- お役立ち記事
- Purchasing department standardization process to ensure procurement quality in the global market
月間76,176名の
製造業ご担当者様が閲覧しています*
*2025年3月31日現在のGoogle Analyticsのデータより
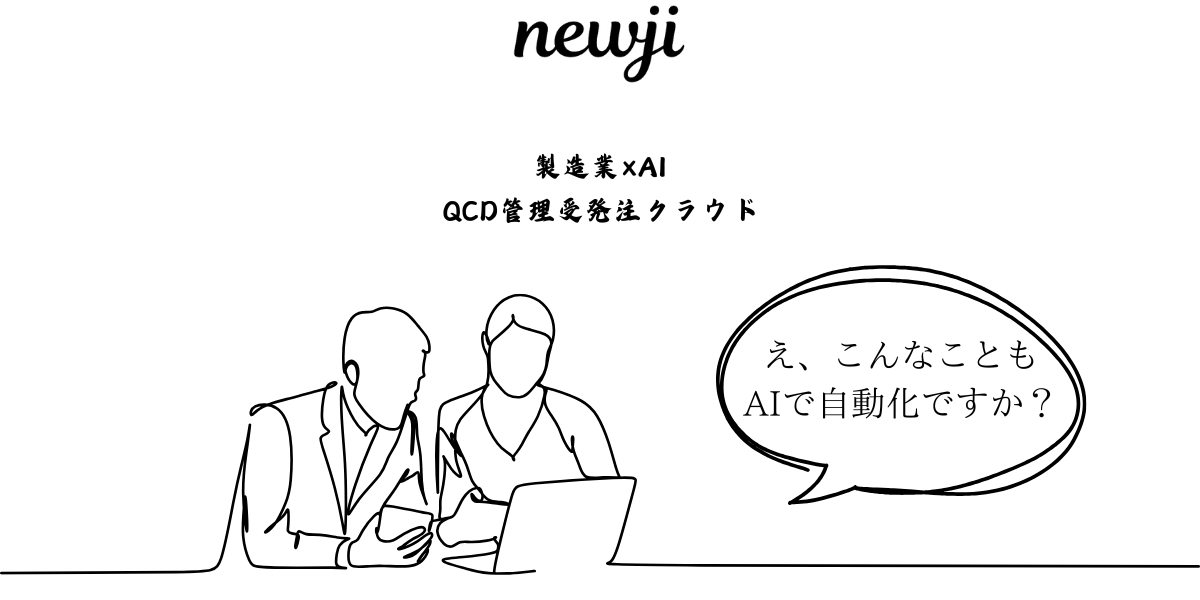
Purchasing department standardization process to ensure procurement quality in the global market
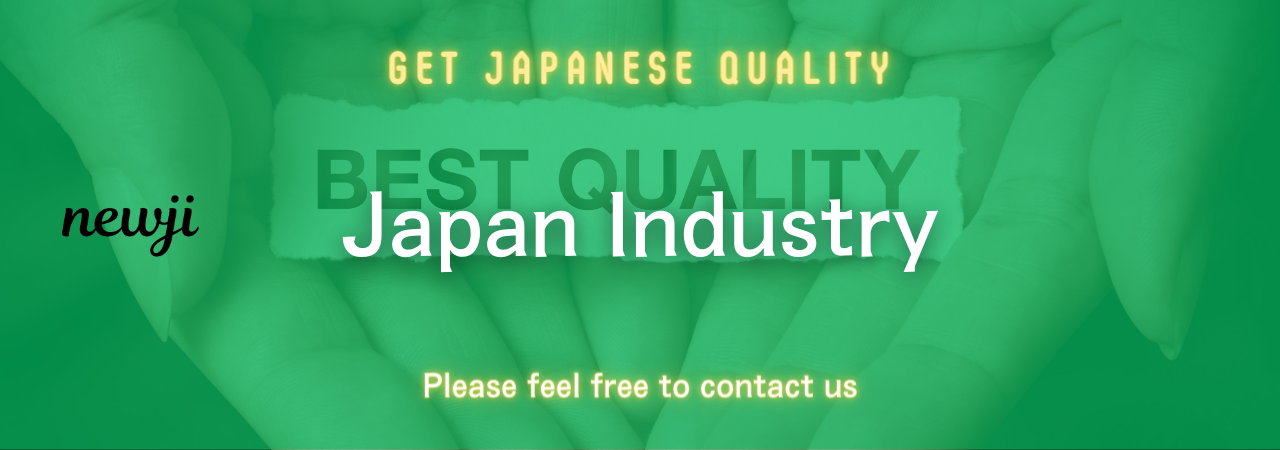
The global market is an ever-evolving landscape, with businesses constantly striving to innovate and stay competitive. Amidst this dynamic environment, the purchasing department plays a crucial role in ensuring the procurement quality necessary for business success. However, achieving consistency and excellence in procurement requires a well-defined standardization process. This article explores the essential steps in standardizing purchasing department processes to ensure procurement quality across the globe.
