- お役立ち記事
- Purchasing department’s role in developing supplier performance evaluation standards
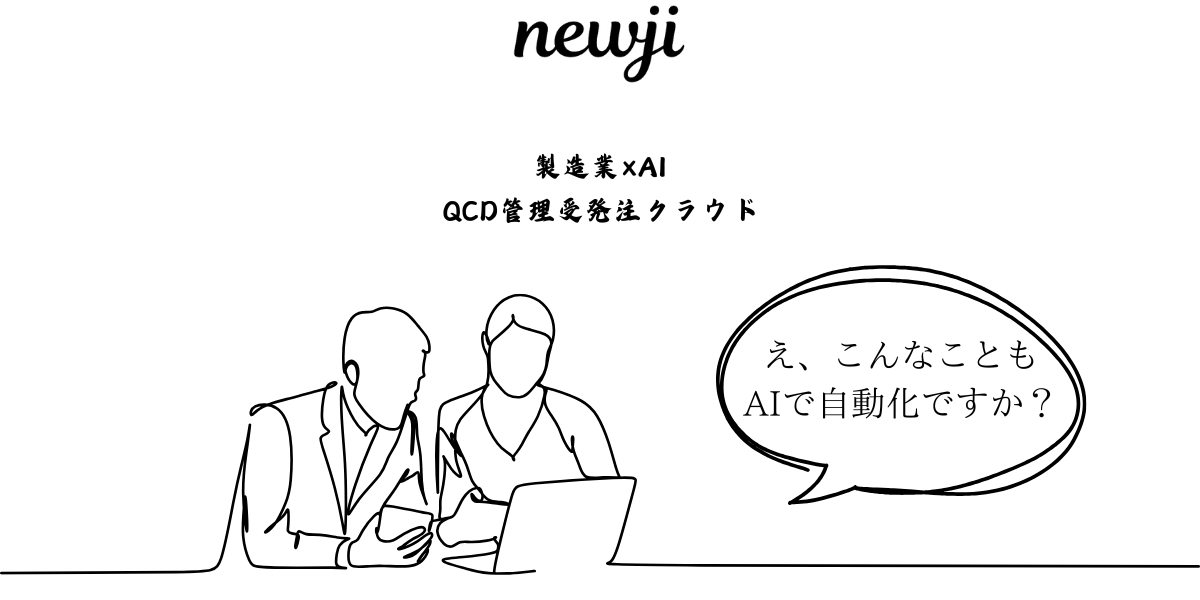
Purchasing department’s role in developing supplier performance evaluation standards
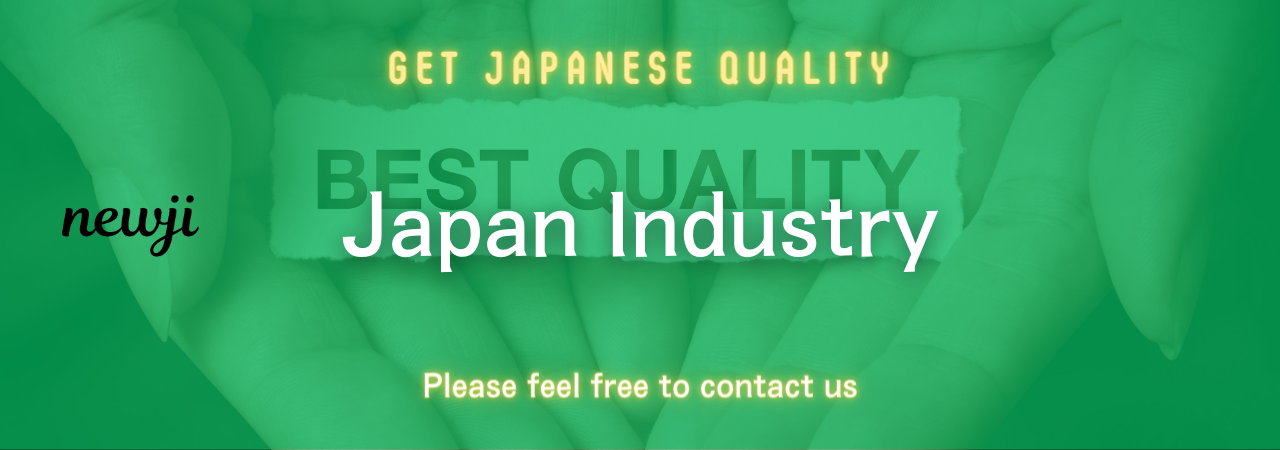
目次
Introduction to Supplier Performance Evaluation
In today’s competitive business environment, the role of the purchasing department has expanded beyond just sourcing and buying goods or services.
One of the critical functions now is developing supplier performance evaluation standards.
These standards are pivotal in ensuring that suppliers meet the desired quality, delivery, and cost requirements.
By setting and maintaining these standards, purchasing departments can establish long-term, fruitful relationships with suppliers, leading to improved business outcomes.
The Importance of Supplier Performance Evaluation
Supplier performance evaluation is essential for several reasons.
Firstly, it helps ensure that suppliers adhere to agreed-upon terms, such as delivery schedules and quality benchmarks.
This adherence can significantly impact an organization’s production process and overall operational efficiency.
