- お役立ち記事
- Purchasing department’s role and success stories in supplier quality management
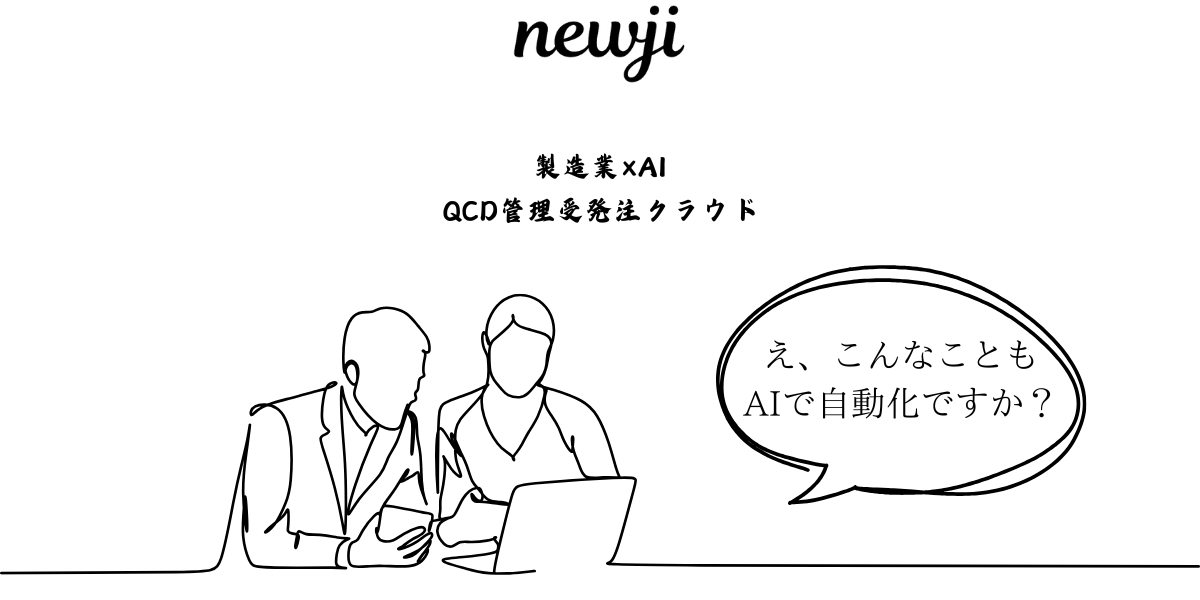
Purchasing department’s role and success stories in supplier quality management
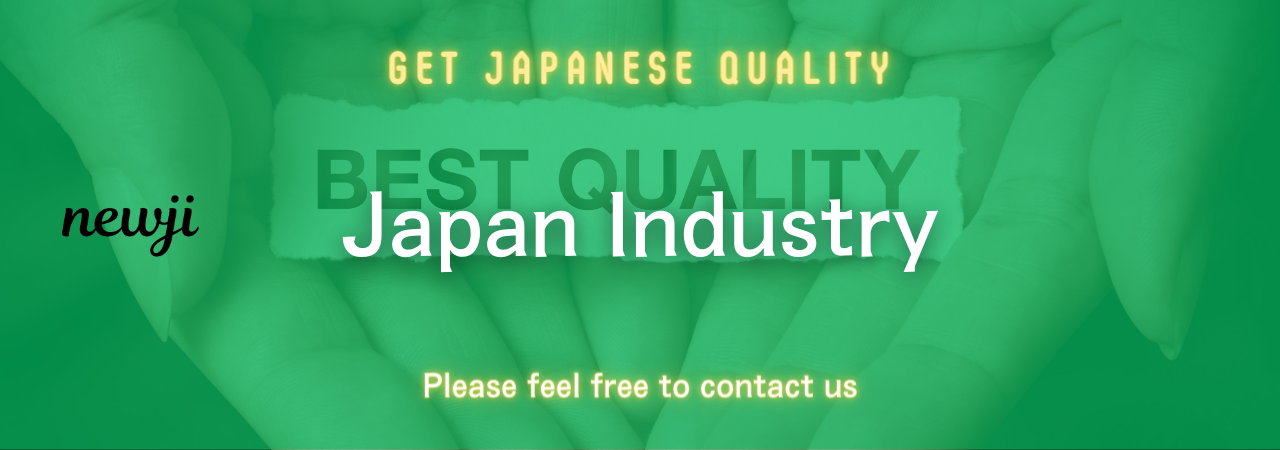
目次
Understanding the Purchasing Department’s Role
The purchasing department plays a crucial role in any organization, particularly in supplier quality management.
Their primary responsibility is to ensure that the goods and services procured meet the set standards.
This involves a keen understanding of the products, efficient communication with suppliers, and a thorough evaluation process.
Supplier quality management hinges on the ability of the purchasing team to select suppliers who meet the company’s quality criteria.
This can involve rigorous assessments and continuous monitoring of supplier performance.
Often, the purchasing team will work closely with quality assurance departments to define the specifications and standards needed.
Identifying the Right Suppliers
The first step in effective supplier quality management is identifying the right suppliers.
This can be a complex process involving research, market analysis, and negotiation.
Purchasing departments often use various tools and systems to assess potential suppliers’ capabilities, track records, and compliance with industry standards.