目次
Understanding the Importance of Standardization
Standardization refers to the implementation of consistent procedures and criteria to achieve uniform quality and efficiency in processes. In the context of procurement, standardization helps maintain the quality of goods and services, reduces costs, minimizes risks, and enhances supplier relationships. It ensures that the purchasing department operates efficiently, no matter the geographic location.
Benefits of Standardized Procurement Processes
Standardization offers several advantages, including:
- Consistency: By implementing standardized procedures, businesses ensure consistent quality, regardless of the supplier’s location.
- Efficiency: Standardized processes streamline operations, reducing time and resources spent on procurement tasks.
- Risk Management: By adhering to standardized practices, companies can better manage risks associated with supplier performance and compliance.
- Improved Supplier Relationships: Clear and consistent procurement processes enhance communication and foster strong relationships with suppliers.
- Cost Reduction: By avoiding process redundancies and leveraging standardized procedures, companies can reduce procurement costs.
The Process of Standardizing Procurement
Step 1: Assess Current Processes
The journey to standardization begins with an in-depth assessment of existing procurement processes. This involves identifying strengths, weaknesses, and variances in current practices across different regions and departments. Engaging with key stakeholders and gathering feedback from employees are vital in understanding current challenges and identifying areas for improvement.
Step 2: Define Clear Objectives
Once a comprehensive assessment is complete, the next step is to establish clear objectives for the standardization process. Consider the overarching goals that need to be achieved, such as improved efficiency, cost savings, or enhanced supplier relationships. Clear objectives provide direction and help align the efforts of the entire purchasing department.
Step 3: Develop Standardized Procedures
Developing standardized procedures involves creating a set of guidelines and best practices for each stage of the procurement process. This may include supplier evaluation criteria, purchasing workflows, and compliance requirements. Document detailed guidelines and make them accessible to all relevant stakeholders to ensure consistent application.
Step 4: Implement Training Programs
To effectively implement standardized procedures, provide comprehensive training programs for employees. These programs should focus on educating staff about the new processes, highlighting their importance, and demonstrating their implementation. Through training, employees can gain the knowledge and skills necessary to adhere to standardized practices.
Step 5: Utilize Technology
Technology plays a vital role in simplifying and standardizing procurement processes. Implement procurement software solutions to streamline operations, improve visibility, and enhance data accuracy. Automated systems facilitate better communication between departments, reduce manual errors, and ensure the consistent application of standardized procedures.
Step 6: Monitor and Evaluate Performance
Regularly monitor and evaluate the performance of standardized procurement processes. Collect feedback, analyze performance data, and identify areas that require refinement. Continual evaluation allows purchasing departments to identify emerging challenges and make necessary adjustments to enhance procurement quality further.
Ensuring Global Compliance
Adapting to Local Regulations
In an international context, compliance with local regulations is paramount. The purchasing department must adapt standardized processes to align with regional laws and regulations. This may involve understanding cultural nuances, trade regulations, and industry-specific requirements. Ensuring global compliance safeguards businesses from legal issues and enhances international relationships.
Building Collaborations and Partnerships
Standardization efforts are strengthened by building strong collaborations and partnerships with suppliers, vendors, and other relevant stakeholders. Establishing mutually beneficial relationships fosters trust, open communication, and cooperation. Collaborations can lead to innovative solutions, improved procurement quality, and increased value for both businesses and their suppliers.
Moreover, partnerships enable organizations to gain insights into local markets and minimize risks associated with international operations.
Conclusion
Standardizing the purchasing department’s processes is a strategic move in ensuring procurement quality in the global market. By assessing current practices, defining clear objectives, developing standardized procedures, and leveraging technology, businesses can achieve consistency, efficiency, and compliance across their procurement operations.
Ultimately, the standardization process not only improves procurement quality but also enhances cost-effectiveness, reduces risks, and cultivates robust supplier relationships. As organizations navigate the complexities of international markets, having a standardized approach to procurement is essential for sustained success and growth.
資料ダウンロード
QCD管理受発注クラウド「newji」は、受発注部門で必要なQCD管理全てを備えた、現場特化型兼クラウド型の今世紀最高の受発注管理システムとなります。
ユーザー登録
受発注業務の効率化だけでなく、システムを導入することで、コスト削減や製品・資材のステータス可視化のほか、属人化していた受発注情報の共有化による内部不正防止や統制にも役立ちます。
NEWJI DX
製造業に特化したデジタルトランスフォーメーション(DX)の実現を目指す請負開発型のコンサルティングサービスです。AI、iPaaS、および先端の技術を駆使して、製造プロセスの効率化、業務効率化、チームワーク強化、コスト削減、品質向上を実現します。このサービスは、製造業の課題を深く理解し、それに対する最適なデジタルソリューションを提供することで、企業が持続的な成長とイノベーションを達成できるようサポートします。
製造業ニュース解説
製造業、主に購買・調達部門にお勤めの方々に向けた情報を配信しております。
新任の方やベテランの方、管理職を対象とした幅広いコンテンツをご用意しております。
お問い合わせ
コストダウンが利益に直結する術だと理解していても、なかなか前に進めることができない状況。そんな時は、newjiのコストダウン自動化機能で大きく利益貢献しよう!
(β版非公開)