- お役立ち記事
- Purchasing department’s procurement of materials for short delivery times and methods for achieving it
Purchasing department’s procurement of materials for short delivery times and methods for achieving it
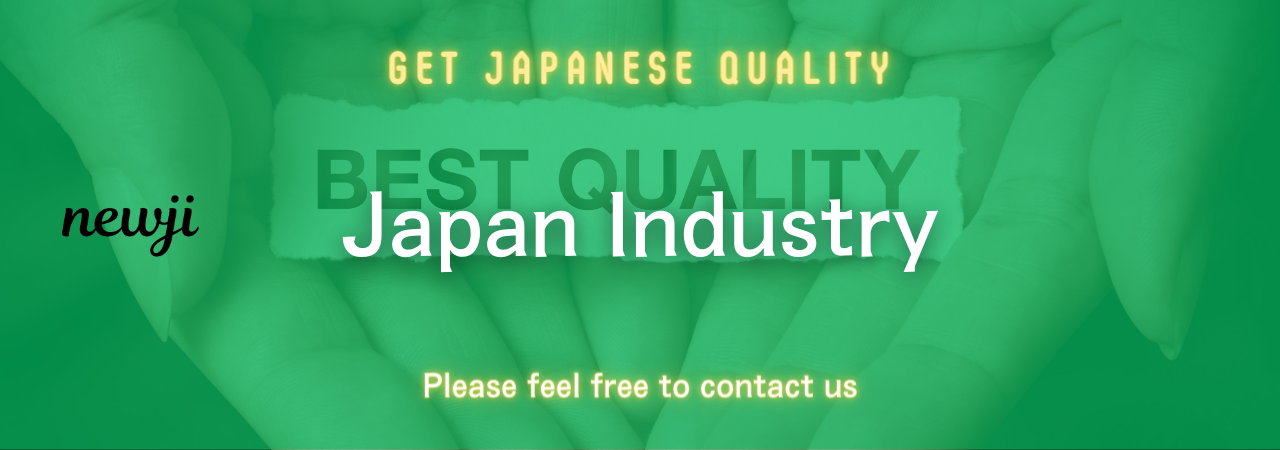
目次
Understanding the Importance of Short Delivery Times in Procurement
In the fast-paced world of business, the ability to procure materials with short delivery times can provide a significant competitive edge.
For purchasing departments, ensuring that materials are acquired quickly and efficiently is crucial.
It allows companies to meet production schedules, respond to market demands swiftly, and keep costs under control.
Short delivery times mean that businesses can maintain lean inventories, reducing storage costs and minimizing the risk of obsolescence.
More importantly, it enables companies to adapt quickly to changes in customer demand or supply chain disruptions.
This agility is essential in today’s market, where consumer expectations are high and competition is fierce.
Strategies for Achieving Short Delivery Times
Developing Strong Supplier Relationships
One of the most effective strategies for achieving short delivery times is developing strong relationships with suppliers.
Collaborative partnerships with suppliers can lead to more favorable terms, including faster delivery times.
It’s important for purchasing departments to communicate regularly with suppliers, understanding their capabilities and challenges.
By working together, both parties can create more efficient processes and improve lead times.
Leveraging Technology
Technology plays a crucial role in reducing delivery times.
Purchasing departments can utilize advanced procurement software to streamline ordering processes and improve communication with suppliers.
Automation tools can handle repetitive tasks, allowing purchasing teams to focus on strategic decision-making.
Real-time data and analytics can also provide valuable insights into supplier performance and potential delays, enabling proactive solutions.
Implementing Just-In-Time (JIT) Inventory
Just-In-Time (JIT) inventory management is another strategy to consider.
JIT reduces the time and cost associated with holding large inventories by aligning raw materials procurement closely with production schedules.
With JIT, materials are ordered and delivered just before they are needed.
This approach requires precise timing and reliable suppliers, but it can significantly cut down delivery times and reduce waste.
Localizing Suppliers
Choosing local suppliers can dramatically decrease delivery times.
Proximity to the supply source reduces transportation time and lowers the risks associated with international shipping, such as customs delays.
Local suppliers can also provide more frequent deliveries, which is beneficial when dealing with unpredictable demand.
Flexible Supplier Contracts
It can be advantageous to negotiate flexible contracts with suppliers to accommodate variable delivery schedules.
This flexibility allows purchasing departments to adjust orders more easily based on changing needs.
Suppliers, in turn, should be incentivized to maintain a level of responsiveness that meets the company’s requirements for rapid delivery.
Overcoming Challenges in Material Procurement
While there are numerous strategies to achieve short delivery times, purchasing departments often face challenges in executing them effectively.
One key challenge is the unpredictability of supply chain disruptions, such as natural disasters or political instability.
These disruptions can lead to delays regardless of the strategies in place.
Additionally, the reliance on a limited number of suppliers can pose a risk.
If one supplier faces difficulties, it can impact the entire procurement process.
Diversifying the supplier base while maintaining quality and price standards is essential to mitigate this risk.
Another challenge is the balance between cost and speed.
While faster delivery times are desirable, they may come at a higher price.
Purchasing departments need to carefully assess whether the premium for quicker delivery is justified by the potential benefits, such as increased production or sales.
Measuring the Success of Procurement Practices
To ensure the effectiveness of procurement practices aimed at achieving short delivery times, it’s crucial to establish key performance indicators (KPIs).
Common KPIs include supplier lead times, on-time delivery rates, and inventory turnover ratios.
These metrics provide insights into how efficiently a purchasing department operates and whether strategies are improving delivery times as intended.
Regularly reviewing these KPIs can help identify areas for improvement.
For instance, if a particular supplier consistently fails to meet delivery expectations, it might be worth exploring alternative partners.
Continuous improvement is an ongoing process that requires adapting strategies based on performance data.
Conclusion
In conclusion, the procurement of materials for short delivery times is an essential component of successful supply chain management.
Through strategic supplier relationships, leveraging technology, adopting JIT inventory practices, and overcoming challenges, purchasing departments can significantly improve delivery times.
By focusing on these elements, businesses can enhance their operational efficiency and responsiveness to market needs.
These efforts ultimately lead to a stronger competitive position in today’s dynamic business environment.
資料ダウンロード
QCD調達購買管理クラウド「newji」は、調達購買部門で必要なQCD管理全てを備えた、現場特化型兼クラウド型の今世紀最高の購買管理システムとなります。
ユーザー登録
調達購買業務の効率化だけでなく、システムを導入することで、コスト削減や製品・資材のステータス可視化のほか、属人化していた購買情報の共有化による内部不正防止や統制にも役立ちます。
NEWJI DX
製造業に特化したデジタルトランスフォーメーション(DX)の実現を目指す請負開発型のコンサルティングサービスです。AI、iPaaS、および先端の技術を駆使して、製造プロセスの効率化、業務効率化、チームワーク強化、コスト削減、品質向上を実現します。このサービスは、製造業の課題を深く理解し、それに対する最適なデジタルソリューションを提供することで、企業が持続的な成長とイノベーションを達成できるようサポートします。
オンライン講座
製造業、主に購買・調達部門にお勤めの方々に向けた情報を配信しております。
新任の方やベテランの方、管理職を対象とした幅広いコンテンツをご用意しております。
お問い合わせ
コストダウンが利益に直結する術だと理解していても、なかなか前に進めることができない状況。そんな時は、newjiのコストダウン自動化機能で大きく利益貢献しよう!
(Β版非公開)