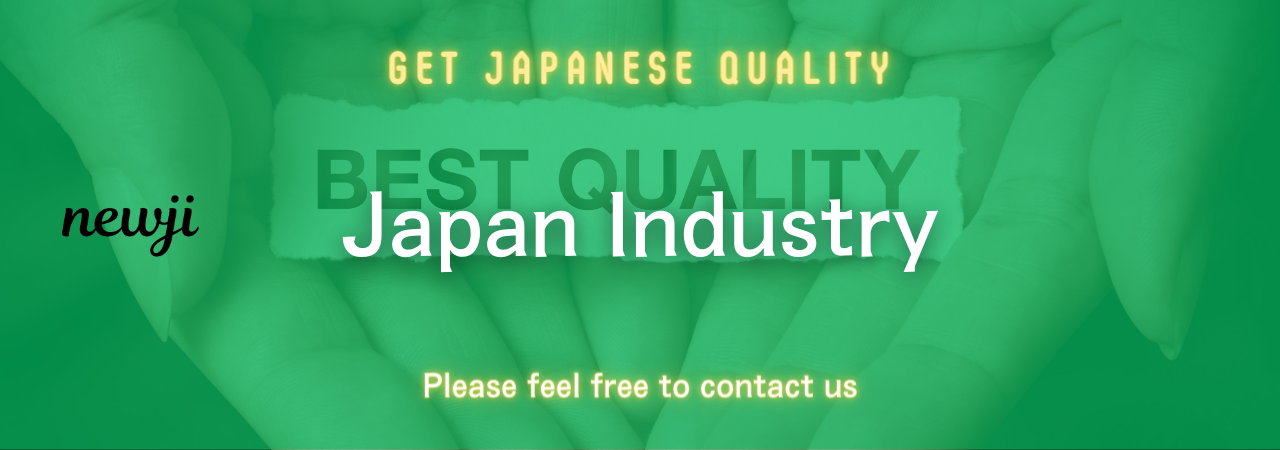
目次
Understanding Traceability in the Supply Chain
Traceability in the supply chain refers to the capability to track all processes from acquisition of raw materials to production, and from distribution to reaching the end consumer.
This aspect of supply chain management has gained significant importance due to increasing consumer awareness and regulatory requirements.
Having robust traceability helps in ensuring product quality, managing recalls, and sustaining overall transparency.
To support traceability, organizations often have departments dedicated to managing and enhancing these processes.
One such key player in this initiative is the purchasing department.
The purchasing department’s role can be pivotal in enhancing traceability across the supply chain.
The Role of the Purchasing Department
Traditionally, the purchasing department focuses on acquiring goods and services required for production at the best possible cost without compromising on quality.
However, their responsibilities have expanded in recent years.
They now play an integral role in ensuring that goods sourced are easily traceable throughout the supply chain.
Here’s how the purchasing department helps improve traceability:
Supplier Selection and Evaluation
The purchasing department is responsible for selecting suppliers genuinely committed to traceability.
This requires thorough vetting and consistent evaluation of suppliers’ capabilities.
The department must ensure that suppliers keep accurate records of their own processes and provide necessary documentation efficiently.
They need to consider suppliers with proven track records and an openness to adopt new traceability technologies.
Sourcing Strategy
Developing a sourcing strategy involves identifying the best sources for materials and products, considering not only cost and quality but also traceability.
The purchasing team should work closely with suppliers who use advanced tracking systems such as RFID or blockchain.
This ensures real-time visibility and an unbroken chain of custody for the materials procured.
Quality Assurance
The department ensures that procured goods meet the required standards.
Working with suppliers to ensure that the production process is transparent and that records are easily accessible is crucial.
By doing so, they help maintain an unbroken chain of traceability, which is vital in case of quality assurance audits or product recalls.
Implementing Technology
To support traceability efforts, purchasing departments often collaborate with IT and supply chain management teams to implement cutting-edge technologies.
These technologies could include electronic records management systems, real-time data tracking software, and automated reporting tools.
These systems allow for seamless tracking of goods from point of origin to delivery.
Benefits of Improved Traceability
Enhancing traceability in the supply chain offers numerous benefits that extend beyond compliance with regulations:
Risk Management
One of the most significant advantages of improved traceability is the ability to manage risks effectively.
By understanding the journey of a product through the supply chain, companies can identify potential areas of concern and mitigate them swiftly before they escalate into larger issues.
This proactive approach helps in identifying, tracking, and resolving problems effectively.
Product Recall Efficiency
In the unfortunate event of a product recall, traceability ensures that the process is swift and accurate.
With complete visibility into the supply chain, companies can pinpoint affected batches easily, isolating only those that require recall.
This helps in minimizing the financial and reputational damage associated with recalls.
Building Consumer Trust
Today’s consumers are more informed and demand transparency about the products they purchase.
By ensuring traceable supply chains, companies can provide products with verified origins, enhancing trust and loyalty among consumers.
This transparency ensures consumers confidently support brands that prioritize safety and responsibility.
Challenges in Implementing Traceability
While the benefits are substantial, implementing an effective traceability system is not without challenges:
Complexity of Supply Chains
Modern supply chains are global and complex, involving multiple parties across different regions.
Ensuring complete traceability across all these nodes requires coordinated effort, robust systems, and continuous monitoring.
It can be challenging to align all stakeholders toward common traceability goals.
Investment in Technology
Establishing and maintaining state-of-the-art traceability systems requires significant investment upfront.
Some organizations may find this investment daunting, especially if they lack the necessary resources or expertise.
Long-term benefits should be considered to offset initial setup costs.
Regulatory Variability
With different regulatory requirements across regions, keeping track of and compliance with these varying regulations can be complex.
The purchasing department must remain informed and ensure that all suppliers meet the necessary regional and international standards.
Conclusion
The purchasing department’s role in supporting improved traceability throughout the supply chain is crucial.
By carefully selecting suppliers, implementing advanced technology, and maintaining stringent quality standards, purchasing teams can significantly enhance the transparency and efficiency of supply chains.
Despite challenges, the benefits of robust traceability systems highlight an undeniable advantage in risk management, consumer trust, and operational excellence.
Companies that prioritize traceability initiatives will be well-positioned to meet the growing demand for transparency and accountability in today’s market.
資料ダウンロード
QCD調達購買管理クラウド「newji」は、調達購買部門で必要なQCD管理全てを備えた、現場特化型兼クラウド型の今世紀最高の購買管理システムとなります。
ユーザー登録
調達購買業務の効率化だけでなく、システムを導入することで、コスト削減や製品・資材のステータス可視化のほか、属人化していた購買情報の共有化による内部不正防止や統制にも役立ちます。
NEWJI DX
製造業に特化したデジタルトランスフォーメーション(DX)の実現を目指す請負開発型のコンサルティングサービスです。AI、iPaaS、および先端の技術を駆使して、製造プロセスの効率化、業務効率化、チームワーク強化、コスト削減、品質向上を実現します。このサービスは、製造業の課題を深く理解し、それに対する最適なデジタルソリューションを提供することで、企業が持続的な成長とイノベーションを達成できるようサポートします。
オンライン講座
製造業、主に購買・調達部門にお勤めの方々に向けた情報を配信しております。
新任の方やベテランの方、管理職を対象とした幅広いコンテンツをご用意しております。
お問い合わせ
コストダウンが利益に直結する術だと理解していても、なかなか前に進めることができない状況。そんな時は、newjiのコストダウン自動化機能で大きく利益貢献しよう!
(Β版非公開)