Secondly, a well-defined supplier performance evaluation system can help in risk management.
It allows companies to identify underperforming suppliers early, reducing potential disruptions in the supply chain.
This proactive approach can save businesses from costly downtime or quality issues.
Lastly, evaluating supplier performance regularly fosters a culture of continuous improvement.
Suppliers are motivated to enhance their processes and services to meet or exceed client expectations.
This improvement can lead to innovations that benefit both the supplier and the purchasing company.
Key Components of Supplier Performance Evaluation
When developing supplier performance evaluation standards, it is crucial to define clear and measurable criteria.
Here are some of the key components that purchasing departments should consider:
1. Quality
Quality is often the foremost parameter in evaluating supplier performance.
Ensuring that suppliers deliver products or services that meet the required quality standards is essential.
To measure quality, companies can use metrics such as defect rates, compliance with specifications, and the results of quality inspections.
2. Delivery Performance
Timeliness is critical in today’s fast-paced market.
Suppliers should meet delivery schedules consistently to support the purchasing company’s operations.
Late deliveries can lead to significant disruptions, so tracking on-time delivery rates and understanding the causes of delays are vital.
3. Cost Management
Cost management involves analyzing whether suppliers provide competitive pricing and deliver value for money.
Purchasing departments should assess cost against the supplier’s performance in other areas, ensuring that lower costs do not compromise quality or service levels.
4. Responsiveness and Communication
Effective communication is essential for a successful supplier relationship.
The supplier’s responsiveness to queries, the promptness of service, and their flexibility in meeting changing requirements can influence overall performance evaluations.
5. Sustainability and Compliance
Many organizations now require their suppliers to adhere to specific sustainability and ethical standards.
Assessing suppliers against these criteria ensures alignment with broader corporate social responsibility goals and regulatory compliance.
Developing an Effective Supplier Evaluation Process
Developing a comprehensive supplier evaluation process involves several critical steps:
Step 1: Establish Clear Criteria
The first step is defining clear, measurable criteria that align with the company’s strategic objectives.
These criteria should cover all aspects of supplier performance and be communicated effectively to the suppliers.
This communication ensures that suppliers understand what is expected of them.
Step 2: Collect Data Consistently
Regular data collection is vital for an accurate assessment of supplier performance.
Purchasing departments can use various tools and technologies, such as enterprise resource planning (ERP) systems, to gather relevant data efficiently.
This data should cover all agreed-upon performance metrics.
Step 3: Analyze and Interpret Data
After collecting data, the next step is analysis.
Purchasing professionals must interpret the data to identify trends and patterns.
This analysis helps in understanding whether suppliers consistently meet performance standards or if there are areas needing improvement.
Step 4: Conduct Regular Reviews
Regular reviews with suppliers can foster open communication and collaboration.
These reviews provide an opportunity to discuss performance issues, recognize achievements, and explore improvement areas.
They also help build a partnership mentality rather than a transactional relationship.
Step 5: Implement Action Plans
When performance shortfalls are identified, implementing corrective action plans is crucial.
These plans should be developed collaboratively with suppliers to address issues and boost their performance.
Regular follow-ups ensure these actions are working effectively.
The Role of Technology in Supplier Performance Evaluation
Technology plays a crucial role in enhancing supplier performance evaluation.
With the advent of sophisticated software solutions, purchasing departments can manage supplier performance more efficiently.
These tools can automate data collection, generate real-time reports, and provide meaningful insights into supplier performance.
Moreover, cloud-based platforms can facilitate better collaboration and data sharing between purchasing teams and suppliers.
These platforms enhance transparency and enable both parties to make informed decisions in real time.
Conclusion
In conclusion, the purchasing department’s role in developing supplier performance evaluation standards is integral to the success of an organization.
By setting clear criteria, consistently collecting data, and fostering open communication, purchasing teams can ensure that suppliers meet or exceed performance expectations.
This effort leads to improved supply chain efficiency, risk mitigation, and stronger strategic partnerships with suppliers, ultimately benefiting the entire organization.
資料ダウンロード
QCD調達購買管理クラウド「newji」は、調達購買部門で必要なQCD管理全てを備えた、現場特化型兼クラウド型の今世紀最高の購買管理システムとなります。
ユーザー登録
調達購買業務の効率化だけでなく、システムを導入することで、コスト削減や製品・資材のステータス可視化のほか、属人化していた購買情報の共有化による内部不正防止や統制にも役立ちます。
NEWJI DX
製造業に特化したデジタルトランスフォーメーション(DX)の実現を目指す請負開発型のコンサルティングサービスです。AI、iPaaS、および先端の技術を駆使して、製造プロセスの効率化、業務効率化、チームワーク強化、コスト削減、品質向上を実現します。このサービスは、製造業の課題を深く理解し、それに対する最適なデジタルソリューションを提供することで、企業が持続的な成長とイノベーションを達成できるようサポートします。
オンライン講座
製造業、主に購買・調達部門にお勤めの方々に向けた情報を配信しております。
新任の方やベテランの方、管理職を対象とした幅広いコンテンツをご用意しております。
お問い合わせ
コストダウンが利益に直結する術だと理解していても、なかなか前に進めることができない状況。そんな時は、newjiのコストダウン自動化機能で大きく利益貢献しよう!
(Β版非公開)