Factors such as the supplier’s financial stability, manufacturing processes, and quality control mechanisms are scrutinized.
Through this rigorous selection process, the purchasing department ensures that only the most reliable suppliers are chosen.
This significantly reduces the risk of supply chain disruptions and ensures consistent product quality.
Ensuring Consistent Quality
Even after a supplier is chosen, the purchasing department’s job is far from over.
To maintain quality, there is a need for ongoing evaluation and interaction with suppliers.
Monitoring Supplier Performance
Regular assessments help ensure that suppliers continue to meet quality and delivery expectations.
Purchasing teams often conduct audits and request performance metrics.
This may include inspecting supplier facilities or reviewing production processes to ensure that they align with required standards.
By building cooperative relationships with suppliers, purchasing departments can work together to address any issues that arise.
This collaborative approach not only ensures consistent quality but also enhances supplier relationship management.
Implementing Quality Controls
Quality controls are an integral part of supplier management, and the purchasing department plays a strategic role in implementing these measures.
This includes setting up clear performance indicators and quality benchmarks that suppliers must meet.
Quality controls can take various forms, from regular product testing to detailed inspections and compliance checks.
For example, purchasing teams might establish inspection plans that outline how often products are tested and the methods used for evaluation.
Communication of these plans to suppliers ensures transparency, and any findings from these controls can help in taking corrective actions if needed.
Success Stories in Supplier Quality Management
The success of supplier quality management can be seen in numerous organizations that have effectively streamlined their procurement processes.
Let’s explore some success stories that illustrate the purchasing department’s impact on supplier quality.
Case Study: Automotive Industry
The automotive industry is particularly reliant on rigorous supplier quality management due to its complex supply chains.
One renowned automotive manufacturer, for example, faced challenges with inconsistent parts from multiple suppliers.
The purchasing department implemented a supplier evaluation framework, requiring all suppliers to undergo a stringent quality audit.
Through collaboration with suppliers, the purchasing team was able to improve communication and set clear quality expectations.
As a result, the manufacturer saw a noticeable reduction in defects and improved production efficiency.
Case Study: Electronics Manufacturer
Another example is an electronics manufacturer that turned its supplier challenges into a competitive advantage.
Their purchasing department identified low-performance suppliers using a dedicated supplier management software.
By fostering direct communication channels and sharing technical knowledge with these suppliers, the company improved product quality and maintained its market position.
This proactive engagement allowed the company to innovate by collaborating with suppliers and incorporating their feedback into product design.
Such initiatives not only enhanced supplier quality but also led to the development of better, more competitive products.
Keys to Success in Supplier Quality Management
Success in supplier quality management hinges on several core principles that purchasing departments should embrace.
These principles ensure effective sourcing and continuous improvement in supplier performance.
Developing Effective Communication Channels
Strong communication is the foundation of successful supplier partnerships.
Maintaining open, transparent, and regular communication allows for immediate issue resolution and fosters trust between the purchasing department and suppliers.
This involves not just discussing concerns but also providing feedback and recognizing good performance.
Collaborative discussions pave the way for shared innovation and improvements.
Investing in Technology
Many successful purchasing departments leverage technology to enhance supplier management.
The use of software tools for tracking supplier performance, managing contracts, and monitoring compliance can streamline processes and provide valuable insights.
These tools assist in making data-driven decisions, securing reliable suppliers, and mitigating risks.
Incorporating technology helps ensure that all supplier activities are aligned with the company’s strategic quality objectives.
Conclusion
In conclusion, the purchasing department’s role in supplier quality management is pivotal to organizational success.
Their efforts in selecting high-quality suppliers, enforcing quality controls, and fostering strong supplier relationships result in reduced risks and improved product quality.
As seen from the success stories, effective supplier quality management requires a proactive approach, a commitment to communication, and the integration of practical tools and policies.
By adopting these strategies, purchasing departments can play a critical role in enhancing supplier quality and driving business success.
資料ダウンロード
QCD調達購買管理クラウド「newji」は、調達購買部門で必要なQCD管理全てを備えた、現場特化型兼クラウド型の今世紀最高の購買管理システムとなります。
ユーザー登録
調達購買業務の効率化だけでなく、システムを導入することで、コスト削減や製品・資材のステータス可視化のほか、属人化していた購買情報の共有化による内部不正防止や統制にも役立ちます。
NEWJI DX
製造業に特化したデジタルトランスフォーメーション(DX)の実現を目指す請負開発型のコンサルティングサービスです。AI、iPaaS、および先端の技術を駆使して、製造プロセスの効率化、業務効率化、チームワーク強化、コスト削減、品質向上を実現します。このサービスは、製造業の課題を深く理解し、それに対する最適なデジタルソリューションを提供することで、企業が持続的な成長とイノベーションを達成できるようサポートします。
オンライン講座
製造業、主に購買・調達部門にお勤めの方々に向けた情報を配信しております。
新任の方やベテランの方、管理職を対象とした幅広いコンテンツをご用意しております。
お問い合わせ
コストダウンが利益に直結する術だと理解していても、なかなか前に進めることができない状況。そんな時は、newjiのコストダウン自動化機能で大きく利益貢献しよう!
(Β版非公開)